Понятие процесса и элементов производства
Объект – любое производственное (производящее) звено и его основа (сущность) – производственные процессы промышленного производства.
Предмет – оперативное организационно-технологическое управление (т.е. несколько шире, чем только «планирование» и «регулирование», как значится в названии курса). Оперативное управление любым производством состоит из: планирования (определения состава, последовательности и сроков проведения работ в какой-либо период времени); организации; учета хода производства (фиксации произошедших плановых и внеплановых изменений текущего состояния производства); регулирования (диспетчирования); анализа; контроля, т.е. практически все функции управления. При этом долгосрочное (стратегическое, прогнозное, т.е. на 5 и более лет), текущее (объемное, т.е. на 1 год), и среднесрочное (календарное, графики работы, т.е. квартал, месяц) планирование интересно лишь частично, а главным образом – краткосрочное (декада, неделя, сутки, смена) или оперативное планирование (управление!). Иногда справедливо говорят об оперативно-производственном, или об оперативно-календарном планировании (ОКП) и оперативном регулировании (диспетчировании). Таким образом, терминология не вполне устоялась, но суть ясна.
На этом этапе управление детализируется, «спускается» на самые низшие иерархические звенья производства, вплоть до технологических установок и рабочих мест. Поэтому некоторые специалисты считают, что «оперативное управление» означает управление отдельными операциями в общем хозяйственном управлении в коротком и среднем периодах.
|
|
Оперативно-производственное планирование по месту его выполнения подразделяется на межцеховое и внутрицеховое.
Межцеховое оперативно-производственное планирование направлено на обеспечение слаженной и равномерной работы основных цехов. Исходной базой межцехового планирования являются сводный календарный план выпуска продукции и портфель заказов предприятия. К задачам межцехового планирования относятся: разработка оперативно-календарных нормативов, взаимная увязка содержания и сроков календарных планов цехов основного и вспомогательного производства и общезаводских служб, составление и выдача цехам квартальных и месячных календарных планов, текущее межцеховое регулирование производства, оперативный учет и диспетчирование выполнения календарного плана цехами. Межцеховое оперативное планирование выполняется производственно-диспетчерским отделом (ПДО) предприятия.
Внутрицеховое оперативно-производственное планирование направлено на обеспечение слаженной и равномерной работы участков и рабочих мест цеха. К внутрицеховому планированию относятся уточнение месячной программы цеха и распределение предусмотренных в ней работ по отделениям и участкам, составление и выдача участкам календарных месячных планов-графиков и заданий по каждому рабочему месту, оперативный учет и диспетчирование выполнения плана участками. Внутрицеховое оперативное планирование выполняется производственно-диспетчерским бюро цеха, мастерами и плановиками участков.
|
|
Как показывает опыт, задачи организационно-технологического управления наиболее трудно поддается автоматизации. Структурно данная АСУ занимает промежуточное положение между АСУП (общезаводская система) и АСУТП (система управления технологическим оборудованием – станки с ЧПУ и др., контрольно-регулирующая аппаратура). Перспективным подходом является создание интегрированных АСУ.
Организационно-технологическое управление, прежде всего, должно дать экономически обоснованные ответы на вопросы: что обрабатывать (какую деталь) и сколько, на каком оборудовании и какие ресурсы при этом использовать, когда начинать и заканчивать операции.
|
|
Главная цель функционирования этой системы управления – организация согласованной во времени и маршрутно-технологически ориентированном пространстве движение деталей.
Иногда те, кто по роду своей практической деятельности и научным исследованиям связаны с управлением качества, добавляют такое важное требование, как обеспечение выпуска продукции установленного качества. Эти работники иногда понимают под целью управления – повышение эффективности использования продукции, а именно: работоспособность и отказ, т.е. два вида состояния – исправное и неисправное, что является очень ценным добавлением, которое часто отсутствует, в том числе и в учебной литературе. Это связано с нечетким формулированием понятия конечный результат.
Развивая эту мысль, можно выделить такое важное требование, предъявляемое к функционированию рассматриваемой системы, как достижение наивысшей эффективности производства, и даже наилучших социально-экономических (народнохозяйственных) результатов. Таким образом, предполагается «стыковка» с системами высших уровней, в противном случае неизбежны кризисы, напряжения, развал.
