Трудоемкость ремонтов на единицу ремонтной сложности механической части технологического оборудования по видам работ, нормо-ч 4 страница
2.6. Причины снижения эксплуатационных свойств
оборудования
Повышение надежности оборудования и снижения затрат на эксплуатацию — составляющие сложной проблемы большого государственного значения. Решение этой проблемы, с одной стороны, обеспечивается промышленными предприятиями за счет выпуска оборудования новых конструкций, обладающего большой эксплуатационной надежностью, с другой — средствами технической эксплуатации.
В процессе эксплуатации происходит изменение исходных характеристик технологического оборудования. Это обусловлено многочисленными факторами, которые действуют на его эксплу-
атационные показатели не изолированно, а комплексно, находясь в сложной зависимости друг от друга. Поэтому всякая классификация факторов носит условный характер, однако является необходимой, так как позволяет обобщать и систематизировать причины, приводящие к изменению исходных характеристик оборудования в процессе его эксплуатации. Основные факторы, обеспечивающие повышение эксплуатационных характеристик оборудования в процессе его использования, можно разделить на три группы: конструктивные, технологические (производственные) и эксплуатационные.
Качество конструкции и производства оборудования определяется надежностью и долговечностью, заложенными в его конструкции и реализуемыми в процессе эксплуатации.
К конструктивным факторам относится совершенствование размеров, формы, начальных зазоров, посадок и допусков, обеспечивающих наименьшее изнашивание сопряженных деталей, наивыгоднейший тепловой режим и надежную смазку. Кроме того, качество конструкции должно обеспечивать удобство обнаружения и устранения отказов оборудования путем диагностических, регулировочных и ремонтных работ.
|
|
Совершенство производства характеризуется применяемыми материалами и их обработкой, обеспечивающими механическую прочность и износостойкость механизмов оборудования.
Технологические факторы определяют компоновку технологического оборудования предприятий сервиса в сложную техническую систему, включающую в себя силовую установку, передаточные механизмы, исполнительные органы, систему управления и регулирования и др. Каждый из агрегатов, входящих в состав оборудования, состоит из механизмов, каждый механизм — из деталей (элементов). Каждый из элементов и комплексов элементов оборудования выполняет определенные технологические функции, обеспечивая работоспособность оборудования.
Следовательно, каждое технологическое оборудование представляет собой определенную упорядоченную структуру связанных между собой элементов. Связь и взаимодействие между отдельными структурами определяется геометрическими размерами, механическими, электрическими, тепловыми и другими величинами. Эти величины называются параметрами технического состояния (структурными параметрами), которые с течением времени изменяются.
|
|
Эксплуатационные факторы проявляются при работе оборудования, когда элементы оборудования подвергаются различным внешним и внутренним воздействиям, которые можно разделить на субъективные и объективные.
К субъективным можно отнести воздействия, связанные с неправильной эксплуатацией оборудования обслуживающим пер-
соналом вследствие недостатка знаний, опыта, небрежности, несоблюдения режимов работы, а также плохой организации технической эксплуатации и др.
К объективным относятся воздействия, не зависящие от обслуживающего персонала. Это — условия работы, качество материала, действие промежуточной среды, климатические и биологические воздействия, внешние взаимодействия деталей и др. В результате оборудование перестает отвечать всем требованиям технической документации, т. е. проявляется ее неисправность.
|
|
О степени исправности технологического оборудования обычно судят по тому, насколько его состояние в данный момент соответствует всем требованиям технической документации, установленным как в отношении основных параметров, характеризующих нормальное выполнение заданных функций, так и второстепенных, характеризующих удобства эксплуатации, внешний вид и т. п. Любое несоответствие хотя бы одному из требований основных или второстепенных параметров свидетельствует о наличии неисправности.
Понятие «исправность» шире понятия «работоспособность»: исправное изделие отвечает всем требованиям, а работоспособное — лишь тем, которые обеспечивают его нормальное функционирование.
