Трудоемкость ремонтов на единицу ремонтной сложности механической части технологического оборудования по видам работ, нормо-ч 3 страница
Основные рабочие устройства аппаратов, как правило, неподвижны. Энергия в аппаратный процесс передается от ее источника к рабочим устройствам, с которыми взаимодействует обрабатываемый объект.
Иногда аппараты включают в себя вспомогательные механические устройства для транспортирования обрабатываемых объектов, интенсификации процессов и др.
Взаимодействие между рабочими органами машины и обрабатываемым объектом составляет основную часть физической сущности технологического процесса, изучение которой является весьма важным, так как это позволяет качественно и количественно определить технологические параметры обработки и выбрать оптимальные формы, размеры и другие технические характеристики рабочих органов.
В зависимости от закономерностей протекающих процессов последние объединены в следующие основные группы.
Механические процессы, описываемые в основном законами механики твердых тел. К этой группе относят механическую обработку и механическое движение материалов и изделий.
Гидромеханические процессы, описываемые законами гидромеханики. К данной группе относятся: перемещение жидкостей и газов через трубопроводы и аппараты, разделение жидких и газовых неоднородных систем, перемешивание материалов и обработка изделий в жидкой и газовой средах и др.
Тепловые процессы, описываемые законами теплообмена и включающие в себя теплопередачу, нагревание, охлаждение и конденсацию.
|
|
Диффузионные (массообменные) процессы, описываемые законами массообмена и включающие в себя перегонку, сушку материалов и изделий, сорбцию.
Химические процессы, описываемые законами физико-химических взаимодействий. К ним относятся мойка одежды в среде органических растворителей, обработка изделий в среде поверх-
28
ностно-активных веществ и др. Необходимо заметить, что химических процессов в чистом виде, т. е. не сопровождающихся другими процессами, почти не существует. Как правило, они происходят одновременно с тепловыми (теплопередача и др.), механическими (перемешивание материалов и др.), диффузионными и прочими процессами.
Технологический процесс делится на части, называемые операциями. Операцией называется законченная часть технологического процесса, выполняемая на одном рабочем месте.
Машинный и аппаратный технологические процессы состоят из отдельных операций, которые можно разделить на основные (технологические) и вспомогательные (нетехнологические). К основным операциям относятся непосредственные действия по обработке объекта, дающие технологические результаты (изменение формы, размеров, свойств и т.д.), к вспомогательным — загрузоч-но-, установочно-съемные, внутримашинные и внутриаппарат-ные, контрольно-измерительные и операции управления.
|
|
Вспомогательные операции не приводят к изменению свойств материалов или изделий. Они не связаны непосредственно с изготовлением нового или восстановлением потребительских свойств какого-то изделия. Операции структурно подразделяются на переходы — законченную часть операции, характеризующуюся постоянством инструмента и поверхностей, образуемых обработкой.
В задачу проектирования технологического процесса входит установление содержания и последовательности выполнения операций, т.е. разработка технологической схемы производства. При ее проектировании руководствуются следующими основными критериями:
• формами и способами производства услуг (изделий);
. режимом работы;
• формами снабжения предприятий полуфабрикатами, сырьем, материалами и др.;
• уровнем механизации основного процесса;
• уровнем специализации (концентрации) процесса производства услуг.
2.2. Принципы организации производственного
процесса
Организация производственных процессов строится на следующих принципах: параллельности, пропорциональности, непрерывности, прямоточности, ритмичности, гибкости.
|
|
Принцип параллельности выполнения частичных процессов (операций) предусматривает расчленение производственного процесса
на отдельные организационные операции, закрепление их за определенным рабочим местом для постоянного выполнения. В этом случае обеспечивается равномерная работа каждого производственного участка и, следовательно, всего предприятия в целом, сокращается длительность производственного цикла и оказания услуги. Соблюдение данного принципа организации производственных процессов особенно актуально на предприятиях, занимающихся изготовлением новых изделий (товаров) по заказам населения (пошив одежды, обуви, изготовление трикотажных изделий, мебели и др.).