В западной традиции оперативного управления упор делается на экономическую (стоимостную) сферу. Ключевой показатель – рост суммы покрытия (равнозначно росту прибыли, когда постоянные издержки принимаются стабильными), который широко используется в текущем и стратегическом планировании. Поэтому сохраняется преемственность, последовательность в планировании. В отечественной практике же часто происходит разрыв между текущим и оперативным планированием: на заводском уровне планирование и учет ведутся укрупнено по цеховым переделам на декаду и месяц; на цеховом уровне такой детализации недостаточно и, естественно, действуют свои системы, в рамках которых разрабатываются сменные задания, планирование переналадок технологического оборудования, работы транспортно-складских систем, почасовой и поминутный учет хода производства и т.д.
|
|
Это, в частности, порождает использование управленческим персоналом разной информации, «непрозрачность» планирования и учета себестоимости продукции и др.
Кстати, на Западе иначе понимается и само оперативное планирование, оно включает все виды оперативной деятельности:
· документооборот;
· управление движением материальных ресурсов;
· техническая подготовка производства;
· управление производством;
· управление использованием оборудования;
· управление качеством продукции;
· управление движением готовой продукции, сбытом и маркетинг;
· управление договорной сферой;
· управление финансовыми расчетами;
· управление кадрами и др.
В достижении необходимых экономических результатов решающее значение принадлежит оперативному, т.к.:
1) это практический уровень, т.е. можно вырабатывать самые перспективные программы экономического развития и даже довести их до планов, графиков, нормативов, но из-за таких причин, как перебои в материальном обеспечении, простоев людей и оборудования, нарушений графиков отгрузки из-за несвоевременной подачи вагонов и т.д., не достичь поставленных целей. Все замыкается, в конечном счете, системой оперативного управления;
2) оперативное управление охватывает все экономические процессы во всех сферах деятельности и звеньях предприятия. Текущее, а тем более стратегическое управление в принципе не затрагивает незавершенные процессы, незаконченные хозяйственные операции, локальные (составные части) процессов и операций. Между тем, именно они и решают исход дела, ведь целое складывается из элементов;
3) в процесс оперативного управления втянуты непосредственно центры принятия решений (мастера, бригадиры, рабочие, которые знают свои процессы значительно лучше, чем вышестоящие работники, связанные с текущим и стратегическим управлением). Мгновенная реакция на складывающиеся ситуации, динамичность – это все несомненные преимущества оперативного управления.
Содержание курса: в начале остановимся на изучении, т.е. на классификации, описании, изучении структуры, сравнительном анализе и тенденциях развития, различного рода производящих объектов, на реальной материальной базе современного производства определяющей соответствующую систему организационно-технологического управления. В процессе изучения объекта станут ясны многие цели и задачи организационного управления и соответствующей службы, организация и функции которой также будут рассмотрены. Затем изучим традиционные, широко используемые на действующих предприятиях порядок, методы, варианты, специфику задач организационно-технологического управления для различных типов производства. При этом ознакомимся с системой календарно-плановых нормативов – основой рассматриваемой системы. Закончится изучение курса нетрадиционными методами управления, возникших, главным образом, из задач регулирования (диспетчирования), т.е. планирования в режиме реального времени в современном гибком автоматизированном производстве (ГАП).
Место курса: дисциплина относится к прикладным экономическим дисциплинам (на Западе курс может называться «economic technology» или «производственная логистика», определяемая как наука об оптимизации потоковых процессов).
Знания, приобретенные при изучении курса, пригодятся студентам в любом случае, где бы они ни работали после окончания университета. Ведь все нынешние проблемы отечественной кризисной экономики связаны с проблемами управления (менеджмента), имеющего множество специфических особенностей в зависимости от того или иного объекта управления.
Структура предприятия
Процесс производства можно рассматривать узко (как процесс изготовления какого-либо продукта), либо широко (системно), как процесс удовлетворения конкретной потребности. В практике управления используется понятие «жизненного цикла» продукции, включающего следующие виды процессов:
1. Процессы научных исследований (фундаментального и прикладного характера).
