Й Государственный шарикоподшипниковый завод 17 страница. Кое-где уже были размещены заказы для советских заводов, а кое-где еще только предстояло осмотреть оборудование
Кое-где уже были размещены заказы для советских заводов, а кое-где еще только предстояло осмотреть оборудование, осмотреть производство, провести переговоры с владельцами фирм и сделать заказы. Первой была итальянская фирма Фальки, расположенная в Турине. Фальки изготовлял электропечи. Но переговоры с ним закончились неудачей. Владелец предъявил такия условия контракта, которые для советской стороны были совершенно неприемлемы:
«Когда я уезжал от Фальки, меня разбирала злоба. Ведь у него ничего, кроме желания заработать, нет. Он просто человек с большой инициативной, активной и голой энергией»[467].
Так охарактеризовал Емельянов владельца фирмы. Переговоры прекратились, и Емельянов только осмотрел металлургический завод в Аосте. Там к нему обратился начальник доменного цеха, который много слышал о заводах-гигантах на Урале и в Сибири, и попросил представить ему возможность поработать на домнах этих заводов. Емельянов пообещал ему, что сделает все возможное.
Ничего не добившись в Италии, комиссия поехала по многочисленным заводам и фирмам Германии. В Бреслау был размещен заказ на детали для электропечей Запорожского ферросплавного завода. Этот заказ почему-то сильно затянулся, и потом, когда уже советские представители грозили расторгнуть конктракт, детали прибыли, но оказались негодными. Емельянову поручили посетить фирму и разобраться с судьбой этого заказа:
|
|
«В кабинете владельца завода – совещание. Он пожилой уже человек. За столом рядом с нами – трое работников, руководящих производством. Хозяин завода явно волнуется. Он с тоской в глазах смотрит на нас. Никто из нас не мог даже предположить, что мое техническое участие будет для него смертным приговором»[468].
Детали – бронзовые корпуса для элетропечей – оказались бракованными и негодными. Емельянов твердо отказался принимать детали и оплачивать их. Хозяин попросил позволить ему переделать их на своем заводе. Но и в этом ему было отказано, так как уже прошли все оговоренные сроки. Когда положение стало ясным, владелец завода вышел в соседний кабинет и застрелился:
«Позднее я узнал, что завод был в долгу, как в шелку. Желая во что бы то ни стало получить заказ, владелец завода взялся за изготовление очень сложных деталей электропечей. Никто до этого в Германии таких печных конструкций не изготовлял»[469].
Осенью 1932 года Тевосян написал письмо Емельянову, который тогда находился в Эссене и вел переговоры с Круппом, с просьбой выехать в Аахен и посетить заводы Гадфильда, Тенка, Ферста и ряд других, на которых изготовлялась очень необходимая в Советском Союзе сталь Гадфильда – марганцевый сплав, обладающий особой вязкостью и стойкостью против износа. Емельянову удалось приобрести оборудование и технологию производства этих сортов стали. Вскоре оно было налажено на заводе «Красный Октябрь».
|
|
Следующей просьбой начальника «Спецстали» была просьба о поездке в Великобританию, в Шеффилд, на заводы, которые выпускали лучшую в мире нержавеющую сталь и делали из нее стальную ленту. После поездки в Шеффилд Емельянов снова вернулся в Германию и стал объезжать заводы и фирмы, которые производили интересующие их сплавы или металлургическое оборудование.
В фирме «Демаг» в Дуйсбурге Емельянов закупил технологию производства мостовых кранов, крайне необходимых для оборудования цехов металлургических заводов. В том же Дуйсбурге на заводе Канто и Клейна Емельянов изучал технологию производства трансформаторного железа и вербовал рабочих для работы на Кузнецком комбинате. Орджоникидзе попросил Емельянова найти 20–30 хороших сталеваров и прокатчиков и завербовать их для работы в Советском Союзе. Тогда Германия еще не вышла из экономического кризиса и на объявление о приеме явилось более семисот человек.
|
|
После этого Емельянов поехал в Фольклинген, на заводы фирмы Рёхлинга, который производил сернистую сталь, используемую для производства метизов. В СССР такой стали не производили. Владелец фирмы пошел навстречу советской стороне. Емельянов получил полную технологию выплавки такой стали, ее обработки, прокатки и калибровки. Более того, Рёхлинг выразил желание более тесно сотрудничать с советскими заводами.
