Формовочные смеси (песчано-глинистые)
Песчано-глинистые смеси по характеру использования делят на облицовочные, наполнительные и единые.
Облицовочная смесь — более качественная, с высокой прочностью, газопроницаемостью и другими свойствами. Для ее получения берут большее количество свежих материалов (песка, глины). При формовке такую смесь наносят на модель, создавая в литейной форме поверхностный слой толщиной 40 - 100 мм, подвергаемый наибольшему воздействию расплава при заливке. Остальной объем формы изготавливают из наполнительной смеси — менее качественной, в основном состоящей из оборотной смеси (смеси, бывшей в употреблении). Оборотные смеси используют для уменьшения расхода свежего песка и глины.
Единые формовочные смеси применяют в массовом производстве, при машинной формовке для заполнения всего объема формы. Эти смеси, как и облицовочные, непосредственно соприкасаются с расплавленным металлом и должны обладать высокими свойствами.
Специальные способы литья
Литье в оболочковые формы
При этом способе детали получают в тонкостенных формах-оболочках, изготовленных из высокопрочных песчано-смоляных смесей. Толщина оболочки для мелкого литья составляет 8 - 10 мм, для среднего 12 - 15 мм. Форма состоит из двух оболочковых полуформ, соединенных по вертикальной или по горизонтальной линии разъема путем склеивания или при помощи скоб, струбцин. Для получения внутренних полостей в отливках при сборке формы в нее устанавливают сплошные или полые стержни.
|
|
Характеристики способа
Отливки имеют на 40 - 50 % меньшие припуски на механическую обработку, чем в песчано-глинистой форме. Одновременно сокращаются затраты на обрубно-очистные операции. Способ применяется для изготовления отливок из черных и цветных сплавов массой до 200 кг с максимальными размерами до 950 мм. Наиболее эффективно изготовление таким образом отливок массой 5 - 15 кг в условиях крупносерийного и массового производства.
Литье по выплавляемым моделям
Сущность способа состоит в том, что детали получают заливкой в неразъемные, тонкостенные керамические формы, изготовленные с помощью моделей из легкоплавящихся составов.
Способ имеет следующие преимущества:
1. возможность изготовления отливок сложной конфигурации практически из любых сплавов;
2. малая шероховатость поверхности;
3. минимальные припуски на обработку резанием;
4. возможность создания сложных конструкций, объединяющих несколько деталей в один узел.
недостатки способа:
1. процесс изготовления формы многооперационный, трудоемкий и длительный;
2. сложность управления качеством;
|
|
3. большая номенклатура материалов, используемых для получения формы;
4. повышенный расход металла на литники.
Метод литья по выплавляемым моделям широко используется при изготовлении отливок массой от десятков граммов до сотен килограммов из черных и цветных сплавов. Особенно широко он применяется для деталей из жаропрочных или специальных труднообрабатываемых сплавов.
Литье в металлические формы
Литьем в металлические формы (кокили) получают более 40% всех отливок из алюминиевых и магниевых сплавов, отливки из чугуна, стали и других сплавов. Сущность способа состоит в получении литых деталей путем свободной заливки расплава в металлические формы.
Конструкции кокилей разнообразны, они могут быть неразъемными (вытряхными) и разъемными. Неразъемные кокили применяют для получения небольших отливок простой конфигурации, которые можно удалять без разъема формы.
Способ имеет следующие преимущества:
1. Кокиль - форма многократного использования. в нем можно получить 300 - 500 стальных отливок массой 100 - 150 кг, около 5000 чугунных мелких отливок, несколько десятков тысяч отливок из алюминиевых сплавов;
2. Возможность механизации и автоматизации обеспечивает высокую производительность при значительном снижении стоимости отливок.
|
|
3. Образование мелкозернистой структуры сплава вследствие быстрого затвердевания, что определяет его высокие механические свойства.
4. высокая точность размеров и качества поверхности отливки.
Недостатками являются высокая стоимость кокилей, трудоемкость в изготовлении сложных по конфигурации и тонкостенных отливок, сравнительно невысокая стойкость кокиля при литье тугоплавких сплавов.
Литье под давлением
Литье под давлением — наиболее производительный способ изготовления небольших отливок, в основном, из цветных сплавов с высокой точностью по размерам и чистотой поверхности. Отливки получают в стальных пресс-формах. Расплавленный сплав заполняет пресс-форму под давлением поршня до 300 МПа, быстро затвердевает и образует отливку. После чего пресс-форма раскрывается, и отливка удаляется толкателями.
Возможности способа. Литьем под давлением изготавливают отливки от нескольких граммов до десятков килограммов из алюминиевых, магниевых, медных и других цветных сплавов, реже из тугоплавкой стали. Этот способ позволяет получать литые детали простой формы и сложные фасонные тонкостенные отливки.
|
|
Машины для литья под давлением, работают в автоматическом режиме, имеют высокую производительность — до 3000 и более отливок в час.
К недостаткам способа относятся ограниченная масса отливаемых деталей - менее 50 кг, высокая стоимость и сложность изготовления пресс-форм, трудность получения отливок со сложными полостями. Отливки имеют газоусадочную пористость.
Центробежное литье
центробежным способом изготавливают отливки из чугуна, стали, сплавов титана, алюминия и тяжелых цветных металлов, сплавов магния и цинка.
Номенклатура изготавливаемых изделий преимущественно ограничена телами вращения: трубы, втулки, кольца, гильзы автомобильных и тракторных двигателей, и др. Масса отливок может составлять от нескольких килограммов до 45 т, а толщина стенок - от нескольких миллиметров до 350 мм. Точность и чистота поверхности отливок зависят от материала формы.
При данном способе отливки имеют повышенные механические свойства, а также увеличенный коэффициент использования материала (0,8 – 0,9).
Кроме – того, центробежным литьем можно получить тонкостенные отливки из сплавов с низкой жидкотекучестью, что невозможно сделать при других способах литья.
Обработка металлов давлением
Сущность ОМД
Обработка металлов давлением основана на их способности в определенных условиях пластически деформироваться в результате воздействия на деформируемое тело (заготовку) внешних сил.
Существенные преимущества обработки металлов давлением посравнению с обработкой резанием — возможность значительного уменьшения отхода металла, а также повышения производительности труда, поскольку в результате однократного приложения усилия можно значительно изменить форму и размеры деформируемой заготовки. Кроме того, пластическая деформация сопровождается изменением физико-механических свойств металла заготовки, что можно использовать для получения деталей с наилучшими эксплуатационными свойствами (прочностью, жесткостью, высокой износостойкостью и т.д.) при наименьшей их массе.
Дата добавления: 2018-04-15; просмотров: 737; Мы поможем в написании вашей работы! |
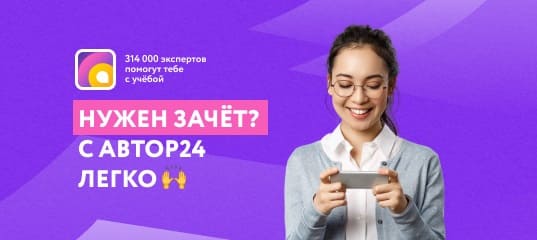
Мы поможем в написании ваших работ!