2. Опытно-конструкторские работы (ОКР).
3. Освоение и доводка конструкции.
4. Подготовка производства (так называемый переходный процесс).
5. Производственные процессы.
6. Транспортировка на склад и к месту потребления (процессы сбыта и маркетинга).
7. Процессы потребления (эксплуатации), которые могут включать монтажные и наладочные процессы, собственно потребление, обслуживание и ремонт, модернизацию, утилизацию после списания.
«Жизненный цикл» иногда понимается еще шире – как естественный процесс смены выпуска моделей (вида) изделий.
На практике наблюдается прогрессивная тенденция к интеграции всех этих процессов у производителя, а отсюда и необходимость управления ими. Например, возник сектор заводской науки, а в потреблении широко развиваются сервисные системы, аренда и лизинг. «Продвинутые» АСУ включают возможности управления всеми этими процессами.
Непосредственно в обработке на машиностроительных предприятиях изделие находится только 5-10% от общего времени его изготовления. остальные 90-95% времени затрачиваются на согласование, подготовку производства, ожидание запуска. Затраты в сфере потребления превышают производственные затраты, что диктует необходимость осуществления управления на протяжении всего «жизненного цикла» продукции. Исключение потерь на станках является главной составляющей эффекта описанной интеграции. К тому же в процессе потребления происходят аналогичные процессы производства другой продукции, что объединяет эти системы в единую производственно-эксплуатационную систему.
Любая производственная система включает:
1. Основные (технологические) процессы, состоящие из действий над продуктом производства, в результате чего происходит изменение его состояния и определение его свойств, т.е. непосредственно создается (формируется) сам продукт производства. Например, к ним относятся: процессы заготовок (паковок, отливок, штамповок и т.п.); процессы обработки (механической, термической, химической и т.п.); процессы сборки; процессы испытаний и регулирования; процессы контроля, консервации, упаковки. Сегодня в промышленности используются самые разнообразные технологии, в том числе электрохимические, электрофизические, плазменные, лазерные, радиационные и другие высокоэффективные методы обработки изделий.
2. Вспомогательные процессы, без которых невозможно выполнение основного процесса (транспортировка, хранение объектов производства, изготовление инструмента, приспособлений, комплектация передаточных партий, инструментальные наладки, переналадка оборудования, утилизация отходов, информационные процессы и др.
3. Обслуживающие процессы включают диагностику элементов производства, ремонт оборудования и др., без которых невозможно выполнение основных и вспомогательных процессов.
4. Обеспечивающие процессы включают процессы обеспечения безопасности и нормальных условий работы, социально-культурное обслуживание, питание, техническую учебу, подбор кадров и др.
5. Управленческие процессы планирования, организации, анализа, регулирования, контроля, учета и др., рассматриваемые в данном случае как виды деятельности конкретных работников, технических и информационных систем.
Часто все процессы 2-5-й групп считают вспомогательными.
Все процессы можно также строго подразделить на промышленные и непромышленные.
Процесс изготовления объекта целиком (например, готового изделия) – сложный процесс, который может состоять из стадий или фаз, которые, в свою очередь, могут состоять из простых (частичных) процессов изготовления отдельных деталей (составных частей объекта производства). Простые процессы могут состоять из технологических операций. Технологическая операция представляет собой законченную часть технологического процесса, выполняемую на одном рабочем месте. В технологическом процессе изготовления изделий машиностроительного профиля основными расчетным элементом, для которого устанавливается время и себестоимость выполнения работы, расход ресурсов, является именно операция.
Технологические операции разделяются на технологические и вспомогательные переходы, а также на рабочие и вспомогательные ходы.
Технологический переход – законченная часть операции, характеризуемая постоянством применяемого инструмента и поверхностей, образуемых обработкой или соединяемых при сборке.
Вспомогательный переход включает действия рабочего и работу оборудования, которые не изменяют форму, размеры и поверхности и необходимы для выполнения операции.
Рабочий ход – это законченная часть технологического перехода, связанного с однократным перемещением инструмента при обработке заготовки.