Принцип пропорциональности предполагает взаимное соответствие пропускной способности отдельных цехов и участков, участвующих в выполнении услуги. Она достигается тем, что количество рабочих мест цехов и участков определяется исходя из трудоемкости выполняемых частичных процессов. Особо важное значение этот принцип имеет при организации работ по выполнению услуг на основе технологического разделения труда. В этом случае рассчитываются алгоритм технологического процесса изготовления (ремонта) изделия и основные и дополнительные условия согласования продолжительности выполнения операций. Нарушение пропорциональности приводит к нарушению равномерности работы предприятия, простою оборудования и рабочих и, в конечном счете, ухудшает показатели производственно-хозяйственной деятельности участков, цехов, предприятия в целом.
|
|
Однако следует учитывать, что на соблюдение принципа пропорциональности в производственных процессах обязательно будет оказывать влияние сезонный характер выполнения услуг. Поэтому предприятия сервиса при проектировании производственных процессов должны учитывать эту особенность выполнения услуг, разрабатывать мероприятия по выравниванию сезонной волны спроса населения на услуги.
Принцип непрерывности процесса выполнения услуги предполагает сокращение до минимума перерывов в процессе изготовления, ремонта, восстановления потребительских свойств изделия и прохождения его от первой до последней технологической операции. На рабочем месте непрерывность достигается при выполнении каждой операции путем сокращения продолжительности вспомогательных подготовительных операций; на участке, в цехе — при передаче полуфабриката (изделия) с одного рабочего места на другое; на предприятии в целом — сведением до минимума межцеховых перерывов.
Соблюдение принципа непрерывности технологического процесса достигается благодаря: разработке рациональных структур технологических процессов; использованию эффективных форм разделения и кооперации труда; построению оптимальных пла-
нировок рабочих мест производственных цехов и участков. В конечном счете непрерывность технологических процессов обеспечивает более полное использование оборудования, рабочего времени, производственных площадей, материальных и энергетических ресурсов. Все это позволяет максимально ускорить оборачиваемость оборотного капитала предприятия, снизить трудоемкость, повысить производительность труда работников предприятия сервиса, увеличить объем реализации услуг.
Принцип прямоточности характеризуется прямолинейным и кратчайшим путем движения деталей, узлов, изделий по рабочим местам, производственным участкам или цехам. Он достигается рациональным размещением оборудования в соответствии с последовательностью технологического процесса и недопущением возврата полуфабриката (изделия) в ходе его обработки. Соблюдение принципа прямоточности способствует сокращению числа переместительных операций и времени, которое затрачивается на их выполнение; сокращениям длительности производственного цикла и продолжительности оказания услуг.
Принцип ритмичности означает регулярное повторение всех элементов производственного процесса во времени. Ритмичность достигается: своевременным регулярным запуском исходных материалов (полуфабрикатов, изделий) в производственный процесс выполнения услуг; соблюдением норм времени и обязательным выполнением всех вспомогательных процессов. Соблюдение принципа ритмичности способствует соблюдению сроков выполнения услуг и росту объемов их реализации.
Принцип гибкости производственных процессов означает способность производственного процесса быстро переналаживаться в соответствии с изменениями во внешней среде. Для предприятий сервиса с их разнообразием оказываемых услуг, сезонным характером спроса этот принцип организации производственных процессов в сегодняшних условиях особенно значим. Данный принцип реализуется за счет использования на предприятиях сервиса высококвалифицированных рабочих-универсалов, создания комплексных бригад с частичной и полной взаимозаменяемостью работников и др. Соблюдение данного принципа позволяет предприятию лучше адаптироваться к происходящим изменениям и выжить в жесткой конкурентной борьбе на рынке товаров и услуг.
2.3. Формы организации производственного процесса
Важнейшими формами организации производственного процесса являются специализация и кооперирование.
Специализация является формой разделения труда. Специализация на уровне предприятия означает концентрацию выполнения однородных услуг, однородной продукции, однородных видов работ в подразделении предприятия.
