Методика назначения режимов резания
Назначение режимов резания основывается на определении глубины, подачи и скорости резания, при которых будет обеспечена наиболее экономичная и производительная обработка поверхности (при условии выполнения заданных технических требований) по точности и шероховатости обработанной поверхности.
Вначале выбирается глубина резания, затем максимально допустимая подача, а потом определяется скорость резания. Такой порядок выбора элементов режима резания определяется тем, что на количество выделяемого при резании тепла, а следовательно, на износ и стойкость резца глубина резания влияет в наименьшей, а подача и особенно скорость резания — в наибольшей степени.
Элементы режима резания должны выбираться так, чтобы режущие свойства инструмента и возможности металлорежущего станка (его мощность и другие динамические и кинематические характеристики) были использованы в достаточной степени. Поэтому для выбора оптимальных режимов резания необходимо знать не только материал обрабатываемой заготовки, но и материал и геометрические параметры резца, допустимую величину его износа, а также характеристики станка, намеченного для выполнения обработки.
Глубина резания в основном определяется припуском на обработку, который по возможности стремятся удалить за один проход.
Величина подачи определяется требуемым классом чистоты обработки. Величина подачи должна быть больше допустимой этим условием, а также жесткостью обрабатываемой заготовки, жесткостью и прочностью резца и прочностью механизмов станка. Определив силы резания, возникающие при выбранных глубинах резания и подачи, можно путем расчета проверить (на основе зависимостей, известных из сопротивления материалов) соответствие выбранного сечения стружки прочности и жесткости детали, резца и прочности механизма подачи станка.
|
|
Практически обычно такие расчеты производить приходится не часто, так как в соответствующих нормативах по выбору режимов резания даны значения подач в соответствии с размерами резцов и характеристик металлорежущих станков.
Скорость резания выбирается в соответствии с определенными значениями глубины резания, подачи и стойкости режущего инструмента, геометрических параметров режущей части. Скорость резания назначается по соответствующим нормативам режимов резания или подсчитывается по эмпирическим формулам.
После выбора всех трех элементов режима резания проверяется их соответствие мощности станка по формуле
N ст = (Pz * v)/(60*102*η) квт,
где Рz — сила резания в н (кГ);
v— скорость резания в м/мин;
η — коэффициент полезного действия станка.
|
|
Обычно в нормативах по режимам резания имеются готовые таблицы для определения мощности резания (без учета к. п. д. станка) при определенных значениях выбранного режима резания.
Основное время при точении и строгании.
Основное (технологическое) время при строгании и долблении плоскостей (рис. 297, а, б и в) определяется по формуле
Т0 = B / n ּ S ּ i мин,
где В — ширина строгания в мм; n— число двойных ходов в мин; S — прямолинейная, периодическая подача в мм/дв. х; i — число проходов, t — глубина резания в мм и h — припуск на обработку в мм.
Число проходов равняется отношению припуска на обработку к глубине резания, т. е.
i = h / t.
Число двойных ходов n, входящее в формулу основного времени, представляет собой число двойных ходов долбяка, равное числу оборотов вращающейся кулисы для долбежных станков, или число двойных ходов ползуна, равное числу оборотов кулисного камня для поперечнострогального станка, или число двойных ходов стола для продольнострогальных станков.
Каждый двойной ход совершается на пути 2L, где L — расчетная длина (рис. 297, а, б и в). Расчетная длина L = l + (l+ l2)мм,
где l — длина обрабатываемой поверхности в мм, l1 + l2 — величина перебега ползуна или стола в зависимости от типа станка в мм. Расчетная длина влияет на число двойных ходов. Величина перебега l1 + l2равна 30 ÷ 70 мм для поперечнострогальных станков и 100 ÷ 400 мм для продольнострогальных станков.
|
|
Ширина строгания В (рис. 297, б и в) равна
B = b + (b1 + b2) мм,
где b —ширина обрабатываемой поверхности в мм; b1—путь врезания в мм; b2 — путь перебега резца (обычно 2 ÷ 5 мм).
Путь врезания определяется по формуле
b1 = t ּ ctg φ,
где t — глубина резания в мм, φ — угол наклона главного режущего лезвия резца.
Дата добавления: 2018-04-04; просмотров: 2336; Мы поможем в написании вашей работы! |
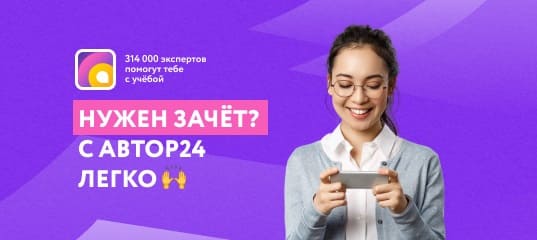
Мы поможем в написании ваших работ!