Несоответствие требованиям второстепенных параметров обычно освещается в конструкторских руководствах и в инструкциях по эксплуатации технологического оборудования. При ремонте приходится сталкиваться с неисправностями, которые изменяют рабочие характеристики оборудования. Это могут быть развиваемая или потребляемая мощность, производительность, удельный расход рабочей жидкости, точность и качество выполняемой работы, развиваемая скорость и др. Для передаточных механизмов основной характеристикой является коэффициент полезного действия, об изменении которого судят обычно по возрастанию потерь передаваемой энергии.
|
|
Основными постоянно действующими причинами, вызывающими изменения технического состояния оборудования, являются процессы изнашивания и старения. Под изнашиванием подразумевается процесс постепенного изменения параметров технического состояния оборудования (изделий), вызываемый воздействием механических, тепловых и других видов нагрузок, наличие которых определяется режимами работы. Старение — процесс постепенного и непрерывного изменения параметров оборудования и его элементов, вызываемый причинами, не зависящими от режима работы оборудования.
В результате изнашивания и старения изменяются основные эксплуатационные качества оборудования и их элементов, снижается эффективность работы. Технологический процесс, направ-
ленный на восстановление работоспособности оборудования, приведение его в состояние годности для дальнейшего использования в течение срока не менее чем межремонтный, называется ремонтом.
2.7. Схема технологического процесса ремонта
оборудований
На ремонтных предприятиях технологический процесс ремонта оборудования сводится к ряду мероприятий (восстановительных операций), с помощью которых изношенное оборудование приводится в исправное состояние.
Процесс ремонта оборудования включает в себя разборочно-сборочные и сопутствующие им дефектовочные, регулировочные и другие операции, а также операции восстановления изношенных и поврежденных деталей. Ремонт оборудования представляет собой комплекс работ, выполняемых по определенному алгоритму. Наиболее полно это проявляется при капитальном ремонте. В этом случае процесс ремонта в общем виде может быть представлен схемой, приведенной на рис. 2.4.
В зависимости от типа производства технологический процесс ремонта оборудования может проводиться необезличенным или обезличенным методом. Единичному производству, характеризуемому широкой номенклатурой ремонтируемых изделий и малым объемом их выпуска, присущ необезличенный метод ремонта. При этом методе сохраняется принадлежность восстановленных составных частей к определенному экземпляру изделия. Следовательно, оборудование находится в ремонте до тех пор, пока на него не поставят все снятые и отремонтированные детали.
Ремонт необезличенным методом выполняют универсальные или специализированные бригады. В первом случае бригада рабочих проводит как разборочно-сборочные, так и ремонтные работы и должна иметь необходимые приспособления, инструмент и запасные части для восстановления работоспособности всех элементов оборудования. При этом каждый член бригады участвует в выполнении всего комплекса ремонтных работ, что требует от него высокой квалификации.
При выполнении ремонта специализированными бригадами разборочно-сборочные работы проводятся одной бригадой, а ремонтные — другими, специализированными на ремонте определенной группы элементов, близких по технологическим и конструктивным признакам. Ремонт проводят на определенных специализированных постах (рабочих местах), оснащенных приспособлениями, инструментом и запасными частями, необходимыми для
![]() |
![]() |
Рис. 2.4. Технологический процесс капитального ремонта оборудования
ремонта только данной группы элементов. Отремонтированные детали и сборочные единицы возвращают обратно в разборочно-сборочное отделение и устанавливают на оборудование, с которого они были сняты.
Положительной стороной необезличенного метода ремонта является то, что приработавшиеся сопряжения после ремонта
сохраняются в паре и впоследствии работают надежно. К его недостаткам относятся длительный простой оборудования в ремонте и необходимость больших производственных площадей на ремонтных предприятиях, так как оборудование все время, которое затрачивается на ремонт или изготовление деталей, находится в цехе. Но, несмотря на это, метод необезличенного ремонта широко применяется на многих ремонтных предприятиях.
Это объясняется тем, что такие предприятия вынуждены сами ремонтировать технологическое оборудование различного типа из-за его большого разнообразия и территориальной рассредоточенное™ предприятий.
