СПОСОБЫ ГОРЯЧЕЙ ОБЪЕМНОЙ ШТАМПОВКИ
Так как характер течения металла в процессе штамповки определяется типом штампа, то этот признак можно считать основным для классификации способов штамповки. В зависимости от типа штампа выделяют штамповку в открытых и закрытых штампах.
Штамповка в открытых штампах (рис. 7, а) характеризуется переменным зазором между подвижной и неподвижной частями штампа. В этот зазор вытекает заусенец (облой), который закрывает выход из полости штампа и заставляет металл целиком заполнить всю полость. В конечный момент деформирования в заусенец выжимаются излишки металла, находящиеся в полости, что позволяет не предъявлять особо высоких требований к точности заготовок по массе. Заусенец затем обрезается в специальных штампах.
рис. 7. Схемы штамповки в открытых и закрытых штампах:
1 – заусенечная канавка
Штамповка в закрытых штампах (рис. 7, б, в) характеризуется тем, что полость штампа в процессе деформирования остается закрытой. Зазор между подвижной и неподвижной частями штампа при этом постоянный и небольшой, так что образование заусенца в нем не предусмотрено. Устройство таких штампов зависит от типа машины, на которой штампуют. Например, нижняя половина штампа может иметь полость, а верхняя — выступ (на прессах), или наоборот (на молотах). Закрытый штамп может иметь не одну, а две взаимно перпендикулярные плоскости разъема, т. е. состоять из трех частей (рис. 7, в).
|
|
При штамповке в закрытых штампах необходимо строго соблюдать равенство объемов заготовки и поковки, иначе при недостатке металла не заполняются углы полости штампа, а при избытке размер поковки по высоте будет больше требуемого.
Листовая штамповка
Листовой штамповкой изготавливают детали с помощью штампов из листового материала, ленты или полосы из низкоуглеродистой и пластичной легированной стали, цветных сплавов и др.
В зависимости от толщины заготовки штамповку делят на тонколистовую (холодную) и толстолистовую (горячую) с толщиной деталей более 5 - 8 мм.
Листовой штамповкой изготовляют плоские и пространственные детали массой от долей грамма и размерами в доли миллиметра (секундная стрелка ручных часов), до деталей в десятки килограммов и размерами в несколько метров (облицовка автомобиля, самолета, ракеты).
Операции листовой штамповки делят на две группы:
1. Разделительные – отрезка, вырубка, пробивка;
2. Формоизменяющие – гибка, вытяжка, обжим, отбортовка, формовка.
Отрезка – это операция отделения части заготовки по незамкнутому контуру. Например разделение листа на полосы заданной ширины.
Вырубка – это операция отделения части заготовки по замкнутому контуру, причем отделяемая часть идет на деталь.
|
|
Пробивка - это операция отделения части заготовки по замкнутому контуру, причем отделяемая часть является отходом (получение отверстий).
Вырубку и пробивку осуществляют пуансоном и матрицей, конфигурации которых соответствуют конфигурации детали.
Для проведения процесса необходимо обеспечить:
1. Острые кромки пуансона и матрицы.
2. Радиальный зазор между матрицей и пуансоном (5 – 10% от толщины заготовки).
3. При вырубке деталей размер отверстия матрицы принимают равным размерам изделия. При пробивке отверстия размер пуансона равен размеру отверстия.
Гибка - это операция изменяющая направление оси заготовки. при изготовлении гибочного штампа необходимо учитывать величину упругой разгрузки изделия (пружинение).
Вытяжка без утонения стенки – это операция, превращающая плоскую заготовку в полое изделие (стакан) с толщиной стенки, равной толщине заготовки. Для снижения концентрации давлений на металл заготовки кромки пуансона и матрицы скругляют. Исходную заготовку для вытяжки получают с помощью вырубки.
Вытяжка с утонением стенки – это операция аналогична вышерассмотренной, однако радиальный зазор между пуансоном и матрицей берут меньше толщины стенки изделия, а также матрица имеет коническую рабочую поверхность.
|
|
Допустимое уменьшение толщины стенки заготовки находят из условия:
(S0 – толщина заготовки, S – толщина изделия)
обжим – это операция, при помощи которой производится уменьшение диаметра верхней части вытянутой детали. В данной операции рабочим инструментом является матрица, в которую заталкивается обжимаемая заготовка.
