Литье в кокиль (в металлические формы).
ВОПРОСЫ
Для проведения дифференцированного зачета по дисциплине
«Технология приборостроения»
СТР. | |
1. Типы производства. Их краткая характеристика. | 2 |
2. Литье. Литье в песчаные формы, литье под давлением, литье по выплавляемым моделям. | 2 |
3. Литье в оболочковые формы, литье в кокиль, центробежное литье, требования к литейным материалам. | 3 |
4. Обработка давлением: гибка, вытяжка, вырубка и пробивка. | 3 |
5. Обработка давлением: объемная штамповка, выдавливание, осадка. | 4 |
6. Получение деталей из пластмасс: прямое и литьевое прессование. | 4 |
7. Получение деталей из пластмасс: литье под давлением, пневматическое формование. | 4 |
8. Электроэрозионная обработка, анодно-механическая обработка. | 5 |
9. Ультразвуковая и электронно-лучевая обработка, электро-химические методы обработки. | 5-6 |
10. Покрытия металлические и неметаллические неорганические покрытия. | 6 |
11. Методы формирования защитного рисунка печатной схемы. | 7 |
12. Опишите процессы, используемые при изготовлении печатных плат (химическая и электрохимическая металлизация, травление меди с пробельных мест, механическая обработка печатных плат). | 8 |
13. Изготовление многослойных печатных плат: метод металлизации сквозных отверстий, метод попарного прессования. | 8 |
14. Типовой технологический процесс изготовления плат комбинированным негативным методом. | 9 |
15. Типовой технологический процесс изготовления плат комбинированным позитивным способом. | 10 |
16. Отличительные признаки резьбовых соединений, детали для выполнения резьбовых соединений. | 11 |
17. Провода монтажные, принцип выбора диаметра проводов и типа изоляции. | 12 |
18. Технология жгутового монтажа. | 13 |
19. Подбор припоев и флюсов для пайки, требования к паяным соединениям. | 13 |
20. Назовите и дайте характеристику корпусам для поверхностного монтажа | 14-15 |
21. Состав и изготовление припойных паст. Методы нанесения паст на плату. | 15 |
22. Пайка SMD-компонентов двойной волной припоя, проблемы. Возникающие при пайке и пути их устранения. | 15 |
23. Пайка SMD-компонентов путем расплавления припойной пасты: пайка горячим газом, технология пайки в паровой фазе | 16 |
24. Классификация методов герметизации и их применение в производстве РЭА. | 16 |
25. Лакирование печатных узлов. | 17 |
26. Назначение и особенности регулировочных работ. | 17 |
27. Назначение и виды испытаний. | 18 |
28. Пути накопления электростатического заряда и методы защиты приборов от воздействия статического электричества. | 18 |
|
|
№1 Единичное производствохарактеризуется широкой номенклатурой изготавливаемых изделий и малым объемом их выпуска.
|
|
Для серийного производствахарактерна ограниченная номенклатура изделий, изготавливаемых периодически повторяющимися партиями при сравнительно большом объеме выпуска. В зависимости от количества изделий в партии и значения К3.0. серийное производство может быть мелкосерийным и крупносерийным.
Массовое производствоотличается узкой номенклатурой и большим объемом выпуска изделий, непрерывно изготавливаемых в течение продолжительного времени. При этом используется специальное высокопроизводительное оборудование, которое располагается по ходу технологического процесса, широко применяются автоматические линии и автоматизированные производственные системы, управляемые ЭВМ. Требуемая точность достигается методами автоматического получения размеров на настроенном оборудовании. Только в отдельных случаях применяется селективная сборка, обеспечивающая групповую взаимозаменяемость.
Квалификация рабочих в массовом производстве ниже, чем в единичном, так как на автоматизированном оборудовании могут работать рабочие-операторы сравнительно низкой квалификации.
№2Литье- это процесс изготовления деталей заливкой расплавленного материала в форму.
|
|
Литье в песчаные формы
Расплавленный металл заливают в формы, изготовленные из песчано-земляной массы ( 80...90% песка, глина и другие компоненты). Формы получают, используя разъемные деревянные модели, повторяющие конфигурацию деталей. Метод характеризуется относительной простотой производства, низким качеством поверхности деталей, значительными искажениями геометрической формы, вследствие коробления, наличием усадочных раковин и значительными припусками на последующую механическую обработку.