На заводе того же Рёхлинга в Крефельде Емельянов ознакомился с технологией изготовления листа из быстрорежущей стали. Вскоре производство такого листа было организовано на заводе «Серп и Молот». Там же удалось приобрести технологию производства марганцевистой стали для буров, применяемых в горной и угольной промышленности. В Советском Союзе такая сталь не производилась, и никто ничего не знал о способе ее изготовления[470].
В начале 1933 года Орджоникидзе вызвал Емельянова из Германии в Москву на совещание. Задачи дальнейшего развития черной металлургии, поставленные во второй пятилетке, заставили Орджоникидзе обратиться к мировому опыту самых крупных и авторитетных металлургических компаний. Орджоникидзе поставил перед Емельяновым задачу – заключить с Рёхлингом договор о технической помощи и узнать, что он думает по поводу развития советской черной металлургии.
|
|
Рёхлинг согласился на заключение такого договора и на оказание технической помощи советской металлургии. Емельянов в ходе одной из бесед с Рёхлингом спросил у него: что бы тот стал делать на месте советских хозяйственных руководителей в деле развития черной металлургии. «Старый, опытный волк промышленности», как его охарактеризовал Емельянов, стал делать свои выкладки. Он начал с того, что в 1937 году Советский Союз собирается выплавить 17 млн. тонн стали. При выплавке мартеновской стали, когда в шихту идет 30 % чугуна и 70 % металлического лома-скрапа, для выплавки такого количества стали нужно 11 млн. тонн скрапа.
Рёхлинг перелистал справочники и показал Емельянову, что при выплавке прошлых лет и при ввозе импортного оборудования в 1937 году в СССР будет самое большее только 4,5 млн. тонн скрапа. То есть этого будет крайне недостаточно для выплавки стали в мартенах. Выход из такого положения – это строительство в дальнейшем не мартеновских печей, а конвертеров, которые позволяют выплавлять сталь без такой большой добавки лома[471].
Рёхлинг был, пожалуй, последним германским сталепромышленником, который поддерживал тесное сотрудничество с Советским Союзом. В 1933–1934 годах тяжелые времена для немецкой промышленности прошли. К власти пришел Гитлер, который стал проводить политику ускоренного вооружения своей державы. Фридрих Крупп, главный производитель вооружения и агитатор за поддержку Гитлера в промышленных кругах Германии, фактически отказался от сотрудничества с Советским Союзом и стал лихорадочно увеличивать объем производства. Началось выполнение большого числа заказов, оборонных по большей части. Перед советскими представителями закрывались ранее доступные цеха. Крупп пересмотрел соглашение о подготовке советских специалистов. Эта работа год от года сокращалась, пока, наконец, в 1933 году подготовка специалистов для советских заводов не прекратилась совсем. Их место заняли большие группы металлургов из Японии, учившиеся основам современной черной металлургии.
Правда, еще оставалась возможность сотрудничества с более мелкими немецкими фирмами. В 1934 году Емельянов проделал большую работу по изучению производства ферросплавов с разными металлами, производства электродов для электросталеплавильных печей. Но вести работу на немецких предприятиях становилось все сложнее и сложнее. Фирмы, одна за другой, отказывались от сотрудничества с советскими заводами. Советских представителей все чаще и чаще стали притеснять. В конце 1934 года несколько раз обыскивались помещения и квартиры торговых представителей. Все указывало на то, что работу в Германии скоро придется прекратить.
В 1935 году, после нескольких конфликтов по поводу притеснения представителей, а также потому, что немецкие фирмы отказались от дальнейшего сотрудничества, работа в Германии была прекращена. Емельянов выехал в СССР. С этого момента советская промышленность развивалась своими силами.
