Диаграмма железо – углерод (цементит)
В сплавах при охлаждении и нагреве происходят изменения и образуются новые фазы и структуры. Эти изменения можно определить по диаграмме состояния, показывающее фазовый состав и структуру сплавов в зависимости от температуры и химической концентрации компонентов в условиях равновесия.
Структурные составляющие железоуглеродистых сплавов. В зависимости от температуры и концентрации углерода железоуглеродистые сплавы имеют следующие составляющие (табл. 1.2):
В структуре чугунов присутствует еще одна структурная составляющая-
Графит - углерод в свободном состоянии, располагается в основной массе металла и имеет развитую объемную форму в виде пластинок; кроме пластинчатого графита можно получить графит компактных форм (шаровидный или хлопьевидный), образующийся в результате распада цементита или выделяющийся из пересыщенных твердых растворов железа с углеродом. В железоуглеродистом сплаве графит образуется при содержании Si 1,5 % и при очень медленном охлаждении. Графит мягок и обладает низкой прочностью.
Принятое разграничение между сталью и чугуном совпадает с предельной растворимостью углерода в аустените. Сталь после затвердевания не содержит хрупкой структурной составляющей – ледебурита – и при высоком нагреве имеет только аустенитную структуру, обладающую высокой пластичностью. Поэтому стали легко деформируются при нормальных и повышенных температурах, т.е. являются в отличие от чугуна ковкими сплавами. По сравнению со сталью чугуны обладают значительно лучшими литейными свойствами, и более низкими температурами плавлениями, имеют меньшую усадку.
|
|
Практическое применение диаграммы Fе—Fе3С. Диаграмму Fе—Fe3С используют для определения видов и температурных интервалов термической обработки стали; для назначения температурного интервала при обработке давлением; для определения температуры плавления и заливки сплава и его литейных свойств (жидкотекучести, усадки).
Влияние углерода на структуру и свойства сталей
Механические свойства углеродистой стали зависят главным образом от содержания углерода. С ростом содержания углерода в стали увеличивается количество цементита и соответственно уменьшается количество феррита, т.е. повышаются прочность и твердость и уменьшается пластичность. Как видно из графика, приведенного на рис. 150, прочность повышается только до 1% С, а при более высоком содержании углерода она начинает уменьшаться. Происходит это потому, что образующаяся по границам зерен в заэвтектоидных сталях сетка вторичного цементита снижает прочность стали.
|
|
Кроме углерода, в стали есть еще другие элементы - примеси, присутствие которых обусловлено разными причинами.
4.5. Влияние примесей на свойства железоуглеродистых сплавов
На свойства железоуглеродистых сплавов влияет наличие в них постоянных примесей (вредных - серы, фосфора, кислорода, азота, водорода; полезных - кремния, марганца и др.). Эти примеси могут попадать в сплав из природных соединений (руд), например, сера и фосфор; из металлического лома — хром, никель и др.; в процессе раскисления - кремний и марганец.
Влияние углерода. Углерод в железоуглеродистом сплаве находится главным образом в связанном состоянии в виде цементита. В свободном состоянии в виде графита он содержится в чугунах. С увеличением содержания углерода возрастает твердость, прочность и уменьшается пластичность.
Влияние серы. Сера является вредной примесью. Она образует легкоплавкую эвтектику FeS + Fе. При кристаллизации сплава легкоплавкая эвтектика располагается по границам зерен и при повторном нагреве расплавляется, в результате чего нарушается связь между зернами, что приводит к образованию трещин и надрывов. Это явление носит название красноломкости. Допускается содержание серы до 0,06%.
|
|
Влияние фосфора. Фосфор — вредная примесь, растворяясь в γ- и α- железе, искажает кристаллическую решетку и ухудшает пластические свойства сплава. Фосфор вызывает явление хладноломкости, и его содержание в сталях не должно превышать 0,08%. В чугуне допускается до 0,3% Р.