Литье под давлением.
Расплав заливают в металлические формы многоразового использования, при значительном избыточном давлении, создаваемом специальными литьевыми машинами поршневого или компрессионного принципа действия. Это наиболее совершенный способ литья, позволяющий получать непосредственно готовые детали или заготовки с минимальным объемом операций последующей механической обработки. Основные недостатки: пористость массы заготовки из-за высокой скорости заполнения формы.
Литье по выплавляемым моделям.
Используемые при этом способе "неразъемные" формы обеспечивают получение отливок повышенной точности и сложности. Для получения формообразующей полости используют выплавляемые модели, изготавливаемые методом литьевого прессования из специальной модельной массы, имеющей низкую температуру плавления (воск, парафин, церезин, канифоль, и т. д.).
|
|
Обычно используют многогнездовые формы, которые изготавливаются следующим образом.
Ø Несколько выплавляемых моделей и отдельно изготовленная литниковая система соединяются в единый блок путем оплавления мест соединения.
Ø Полученный модельный блок покрывают жаропрочной пленкой, окуная в водный раствор жидкого стекла, содержащий каолин и графит, после чего присыпают мелким кварцевым песком и сушат при комнатной температуре в течении нескольких часов. Такая операция повторяется 2-3 раза для получения слоя обмазки необходимой толщины.
Ø Затем модельный блок устанавливается в металлическую опоку, засыпается формовочной смесью и подвергается двухэтапной термической обработке. На первом этапе происходит выплавление модельной массы и сушка формовочной смеси при температуре 100...150оС. На втором этапе происходит выпаривание остатков модельной массы и оплавление слоя обмазки при температуре 800...850ос.
Заливку расплава производят в предварительно нагретую форму методом закрытого перелива, создавая небольшое избыточное давление (4...5 атм.) для лучшего заполнения формы.
№3Литье в оболочковые формы
Для получения оболочковой формы изготавливают разъемную металлическую модель, повторяющую конфигурацию детали с незначительными припусками. Каждую половину модели с элементами литниковой системы устанавливают на металлическом основании и покрывают смесью мелкого кварцевого песка с термореактивными компонентами. Под действием температуры (до250ос) термореактивные соединения оплавляются и, растекаясь по поверхности модели, склеивают частицы песка, образуя пластичную оболочку. После остывания полуоболочки снимаются с модельной плиты и соединяются между собой, образуя внутреннюю формообразующую полость. После этого форма устанавливается в металлической опоке, заполняемой формовочной смесью.
Литье в кокиль (в металлические формы).
Данный способ литья предполагает свободную заливку расплава в металлические формы многоразового использования, называемые кокилями. Для снижения термического удара при заливке кокиля предварительно разогревают до температуры 250°С с помощью встроенных или автономных нагревателей. Данный метод относится к прогрессивным, так как имеет относительно высокую производительность, меньший расход жидкого металла (на 20...30%), за счет более рациональной литниковой системы. Основные недостатки: высокая стоимость формы и ограничение сложности формы отливки.
Кроме перечисленных существуют и другие методы формирования литых деталей.
К ним относят центробежное литье, реализуемое заливкой расплава во вращающуюся форму.формообразование и кристаллизация массы отливки происходит под давлением центробежной силы, поэтому отливка получается беспористой и без шлаковых включений. Литье намораживанием применяется для изделий постоянного профиля путем вытягивания из расплава через профилированное отверстие в поплавке. Затравка изготавливается из того же материала, что и расплав.
Требования к литейным материалам. Материалы должны обладать: 1) жидкой текучестью 2) минимальным газопоглощением 3) миним. Присадки 4) незначительным внутренним напряжением. Наиболее распространенными являются следующие сплавы: магниевые, латуниевые, цинковые, стали.
№4Обработкой давлением называют процессы переработки материалов в изделие, при которых исходная заготовка под действием давления пластически деформируется и приобретает новые заданные формы и размеры или заданные физические свойства поверхности.
Гибка- это процесс обработки давлением, в результате которого достигается изменение кривизны поверхности плоских листовых и прямолинейных профильных заготовок.
