Степень точности и чистота обработки
Под точностью детали подразумевается степень соответствия фактически полученных при обработке размеров деталей расчетным. Точность детали определяется отклонениями реальной детали от заданной по форме, размерам, взаимному расположению поверхностей и шероховатости. Отступление данных показателей реальной детали от заданной является отклонением (погрешностью).
Точность обработки зависит от точности станков, приспособлений, инструмента, погрешности установки детали, тепловых деформаций и других факторов. Точность станков, измеренную в ненагруженном состоянии, называют геометрической точностью. Так, радиальное биение шпинделя фрезерного и токарного станка допускается не более чем 0,01—0,015 мм, а допустимая непараллельность и непрямолинейность направляющих токарного или продольно-строгального станка на длине 1000 мм не должна превышать 0,02 мм. В процессе эксплуатации станок подвергается износу, что приводит к увеличению погрешности детали. Механическую обработку деталей осуществляют в приспособлениях, погрешности изготовления которых также влияют на точность обработки деталей. Погрешности изготовления режущих инструментов, а также износ мерного (сверло, метчик и др.) и профильного (фрезы, фасонные резцы) инструментов также значительно влияют на точность изготовления деталей. При неточности изготовления или износе измерительного инструмента, погрешности его переносятся на обрабатываемое отверстие. Величина погрешности установки заготовки на станке зависит от точности и чистоты поверхности технологической базы заготовки и соответствующей поверхности станка или приспособления. Погрешность установки заготовки включает погрешность базирования заготовки и погрешность закрепления. Погрешность закрепления заготовки существенно влияет на точность обработки нежестких деталей; усилие для закрепления детали и место его приложения принимают таким, чтобы обеспечивалась требуемая точность обработки.
|
|
В процессе резания, а также вследствие нестабильного теплового режима в цехе, возникают тепловые деформации станка, инструмента и детали, что приводит к погрешностям обработки. Фактические погрешности в результате температурных деформаций велики и примерно равны допускам 2—3-го класса точности. Температурные изменения узлов станков составляют 10—160 С, а смещения узлов достигают 0 01—0,1 мм, что приводит к погрешностям обработки. Тепловая деформация (удлинение) резца из быстрорежущей стали, нагреваемого ё зоне резания до 800° С, достигает 0,05 мм, а следовательно, диаметр обрабатываемой детали при точении уменьшится на 0,1 мм. Все это необходимо учитывать при обработке точных деталей.
|
|
Гидравлические схемы.Условное обозначение устройств.
Гидравл́ическая (пневмат́ическая) сх́ема — это технический документ, содержащий в виде условных графических изображений или обозначений информацию о строении изделия, его составных частях и взаимосвязи между ними, действие которого основывается на использовании энергии сжатой жидкости (газа). Гидравлическая схема является одним из видов схем изделий и обозначаются в шифре основной надписи литерой «Г» (пневматическая — литерой «П»)
Стойкость и износ фрезы.
В результате периодических динамических и тепловых нагрузок происходит износ зубьев фрез. Характер износа фрез несколько отличен от износа резцов в силу того, что толщина срезаемого слоя при фрезеровании небольшая. В связи с этим износ происходит в основном по задним поверхностям hз (рис. 5.5) и является лимитирующим.
В процессе резания на снятие стружки с заготовки затрачивается определенная работа на преодоление упругих и пластических деформаций, а также трения по передней и задней поверхностям инструмента.
Дата добавления: 2018-04-04; просмотров: 380; Мы поможем в написании вашей работы! |
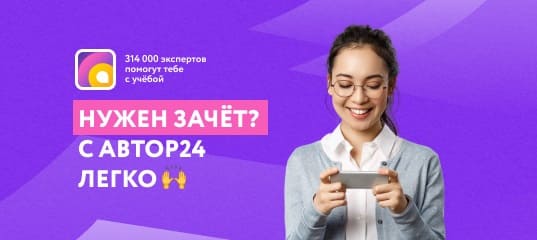
Мы поможем в написании ваших работ!