Во избежание образования складок на обжимаемом крае заготовки и осадки ее цилиндрической части соблюдают следующее условие:
Отбортовка – это операция, с помощью которой из плоской заготовки с отверстием путем раздачи отверстия получают горловину (борт).
Во избежание образования трещин по краю отверстия горловины допустимое увеличение диаметра горловины определяют из соотношения:
где КОТ – коэффициент отбортовки,
dД – диаметр отверстия детали,
dОТВ - диаметр отверстия заготовки.
формовка – это операция, изменяющая форму заготовки, а также, в некоторых случаях, и толщину стенки посредством местных деформаций. (Изготовление ребер жесткости, местное увеличение размеров заготовки и т.д.).
|
|
ВОЛОЧЕНИЕ
При волочении заготовку протягивают через постепенно сужающееся отверстие в инструменте, называемом волокой. Волочение, как правило, осуществляют в холодном состоянии. Исходными заготовками служат прокатанные или прессованные прутки и трубы из стали, цветных металлов и их сплавов.
Волочение труб можно выполнять без оправки (для уменьшения внешнего диаметра) и с оправкой (для уменьшения внешнего диаметра и толщины стенки). На рис. 8, а показана схема волочения трубы 1 на короткой удерживаемой оправке 3. В этом случае профиль полученной трубы определяется зазором между волокой 2 и оправкой 3.
Рис. 8. Схема волочения трубы (а)
и примеры профилей, получаемых волочением (б)
При волочении сплошного и полого профилей площадь поперечного сечения заготовки уменьшается, а длина увеличивается.
Волочением обрабатывают стали и цветные металлы: медь и ее сплавы, алюминий и его сплавы и др. Сортамент изделий, изготовляемых волочением, очень разнообразен: проволока диаметром 0,002—5 мм и фасонные профили, примеры которых показаны на рис. 8, б (призматические и фасонные направляющие; сегментные, призматические и фасонные шпонки; шлицевые валики; и т. д.). Волочением калибруют стальные трубы диаметрами от капиллярных до 200 мм, стальные прутки диаметром 3—150 мм.
Основными параметрами процесса являются:
1. Коэффициент вытяжки и составляет до 1,3;
2. Обжатие и составляет до 35%;
3. Усилие волочения Р.
при волочении необходимо соблюдать условие . Где
- предел текучести обрабатываемого материала, F0, l0 – исходные сечения и длина, F, l – после волочения.
Волочильный инструмент изготавливают из чугуна, инструментальных сталей, твердых сплавов, а также из естественного алмаза для получения проволоки до 1,2 мм.
Волоки по конструкционному исполнению подразделяют на:
1. Цельные нерегулируемые;
2. Составные регулируемые;
3. Роликовые регулируемые.
В процессе волочения между рабочей поверхностью волоки и внешней поверхностью заготовки возникают значительные силы трения, приводящие:
1. к возрастанию усилия волочения;
2. к задиру поверхности заготовки.
Для снижения сил трения применяют:
1. Обильную смазку;
2. Предварительное покрытие заготовки (омеднение);
3. Роликовую матрицу (трение качения).
В качестве оборудования для осуществления процесса волочения используют волочильные станы. Сила тяги цепного волочильного стана достигает 150 – 200 тонн.
Прессование
При прессовании металл выдавливается из замкнутой полости через отверстие, соответствующее сечению прессуемого профиля. Прессованием изготовляют как сплошные, так и полые профили (рис. 9, а). для этого в заготовке предварительно получают сквозное отверстие, как правило на том же прессе. В процессе прессования при движении пуансона 1 с пресс-шайбой 5 металл заготовки 2 выдавливается в зазор между матрицей 3 и иглой 4. Прессование по данной схеме называют прямым. Значительно реже применяют обратное прессование. При прямом прессовании направление движения пуансона совпадает с течением металла, при этом затрачивается большое усилие прессования. при обратном прессовании значительно усложняется конструкция пуансона.