На уровне предприятия используется несколько видов специализации:
• предметная, когда за структурным подразделением предприятия закрепляется производство определенного вида продукции, выполнение определенного вида услуг;
• подетальная ~ закрепление за структурным подразделением изготовления отдельных узлов и деталей изделий;
• технологическая — закрепление за структурным подразделением определенной стадии технологического процесса.
На предприятиях сервиса получили распространение предметная и технологическая специализация. Каждый из них имеет свои достоинства и недостатки.
Так, при предметной специализации: упрощаются внутрипроизводственное кооперирование, планирование деятельности, повышается ответственность руководителей подразделений за сроки и качество выполнения работ; создаются условия для повышения уровня механизации труда и внедрения прогрессивных форм и методов работы. Однако рыночные условия хозяйствования диктуют постоянное расширение номенклатуры и ассортимента выполняемых услуг и работ, поиск новых видов оборудования, инструментария, современных технологий и, следовательно, нередко вступают в противоречие с процессами определенной специализации.
Технологическая форма специализации встречается на предприятиях почти повсеместно. Ее достоинства следующие: способствует применению рациональных технологий; создает возможности наиболее полного использования оборудования и материалов; обеспечивает большую гибкость производства при освоении новых видов услуг. Но технологическая специализация имеет и такие недостатки: ответственность руководителей ограничивается лишь выполнением отдельной части производственного процесса; несколько усложняется внутрифирменное планирование.
Кооперирование является формой организации производства. Оно предусматривает объединение и установление рациональных взаимосвязей между цехами, участками, отдельными исполнителями для выполнения общей работы.
Важнейшей формой кооперирования производства является кооперирование труда, т.е. совместное участие людей в одном или разных, но связанных между собой процессах труда. Основной формой кооперирования труда является производственная бригада.
2.4. Технология производства услуг в зависимости от вида предприятия сервиса
Среди материальных услуг стирка белья, химическая чистка и крашение одежды занимают важное место и являются перспективными видами, базирующимися на индустриальной основе. Современные фабрики-прачечные и фабрики химической чистки представляют собой высокомеханизированные предприятия, выполняющие комплекс технологических операций по обработке белья и одежды.
Технологический процесс обработки белья на фабриках-прачечных является довольно сложным и состоит из ряда операций. Структурная схема обработки белья на фабриках-прачечных приведена на рис. 2.1.
Рис. 2.1. Структурная схема обработки белья на фабриках-прачечных
2 Болгов 33
![]() |
![]() |
Рис. 2.2. Структурная схема обработки изделий на фабриках химической
чистки
Химическая чистка изделий включает в себя процессы мойки, отжима, сушки, а также процессы облагораживания и влажно-тепловой обработки. Структурная схема обработки изделий на фабриках химической чистки приведена на рис. 2.2.
Для химической чистки одежды и стирки белья характерны следующие процессы:
• физико-химические — обработка изделий в среде органических растворителей, в водных растворах поверхностно-активных веществ, крашение изделий и др.;
• массообменные процессы — сушка, увлажнение, дистилляция и др.;
• теплофизические и физические — нагревание, охлаждение, адсорбция;
• механические и гидромеханические — прессование, перемешивание, отстаивание, центрифугирование, фильтрование и др.
При ремонте и изготовлении швейных изделий, головных уборов и галантереи технологические операции включают в себя главным образом следующие механические процессы: резание, перемеще-
ние (подача) штучных изделий, скрепление деталей одежды ниточным способом, прессование и формование изделий и др. Кроме того, имеют место массообменные (увлажнение и сушка) и тепловые (нагревание и охлаждение) процессы, а в связи с созданием новых видов клеев — физико-химические (клеевые) процессы при скреплении деталей одежды и с распространением синтетических термопластичных материалов — физические процессы (ультразвуковая и высокочастотная обработка материалов свариванием).