Вспомогательный ход – однократное перемещение инструмента относительно заготовки, необходимое для выполнения рабочего хода.
Иногда для обозначения ходов используют понятие «элементарная работа» или «действие».
Положение обрабатываемой заготовки или собираемого изделия относительно оборудования или инструмента характеризует занятую позицию для выполнения технологической операции или перехода. Позиция – это фиксированное положение заготовки, изделия для выполнения технологической операции или определенного перехода.
Разделяют следующие виды технологических процессов (операций):
1. В зависимости от количества изделий, охватываемых процессом:
1) единичный,
2) типовой,
3) унифицированный,
4) групповой.
2. В зависимости от степени разработанности (детализации):
1) маршрутные,
2) операционные,
3) маршрутно-операционные.
Основная цель маршрутной технологии – дать общий план обработки заготовки, наметить содержание операций технологического процесса и выбрать тип оборудования, методы обработки, число и последовательность выполняемых переходов. В результате разработки маршрутной технологии заполняется маршрутная карта. В ней дается полное описание технологического процесса, включая все технологические операции, а также операции контроля и перемещения детали (изделия) в технологической последовательности ее изготовления с указанием данных о том, где (на каком оборудовании), с каким оснащением и материальными и трудовыми затратами он должен осуществляться.
Операционная технология разрабатывается с учетом места каждой операции в маршрутной технологии, с детализацией – какие поверхности и с какой точностью обрабатываются на предшествующих операциях, какие поверхности и с какой точностью необходимо обрабатывать на данной операции. При этом уточняется ее содержание, устанавливается последовательность и возможность совмещения переходов во времени, окончательно выбирается оборудование, инструмент и приспособления, назначаются режимы резания, определяется норма времени, устанавливаются настроечные размеры, и составляется схема наладки.
Проектирование операции – задача многовариантная. Каждый вариант оценивается по производительности и себестоимости. Обращается внимание на уменьшение штучного времени.
Разработанная операционная карта позволяет выдать задание на конструирование специального оборудования, средств механизации и автоматизации, на разработку технологического оснащения и метрологического обеспечения процесса. Так, например, операционные карты сборки составляются на основе маршрутных карт сборки и содержат описание сборочных операций с расчленением их на технологические переходы и указанием режимов работы и расчетных норм. Как общая, так и узловая сборка начинаются с установки базовой детали на стенд или в приспособление. Технологический процесс сборки состоит из ряда отдельных операций, среди которых основным являются операции соединения сопрягаемых элементов изделия. Сборка изделий осуществляется либо в стационарных условиях, либо на поточных линиях.
В маршрутно-операционной карте определенным образом сочетаются оба указанных выше технологических процесса.
Длительность протекания всех процессов изготовления продукта называется производственным циклом, который включает:
1. Технологический период, состоящий из:
- времени непосредственного изготовления или сборки изделия (т.е. время протекания основных технологических процессов);
- время протекания естественных процессов (сушка, брожение, старение чугуна, остывание);
- времени вспомогательных процессов (контрольных, транспортных, подготовительно-заключительных, ремонтных и т.д.).
2. Перерывы в изготовлении продукта:
- вызванные календарным режимом (регламентом) работы (междусменные, выходные и праздничные дни, обеденные перерывы);
- вызванные пролеживанием изделий между операциями (партионные, ожидания, комплектации);
- вызванные простоями из-за неисправности оборудования, отсутствия инструментов, материалов, невыхода рабочего.
Все перерывы также желательно планировать и нормировать.
Длительность производственного цикла изготовления изделия, его структура не являются простой арифметической суммой времени протекания указанных процессов, т.к. многие процессы осуществляются одновременно (параллельно).
Расчеты длительности производственного цикла тесно связаны со следующими фондами времени:
1. Календарный фонд времени (общее количество часов в календарном периоде). Годовой календарный фонд времени:
час.
2. Номинальный (режимный) фонд времени:
,
где - потери, связанные с режимом работы, в том числе в выходные и праздничные дни, сокращенное время в предпраздничные дни, простои из-за не использования 3-ей смены, перерывы на обед.