Период активного и тесного сотрудничества с иностранными фирмами в 1928–1935 годах принес для советской промышленности огромную добычу. Были освоены новейшие строительные технологии и получен опыт проектирования и строительства новейших крупных предприятий. Были освоены технологии производства машин, оборудования, деталей, сплавов и металлов, которые до этого или совершенно не производились, или же производились в крайне недостаточном количестве. Были подготовлены кадры квалифицированных рабочих новейшей крупной промышленности. Прямое заимствование иностранного опыта сэкономило миллиарды рублей. Можно сказать, что без такой крупномасштабной технической помощи достижения и успехи первой и второй пятилеток были бы невозможны.
Вместе с изучением и заимствованием зарубежного опыта, работа по созданию прочной металлургии качественных сталей развернулась на самых лучших заводах Советского Союза. Пионером в выработке технологии, освоении и производстве новых качественных, высококачественных и специальных сталей стал «Красный путиловец». На нем имелся мощный сталелитейный отдел, который и до революции держал первенство по стране в деле выплавки самых лучших качественных и инструментальных сталей. Здесь были собраны очень хорошие с огромным опытом работ кадры сталеваров-путиловцев.
Заимствованные за рубежом технологии первым делом проходили апробацию и освоение на «Красном путиловце». Путиловские сталевары, однако, не только изучали иностранную технологию, но и разрабатывали свои варианты, разрабатывали свои марки сталей и внедряли их в производство. Сталелитейный отдел завода стал лабораторией качественной металлургии во всесоюзном масштабе.
Первая крупная задача в деле производства качественной стали встала в связи с освоением выпуска танка Т-28 на заводе. Завод имел хорошо оборудованный отдел тракторостроения, сыгравший большую роль в начале коллективизации сельского хозяйства, который перепрофилировали под выпуск танка. В этом отношении особых проблем у завода не было. Но броневая сталь стала настоящей загвоздкой. Броневую сталь в Советском Союзе тогда почти не производили. Лишь в тресте «Югосталь» был небольшой цех, где варили в «кислых» печах броневую сталь марки «Щ». Мощности этого цеха явно не хватало для развития в стране современного танкостроения. Маститые специалисты-металлурги говорили, что невозможно выплавить броневую сталь в каких-то других печах, кроме мартенов с кислым подом.
Но путиловские металлурги были уверены, что они смогут получить броню гораздо лучшего качества, чем броневая сталь марки «Щ». Работу по получению брони возглавил инженер центральной лаборатории Семен Баранов. Под его руководством в 1932 году в сталелитейном отделе завода сумели разработать технологию и получить новую броневую сталь марки «ПИ». Она могла быть выплавлена в «основной» печи.
На испытания брони приехал Киров. На заводском полигоне выставили щиты из стали «Щ» и «ПИ». Их расстреливали с расстояния 450 метров по шесть снарядов. Оба щита выдержали испытания. Тогда Баранов предложил сократить дистанцию на сто метров. Щит «Щ» обстрела не выдержал:
«Все притихли. Было слышно, как Баранов, стараясь прикурить, ломал спички. Через мгновение снова грохнул выстрел»[472].
Щит из новой марки стали выдержал испытание. Вскоре завод из нее стал изготавливать броневые плиты и детали танка. Баранов за разработку новой марки броневой стали получил орден Ленина. В 1933 году по такому же способу удалось изготовить специальную сталь для производства артиллерийских орудий.
В сталелитейном отделе завода и в центральной лаборатории шли опыты по замене хромоникелевой стали другими марками, которые бы не содержали дефицитного тогда никеля, который в те времена производился в очень небольшом количестве. В 1934 году удалось разработать две новые марки: хромокремниевую сталь «КХ» и кремнемарганцевую сталь «КМ», которые по своим свойствам вполне могли заменить хромоникелевую сталь. Вскоре после этого вышел приказ по НКТП о замене никелевых марок сталей сталью марок «КХ» и «КМ».