Влияние азота, кислорода и водорода. Эти элементы присутствуют в сплавах или в составе хрупких неметаллических включений или в свободном состоянии, при этом они располагаются в дефектных местах в виде молекулярного и атомарного газов. Неметаллические включения служат концентраторами напряжений и могут понизить механические свойства (прочность, пластичность).
Влияние кремния и марганца. Кремний, растворяясь в феррите, повышает предел текучести и уменьшает склонность к хладноломкости. Кремний способствует графитизации чугуна.
Марганец образует твердый раствор с железом и немного повышает твердость и прочность феррита. В присутствии серы он частично связывается с серой в сернистый марганец и переходит в шлак. При содержании марганца более 1,5 % снижаются пластические свойства стали. В сталях содержится обычно не более 0,4 % Si и 0,8 % Мn.
Классификация сталей
|
|
Стали классифицируют, главным образом, по:
Химическому составу,
Качеству,
Назначению.
Дополнительно классифицируют по:
1. степени раскисления,
2. структуре.
По химическому составу классифицируют главным образом конструкционные стали. Конструкционные стали делят на углеродистые и легированные.
Углеродистые стали бывают низкоуглеродистыми С = (0,05 – 0,25)%; среднеуглеродистыми С = (0,30 – 0,55)% и высокоуглеродистыми С = (0,60 – 0,85)%.
Легированные стали условно подразделяют на низколегированные с содержанием легирующих элементов в сумме 2,5 – 5%; среднелегированные – до 10%; и высоколегированные – более 10%.
Качество сталей определяются условиями металлургического производства и содержанием в них вредных примесей. Стали классифицируют на 4 класса:
1. стали обыкновенного качества (углеродистые) S 0,06% и P
0,07%. Сп, кп, пс,
2. качественные стали – углеродистые или легированные S,P 0,035%,
3. высококачественные стали, главным образом легированные S,P 0,025%,
4. особо высококачественные стали для повышения чистоты получают вспомогательную улучшающую обработку, вид которой указывают в конце марки через тире. S 0,015% и P
0,025%.
По назначению стали классифицируют на конструкционные, с содержанием С < 0,8% и инструментальные, с содержанием С > 0,8%.
Конструкционные стали представляют наиболее обширную группу, предназначенную для изготовления строительных сооружений, деталей машин и приборов. К этим сталям относят цементуемые, улучшаемые, высокопрочные и рессорно-пружинные.
Инструментальные стали имеют высокие твердость, прочность и износостойкость. Их используют для изготовления режущего и мерительного инструмента, штампов холодного и горячего (до 200°С) деформирования.
По степени раскисления и характеру затвердевания стали классифицируют на спокойные, полуспокойные и кипящие. Раскисление — процесс удаления кислорода из жидкого металла, проводимый с целью предотвращения хрупкого разрушения стали при горячей деформации.
Спокойные стали раскисляют марганцем, кремнием и алюминием. Они содержат мало кислорода и затвердевают спокойно без газовыделения. Кипящие стали раскисляют марганцем. Перед разливкой в них содержится повышенное содержание кислорода, который при затвердевании частично взаимодействует с углеродом и удаляется в виде СО. Выделение пузырьков СО создает впечатление кипения стали, с чем и связано ее название. Кипящие стали достаточно дешевые, их производят низкоуглеродистыми и практически без кремния (Si < 0,07%), но с повышенным количеством газовых примесей.
Полуспокойные стали по степени раскисления занимают промежуточное положение между спокойными и кипящими. Легированные стали производят спокойными, углеродистые — спокойными, полуспокойными и кипящими.
По структуре в равновесном состоянии стали делятся на:
1. доэвтектоидные, имеющие в структуре феррит и перлит;
2. эвтектоидные, структура которых состоит из перлита;
3. заэвтектоидные, имеющие в структуре перлит и цементит вторичный.
Классификация чугунов
1. серые чугуны. представляют собой железоуглеродистый сплав, в состав которого входят от 2,2 до 3,8% углерода, а также такие примеси, как кремний (1,0 - 2,9%), марганец (0,2 - 1,1%), фосфор (до 0,3%) и сера (до 0,15%).
