Й Государственный шарикоподшипниковый завод 18 страница. Л.Б. Кафенгауз в своей работе оставил нам как бы моментальную фотографию советской сталеплавильной промышленности в 1938 году
Л.Б. Кафенгауз в своей работе оставил нам как бы моментальную фотографию советской сталеплавильной промышленности в 1938 году. Производством стали занималось 30 крупных заводов, из которых выделялись своими мощностями:
▪ 1. Магнитогорский комбинат – 1 млн. 490,1 тысяч тонн;
▪ 2. Кузнецкий комбинат – 1 млн. 678,3 тысячи тонн;
▪ 3. Макеевский завод:
▪ 4. Цех № 1 – 829 тысяч тонн;
▪ 5. Цех № 2 – 423 тысячи тонн;
▪ 6. Завод им. Дзержинского:
▪ 7. Цех № 1 – 117,1 тысячи тонн;
▪ 8. Цех № 2 – 260,4 тысячи тонн;
▪ 9. Цех № 3 – 493,2 тысячи тонн;
▪ 10. Завод им. Петровского – 536,7 тысячи тонн;
▪ 11. «Азовсталь» – 476,7 тысячи тонн;
▪ 12. «Запорожсталь» – 703,6 тысячи тонн;
▪ 13. «Красный Октябрь» – 744,7 тысячи тонн;
▪ 14. Завод им. Сталина – 530,7 тысячи тонн стали[482].
Только эти заводы выдавали 8 млн. 283,5 тысячи тонн стали, или 46,7 % всей выплавки стали в Советском Союзе в 1938 году. Это были перечислены только заводы, мощность которых была свыше 400 тысяч тонн стали в год. Но кроме них были еще заводы, которые производили 200–300 тысяч тонн стали в год. Во всей крупной советской черной металлургии только один завод – ДЗМО имел годовую производительность менее 100 тысяч тонн стали в год, всего 58,3 тысячи тонн в 1938 году.
Большая часть выпускаемой стали производилась в мартеновских печах. Заводы, которые строились или переоборудовались в первую пятилетку, оснащались мартеновскими печами. В то время им отдавался однозначный приоритет как наиболее простым, дешевым и надежным агрегатам. Во вторую пятилетку стали говорить о развитии производства стали в конвертерах, по томасовскому и бессемеровскому способам. Освоение этих печей и способов производства стали позволяло освоить переплавку руд новых месторождений, получать более дешевую качественную или специальную сталь. Но несмотря на то что в развитие конвертерного производства вкладывались солидные суммы, тем не менее основой советского сталеплавильного производства остались мартеновские печи.
|
|
Это, кстати, вызывало некоторые сложности в работе сталеплавильной промышленности. Например, были очень высоки потери железа в процессе производства стали, и большая часть этих потерь приходилась именно на мартеновские печи. В 1937 году на тонну стали приходилось 168 килограммов потерь железа в виде брака, угара, скрапа. Всего в масштабах всей советской черной металлургии расходовалось 2 млн. 900 тысяч тонн железа вместо запланированного показателя в 1 млн. 900 тысяч тонн, то есть на 52 % больше планового показателя[483].
|
|
Производством качественной стали занимался 21 металлургический завод, из которых самым крупным был «Красный Октябрь», производивший 392,3 тысячи тонн качественной стали в год. Другие мощные заводы, с производством более 100 тысяч тонн качественной стали в год, выплавляли в 1938 году:
▪ 1. Кузнецкий комбинат – 119,5 тысячи тонн;
▪ 2. Сталинский – 105, 3 тысячи тонн;
▪ 3. Надеждинский – 150,3 тысячи тонн;
▪ 4. «Электросталь» – 150,6 тысячи тонн;
▪ 5. «Запорожсталь» – 133,4 тысячи тонн;
▪ 6. Златоустовский – 214,1 тысячи тонн;
▪ 7. «Серп и Молот» – 168 тысяч тонн.
Эти крупные заводы производили 1 млн. 433,5 тысячи тонн стали в год, или 78 % всего производства качественной стали, составившей в 1938 году 1 млн. 836,1 тысячи тонн[484].
