Концентрация различных солей в моноэтаноламина С
при 25 оС, %(масс.)
Соль | С | Соль | С | Соль | С |
NaCl | 1.86 | KBr | 3.27 | NaClO4 | 90.8 |
NaBr | 33.6 | KCl | 42.3 | KClO3 | 0.300 |
NaJ | 22.0 | NaClO3 | 19.7 | KClO4 | 1.36 |
KCl | 0.27 | LiBr | 60.0 | CrCl2 | 19.5 |
LiCl | 30.0 | CaCl2 | 14.0 | BaCl2 | 45.2 |
С понижением концентрации растворов растворимость в них солей увеличивается. Минеральные соли в систему могут попасть также с водой, используемой при приготовлении аминовых или других растворов.
Пенообразование на установках очистки кислых газов
Одной из серьезных трудностей, встречающихся при эксплуатации установок очистки газов от кислых компонентов, является пенообразование. Оно типично для предприятий, применяющих технологию адсорбционного извлечения сероводорода и диоксида углерода водными растворами диэтоламина. Эти негативные явления приводят к потерям амина, снижению производительности установки, снижению производительности установок, коррозии химического оборудования и значительному повышению эксплуатационных затрат. Причины возникновения пенообразования могут быть следующие [33-44]:
- повышение скорости коррозии в системе;
- поступление на установку различных ингибиторов, используемых при добыче газа;
- разложение аминов под воздействием высоких температур;
- накопление в аминовых растворах продуктов побочных реакций;
- попадание в абсорбер тяжелых углеводородов в виде капель;
- наличие в газе минерализованной капельной воды на входе в абсорбер;
|
|
- вход в систему минеральных солей с технической водой, используемой для приготовления поглотителей кислых компонентов.
На практике может иметь место каждый из указанных факторов, чаще всего взаимодействуют сразу несколько факторов, и выдача рекомендаций по борьбе с пенообразованием становится трудной задачей. Нередко эти рекомендации сводятся к борьбе с последствиями пенообразования, а не его причиной.
Доказано [39], что вспенивание чаще возникает в аппаратах с высокими нагрузками по газу и жидкости. Внешним признаком пенообразования является резкое увеличение перепада давления в колонне, поэтому для своевременного предупреждения вспенивания необходим контроль за этим показателем.
Наличие в системе интенсивного пенообразования приводит к увеличению потерь абсорбента и ухудшению качества товарного газа. Эти факторы, а также повышенный перепад давления в абсорбере могут служить подтверждением пенообразования в системе.
Интенсивность пенообразования зависит также от поверхностного натяжения абсорбента. Этот процесс осуществляется тем легче, чем меньше поверхностное натяжение раствора (σ). Поэтому попадание поверхностно-активных веществ (ПАВ) в поглотители снижает значение σ и способствует пенообразованию.
|
|
Плохо смачиваемые вещества (механические примеси, продукты коррозии и т.д.) прилипая к поверхности пузырьков газа, препятствуют их сращиванию и вместе с ними переходя в пену способствуют ее стабилизации.
Влияние углеводородов и метанола на вспениваемость раствора ДЭА характеризуется кривыми рисунка 2.3.1 [34]. С увеличением температуры кипения углеводородов их влияние на впениваемость раствора возрастает. Наибольший эффект оказывают парафиновые углеводороды.
Рисунок 2.3.1. Влияние содержания различных добавок С на пенообразующую способность 25%-го раствора ДЭА (Н – высота пены): 1 – ундекан; 2 – нонан; 3 – фракция конденсата К.К. – 150оС; 4 – конденсат ГКМ; 5 – циклогексан.
Влияние смеси солей MgCO3, CaCO3, KCl, K2SO4 на вспениваемость раствора МЭА показано на рисунке 2.3.2. В работе [36] отмечено, что наибольшее пенообразование вызывают карбонаты кальция и магния.Рисунок 2.3.2. Зависимость продолжительности жизни пены т от концентрации солей с в растворе МЭА.
На установках очистки газов от кислых компонентов борьба с пенообразованием ведется в основном по двум направлениям:
|
|
- применение специальных реагентов для гашения пены;
- очистка растворов от побочных примесей.
Большое значение придается также подбору реагентов для интенсификации добычи и борьбы с коррозией с тем, чтобы их попадание в поглотители кислых компонентов не вызывало интенсивного пенообразования [34].
В качестве пеногасителей могут использоваться полиметилсилоксаны или их смеси, вещества на основе кремнеорганического полимера – «Антиадгезив АС», высокомолекулярные спирты (полиалкиленгликоль, октилфеноксиэтанол, стеариновый спирт, олеиловый спирт и т.д.).