Сущность обезличенного метода ремонта заключается в том, что в процессе разработки и дефектации детали оборудования одной марки обезличиваются (т. е. не сохраняется принадлежность восстановленных составных частей к определенному экземпляру изделия), а отремонтированные детали комплектуются для сборки обезличенных элементов. Из них затем собирают оборудование, причем операции подгонки деталей сводятся до минимума.
На специализированных ремонтных предприятиях, ремонтирующих оборудование (агрегаты) этим методом, широко применяется специализация бригад и постов, характерная для серийного производства.
Обезличенный метод ремонта дает возможность укрупнить партии деталей и сборочных единиц, использовать преимущества серийного производства: специализировать производственные участки, применять высокопроизводительное оборудование и оснастку, механизировать и автоматизировать ремонтные операции, специализировать рабочих на ремонте и сборке определенных элементов. Все это позволяет уменьшить трудоемкость, стоимость и продолжительность ремонта деталей и оборудования в целом.
Обезличенный метод ремонта, при котором неисправные агрегаты заменяются новыми или заранее отремонтированными, называется агрегатным. Под агрегатом в данном случае подразумевается сборочная единица, обладающая свойствами полной взаимозаменяемости, независимой сборкой и самостоятельным выполнением определенной функции в изделиях различного назначения, например электродвигатель, редуктор, насос и т.д.
Основные преимущества агрегатного метода ремонта заключаются в сокращении продолжительности ремонта и в повышении вследствие этого коэффициента их использования, а также в увеличении пропускной способности ремонтного предприятия.
Основой агрегатного метода ремонта является оборотный фонд, который представляет собой комплект исправных агрегатов установленной номенклатуры и определенного количества. Первона-
чально он создается из сборочных единиц и агрегатов, получаемых от заводов-изготовителей, а также из отремонтированных элементов списанного оборудования. Потребное число сборочных единиц или агрегатов данного типа в оборотном фонде подсчитывают по формуле
где — коэффициент, учитывающий возможные отклонения при оборачиваемости элементов (
обычно принимается равным 1,2); А — количество однотипных элементов и агрегатов на одном оборудовании; Б — количество однотипного оборудования;
— продолжительность оборачиваемости элемента (продолжительность нахождения в ремонте с момента сдачи до получения из ремонта), дни;
— планируемая продолжительность работы оборудования в году, ч;
— срок службы элемента до очередного ремонта, ч.
При ремонте агрегатным методом оборудование поступает на ремонтное предприятие, где его разбирают на элементы и затем направляют в цехи. После ремонта они поступают в оборотный фонд и используются впоследствии для сборки другого оборудования той же марки. Сборку же разобранного оборудования ведут с помощью элементов и агрегатов, полученных со склада оборотного фонда.
Поточный метод ремонта как разновидность обезличенного метода выполняется на специализированных рабочих местах (постах) в определенной технологической последовательности и ритме. Он присущ массовому производству, которое характеризуется узкой номенклатурой и большим объемом выпуска изделий. При массовом производстве существенное значение имеют устойчивость объекта ремонта и оснащение рабочих мест специальным оборудованием (оснасткой). Отремонтированные изделия собираются согласно нормам их выпуска и, как правило, непрерывно в запланированные рабочие смены.
Оборудование может ремонтироваться не только на специализированных ремонтных предприятиях, но и самой эксплуатирующей организацией. По принципу организации ремонт оборудования внутри предприятия, эксплуатирующего оборудование, может выполняться в централизованной, децентрализованной и смешанной формах.
При централизованной форме оборудование всего предприятия ремонтирует ремонтная бригада (ремонтно-механи-ческий цех). В этом случае отдел главного механика не только планирует все виды ремонта, но и выполняет его силами подчиненного ему ремонтно-механического цеха. Централизация создает условия для организации индустриального ремонта, а следователь-
но, и для применения наиболее прогрессивных технологических и организационных решений.