Для гибки используют штампы с жесткой матрицей и пуансоном или эластичной матрицей и жестким пуансоном.Пригибке в жестком штампе матрица и пуансон имеют форму заготовки, которую она должна приобрести после гибки. В штампе с эластичной матрицей форму, которую необходимо придать заготовке имеет только пуансон.
Вытяжка - это процесс формообразования полых деталей коробчатой, цилиндрической и других форм из плоских листовых заготовок.
По характеру протекания процесса различают два способа вытяжки: без утонения стенок и с утонением стенок. В первом случае зазор между пуасоном и матрицей делают равным толщине листа заготовки. По мере движения пуансона заготовка втягивается в матрицу, увеличивается длина цилиндрической части и уменьшается диаметр плоского фланца заготовки. При втягивании заготовки в матрицу возможно складкообразование материала. Для его предотвращения применяют прижим. Операция характеризуется коэффициентом вытяжки m = d/dз,где dз - диаметр заготовки, d -диаметр формируемой цилиндрической части.
При вытяжке с утонением стенок зазор между пуансоном и матрицей делается меньше толщины материала. В результате формуется изделие с толщиной дна, равной толщине листовой заготовки и более тонкими стенками. Операция характеризуется коэффициентом утоненияm=s/so,где so - толщина листовой заготовки, s - толщина стенки изделия .
Коэффициенты вытяжки и утонения зависят от механических свойств материала, толщины листа, размеров и формы изделия и т.д. их оптимальные значения устанавливаются практикой.
Вырубка и пробивка относятся к раздельным операциям выполняемым в штампах. Разделение материала осуществляется острыми кромками пуансона и матрицы (рис. 2.2.6). Обычно вырубку осуществляют без прижима заготовки, прижим используют при чистой вырубке. Вырубку и пробивку производят в металлических и неметаллических материалах, толщиной 0,5 - 20 мм с поверхностью среза, перпендикулярно плоскости листа.
№5 Обработкой давлением называют процессы переработки материалов в изделие, при которых исходная заготовка под действием давления пластически деформируется и приобретает новые заданные формы и размеры или заданные физические свойства поверхности.
Объемной штамповкой называют группу технологических операций, в которых изменение формы и размеров заготовки достигается пластическим деформированием всей массы заготовки.
Процессы объемной штамповки отличаются высокими скоростями деформирования и достаточно высокой точностью размеров и формы изделий.
Технологический процесс штампованных деталей включает:заготовительный этап, штамповку (формообразование), дополнительные обработки (механические, термические и т. п.).
Точность размеров штампованных деталей составляет 10...12 квалитет для обычных штампов; 6...9 квалитет для специальных штампов. Следует помнить, чем тоньше лист заготовки, тем выше точность.
Предельная производительность штамповки определяется быстродействием прессов. Для малых прессов - 1200...2000 ходов/мин., для крупных - 350 ходов/мин. При этом основными проблемами являются механизированная подача заготовок и удаление готовых изделий и отходов.
Осадка выполняется штампами с плоскими или плоскими кольцевыми пуансоном и матрицей. В результате пластической деформации уменьшается высота и увеличивается диаметр заготовки.
№6Прессование
Технологический процесс прессования заключается в том, что под влиянием нагрева, и давления пресс-материал заполняет рабочее пространство пресс-формы и полимеризуется в твердое состояние. Этот способ обработки применяется для большинства пластмасс (фенопласты, аминопласты и пластмассы на основе кремнийорганической смолы).Прессование подразделяется на два вида: прямое и литьевое.
Прямое прессование.При прямом прессовании пресс-материал загружается непосредственно в формообразующую полость или загрузочную камеру горячей пресс-формы, после чего подвергается Давлению пресса. Нагретый пресс-материал размягчается, заполняет гнезда пресс-формы и остается в ней определенное время до полного затвердевания. После этого пресс-форму открывают и извлекают отформованную деталь.
Прямым прессованием изготавливают уплотнительные прокладки, изоляционные колпачки и шланги, а также различные толстостенные детали (втулка, конусы, раструбы).
Литьевое прессование. Литьевое прессование отличается от рассмотренного выше прессования конструкцией пресс-формы, которая имеет дополнительную загрузочную камеру, соединенную с матрицей тонким литниковым каналом.Оно осуществляется, как правило, на гидравлических прессах. Материал загружается в накладную камеру, нагревается от стенок камеры до полужидкого состояния и с большой скоростью нагнетается пуансоном в полость матрицы. Режимы литьевого прессования отличаются от прямого прессования большим временем выдержки и большим (на 10—30%) давлением.