Из силоксановых соединеий применяют ДЦ антифоам А, спластик, компаунд (США), антифрон (ГДР), Родорсил-426Р (Франция). Из российских антивспенивателей можно указать эмульсяя ВНИПИГАЗ-1, КЭ-10-12, КЭ-10-21, И-1-А. Они нетоксичны, взрывобезопасны, негорючи, их активные вещества имеют температуру кипения более 300 оС.
Полисилоксаны (Re2SiO3)n представляют собой бесцветные маслянистые жидкости с различной молекулярной массой и вязкостью. Силоксановые жидкости имеют высокую термическую стабильность. Их пеногасящая способность проявляется в кислой, щелочной и нейтральных средах при самых незначительных массовых долях (0,0001-0,001%).
|
|
Пеногасители снижают прочность поверхности пленок, разделяющих газовые пузырьки и жидкую фазу. Противопенные свойства пеногасителей проявляются только при концентрациях, превышающих пределы их растворимости в пленке.
На установках сероочистки для пеногасителей устанавливаются специальная емкость и дозировочные насосы. По мере необходимости с помощью дозировочных насосов пеногаситель нагнетается в поток регенерированного раствора перед входом в абсорбер. За счет подачи пеногасителя в трубопровод беспечивается его равномерное распределение в абсорбенте.
Коррозия аппаратуры
Практически все оборудования и коммуникации установок очистки газа от кислых компонентов подвергаются коррозии. Основной причиной коррозии считается наличие в системе сероводорода и диоксида углерода, который является более агрессивным, чем H₂S [14].
Принято считать, что СО₂ при взаимодействии с материалом оборудования и труб образует растворимый бикарбонат железа. При подогреве раствора происходит выделение СО₂ и осаждение железа в виде нерастворимого карбоната.
Сероводород приводит к образованию сернистого железа. Частично это соединение может образовывать на поверхности металла защитную пленку. Однако одновременное наличие в газе СО₂ и H₂S в определенных условиях может обусловить синэргический эффект, т.е. каждый из этих компонентов может усилить коррозионное действие другого.
Коррозии оборудования также способствует накопление в растворе твердых частиц, которые разрушают защитные пленки, вызывают эрозию металла. Такими твердыми частицами являются сульфид железа, окись железа, пыль, песок, прокатная окалина, которые попадают в абсорбер вместе с потоком газа.
В определенных условиях, особенно при повышенной температуре, возможно образование комплексов железа с моноэтаноламином хелатного типа
,
.
Такие же соединения могут образовывать диамины и другие полиамины. При охлаждении раствора и взаимодействии этих соединений с сероводородом выпадает в осадок сернистое железо, а исходный компонент, участвующий в образовании хелата, регенерируется и вновь реагирует с железом в тех частях установки, где поддерживается высокая температура.. Таким образом, продукты коррозии не расходуются в процессе коррозии, а накапливаются в растворе.
При высоких температурах может протекать реакция между металлическим железом и угольной кислотой с образованием растворимого бикарбоната железа Fe(HCO3)2. При десорбции СО2 в регенераторе бикарбонат железа превращается в нерастворимый карбонат железа FeCO3, который осаждается на стенках аппаратов и трубопроводов [53].
Оборудование установок аминовой очистки газов помимо общей коррозии подвергается и другому виду разрушения – коррозионному растрескиванию низколегированных и углеродистых сталей в регенерированных и насыщенных сероводородом и углекислым газом (или одним из этих газов) аминовых растворах. Верятность растрескивания возрастает с повышением температуры. Зарегистрированы случаи появления коррозионных трещин в абсорберах, десорберах, теплообменниках, трубопроводах.
Таблица 2.4.1.
Скорость коррозии стали 20 в различных абсорбентах (p=50 МПа, t=90 оС, ∑α=0,5 моль/моль, H2S/СО2=2:1)
Абсорбент, % масс. | Скорость коррозии, мм/год |
ДЭА (40 %) | 0,06 |
МДЭА (40 %) | 0,074 |
МДЭА + ДЭА (40 %) | 0,09 |
Укарсол-702 (70 %) | 0,05 |
Ещё одним видом коррозии оборудования установок сероочистки является расслоение углеродистых и низколегированных сталей под действием водных сероводородсодержащих сред, образующихся в результате десорбции кислых газов.
В отдельных видах оборудования установок сероочистки при изготовлении его из углеродистых и низколегированных сталей скорость электрохимической коррозии столь значительна, что не может быть обеспечен проектный срок службы таких аппаратов из-за утонения стенок. Это относится к кипятильникам (ребойлерам) колонн, десорберам, сепараторам и некоторым другим аппаратам, эксплуатирующимся в среде кислых газов, поступающих из десорбера. Перечисленные аппараты или отдельные их элементы рекомендуется изготавливать из легированных сталей (Х18Н10Т; Х17Н13М2Т и др.) [54]. Стоимость оборудования в этом случае возрастает в несколько раз.
