Технология обработки деталей резанием
Обработка металлов резанием – это процесс срезания режущим инструментом с поверхности заготовки слоя металла в виде стружки для получения необходимой геометрической формы, точности размеров, взаиморасположения и шероховатости поверхностей детали. Чтобы срезать с заготовки слой металла, необходимо режущему инструменту и заготовке сообщить относительные движения.
Обработка заготовок на токарных станках
Среди различных способов изготовления деталей машин применяют обработку резанием: точение, сверление, фрезерование, шлифование и т.д.
Обработка резанием заключается в образовании новых поверхностей путем деформирования и последующего отделения поверхностных слоев материала с образованием стружки.
Валы, шкивы, зубчатые колеса и многие другие детали, называемые телами вращения, можно изготавливать на токарных станках.
Инструментами для обработки заготовок служат резцы, сверла, зенкеры, развертки, метчики и др.
Токарной обработкой (точением) можно получить детали с цилиндрическими, коническими, фасонными и плоскими поверхностями, а также нарезать резьбу, делать фаски и галтели (рис. 1).
|
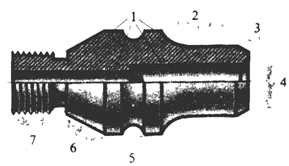
Режущий инструмент
В зависимости от геометрии получаемой поверхности существуют следующие типы резцов:
|
|
1. проходной,
2. подрезной,
3. отрезной,
4. прорезной,
5. фасонный,
6. резьбовой,
7. расточной.
Классификация резцов по назначению
а - проходной прямой, б - проходной отогнутый, в -проходной упорный, г - подрезной, д - отрезной, е -прорезной, ж - фасонный, з - резьбовой, и - расточной проходной, к - расточной упорный
режущую часть резцов изготавливают из быстрорежущей стали, твердых и сверхтведых материалов.
При обтачивании наружных и растачивании внутренних поверхностей тел вращения получают следующие геометрические параметры поверхности:
1. черновое – Ra = 12,5 – 50 мкм, JT 14-12
2. получистовое – Ra = 3,2 – 12,5 мкм, JT 12-10
3. чистовое – Ra = 0,8 – 3,2 мкм, JT 10 - 8
4. тонкое – Ra = 0,1 – 0,8 мкм, JT 6 – 8 (JT7 для растачивания).
Следует учитывать, что при обработке наружных поверхностей квалитет точности будет на 1 класс выше, и величина шероховатости на (50 – 100)% меньше по сравнению с обработкой внутренних поверхностей при одинаковой операции (чистовой, тонкой и т.д.).
Дополнительные возможности токарных станков
1. нарезание внутренней резьбы метчиками. Максимальный диаметр резьбы составляет 20 мм, минимальный – 1 мм. По числу перьев различают трехперые и четырехперые метчики. По назначению метчики бывают ручные, машинные и гаечные с удлиненным хвостовиком. Нарезание резьбы выполняют с использованием качающейся самовидвижной оправки, вставляемой в конусное отверстие пиноли задней бабки. Во втором варианте используют слесарный вороток, в который вставляют метчик. Кроме – того в резцедержатель устанавливают сверлильную державку с центром, вставляемым в отверстие хвостовика метчика, а для передачи (удержания метчика) крутящего момента в резцедержатель еще устанавливают упорную планку.
|
|
2. Нарезание внешней резьбы за 1 ход диаметром от 1 до 52 (76) мм можно нарезать круглой плашкой (леркой). Для нарезания резьбы используют слесарный вороток (плашкодержатель), в который вставляют лерку. В начале нарезания резьбы плашкодержатель поджимают упором, закрепленном в резцедержателе, а рукоятку плашкодержателя упирают в планку, закрепленную в резцедержателе.
3. Растачивание глубоких отверстий с помощью борштанг (расточных оправок). Применяют для растачивания отверстий диаметром 80 мм и более. В качестве РИ используют расточные резцы, закрепляемые в оправках, которые чаще всего устанавливают в резцедержателе.
|
|
4. Сверление отверстий диаметром до 30 мм. РИ закрепляют в пиноли задней бабки и подают вручную, вращением маховика. Перед сверлением подрезанный торец заготовки засверливают сверлом большего диаметра с тем условием, чтобы не произошло увода оси сверла. В случае, если обработка отверстия сверлом является окончательной, то необходимо учитывать величину разбивки отверстия, которая составляет Р0 = (0,05 – 0,12)dc. Где dc – диаметр сверла.
5. Зенкерование отверстий. Не устраняет увод от оси отверстия. Применяют цельные хвостовые зенкеры d = 10 – 32 мм, с 3-мя режущими кромками, и насадные (цельные и сборные со вставными ножами из твердого сплава). Диаметр = 32 – 100 (120) мм, число режущих кромок (РК) – 4. Зенкеры или оправки закрепляют в пиноли задней бабки.
6. Развертывание отверстий. Также не устраняет увод от оси с предыдущей операции. По способу применения развертки подразделяют на ручные и машинные. В свою очередь машинные развертки по способу крепления на станке делятся на цельные хвостовые развертки, диаметром 6 – 32 мм, и сборные насадные, диаметром 32 – 100 мм. Существуют также регулируемые (механические) развертки с изменением диаметра в узком диапазоне. РК=6-16, в зависимости от диаметра РИ.
Дата добавления: 2018-04-15; просмотров: 348; Мы поможем в написании вашей работы! |
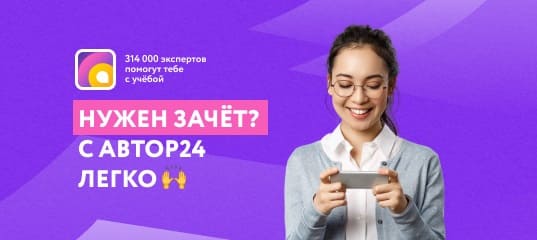
Мы поможем в написании ваших работ!