Серый чугун получил такое название потому, что его структура представляет металлическую основу, в которой расположено множество включений углерода в виде графитовых частиц пластинчатой формы. Это придает характерный серый цвет излому такого чугуна. Серый чугун широко распространен как материал для получения самых разнообразных отливок. Вместе с тем графитовые включения отрицательно влияют на механические свойства серых чугунов, снижают их пластичность и прочность при растяжении.
С увеличением количества связанного углерода можно получить отливки из белого чугуна. В таком чугуне весь углерод находится в связанном состоянии. Ввиду высокой твердости и хрупкости белый чугун почти не применяется в машиностроении.
2. Ковкие чугуны. Их получают из отливок белого чугуна путем отжига, т. е. длительного нагрева при температуре ~ 1000 °С. В результате отжига устраняются хрупкость и твердость, свойственные белым чугунам. Ковкие чугуны обеспечивают высокую прочность в сочетании с вязкостью и хорошей обрабатываемостью. Ковкие чугуны содержат от 2,2 до 3,0 % углерода, кремния (0,7—1,5 %), марганец (0,2—0,6 %), фосфор (до 0,2 %) и сера (до 0,1 %). Форма графита – хлопьевидная.
Название «ковкие чугуны» несколько условно. Они, как и серые чугуны, ковке не подвергаются. Но, отличаясь большей прочностью и пластичностью, чем серые чугуны, отливки из ковких чугунов могут даже правиться на прессах.
3. Высокопрочные чугуны. Повышение прочности серого чугуна может быть осуществлено проведением специального технологического процесса - модифицирования, при котором в расплавленный чугун вводится небольшое количество (0,1 - 0,6 %) специальных добавок (модификаторов). В результате модифицирования происходит образование мелкозернистой металлической основы чугуна с мелкодисперсными включениями графита шаровидной формы. Высокопрочные чугуны содержат от 3,0 до 3,6 % углерода.
Высокопрочный чугун получается путем обработки расплава серого чугуна модификаторами на основе магния, церия, кальция (например, в состав лигатуры ФЦМ-5 входят Mg, Ce, Fe).
Теория термической обработки
Основой процессов термической обработки является полиморфизм (разные кристаллические формы) железа и его твердых растворов на базе α- и γ-железа. Полиморфные превращения стали происходят в интервале температур, ограниченном нижней А1и верхними A3 и Асm критическими точками.
В результате полиморфизма происходит перекристаллизация в твердом состоянии. Перекристаллизация - это изменение кристаллического строения стали при ее нагреве или охлаждении до определенных температур.
Таким образом, термическая обработка заключается в нагреве сплавов до определенных температур, выдержке их при этих температурах и последующем охлаждении с различной скоростью. При этом изменяются структура сплава, а следовательно, и его свойства. Изменяя режим термической обработки, можно получить различные физико-механические свойства и структуры железоуглеродистых сплавов.
Термическая обработка может быть промежуточной и окончательной. Главной задачей промежуточной термической обработки является снижение твердости стали для ее лучшей обрабатываемости режущим инструментом или обработкой металлов давлением. Окончательная термическая обработка преследует цель придать стали такие свойства, которые требуются в условиях эксплуатации деталей.
Отжиг
Основное назначение отжига - получение равновесной структуры, поэтому при отжиге, как правило, детали охлаждают медленно. Углеродистые стали - со скоростью ~200 °С, легированные стали – (30 – 100)°С/час.
Отжиг I рода
Диффузионный (гомогенизирующий) отжиг применяют для устранения ликвации (выравнивание химического состава). В его основе - диффузия. При этом выравнивается состав и растворяются избыточные карбиды. Такой отжиг проводят при высокой температуре с длительной выдержкой. Гомогенизирующему отжигу подвергают в основном легированные стали. Это объясняется тем, что скорость диффузии углерода, растворенного в аустените по способу внедрения, на несколько порядков больше скорости диффузии легирующих элементов, которые растворяются в аустените по способу замещения. Гомогенизация углеродистых сталей происходит практически в процессе их нагрева.
