Технические решения, положенные в основу проекта
Образование продуктов деградации в растворах алканоламинов – одна из серьезных проблем, возникающая при эксплуатации установок очистки газа, приводящая к нарушению режима работы установок, ухудшению качества очищенного газа, потерям абсорбента и, как следствие этого, к необходимости снижения производительности установки по газу.
Основная причина продуктов деградации – примеси, поступающие с сырым газом и попадающие в абсорбент (жидкие углеводороды, пластовая вода, механические примеси, ингибиторы коррозии, ПАВ, смолистые вещества и др.). Также огромное влияние оказывают высокие температуры процесса, перепады даления, смазочные масла, продукты коррозии и вспенивания амина.
Для предотвращения указанных проблем на газоперерабатывающем заводе выполняются следующие основные мероприятия:
1. Сведение к минимуму содержания в поступающем на очистку газе примесей, вызывающих или способствующих вспениванию, коррозии и образованию побочных продуктов.
2. Периодическая промывка и очистка аппаратов от шлама.
3. Для удаления из циркулирующего аминового раствора веществ, вызывающих повышенное вспенивание, используется фильтрация этого раствора через слой активированного угля (АУ). При этом через систему очистки пропускается от 5 до 20 % циркулирующего поглотительного раствора.
4. Применение антивспенивателей, ингибиторов коррозии [22].
Но у всех этих мероприятий есть недостатки:
|
|
1. Применение пеногасителей не устраняет полностью самих возбудителей пенообразования, а только на время гасит процесс вспенивания. Передозировка пеногасителя ведет к образованию более стабильной и трудно гасимой пены;
2. Применение фильтрации на угольных адсорбентах эффективно непродолжительный период времени, в период перезагрузки угля полностью выключается узел фильтрации амина, что ведет к накоплению пенообразующих веществ [8, 25].
В свою очередь, применение процесса фильтрации всего объема амина через угольные фильтры приводит к увеличению числа фильтров и объема отработанного адсорбента и, как следствие, к резкому увеличению затрат на обслуживание процесса.
Согласно существующей схеме (Рис. 3.3.1) на линии подачи регенерированного амина установлен ряд фильтров грубой и тонкой очистки, которые задерживают уносимый с аминовым раствором активированный уголь.
При работе по данной схеме предусмотрены такие операции, как: еженедельная замена фильтрующего агента в FL01 (целлюлоза), ежемесячная пропарка угольных фильтров (проводится в атмосферу) и их промывка, также предусмотрена ежеквартальная замена всего объема активированного угля в узле фильтрации [26].
|
|
Процесс замены адсорбента представляет собой длительный и трудоемкий процесс. Перед сменой угля проводится пропарка угольного фильтра и системы фильтрации в целом с выходом в атмосферу. После пропарки и снижения температуры в фильтре, его вскрывают и выгружают вручную уголь, что влечет за собой большие трудозатраты.
Рисунок 3.3.1. Технологическая схема существующего адсорбционного узла фильтрации аминового раствора:
Т01 – емкость хранения амина; FL01 – фильтр грубой очистки; FL02 А,В – угольные фильтры; FL03 А,В – фильтры очистки аминового раствора от уносимого активированного угля; FL04 – фторопластовый фильтр; Р01 – аминовый насос; 1 – раствор амина на фильтрацию; 2 – раствор амина на стадию абсорбции; 3 – отфильтрованный раствор амина в ёмкость хранения.
Загрузка угля идет также вручную через верхний люк аппарата. После загрузки угольный фильтр заполняют водой, дренируют и пускают в работу.
На основании вышесказанного, были предложены альтернативные методы вывода пенообразующих веществ из поглотительного алканоламинового раствора, лишенные перечисленных недостатков.
Наиболее перспективным представляется экстракционный процесс, при котором удаление пенообразователей осуществляется экстракцией [24].
|
|
В качестве экстрагента предлагается использовать полифениловые эфиры (ПФЭ) марок 5Ф4Э и Н-ПФЭ. Эффективность ПФЭ в качестве экстрагента в процессе вывода пенообразующих веществ из поглотительного аминового раствора доказана лабораторными исследованиями.
Для проведения процесса экстракционной очистки предложена следующая схема (Рис. 3.3.2): часть или весь поток аминового раствора, подаваемый из емкости хранения T01, после охлаждения поступает в экстрактор Э01, где происходит смешение аминового раствора и экстрагента (ПФЭ). В процессе экстракции происходит разделение очищенного аминового раствора и насыщенного ПФЭ. Аминовый раствор возвращается в систему, а в насыщенный раствор ПФЭ впрыскивается реэкстрактор-метилэтилкетон (МЭК), после чего эта смесь направляется в разделитель Э02. В разделителе происходит механическое удаление выделяющегося осадка веществ, растворимых в ПФЭ и не растворимых в смеси ПФЭ и МЭК.
|


Рисунок 3.3.2. Технологическая схема предлагаемого экстракционного узла фильтрации
аминового раствора:
T01 – резервуар хранения аминов; P01, 04, 05 – насосы; А02 – воздушный холодильник; F01 – фильтр от мехпримесей; B04 – емкость хранения экстрагента (ПФЭ); E04 A,B – испарители; B05 – емкость хранения МЭК; Э01, 02 – экстракторы; К01 – отпарная колонна, Т02 – емкость хранения нефтешламов.
|
|
Смесь МЭК+ПФЭ подается в отпарную колонну К01, где происходит регенерация экстрагента. Сверху колонны выходит регенерированный МЭК, снизу – ПФЭ.
Оценка существующего оборудования установки аминовой очистки газа на ГПЗ показала, что внедрение экстракционной очистки возможно на уже существующих мощностях. Данная схема предусматривает частичное переоборудование существующих аппаратов. Фильтр FL01A переоборудуется в экстрактор Э01, фильтр FL01B – в разделитель Э02, фильтр FL02A – в отпарную колонну К01 для смеси ПФЭ+МЭК с подводом тепла за счет потока регенерированного амина. Емкость B05 – емкость хранения ПФЭ.
Внедрение этого процесса на производстве уменьшит выброс отходов в виде насыщенного активированного угля, исключит трудозатраты на перегрузку этого адсорбента и позволит отказаться от использования угольных фильтров. Наличие установки экстракционной очистки обеспечит непрерывность цикла очистки аминовых растворов и существенно снизит возможность вспенивания раствора амина в абсорбере.
Все перечисленное приведет к значительному улучшению технико-экономических показателей работы установки аминовой очистки на ГПЗ. Кроме того, выгрузка отработанных материалов (активированного угля в количестве 29 т/г и др.), а также исключение из рабочего цикла установки процесса пропарки и промывки угольных фильтров и других фильтрующих элементов сократит выброс в атмосферу вредных веществ. Следовательно модернизированный процесс существенно улучшит экологическую обстановку в районе расположения предприятия.
Дата добавления: 2018-02-28; просмотров: 427; Мы поможем в написании вашей работы! |
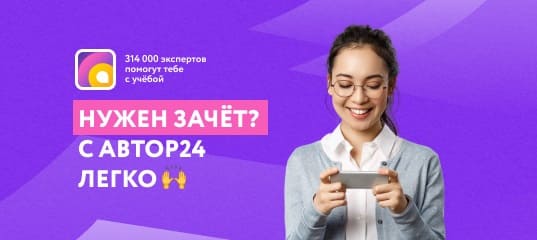
Мы поможем в написании ваших работ!