Децентрализованная форма ремонта предусматривает выполнение всех видов ремонта силами ремонтных ячеек цехов. Для этого в каждом цехе создается своя ремонтная служба во главе с механиком (мастером) цеха. Отдел главного механика при децентрализованной системе осуществляет планирование и учет видов ремонта, составление заявок на материалы и покупные изделия для нужд ремонта и т. д.
При смешанной форме капитальные ремонты сложного оборудования выполняются силами ремонтной службы предприятия (ремонтно-механический цех), а остальные ремонты выполняются ремонтной службой цеха.
На предприятиях, эксплуатирующих оборудование, ремонт целесообразно проводить на базе запасных частей (новых и отремонтированных) и оборотного фонда агрегатов.
Предпосылкой такой организации должно являться достаточное производство запасных частей и широкое восстановление изношенных деталей в специализированных цехах или на ремонтных предприятиях. Изношенные агрегаты и детали предприятия, эксплуатирующие оборудование, должны сдавать в приемно-об-менные пункты специализированных ремонтных организаций и взамен получать отремонтированные. Агрегатный метод ремонта возможен лишь при следующих основных условиях: межремонтный срок агрегатов должен быть достаточно длительным; агрегаты должны быть транспортабельны; конструкция самого оборудования должна обеспечивать возможность быстро и легко снимать и устанавливать на место отдельные агрегаты без большой и трудоемкой разборки всего оборудования.
В тех случаях, когда эксплуатирующая организация имеет значительный по количеству парк однотипного оборудования, можно создать свой оборотный фонд. В практике существует следующая связь между количеством агрегатов оборотного фонда и количеством оборудования
поступающего в ремонт в течение года:
где — коэффициент, учитывающий неравномерность поступления оборудования в ремонт, равный
— длительность простоя оборудования в ремонте, дни.
Для нетранспортабельного оборудования возможен абонементный (выездной) ремонт силами специализированных ремонтно-монтажных организаций, так как его перевозка экономически нецелесообразна в связи с большими затратами средств и времени на демонтаж и монтаж, а также сложна ввиду его малой транспортабельности.
2.8. Система технического обслуживания и ремонта
оборудования
В процессе эксплуатации техническое состояние оборудования, характеризующее его относительную способность и потенциальную возможность качественно и экономично выполнять заданные функции, постепенно ухудшается. Количественно эти изменения можно оценить совокупностью отклонений от начальных технических параметров, определяющих уровень работоспособности. Так, в процессе потребления технические параметры оборудования изменяются от номинальных значений до пре-
дельных обусловленных технико-экономиче-
ской целесообразностью эксплуатации. Разность между текущими и номинальными значениями этих величин определяет отклонение работоспособности от номинала. Вредные остаточные изменения могут вызвать быстрый выход оборудования из строя или, постепенно накапливаясь, через некоторый период эксплуатации привести его к предельному состоянию.
Таким образом, нормальное функционирование оборудования возможно в течение такого периода эксплуатации, при котором величина накопившихся остаточных изменений В0 не превзошла допустимого предела обору-
дование неисправно и требует проведения мероприятий по устранению накопившихся вредных остаточных изменений.
Технические параметры оборудования должны восстанавливаться целым комплексом организационно-технических мероприятий, т. е. совокупностью взаимосвязанных средств, документации и исполнителей, необходимой для поддержания и восстановления качества изделий, входящих в систему технического обслуживания и ремонта оборудования.
От видов технического обслуживания и ремонта зависит степень использования и соответственно рентабельность эксплуатации оборудования.
Цель технического обслуживания — подготовка оборудования к использованию по назначению, а также непосредственно по окончании работы к хранению, к переходу от одного сезона эксплуатации на другой и т.д. В связи с этим комплекс мероприятий по техническому обслуживанию должен содержать обязательный перечень проверочных и профилактических работ, выполняемых независимо от фактического состояния оборудования. Кроме того, при техническом обслуживании выполняются работы, вызванные отказами и неисправностями, обнаруженными в результате технического осмотра, который обязательно проводится при техническом обслуживании.