Весной 1933 года директор завода Карл Мартович Отс получил в Наркомате тяжелой промышленности заказ на изготовление специальной кислотоупорной стали. Во второй пятилетке ставилась задача развития азотно-туковой промышленности, резкого увеличения производства химических удобрений для сельского хозяйства и строительства новых азотно-туковых предприятий. Для изготовления оборудования этих предприятий нужна была сталь, которая могла бы сопротивляться действию кислоты.
В Советском Союзе кислотоупорная сталь не производилась. Для того чтобы освоить ее производство, Отсу пришлось очень существенно переоборудовать имеющийся электросталелитейный цех. Летом 1934 года кончилась его реконструкция, и в новом цехе начались опыты по выплавке кислотоупорной стали. Первые плавки оказались неудачными: сталь не выдерживала испытания на коррозию или на распределение титана, что имело значение для прочности детали.
Пригласили ведущего специалиста по кислотоупорной стали, британского инженера Брирлея, который когда-то создавал это производство, и пытались применить технологию, которая использовалась на американских заводах. Но и с его помощью дело никак не шло. Сталь получалась, но не соответствовала предъявляемым к ней требованиям. Главная загвоздка заключалась в распределении титана в массе стали. Никак не удавалось добиться его равномерного распределения. Наконец, инженеры центральной лаборатории Левитский и Заморуев предложили решить вопрос распределения титана в стали так: производить завалку ферротитана перед выпуском стали и перемешивать сталь в печи шомполами. Опытная плавка показала очень хорошее качество стали. От американской технологии пришлось отказаться и разработать свою. По разработанной на «Красном путиловце» технологии стали выплавлять кислотоупорную сталь еще на «Электростали» и на «Запорожстали».
Кислотоупорную сталь нужно было еще перед отправкой на металлообрабатывающий завод предварительно протравить, чтобы получить ровную, гладкую поверхность заготовки. О травлении листов кислотоупорной стали на заводе никто ничего не знал. Способ травления позаимствовали у Круппа. Он основывался на использовании сильных, концентрированных кислот. Это было очень вредное и опасное производство. Но другого способа пока не было. Завод создал и оборудовал специальный цех, где травились кислотами листы кислотоупорной стали.
Работавшие в лаборатории завода супруги Зимневы, инженеры-химики, взялись за разработку способа травления стали в слабых кислотах. В конце концов после многих опытов им удалось создать технологию травления кислотоупорной стали в слабой кислоте с использованием тока. Качество ничем не отличалось от крупповской технологии. Директор завода упразднил цех травления кислотоупорной стали и приказал перейти на метод Зимневых. Для завода это упразднение опасного и вредного производства стало настоящим праздником[473]. Рабочие радостно отпраздновали ликвидацию этого цеха.
«Красный путиловец», с 1934 года – завод имени Кирова, добился в изготовлении качественных и специальных сталей огромных успехов. В 1937 году он выплавлял 130 марок сталей. Общий объем производства составил 500 тысяч тонн[474].
После этого только недобитые гитлеровцы могут говорить о том, что будто бы Советский Союз перед войной выплавлял «всего 10 видов качественных сталей».
Советская черная металлургия росла во второй пятилетке как на дрожжах. По чугуну производство было удвоено. Если в 1932 году было выплавлено 6 млн. 161 тысяча тонн, то в 1938 году – 16 млн. тонн, в том числе на предприятиях Главного управления металлургической промышленности (ГУМП) 14 млн. 991 тысяча тонн чугуна[475]. Производственный план по чугуну выполнили без существенного перевыполнения планового задания. Этого не позволили сделать имеющиеся производственные мощности, которые в конце второй пятилетки были загружены на полную мощь. Еще более повысить производство чугуна без строительства новых доменных печей было тогда делом трудноосуществимым.
Причин невысокого уровня выполнения плана несколько. Во-первых, в начале пятилетки заводы фактически работали на голодном топливном пайке. Из-за плохой работы Донецкого угольного бассейна заводы то и дело недополучали кокса и не могли создать у себя каких-либо топливных запасов. В первые годы заводы недодавали своей продукции и были вынуждены в конце пятилетки наверстывать былые упущения.