При очистке газа водными растворами аминов коррозия происходит по всему тракту поглотительного раствора. Наиболее интенсивная коррозия наблюдается в зонах с максимальной концентрацией кислых газов и максимальной температурой, поэтому в промышленных условиях наиболее интенсивной коррозии обычно подвержены теплообменники, кипятильники, конденсаторы, десорберы.
Скорость коррозии увеличивается с повышением температуры, концентрации кислых компонентов и количества воды в системе, а также при наличии продуктов реакций окисления и разложения аминов, минеральных солей, увеличение скорости насыщенного абсорбента в коммуникациях и т.д. Следовательно, в этих условиях скорость коррозии может быть снижена при соответствующем увеличении производительности разгонки и фильтрации.
Скорость коррозии зависит от материала оборудования и качества его изготовления. Легированные стали менее подвержены коррозии, следовательно, наиболее уязвимые места установок (коммуникация насыщенного раствора от рекуперативного теплообменника до десорбера, верхняя часть десорбера, конденсатор-холодильник, используемый для охлаждения верхнего продукта десорбера, трубный пучок испарителя и т.д.) должны быть изготовлены из легированных сталей.
Следует отметить, что на надежную эксплуатацию установок очистки высокосернистых газов влияет выбор материала для тех частей установки, которые непосредственно контактируют с высокосернистым газом. С увеличением прочности сталей их чувствительность к водородной коррозии возрастает.
Продукты разложения вызывают повышенный, нежели сами чистые растворы аминов, износ аппаратов и коммуникаций, поэтому их следует периодически удалять из раствора.
Скорость коррозии стали различных марок в водном растворе аминов, содержащем СО2, изучена в ряде работ [53, 54]. Установлено, что скорость коррозии стали Ст.3 в 10-100 раз выше скорости коррозии нержавеющей стали марки 1Х18Н10Т [14]. Кроме того, коррозия углеродистой стали резко возрастает в местах ее контакта с легированными сталями [ 29]. Наблюдались случаи коррозии нержавеющих сталей [38]. Наибольшей стойкостью к коррозионному растрескиванию и межкристаллитной коррозии обладает сталь марки 0Х21Н6М21 [54].
При неблагоприятных условиях эксплуатации и отсутствииспециальных мер коррозия может принять катастрофический характер и за 5-6 месяцев вывести из строя почти все оборудование, работающее при температуре выше 100 оС (включая насосы). Эрозионно-коррозионному разрушению подвергается даже оборудование, находящееся в контакте с жидкостью при температуре окружающей среды. Наиболее сильной коррозии обычно подвержены теплообменники, кипятильники, а также конденсаторы флегмы, регенераторы и дроссельные вентили на линии насыщенного раствора.
На скорость коррозии оказывает влияние также соотношения СО₂:H₂S в очищаемом и десорбированном газах. Принято считать, что H₂S при взаимодействии с железом образует сульфид железа. При отсутствии эрозии сульфид железа на поверхности металла создает защитную пленку. Учитывая это, наибольшее насыщение раствора допускается при очистке газов с меньшим содержанием СО₂ и большим содержанием H₂S. В обратном случае степень насыщения раствора должна быть как можно меньше [9].
Выбор концентрации применяемого раствора также осуществляется с учетом отношения H₂S:СО₂. Чем выше его значение, тем более концентрированный раствор можно применять.
Интенсивность коррозии возрастает в ряду: первичные алканоламины-вторичные-третичные, так как более реакционноспособные первичные и вторичные амины требуют более высоких температур для десорбции кислых газов, остаточное содержание кислых газов в регенерированных растворах таких аминов также выше. На границе раздела фаз существенным фактором разрушения становится кавитация.
Сульфид железа (FeS) обычно содержится в качестве загрязняющей примеси в рабочем/технологическом газе аминной сиситемы, содержащем H2S. Серная кислота воздействует на углеродистую сталь, образуя FeS, который оседает на углеродистой стали и образует слой, защищающий от воздействия кислоты. Такая пассивация позволяет использовать углеродистую сталь в деталях конструкции.