Устранение неисправностей и восстановление ресурса оборудования осуществляются путем ремонта. Объем ремонтных работ,
требующийся для возобновления работоспособности оборудования, зависит от ремонтных особенностей техники, качества выполняющихся ремонтов и технического обслуживания, условий и продолжительности эксплуатации машин без ремонта.
Поддержание оборудования в работоспособном состоянии может осуществляться мероприятиями двух систем: системы после-осмотровых ремонтов и периодических плановых ремонтов (ППР). Принципиальное отличие системы послеосмотровых ремонтов от ППР заключается в том, что планируются не ремонты, а периодические осмотры. На основании результатов осмотров устанавливается техническое состояние оборудования, в зависимости от которого намечаются сроки и вид ремонта.
Так как ремонты по этой системе планируются на основе данных о техническом состоянии оборудования, полученных путем периодических осмотров, точность планов ремонта, их соответствие действительной потребности в ремонте находятся в непосредственной зависимости от точности оценки технического состояния оборудования.
Сущность системы планово-предупредительного ремонта заключается в том, что оборудование, проработавшее определенное количество часов, подвергают осмотрам и плановым ремонтам.
Система ППР предполагает, что работы по ремонту оборудования планируются заранее и выполняются в определенной последовательности. Наименьшие повторяющиеся интервалы времени (наработка изделия), по истечении (достижении) которых выполняются в соответствии с требованиями нормативно-технической документации все установленные виды ремонта, называют ремонтным циклом. Перечень и последовательность выполнения этих работ в период между капитальными ремонтами (или с момента пуска нового оборудования в эксплуатацию и первым капитальным ремонтом), т.е. в течение ремонтного цикла, называют структурой ремонтного цикла.
Продолжительность и структуру ремонтного цикла устанавливают с учетом всех факторов, определяющих необходимость ремонтов. Расчет продолжительности ремонтного цикла сводится к корректировке исходного норматива длительности работы оборудования в течение ремонтного цикла в зависимости от ряда факторов, характеризующих особенности эксплуатации оборудования. Например, расчетная формула для определения продолжительности эксплуатации до первого капитального ремонта выглядит так:
где — исходный норматив работы оборудования, ч;
—
коэффициент, учитывающий тип производства; — коэффици-
снт, учитывающий род обрабатываемого изделия; — коэф-
фициент, учитывающий условия эксплуатации оборудования; 0,25 — 25 % длительности ремонтного цикла (начиная со второго цикла, т.е. после первого капитального ремонта
из расчета исключается).
Интервал времени работы оборудования между двумя ближайшими ремонтами называют межремонтным периодом. Продолжительность межремонтного периода определяют из выражения
где — количество соответственно средних и текущих ре-
монтов в ремонтном цикле; для первого цикла продолжительность периода увеличивается на
Период работы оборудования между двумя очередными осмотрами или между очередным плановым ремонтом и осмотром называют межосмотровым и определяют по формуле
где — количество осмотров в ремонтном цикле.
Структура ремонтного цикла определяется сроками службы основных деталей, подлежащих замене при том или ином виде ремонта, а также технологическим назначением оборудования. При определении структуры ремонтного цикла обычно исходят из того, что все детали делят на отдельные группы с одинаковыми сроками службы и кратностью сроков износа деталей различных групп и сочленений.
Однако подбор групп деталей и агрегатов, имеющих сроки износа не только равные, но и кратные срокам износа одной группы деталей, — задача трудно выполнимая. Поэтому распределение всех деталей оборудования по группам и установление периодичности ремонта в соответствии со сроками его службы в значительной степени условно и не может считаться обязательным для всех предприятий. Предприятия должны самостоятельно устанавливать оптимальную периодичность ремонтов, исходя из технического состояния оборудования, его возрастной структуры, условий эксплуатации и других факторов.
Структура ремонтного цикла оборудования различной сложности весьма разнообразна. Для технологического оборудования предприятий возможны следующие чередования видов ремонта:
текущие, средние и капитальный;
текущие и капитальный;
средние и капитальный;
текущие.