рис. 9. Схема прессования полого профиля (а)
и примеры прессованных профилей (б)
характеристика процесса
Прессованием изготовляют изделия разнообразного сортамента из цветных металлов и сплавов - прутки диаметром 3 - 250 мм, трубы диаметром 20 - 400 мм со стенкой толщиной 1,5 - 12 мм и другие профили (рис. 3.48, б). Прессование осуществляют при температурах горячей обработки давлением на горизонтальных прессах, с усилием до 1500 Т.
Основным преимуществом прессования является получение сложных профилей, высокой точности по сравнению с прокаткой.
К недостаткам прессования следует отнести:
1. значительный износ инструмента,
2. большие отходы металла: до 40 % пресс-остатка от исходной массы заготовки (при прессовании труб большого диаметра, более 250мм).
СВАРОЧНОЕ ПРОИЗВОДСТВО
Сварка — технологический процесс получения неразъемных соединений материалов посредством установления межатомных связей между свариваемыми частями при их местном или общем нагреве, или пластическом деформировании, или совместным действием того и другого. Сваркой соединяют однородные и разнородные металлы и их сплавы, металлы с некоторыми неметаллическими материалами (керамикой, графитом, стеклом и др.), а также пластмассы.
К термическому классу относятся виды сварки, осуществляемые плавлением с использованием тепловой энергии (дуговая, плазменная, электрошлаковая, электронно-лучевая, лазерная, газовая и др.
К термомеханическому классу относятся виды сварки, осуществляемые с использованием тепловой энергии и давления (контактная, диффузионная и др.).
К механическомуклассу относятся виды сварки, осуществляемые с использованием механической энергии и давления (ультразвуковая, взрывом, трением, холодная и др.).
Свариваемость — свойство металла или сочетания металлов образовывать при установленной технологии сварки соединение, отвечающее требованиям, обусловленным конструкцией и эксплуатацией изделия.
ДУГОВАЯ СВАРКА.
СУЩНОСТЬ ПРОЦЕССА
Источником теплоты при дуговой сварке служит электрическая дуга, которая горит между электродом и заготовкой. В зависимости от материала и числа электродов, а также способа включения электродов и заготовки в цепь электрического тока различают следующие способы дуговой сварки: сварка неплавящимся (графитным или вольфрамовым) электродом 1 дугой прямого действия 2 (рис. 5.1, а), при которой соединение выполняется путем расплавления
Рис. 5.1. Схемы дуговой сварки
только основного металла 3 либо с применением присадочного металла 4; сварка плавящимся (металлическим) электродом 1 дугой прямого действия 2 (рис. 5.1, б) с одновременным расплавлением основного металла 3 и электрода, который пополняет сварочную ванну жидким металлом.
РУЧНАЯ ДУГОВАЯ СВАРКА
Ручную дуговую сварку выполняют сварочными электродами, которые вручную подают в дугу и перемещают вдоль заготовки. В процессе сварки металлическим покрытым электродом (рис. 5.7) дуга 8 горит между стержнем электрода 7 и основным металлом 1. Стержень электрода плавится, и расплавленный металл каплями стекает в металлическую ванну 9. Вместе со стержнем плавится покрытие электрода 6, образуя газовую защитную атмосферу 3 вокруг дуги и жидкую шлаковую ванну 4 на поверхности расплавленного металла. Металлическая и шлаковая ванны вместе образуют сварочную ванну. По мере движения дуги сварочная ванна затвердевает и формируется сварной шов 3. Жидкий шлак после остывания образует твердую шлаковую корку 2.
Рис. 5.7. Схема процесса сварки
металлическим покрытым электродом
Дата добавления: 2018-04-15; просмотров: 572; Мы поможем в написании вашей работы! |
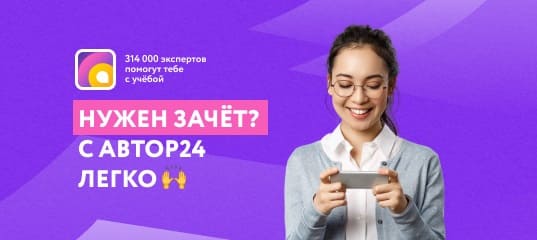
Мы поможем в написании ваших работ!