Режим гомогенизирующего отжига: нагрев до температуры (1050 – 1200)°С, время выдержки составляет 8 - 10 ч.
Рекристаллизационный отжиг. В заводской практике для устранения наклепа холоднокатаных листов из углеродистой стали с (0,1 - 0,2)% С отжиг проводят, при (680 – 700)°С, для холоднотянутых прутков из легированных сталей при (700 – 730)°С и т.д. Время выдержки при нагреве зависит от толщины сечения. Для тонких листов и проволоки оно составляет 25 - 30 мин.
Отжиг для снятия напряжений проводят для деталей из углеродистой стали при нагреве до (400 – 600)°С с выдержкой 2,5 мин на 1 мм толщины сечения.
Отжиг II рода
Перекристаллизационный отжиг основан на фазовой перекристаллизации, т.е. является отжигом II рода. Основное его назначение - возможно более полное изменение фазового состава. Поэтому температура нагрева и время выдержки должны обеспечить нужные структурные превращения, скорость охлаждения выбирают такой, чтобы успели произойти обратные диффузионные фазовые превращения. После такого отжига получают более однородную мелкозернистую структуру, твердость понижается, пластичность повышается, поэтому отжиг II рода применяют в качестве предварительной термической обработки и перед обработкой стальных деталей на металлорежущих станках.
В зависимости от температуры нагрева различают полный и неполный отжиг.
Полный отжиг обычно применяют для доэвтектоидной стали. Изделия нагревают до температуры на (30 – 50)°С выше точки Ас3, что обеспечивает полную перекристаллизацию - превращение исходной ферритно-перлитной структуры в аустенит. При такой температуре нагрева аустенит получится мелкозернистым, следовательно, при охлаждении сталь будет иметь также мелкозернистую структуру. Если при отжиге нагреть изделия значительно выше Ас3, то зерна аустенита могут вырасти до крупных размеров. После охлаждения получится грубая структура, состоящая из крупных зерен феррита и перлита. Сталь с такой структурой обладает пониженной пластичностью.
Неполный отжиг применяют для заэвтектоидной стали. При нагреве на (20 – 50)°С выше Ас1 (740 - 770)°С в структуре сохраняется вторичный цементит. В результате отжига цементит получается в виде зерен (глобулей), поэтому такой отжиг называют также сфероидизацией. Получению зернистого цементита способствует предшествующая отжигу горячая пластическая деформация, при которой цементитная сетка дробится. Сталь с зернистым цементитом лучше обрабатывается режущим инструментом и приобретает хорошую структуру после закалки. Неполный отжиг для доэвтектоидной стали применяют редко. При нагреве до этой температуры не происходит полной перекристаллизации, часть зерен феррита остается в том же виде, что и до нагрева. Такой отжиг проводят только в тех случаях, когда исправления структуры не требуется, а необходимо только понижение твердости.
Нормализация
Нормализацией называют термическую обработку стали, при которой изделие нагревают до аустенитного состояния (на (30 – 50) град выше Ас3 или Асm) и охлаждают на спокойном воздухе. Следовательно, отличие нормализации от полного отжига для доэвтектоидных сталей заключается только в скорости охлаждения. В результате нормализации получается более тонкое строение эвтектоида (тонкий перлит или сорбит), уменьшаются внутренние напряжения, устраняются многие пороки, возникшие в процессе предшествующих обработок изделий. Твердость и прочность выше, чем после отжига. Поэтому, несмотря на значительную экономию времени, нормализация не всегда может заменить отжиг. В заэвтектоидных сталях нормализация устраняет грубую сетку вторичного цементита. Нормализацию чаще применяют как промежуточную операцию, улучшающую структуру. Но иногда ее применяют и как окончательную, например, при изготовлении сортового проката (рельсы, швеллеры и т. п.).
Закалка
Основные параметры при закалке - температура нагрева и скорость охлаждения. Температуру нагрева для сталей определяют по диаграммам состояния, скорость охлаждения - по диаграммам изотермического распада аустенита.