Чередования видов ремонта через определенные промежутки времени обусловливается рациональной структурой ремонтного
цикла в зависимости от видов предприятий сервиса и оборудования. Например, структура ремонтного цикла следующая: для машин химической чистки и стирки одежды
где К, С и Т — соответственно капитальный, средний и текущий ремонты; О — технический осмотр;
отделочного оборудования предприятий химической чистки
металлорежущего оборудования
кузнечно-прессового оборудования
раскройно-ленточного швейного оборудования
Определение периодичности ремонтов, ремонтных циклов и его структуры для каждого типа оборудования имеет большое технико-экономическое значение, так как этим определяются затраты на ремонтные работы, длительность простоев оборудования в ремонте и степень использования оборудования в работе. При определении периодичности ремонтов необходимо, чтобы плановый ремонт полностью предусматривал потребность в нем. При этом в межремонтные периоды оборудование должно работать бесперебойно при минимальной продолжительности технического обслуживания. Межремонтные периоды не должны быть слишком малыми, так как это вызывает сокращение продолжительности работы оборудования и одновременно увеличивает длительность простоя из-за ремонта.
Планируемый объем работ по системе планово-предупредительного ремонта определяется планом-графиком на ремонт оборудования. При составлении плана-графика учитываются межремонтные периоды и ремонтные циклы, которые в зависимости от про-
должительности работы и количества выполненных ремонтов оборудования должны соответствовать установленным для предприятия периодичности ППР и срокам его простоя в ремонте. Отдел главного механика составляет годовой план-график ремонта.
При составлении плана-графика ремонта кроме технического состояния оборудования необходимо учитывать возможность одновременного ремонта различных машин, работающих в потоке и связанных единым технологическим процессом, или поочередного ремонта однотипных агрегатов. Это позволяет компенсировать простой ремонтируемого оборудования более интенсивной работой другого оборудования. При планировании и осуществлении ремонтных работ необходимо возможно полнее использовать нерабочие смены, выходные и праздничные дни, чтобы снизить потери рабочего времени и повысить коэффициент использования оборудования.
Годовой план-график планово-предупредительных ремонтов оборудования составляют по соответствующей форме (табл. 2.1). В график для соответствующего месяца проставляют число, а также буквенные символы с дробными числами (например, ЮТ 200/19; 5С 1 170/77). Буквы обозначают вид ремонта (Т, С), в числителе показывается трудоемкость ремонта (нормо-ч), а в знаменателе — длительность простоя оборудования в ремонте (ч). Исполнение ремонта отмечают штриховкой соответствующей клетки в графике с указанием даты. На основании годового плана и учета отработанных смен (часов) составляют ежемесячные планы-графики.
Чтобы составить график ППР и определить объем ремонтных работ, необходимо знать периодичность ремонта каждого вида технологического оборудования и нормы продолжительности ремонтов.
Для определения количества ремонтов в год необходимо знать ремонтный цикл, количество однотипного оборудования, находящегося в работе, коэффициент использования и календарный фонд времени работы оборудования.
Коэффициент использования оборудования можно определять как по основной продолжительности технологического цикла
так и по календарной продолжительности работы оборудования
— основная продолжительность технологического цикла, ч;
— штучно-кулькуляционная продолжительность, ч;
— фактическая продолжительность работы оборудования, ч;
— календарная продолжительность работы оборудования, ч.
Дата добавления: 2015-12-17; просмотров: 12; Мы поможем в написании вашей работы! |
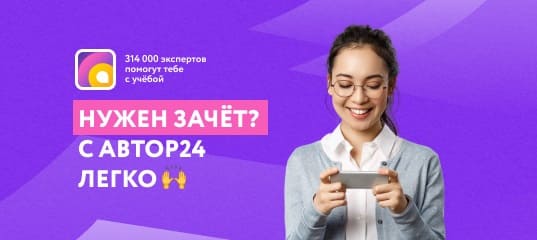
Мы поможем в написании ваших работ!