Производство проката в 1937 году составило 15 млн. 600 тысяч тонн, в том числе на предприятиях ГУМПа – 11 млн. 386 тысяч тонн. В том числе было 38,4 % сортового проката, 23 % листа, 11,1 % рельс, 4,8 % балок[485]. По выпуску проката общий план на вторую пятилетку не составлялся. Планировалось производство рельс, особенно необходимых для масштабного железнодорожного строительства во второй пятилетке, и производство качественного проката, остронеобходимого для автотракторной и авиационной промышленности. План давал задание добиться уровня производства к концу второй пятилетки 1 млн. 300 тысяч тонн рельс. В 1937 году было выпущено 2 млн. 800 тысяч тонн, или на 40 % больше запланированного объема. По качественному прокату плановое задание предписывало в 1937 году произвести 2 млн. тонн качественного проката. Было реально произведено 2 млн. 276 тысяч тонн, на 13,8 % больше запланированного объема[486].
|
|
Представитель НКТП Л.Б. Кафенгауз в своей работе сопоставляет состояние черной металлургии Советского Союза, Германии и Соединенных Штатов.
В 1937 году по выплавке чугуна Советский Союз и Германия шли вровень: 16 млн. тонн – СССР и 15 млн. 960 тысяч тонн – Германия. США выплавляли 56 млн. 260 тысяч тонн чугуна, то есть превосходили в полтора раза СССР и Германию, вместе взятых. В одной только Пенсильвании производилось столько же чугуна, сколько во всем Советском Союзе – 16 млн. 723 тысячи тонн. Зато в Германии производилось больше стали, чем в СССР. 20 млн. 444 тысячи тонн, против 17 млн. 729 тысяч тонн. В этом нет ничего необычного. Германия к тому моменту являлась индустриальной страной уже более полувека и накопила большой запас железного лома, который пускался в передел на сталь. Потом немецкие сталеплавильные заводы лучше работали, нежели советские. Производство стали на них было налажено намного лучше, и намного лучше оно было освоено. В сталелитейном производстве не было таких крупных диспропорций, которые имелись в советской черной металлургии.
|
|
При выплавке стали в Германии использовалось гораздо больше передельного чугуна, чем в СССР. Немцы использовали 13 млн. 300 тысяч тонн чугуна и 7 млн. 144 тысячи тонн скрапа, тогда как в СССР использовалось для производства стали 9 млн. 632 тысячи тонн передельного чугуна и 6 млн. 937 тысяч тонн скрапа[487].
По производству проката Советский Союз уступал Соединенным Штатам: 15,6 млн. тонн против 36,7 млн. тонн, но опережал Германию, производившую 14,1 млн. тонн проката в 1937 году. В годы второй пятилетки в СССР целенаправленно развивалась и расширялась производственная база выпуска проката, и к концу второй пятилетки Советский Союз перестал нуждаться в закупках заготовок и готового проката за рубежом. А вот Германия продолжала крупномасштабные закупки заготовок и проката для своей промышленности. В 1934 году она закупила 1 млн. 108 тысяч тонн проката, а в 1935 году – 462 тысячи тонн[488].
В США большая часть проката приходилась на лист – 46,1 % от всего объема. В СССР производство листа составляло 23 %, а в Германии – 26,2 % от всего объема производства проката. Лист – это в первую очередь производство автомобилей и судостроение.
Но вот в сортовом прокате по доле его в производстве Советский Союз занимал первое место: 38,4 % всего объема. Чуть меньше, 37,8 % объема производства проката, имела Германия, и 16,4 % имели США. Сортовый прокат – это в первую очередь производство тяжелого оборудования и тяжелое машиностроение, хорошо развитое в СССР и в Германии. И по производству рельс в объеме производства Советский Союз держал первое место. На долю рельс приходилось 11,1 % выпуска проката. В Германии – 6,1 %, а в США рельсы практически не производились. Советский Союз активно развивал свои железные дороги, проводил во второй пятилетке масштабное железнодорожное строительство, переоборудование существующих магистралей, а вот в США железные дороги приходили в упадок из-за бурного развития автомобильного транспорта.
В конце второй пятилетки советская черная металлургия вошла в число ведущих мировых производителей черного металла и прочно закрепилась в первой тройке стран – производителей чугуна, стали и проката. Под советскую машиностроительную промышленность была подведена надежная металлургическая база.