Во-вторых, до 1935 года имело место неэффективное использование руды. Рудная база, на которой работала советская черная металлургия, поражала своим богатством. В среднем в рудах содержалось 54,3 % железа. Но из-за отсутствия предварительной подготовки, обогащения и агломерации руды на заводах сплошь и рядом имелся большой перерасход руды на тонну готового чугуна. Вынос руды в виде колошниковой пыли составил 5 млн. 498 тысяч тонн, или 29,3 % всей используемой руды. На тонну чугуна получался перерасход 265 кг чистого железа, не перешедшего в чугун[476].
В-третьих, в ходе эксплуатации выявлялись изъяны и недостатки конструкций печей. Вот, например, Л.Б. Кафенгауз[477] пишет о работе домен Кузнецкого комбината:
«В первый период работы домен Кузнецкого завода было много аварий и брака. Из-за горения фурм печи заливало водой. Вынос пыли составлял до 30–40 %. Все домны скоро оказались закозленными. В 1935–1936 годах печи были отремонтированы № 1 и № 2[478], исправлены профили печи № 3 и № 4. Вынос пыли сократился до 402 килограммов на тонну чугуна в 1937 году и до 333 килограммов на тонну чугуна в 1938 году»[479].
В-четвертых, так и не вышел на проектную мощность Магнитогорский комбинат. Он должен был давать по проекту 2 млн. 750 тысяч тонн чугуна, а давал в 1937 году только 1 млн. 530 тысяч тонн[480].
Во второй пятилетке была проделана большая работа по исправлению допущенных сразу после пуска ошибок, устранение последствий аварий и неправильной эксплуатации домен. На заводах достраивались и пускались в ход агломерационные фабрики, работа которых позволяла резко сокращать потери руды при плавке и увеличивать выплавку чугуна. После реконструкции доменного цеха Кузнецкого комбината вынос колошниковой пыли сократился до 17,9 % вместо 30 %. После пуска аглофабрики в 1935 году на Магнитогорском комбинате вынос пыли сократился до 17,5 % вместо 27,4 % до ее пуска. Это позволило сократить расход кокса и повысить эффективность использования печей.
Было поправлено положение с коксом. Вмешательством Политбюро ЦК и посылкой в Донбасс комиссии ЦК ВКП(б) под председательством Кагановича работу на угольных шахтах бассейна удалось выправить. Кроме того, в 1932 году на шахтах бассейна началось движение передовиков производства, которое привело к коренной перестройке технологии и к резкому росту добычи угля.
Еще можно отметить, что за второе пятилетие удалось удвоить производство чугуна по сравнению с производством в 1932 году. Это уже само по себе большое достижение. При недостатке литейного чугуна удалось также добиться полного обеспечения потребности производства стали в передельном чугуне. В 1937 году на производство стали было отпущено 11 млн. 218 тысяч тонн чугуна, против 3 млн. 172 тысяч тонн в 1932 году.
Гораздо большие успехи были достигнуты в производстве стали. При плане в 17 млн. тонн стали, в 1937 году было выплавлено 17 млн. 729 тысяч тонн. Сталеплавильное производство перевыполнило пятилетний план. За второе пятилетие были удвоены мощности мартеновских печей и увеличены в восемь раз мощности электросталеплавильных печей. Электростали стало производиться 799 тысяч тонн вместо 104,9 тысяч тонн в 1932 году[481].
Дата добавления: 2018-02-28; просмотров: 275; Мы поможем в написании вашей работы! |
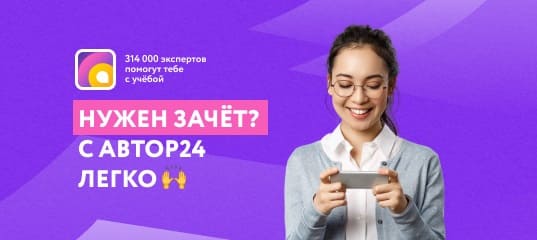
Мы поможем в написании ваших работ!