Взвешенные частицы FeS являются причиной многих проблем: они забивают трубки обменников, поддонов абсорбционных и десорбционных отсеков, трубопровод, что приводит к сбоям и снижению показателей тепло- и массообмена. Взвешенный FeS представляет собой твердые частицы, вызывающие износ, которые являются еще одной причиной эрозии защитных слоев FeS, что приводит к циклу коррозия – эрозия – коррозтя – эрозия. Эти твердые частицы имеют тенденцию к перемещению на границу раздела воды и нефти. Соединение верхних слоев углеводородов и твердых частиц FeS на поверхности аминного раствора приводит к усилению пенообразования. FeS также стабилизирует структуру пены и эмульсий, не давая выделиться жидкости.
В аминной системе существует три вида условий, препятствующих пассивации сульфидом железа, таким образом, увеличивающих коррозию и образование сободного FeS: механические, термальные и химические. Механические условия включают вибрации, эрозию в высокоскоростных зонах, механические удары при запуске и остановке, которые повреждают слой сульфида железа, а высвободившиеся частицы попадают в аминный поток. В результате резких температурных изменений частицы FeS также могут отделиться от углеродистой стали, и в результате механического воздействия увлечь за собой еще большее количество частиц, и привести к износу всей системы. Химические факторы воздействия на пассивационную способность FeS – это высокое содержание термостойких солей и продуктов аминного распада.
Основное оборудование установок очистки газа изготавливается из углеродистой стали и лишь наиболее подверженные коррозии узлы (трубные пучки теплообменников, кипятильников, холодильников) из нержавеющей стали, скорость коррозии которой в 10-100 раз ниже, чем углеродистой стали.
Абсорберы обычно не корродируют, хотя бывают случаи коррозионного растрескивания при определенных условиях. Одним из средств борьбы с растрескиванием является ожиг сварных швов.
Термообработке подвергаются и сами колонны. Срок службы абсорберов и десорберов поддерживается увеличением толщины стенок при их изготовлении.
В теплообменниках трубные пучки корродируют как со стороны насыщенного, так и регенерированного раствора, что объясняется высоким содержанием кислых газов в растворе и неполной их отпаркой из раствора. При этом особенно интенсивная коррозия происходит в высокотемпературной секции теплообменников, в которых раствор перегревается выше температуры кипения и происходит десорбция кислых газов. Кожухи из углеродистой стали обычно корродируют значительно слабее.
Особенно агрессивны условия работы кипятильников (ребойлеров), что связано с тем, что в них зачастую происходит отпарка значительного количества СО2 при температуре около 130 оС, и образуются застойные зоны, содержащие СО2 и продукты деструкции амина.
Подвержены коррозии и конденсаторы-холодильники парогазовой смеси, выходящей из десорбера. Добавление этаноламина (до 1%) в газообразную систему H2O-H2S-CO2 приводит к значительному ослаблению коррозии углеродистой стали. Поэтому, в последнее время охлаждение парогазовой смеси проводится в верхней части десорбера путем непосредственного контакта с флегмой, циркулирующей в замкнутом контуре.
Ниже приведены мероприятия по борьбе с коррозией на аминовых установках очистки газа.
На стадии эксплуатации:
- поддержание низких скоростей в теплообменниках амин/амин;
- циркуляция насыщенного раствора амина по трубам теплообменника, а регенерированного раствора – в межтрубном пространстве;
- поддержание повышенного давления в теплообменниках с целью предотвращения выделения из раствора кислых газов при снижении давления и повышении температуры насыщенного раствора;
- применение ингибиторов коррозии, особенно при высокой степени насыщения амина кислыми газами (>0,5 моль/моль).
На стадии проектирования и изготовления:
- правильный выбор рабочего раствора и конструкции оборудования;
- правильный выбор металла для изготовления оборудования и трубопроводов;
- термообработка сварных соединений.
Главным требованием для ослабления коррозии является хорошее качество поглотительного раствора (снижение содержания в растворе продуктов побочных реакций – не более 0,2%, а также солей жесткости и механических примесей) – это достигается путем непрерывного вывода примесей из раствора на фильтрацию.
Рисунок 2.4.1. Зависимость скорости коррозии углеродистой стали от концентрации СО2 в 20%-ном растворе МЭА и температуры: 1 – при 40 оС; 2 – при 60 оС; 3 – при 100 оС; 4 – при 130 оС.
Дата добавления: 2018-02-28; просмотров: 702; Мы поможем в написании вашей работы! |
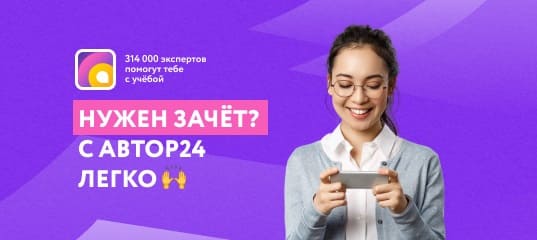
Мы поможем в написании ваших работ!