Глава двенадцатая
Болезни пуска
«У нас было слишком мало технически грамотных людей. Перед нами стояла дилемма: либо начать с обучения людей в школах технической грамотности и отложить на 10 лет производство… либо приступить немедленно к созданию машин и развивать их массовую эксплуатацию… чтобы в самом процессе производства и эксплуатации обучать людей технике, вырабатывать кадры. Мы выбрали второй путь».
И.В. Сталин Из беседы с металлургами 26 декабря 1934 года
Построенные в первую пятилетку предприятия сразу же после пуска, после выдачи первой, пробной продукции вступали в очень сложный период – пусковой период.
До этого завод был, по существу, скопищем станков и оборудования, которые привезли, расставили по местам, подключили и отрегулировали. Но это еще не завод. Это пока еще только собранное вместе оборудование, которое еще предстоит заставить выпускать нужную продукцию.
Отдел кадров комплектует рабочие кадры завода. Привлекаются или готовятся те люди, кто будет на этих станках работать. Но даже станки и оборудование вместе с рабочими – это еще не завод. Заводом это скопище машин и людей станет только тогда, когда люди станут на станках изготовлять ту продукцию, ради выпуска которой этот завод был построен.
На всех заводах, которые вводились в строй, нужно было организовать и наладить производство той продукции, для которой заводы проектировались. Нужно было научить людей работать на станках, выдерживая при этом требования, которые предъявляются к изделиям. Нужно было установить реальную производительную способность завода, основанную не на паспортных данных станков, а на том, как на них могут работать рабочие. Нужно было организовать бесперебойную работу всех цехов и отделов завода, так, чтобы в конце выходил в нужном количестве, нужного качества конечный продукт завода. И, наконец, нужно было освоить производство до такой степени, чтобы превзойти возможности машин и добиться наивысшей производительности. Все это были исключительно сложные задачи со множеством составляющих.
Пусковой период сложен и труден на любом заводе, в какой бы стране он ни пускался. Но в СССР он был, наверное, сложнее, чем где бы то ни было. Сложнее потому, что у нас были такие факторы, которых никогда не было, и не могло быть в других, более развитых странах.
Во-первых, в СССР в тот момент не было достаточного количества квалифицированных рабочих, необходимых для быстрого освоения производства. Для многих производств, которые создавались в Советском Союзе впервые, опытных, квалифицированных рабочих не было вообще. Отсутствие опыта тут же порождало ошибки, вело к авариям, поломкам станков, к остановке пущенного с такими трудами производства. Эти поломки, остановки, аварии устранялись с очень большими трудами.
Во-вторых, пускались заводы, оснащенные новейшим, высокопроизводительным оборудованием, многие из которых были организованы по принципу поточного производства. Опыта поточного производства в Советском Союзе практически не было. В таких масштабах оно организовывалось впервые. Не было ни инженеров, ни технологов, ни рабочих, которые были бы знакомы хотя бы с аналогичным производством.
В-третьих, заводы пускались в значительной степени недостроенными. То есть пуск и выпуск первой продукции происходил тогда, когда не был завершен полностью монтаж оборудования, а нередко не было даже завершено строительство завода.
В-четвертых, пуск и наладка производства велась при острой нехватке сырья, материалов и инструмента. Машиностроительные заводы не были обеспечены в нужном количестве чугуном и сталью. Качество этого чугуна и стали на первых порах было далеко от предъявляемых требований. Совершенно не было некоторых важных видов заготовок. Например, остро не хватало холоднокатаного листа, который применяется для изготовления кабин автомобилей. Из-за этого пришлось изготовлять деревянные кабины. Еще, к примеру, очень плохо поначалу работали литейные цеха заводов и крайне нерегулярно поставлялись отливки с других заводов, что тормозило сборку важнейших узлов машин. Остро не хватало инструмента, особенно для импортных станков. Практически отсутствовал измерительный инструмент, без которого невозможно обеспечить точность в изготовлении деталей и узлов. Производство нужного инструмента налаживалось тут же, по ходу работ.
Все это вместе превращало и без того тяжелый пусковой период в настоящую борьбу за производство. То, что было на Сталинградском тракторном заводе в 1930-м и в 1931 году, то разразилось на остальных заводах-новостройках годом-двумя позже.