1 Для полного отжига, нормализации и закалки изделия практически нагревают до одинаковых температур, отличие в этих видах термической обработки заключается только в скорости охлаждения
Температура закалки. Доэвтектоидные стали нагревают до температуры выше критической точки Ас3 на (30 – 50)°С. Если такие стали нагреть до температуры между критическими точками Ас1 и Ас3 и охладить, то в структуре закаленной стали, кроме мартенсита, будет присутствовать феррит, что существенно ухудшает свойства. Такая закалка называется неполной.
Заэвтектоидные стали при закалке нагревают до температуры Ас1 + (40 - 60)0С. После охлаждения с таких температур получают структуру мартенсита с включением вторичного цементита, который повышает твердость и износостойкость режущего инструмента. Если заэвтектоидную сталь нагреть выше критической точки Аст, то после закалки получится дефектная структура грубоигольчатого мартенсита.
Время нагрева зависит от размеров детали и теплопроводности стали, и его обычно определяют экспериментально. Для определения времени нагрева в справочниках приведены также полуэмпирические формулы.
Режим охлаждения при закалке должен исключать по возможности возникновение больших остаточных закалочных напряжений, но в то же время он должен обеспечить необходимую глубину закаленного слоя.
Отпуск
Отпуском называется нагрев закаленной стали до температур ниже критической точки Ас1, выдержка при этой температуре с последующим охлаждением (обычно на воздухе). Отпуск является окончательной термической обработкой.
Целью отпуска является изменение строения и свойств закаленной стали: повышение вязкости и пластичности, уменьшение твердости, снижение внутренних напряжений.
С повышением температуры нагрева прочность обычно уменьшается, а удлинение, сужение, а также ударная вязкость растут. Температуру отпуска выбирают, исходя из требуемой прочности конкретной детали.
В зависимости от температуры нагрева различают три вида отпуска: низкотемпературный, среднетемпературный и высокотемпературный.
При низкотемпературном отпуске закаленную сталь нагревают до (150 – 250)°С. После соответствующей выдержки при этой температуре (обычно 1 - 3 ч) в детали получают структуру отпущенного (кубического) мартенсита. При низком отпуске частично снимаются закалочные напряжения. Если в стали было значительное количество остаточного аустенита, то в результате его превращения в кубический мартенсит твердость после низкого отпуска может увеличиться на 2 - 3 единицы HRС.
Низкий отпуск применяют для инструментальных сталей, после цементации, поверхностной закалки и т.д.
При среднетемпературном отпуске закаленную сталь нагревают до (350 – 400)°С. В результате получается структура троостита (бейнит). После такого отпуска в изделиях получается сочетание сравнительно высокой твердости (HRC 40 - 45) и прочности с хорошей упругостью и достаточной вязкостью. Поэтому среднему отпуску подвергают пружины и рессоры.
При высокотемпературном отпуске закаленные изделия нагревают до (450 – 650)°С. После такого нагрева и соответствующей выдержки в изделиях получается структура сорбита. В отличие от сорбита, образующегося после нормализации, когда цементит пластинчатый, после высокого отпуска цементит приобретает зернистую форму. Это существенно повышает ударную вязкость при одинаковой (или даже более высокой) твердости по сравнению с нормализованной сталью. Поэтому такой отпуск применяют для деталей машин, испытывающих при эксплуатации ударные нагрузки. Закалку с высоким отпуском часто называют улучшением.
5.5. ПРОКАЛИВАЕМОСТЬ
Под прокаливаемостью подразумевают глубину проникновения закаленной зоны.
Несквозная прокаливаемость объясняется тем, что при закалке деталь охлаждается быстрее с поверхности и медленнее - в сердцевине. При закалке скорость охлаждения распределяется по сечению так, как это показано на рис. 235-
пунктирной линией: у поверхности скорость охлаждения максимальная, в центре - минимальная. Если критическая скорость закалки равна величине, показанной на этой схеме горизонтальной пунктирной линией, то деталь не прокаливается насквозь, и глубина закалки будет равна заштрихованному слою (рис. 235, а).