При двухсменной работе равен примерно 47% от
или
,
где - время на обработку;
- нормируемое время проведения планово-предупредительных ремонтов;
- время простоев по техническим причинам (восстановление при сбоях и отказах);
- время простоев по организационным причинам (отсутствие работы или рабочих, нехватка или неподготовленность техоснастки и др.).
3. Эффективный фонд времени работы:
или
.
Так, время обработки (длительность производственного цикла) партии деталей рассчитывается следующим образом:
,
где - подготовительно-заключительное время на партию;
- размер партии запуска (число деталей в партии);
- штучное время на деталь.
Подготовительно заключительное время затрачивается рабочим один раз на всю партию обрабатываемых деталей. Величина этого времени не зависит от размера партии. В условиях массового производства подготовительно-заключительное время отсутствует и поэтому технически обоснованная норма времени совпадает с нормой штучного времени.
,
где - оперативное время на деталь;
- доля операционного времени, добавляемая на отдых и личные надобности рабочего (для ГПМ эта доля равна нулю, а для станков с ЧПУ – 0,04);
- доля оперативного времени, добавляемая на техническое и организационное обслуживание рабочего места (для станков с ЧПУ – 0,04-0,09, для обрабатывающих центров – 0,12, для ГПМ этот коэффициент определяется в расчете не на деталь, а на сутки работы).
,
где - время работы по управляющей программе;
- ручное вспомогательное время (на установку деталей и проведение измерений).
,
где - основное машинное время;
- вспомогательное время (автоматический подвод и смена инструмента, холостые ходы).
В оперативном управлении широко используется также такое понятие, как штучно-калькуляционное время на деталь:
.
Удельные веса различных составляющих в общей длительности производственного цикла зависит от уровня автоматизации, серийности производства, степени технической унификации изготавливаемых деталей и длительности технологического времени изготовления.
Технически обоснованная норма времени определяет время, необходимое для выполнения работы в данных операционно-технических условиях при наиболее полном использовании рабочего времени и оборудования. Время устанавливается в часах и минутах. На основе технически обоснованных норм времени назначаются расценки, определяется производительность оборудования и соответствие производственных программ производственной мощности участков, цехов и предприятия в целом. Технически обоснованные нормы времени разрабатываются применительно к типу производства, так как каждый из них (массовое, серийное и единичное производство) определяет степень дифференциации и точность нормативных материалов. Для массового производства устанавливаются наиболее точные и дифференцированные нормы времени на отдельные движения рабочего и приемы (прием представляет собой законченную закономерность действий рабочего, характеризующуюся частным целевым назначением) обработки тех или иных деталей на определенных станках. В серийном производстве технически обоснованные нормы времени разрабатываются на комплексы приемов соответственно их технологической последовательности (нормы времени на станочные и слесарные работы) или же группируются в комплексы в зависимости от однородности факторов, влияющих на продолжительность отдельных приемов (нормы времени по литейным и другим работам). Для мелкосерийного и единичного производства нормы времени разрабатываются по укрупненным комплексам приемов на технологические переходы и отдельные типовые операции в целом.
Технологические процессы целесообразно представлять графически как последовательность операций (сеть действий) – см. рис. 1-6.
![]() |
или
Рис. 1. Традиционно представляемая структура технологического процесса
![]() |
Рис. 2. Сетевое изображение технологического процесса (сетевая модель)
![]() |
Рис. 3. Циклограмма или схема сборки изделия
![]() |
Рис. 4. Ленточная диаграмма (Ганта)
991
111 161
112 162
401
201 601
601 201
999
Рис. 5. Вариантная (альтернативная) технология
Кроме того, технологический процесс графически можно представить с помощью сетей Петри. В данном случае графическое описание процесса управления производственным циклом однозначно определяет рабочие алгоритмы управления, составляется данное описание инженером-технологом на основании его собственных исчерпывающих представлений о требуемом ходе производственного процесса. Будучи составленным, это описание попадает в распоряжение специалистов по алгоритмизации и программированию, которые далее работают исключительно на его основании, совершенно не обращаясь к существу производственного цикла. Поэтому во избежание ошибок в реализации процедуры управления необходимо обеспечит адекватность подобного описания требуемому ходу производственного процесса во всех потенциально возможных ситуациях. Составление описания процесса управления с проверкой и подтверждением его адекватности производственному циклу и является сущностью процесса верификации этого описания. После верификации описания может быть представлено в типовом формализованном виде для дальнейшего использования в целях алгоритмизации и, в случае необходимости, программирования.