Как разворачивалась борьба за производство, мы посмотрим на примере нескольких крупных заводов-новостроек: Челябинского тракторного, Уральского завода тяжелого машиностроения и Нижегородского, позже Горьковского автомобильного завода.
К слову сказать, эта страница истории советского хозяйства известна меньше всего. Как бы там ни было, но о подвигах первой пятилетки писали гораздо больше и гораздо охотнее. Там было о чем писать, были яркие личности и по-настоящему большие свершения. Но вот о том, как советская промышленность перешла к массовому, поточному, налаженному производству, литературы и материалов об этом невероятно мало. Гораздо легче изучать состояние хозяйства середины 1920-х годов, нежели хозяйство середины 1930-х годов. Но написать об этом времени и его делах стоит. Это время, когда от достижений первой пятилетки был получен первый результат.
Челябинский тракторный завод
После того как завод был в основном построен и пущен, старые строительные кадры перебросили на новые стройки. Леон Борисович Сафразьян с ЧТЗ и Павел Семенович Каган с СТЗ были направлены на строительство Ярославского автозавода. Сафразьян – начальником строительства, Каган – главным инженером и заместителем начальника. Ловин был передвинут с начальника Челябинсктракторостроя на пост первого заместителя начальника Главэнерго Наркомтяжпрома. Директором Челябинского тракторного завода 20 марта 1933 года был назначен Александр Давыдович Брускин.
К заводу было приковано внимание всего мира. Тракторный завод в Сталинграде, считали капиталисты, не может служить показателем технических успехов большевиков, потому что освоить выпуск трактора типа «Фордзон» можно и в России. Но гусеничные, тяжелые трактора типа «Картепиллер», с маркой «ЧТЗ» – это серьезное изделие, требующее хорошо развитого производства. Если большевики справятся с производством трактора, то нужно будет признать, что у них есть современная машиностроительная промышленность. Весь мир следил за тем, справятся большевики с трактором «ЧТЗ» или нет.
На оставшиеся семь месяцев 1933 года заводу был определен план в 2 тысячи машин. В декабре завод должен был произвести 750 тракторов, то есть по 30 тракторов в день, что составляло всего треть от проектной мощности завода. Но, как и на остальных заводах, производство в первые месяцы работы резко отставало от плана. В ноябре вместо 450 запланированных машин удалось произвести только 231 трактор.
9 декабря 1933 года в литейном цехе произошел пожар, выведший на несколько недель этот цех из строя. На участок сборки двигателей на некоторое время перестали поступать отливки блоков. Срочно, в самом спешном порядке, изготовление блоков и других литых деталей было налажено на опытном заводе. Это позволило удержать производство на уже достигнутом уровне и даже немного поднять его, по сравнению с предыдущим месяцем. Но план роста производства до 750 тракторов в декабре был провален. Всего было собрано только 357 тракторов. На конец года из 2 тысяч тракторов удалось произвести только 1650 машин[489].
Но задел был сделан. Уже на XVII съезде, в феврале 1934 года Орджоникидзе заявил, что тракторов Советский Союз больше не ввозит. Советская промышленность может удовлетворить потребности народного хозяйства в тракторах всех марок и модификаций.
Проектная мощность завода была достигнута в ноябре 1934 года, когда завод стал выпускать по сто машин в день. Из первой партии этих тракторов завод 1 января 1935 года сформировал колонну имени Кирова.
Но, как оказалось, освоение гусеничного трактора с бензиновым двигателем было только первой ступенью развития производства. Следующей ступенью было освоение массового производства дизелей, дизельной топливной аппаратуры и массовое производство тракторов с дизельными двигателями.
Летом 1934 года Наркомат тяжелой промышленности объявил конкурс на лучший дизельный двигатель. В самые короткие сроки разными проектными организациями было разработано три проекта: М-13, М-75 и ЧТЗ-НАТИ, Проекты дизелей рассматривались в марте 1935 года. Лучшим оказался двигатель М-75, который потом и запустили в производство. На испытаниях в августе 1935 года он дал запроектированные показатели мощности, веса и расхода топлива.
В апреле 1935 года в Наркомате тяжелой промышленности стал обсуждаться вопрос о реконструкции Челябинского тракторного завода сразу в двух направлениях: увеличения производственных мощностей для выпуска бензиновых тракторов и освоения производства дизельных двигателей. Орджоникидзе предложил удвоить производство тракторов. Брускин удвоения не взял, но план производства увеличил. Было увеличено дневное задание по выпуску тракторов.