Очевидно, с уменьшением критической скорости закалки увеличивается и глубина закаленного слоя, и если Uк будет меньше скорости охлаждения в центре, то это сечение закалится насквозь. Если же сечение велико и скорость охлаждения на поверхности меньше, то при данном способе закалки сталь не закалится даже на поверхности.
Следовательно, чем меньше Uк, тем глубже прокаливаемость. Прокаливаемость, как и Uк, тесно связана со скоростью превращения аустенита в перлит и, следовательно, с расположением кривой начала превращения на С - диаграмме.
Предположим, что имеем цилиндрическую деталь. Кривые охлаждения центра, поверхности и сечения, расположенного на половине радиуса от поверхности, наложенные на С - диаграмму, показаны на рис. 235, б. Для данной стали при данных условиях охлаждения на поверхности получится мартенситная структура, в центре - перлитная, на расстоянии половины радиуса получится мартенсит + тростит.
Закаливаемость - способность стали принимать закалку, т.е. приобретать при закалке детали высокую твердость. Закаливаемость определяется содержанием углерода в стали. Низкоуглеродистые стали (до 0,20 % С) практически не закаливаются, так как при закалке их твердость не повышается.
Цементация
Обычно при химико - термической обработке деталь помещают в среду, богатую элементом, который диффундирует в металл.
В случае газового окружения (наиболее частный случай) при химико-термической обработке происходят три элементарных процесса.
1. - диссоциация. Протекает в газовой среде и состоит в распаде молекул и образовании активных атомов диффундирующего элемента. Например
2 СО → СО2 + С или NH3 → 3Н + N.
При этом образуются активные атомы углерода и азота, способные растворяться в металле. Степень распада молекул газа (%) называется степенью диссоциации.
2. - абсорбция. Происходит на границе газ-металл и состоит в поглощении (растворении) поверхностью свободных атомов. Этот процесс возможен только в том случае, если диффундирующий элемент В способен растворяться в основном металле А.
Проникновение насыщающего элемента вглубь - диффузия. Она характеризует третий процесс.
В результате образуется диффузионный слой на поверхности которого концентрация диффундирующего элемента наибольшая; по мере удаления от поверхности концентрация падает (рис. 256), глубина проникновения (у на рис. 256) будет представлять собой толщину слоя.
При цементации происходит поверхностное насыщение стали углеродом, в результате чего получается высокоуглеродистый поверхностный слой. Так как для цементации берут низкоуглеродистую сталь, то сердцевина остается мягкой и вязкой, несмотря на то что после цементации сталь подвергается закалке.
Различают два вида цементации: твердую и газовую.
При твердой цементации детали запаковывают в ящик, наполненный карбюризатором - науглероживающим веществом. Карбюризатором является древесный уголь с различными добавками. В ящике, в промежутках между кусочками угля, имеется воздух, кислород которого при температуре процесса (900 - 950° С) соединяется с углеродом, образуя окись углерода СО (образуется именно СО, а не С02, из-за недостатка кислорода).
Однако при температурах процесса окись углерода неустойчива и при контакте с железной поверхностью разлагается по реакции
2СО → СО2 + С
с образованием атомарного углерода, который поглощается поверхностью.
Газовая цементация осуществляется в стационарных или методических (непрерывно действующих) конвейерных печах. Цементирующий газ приготавливают отдельно и подают в цементационную реторту.
Практически цементацию проводят при 900 - 930° С, но имеется тенденция повысить температуру цементации до 950 - 970° С и выше.
Дата добавления: 2018-04-15; просмотров: 875; Мы поможем в написании вашей работы! |
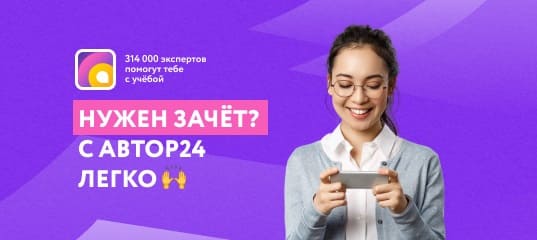
Мы поможем в написании ваших работ!