К преимуществам литьевого прессования относятся: получение в деталях глубоких отверстий малого диаметра, высокая точность деталей и возможность заформовывать в изделия тонкую арматуру. К недостаткам относятся: сложная и дорогостоящая пресс-форма и большой расход материала (на литники).
№7Литье под давлением
Применяется при изготовлении сложных деталей из термопластических масс с большим количеством арматуры и сложной конфигурации. Оно производится на специальных машинах, которые называются инжекционными. Дозировка прессового материала, нагрев, нагнетание его в пресс-форму, выдержка, разъем пресс-форм и выталкивание изделий в современных машинах производится автоматически. Поэтому данный способ изготовления пластмассовых изделий является одним из самых производительных.На рисунке 2.3.2 показана схема инжекционной машины. В бункер 3 засыпается пресс-порошок 4, попадающий в цилиндр 6, где он сжимается поршнем 5 и проталкивается к литниковому мундштуку 8, Под влиянием обогревателя 7 пресс-порошок плавится и через мундштук проталкивается в пресс-форму 2, образуя изделие 1. Обычно пресс-форма имеет температуру 30—40°С, которая поддерживается охлаждающей водой. Это способствует быстрому затвердеванию деталей. Материалом для изготовления их служат: полистирол, полиэтилен, этилцеллюлоза и др.
Пневматическое формование.
Этим способом изготавливают детали из листовых термопластических материалов. Сущность процесса состоит в том, что разогретый лист материала приобретает форму матрицы под действием вытяжного штампа или под влиянием вакуума.
№8Электроэрозионная обработка (ЭЭО).
1-инструмент, 2-деталь.
Этот метод основан на отображении формы инструмента на заготовке под действием электрической энергии.
ЭЭО целесообразна для изготовления деталей из токоведущих материалов, которые трудно обрабатываются обычными методами, наиболее эффективна при изготовлении изделий сложной формы.
О сути процесса. Электроды - инструмент и заготовка - закреплены оснасткой станка и не соприкасаются друг с другом. Генератор задает периодичность и напряженность электрического поля вокруг электродов. Во время процесса электроискрового воздействия серия периодических электрических разрядов снимает тончайший слой материала с заготовки. Пространство между электродами заполнено жидким диэлектриком.
В точке, где напряженность электрического поля достигает максимума, происходит электрический разряд - молния в "микроатюре". Этот процесс приводит к моментальному плавлению микрослоев вещества у электрода. При исчезновении электрического поля внезапное снижение температуры приводит к отрыву части материала с заготовки и к образованию на этом месте микроскопического кратера.
Функции диэлектрика
Электроизолирующая. Диэлектрик разделяет заготовку и электрод. Искровой разряд происходит в максима-льно узком промежутке меж заготовкой и электродом, что позв сделать процесс производит-ным и точным.
Ионизационная. Диэлектрик должен способствовать максимальному сужению искровой зоны, чтобы добиться высокой плотности энергии в этой зоне.
Охлаждающая. Искровой разряд имеет сверхвысокую температуру, поэтому диэлектрик должен остудить и электрод, и заготовку. Также важно увести металлические газы, образующиеся в процессе электроэрозии.
Промывочная. Чтобы избежать электрического пробоя диэлектрик должен эффективно удалять эродированные крупицы металла.
Для электродов используется медь, латунь чугун, сталь. Частота импульсов порядка 100 тыс. в сек. Эрозионный съем достигает 1000мм3/сек.(300 кв. мм/мин)
Дата добавления: 2018-04-15; просмотров: 432; Мы поможем в написании вашей работы! |
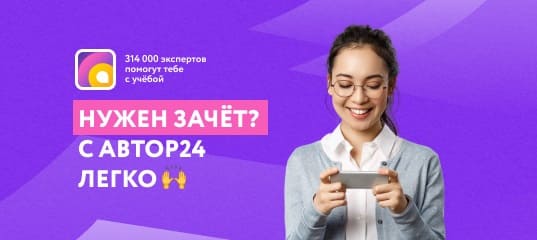
Мы поможем в написании ваших работ!