6 апреля 1935 года на заводе состоялось техсовещание, на котором обсуждался вопрос производства дизельных двигателей и особенно дизельной топливной аппаратуры. Была создана дизельная комиссия во главе с Элизаром Ильичом Гуревичем[490].
Главным в дизельном двигателе для производственников была топливная аппаратура. При ее изготовлении нужно было соблюсти очень большую точность и чистоту обработки, чтобы получить годные детали. Малейшая неточность, малейшая неряшливость в обработке – и деталь уже выбраковывается. Неточно и плохо обработанные детали не могли обеспечить того распыления дизельного топлива, которое требовалось для нормальной работы дизельного двигателя.
В мире было очень мало фирм, которые могли осилить такую работу. 90 % деталей к топливной аппаратуре производилось немецкой фирмой «Бош». Эта фирма была, по существу, мировым монополистом в производстве этой важнейшей части дизельного двигателя. Когда к руководству фирмы обратились советские представители с просьбой оказания технической помощи, фирма наотрез отказалась от сотрудничества в какой бы то ни было форме. Получив отказ, хозяйственное руководство пошло другим путем. На заводе была организована опытная мастерская, в которой развернулись работы по освоению технологии изготовления прецизионных деталей. Была также образована комиссия из четырех инженеров дизельного цеха под руководством Э.И. Гуревича, которые поехали в США, на завод «Картерпиллер», где уже была к тому времени освоена технология производства тракторных дизельных двигателей. Фирма согласилась ознакомить советских инженеров с этим производством. Там советские дизелестроители получили первоначальный опыт современного на тот момент дизелестроения.
На Челябинском тракторном заводе возводился специальный цех для изготовления и сборки топливной аппаратуры, со специальным оборудованием для герметизации и обеспыливания цеха. Был размещен большой заказ на изготовление станков высокой точности. На «Красном пролетарии» в Москве заказали 51 станок, на Горьковском заводе фрезерных станков – 55 станков, на Ижевском станкостроительном заводе – 29 станков для оборудования цеха дизелестроения. На заводе были организованы специальные курсы для обучения рабочих будущего дизельного цеха.
Освоение изготовления прецизионных деталей топливной аппаратуры растянулось на полтора года. Только добиться высокой точности и чистоты обработки деталей было уже само по себе очень большим достижением. Но нужно было, кроме этого, добиться массового изготовления таких деталей, изготовления в таких масштабах, чтобы можно было обеспечить ими сборку больших серий тракторов. Из опыта освоения производства вынесли необходимые уроки. Производство не пускали до тех пор, пока не были изучены все тонкости процесса, пока не были расшиты все «узкие места» и процесс не был полностью освоен всеми рабочими цеха. Только после этого началось изготовление аппаратуры для массовой сборки дизелей.
Шаг за шагом на заводе продвигались к выпуску первого дизельного трактора. Это была изнурительная работа. Изготовлялись, тщательно проверялись на качество обработки, на размеры и допуски высокоточные, прецизионные детали топливной аппаратуры. Сотни деталей выбраковывались и тут же шли на стол к инженерам, которые искали причины брака. Освоение нового производства потребовало титанического упорства и терпения. Но, наконец, была собрана и испытана топливная аппаратура для первого дизеля. Был собран и испытан сам дизельный двигатель. И вот 20 июня 1937 года в 3 часа 15 минут с главного конвейера завода сошел первый дизельный трактор «С-65». Уже в сентябре 1937 года завод выпустил первый тысячный дизельный трактор[491].
Дата добавления: 2018-02-28; просмотров: 312; Мы поможем в написании вашей работы! |
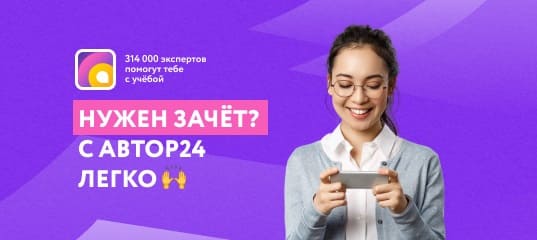
Мы поможем в написании ваших работ!