Узлы разветвления в безальтернативных технологиях не означают, что можно действовать как-либо иначе, нет, в этих случаях следует пройти весь маршрут, все ветвления, чтобы получить нужный результат.
Вариантность возникает:
- при модификации маршрутной технологии, проводимой с целью устранения локальных перегрузок отдельных видов оборудования;
- при модификации операционной технологии (т.е. режимы, оснастка, инструмент и др.) с целью подготовки к возможным изменениям параметров заготовок, а иногда, и номенклатуры имеющегося в наличии инструмента.
Так, в гибких производственных системах (ГПС) обычно имеется несколько видов оборудования с частично совпадающими технологическими возможностями. На рис. 5 вариант соответствует случаю альтернативных технологий. Здесь 111, 112 и 161, 162 – токарная обработка на станках различной модели; 201 – сверлильная обработка; 601 – фрезерная обработка; 401 – токарно-сверлильно-фрезерная обработка (на обрабатывающем центре).
Таким образом, на рисунке вариантной технологии выделены 3 вида ветвления, когда:
- последующий маршрут не зависит от того, на каком станке выполнялась предшествующая обработка;
- равноправны не просто отдельные операции, но и целые наборы операций;
- равноправной является обработка на принципиально различном оборудовании.
При описании многовариантного технологического процесса иногда пользуются такой компактной записью:
991,401 = ((111=161,112 = 162),(201,601) = (601,201)),999
Здесь знаком «равно» обозначаются равноценные ветви маршрута, а ветви в круглых скобках указывают ветви маршрута, содержащие более одной операции (установок).
Широко используются кодирование и методы математического моделирования технологических процессов.
9.3. Характеристика управления процессами и элементами производства.
Чтобы любой процесс мог совершаться, необходимо иметь в наличии определенный набор материальных элементов – элементов производственно (производственно-эксплуатационной) системы, т.е. необходима элементная (объектно-субъективная) структура процесса:
· машины и оборудование, в том числе силовые, рабочие, регулирующие, приборы;
· передаточные устройства и транспортные средства;
· рабочий инструмент;
· производственный инвентарь и принадлежности;
· здания и сооружения;
· обобщенный продукт (идеальный образ в голове конструкторов, технологов);
· полуфабрикат в процессе изготовления изделия;
· сырье и материалы;
· топливо и энергия;
· информация;
· финансы (деньги);
· элементы окружающей среды;
· люди (работники).
В совокупности эти элементы определяют производственный потенциал предприятия.
Результат производства в промышленности, в том числе машиностроении – готовое изделие, что является важнейшим элементом исследуемой системы, центральный объект управления.
Под изделием понимается отдельная деталь, механизм, машина и их элементы в сборе, являющиеся продуктом конечной стадии производства. Изделия, предназначенные для поставки (реализации) заказчикам, являются предметами изготовления в подразделениях основного производства, а предназначенные для внутреннего потребления, т.е. для собственных нужд организации, относятся к изделиям вспомогательного производства.
Установлены следующие виды изделий:
· детали;
· сборочные единицы;
· комплексы;
· комплекты.
Дата добавления: 2018-02-28; просмотров: 61; Мы поможем в написании вашей работы! |
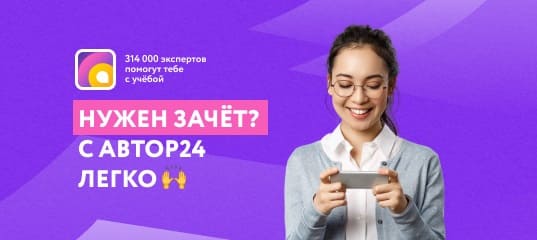
Мы поможем в написании ваших работ!