При ремонте и изготовлении обуви в основном имеют место следующие процессы обработки материалов и изделий:
• механические — резание при раскрое материалов, скрепление деталей нитками, гвоздями, шпильками, прессование и формование давлением, формование растяжением и изгибом, открепление изношенных деталей при ремонте обуви и др.;
• физико-химические — склеивание, вулканизация, вощение, нанесение пленочных покрытий и др.;
• массообменные — сушка, увлажнение и др.;
• тепловые — главным образом нагревание и охлаждение.
Услуги по изготовлению и ремонту хозяйственно-бытовых изделий имеют гибкий технологический процесс, который в кратчайшие сроки должен переналаживаться под нужный вид изделий. Вместе с тем производство услуг должно быть безотходным, с минимальными затратами на приобретение исходного материала. Структурная схема производства хозяйственно-бытовых изделий на примере изделий из полимерного материала приведена на рис. 2.3, где указаны основные операции технологического процесса. Так, в соответствии с условиями поставки сырья предприятиями-изготовителями предприятию по переработке полимерных материалов на нем предусматривается прием сырья в мешках. Сырье в мешках на поддонах снимается с машин цеховым транспортером и перевозится на склад.
Хранение сырья, поступившего в мешках, осуществляется партиями в цеховом складе. Цеховой склад должен быть спроектирован из расчета 10... 15 суточных запасов сырья. Оптимальным является стеллажный способ хранения сырья на поддонах. Для улучшения использования высоты помещений используются штабелеры, с помощью которых осуществляются установка и выем пакетированного сырья. Управление штабелером может быть местным или дистанционным.
Растаривание сырья, поступившего в мешках с цехового склада, осуществляется на растарочной установке, после чего термопласты перегружаются либо в цеховые вместимости, либо в контейнеры.
Поступившее сырье сопровождается соответствующей документацией. Для определения параметров перерабатываемое™ сырья,
Рис. 2.3. Структурная схема производства хозяйственно-бытовых изделий
а также соответствия показателей величинам, указанным в сопроводительном документе, проводится так называемый входной контроль сырья. В ходе этого контроля определяются однородность материала и партии и индекс расплава.
Подготовка сырья (полимерного материала) выполняется в зависимости от технических условий по его переработке, требований к качеству готовой продукции, к поверхности изделий и к их окраске. В связи с этим в отделении подготовки могут выполняться операции сушки сырья и смешивания его с концентратами красителей.
Транспортирование сырья с участка подготовки или со склада сырья и подача его в бункер литьевой машины предполагают выбор способа транспортирования сырья, который зависит от режима работы и мощности литьевых машин, постоянства номенклатуры изделий, организации производства, типа сырья.
Для формования изделий применяют литьевые машины. Некоторые из отлитых изделий подвергаются механической обработке. Их количество составляет не более 15 % общего объема производства изделий. К основным видам механиче-
ской обработки относятся удаление литниковых систем, сверление, фрезерование, зачистка и полировка.
Выходной контроль предполагает окончательную проверку соответствия изделий установленным параметрам (на основании ТУ или требований к технологическому регламенту производства), после чего проводятся упаковка, укладка и дозирование готовых изделий.
Процесс упаковки определяется требованиями, предъявляемыми к изделиям, организацией производства и режимом работы оборудования.
В зависимости от требований, предъявляемых к изделиям, устанавливается способ укладки, который может производиться внасыпь или с упорядоченной укладкой.
Дозирование изделий может быть весовым и поштучным. В зависимости от размера изготовляемых изделий определяется способ их дозирования.
С окончанием технологических операций по выпуску хозяйственно-бытовых изделий из термопластов методом литья под давлением производится переработка отходов, которые подразделяются на безвозвратные и возвратные. Безвозвратные отходы представляют собой потери в виде газообразных выделений (мономеры и другие продукты деструкции полимеров, пары воды и т.п.), а также потери при транспортировании, механической обработке, при отработке технологического режима на машине, вышедшей из ремонта.
Возвратные отходы — это некондиционная продукция, полученная в наладочном режиме, а также изделия, подвергающиеся испытанию, и др.
Возвратные отходы после переработки (дробления или грануляции) должны использоваться для изготовления этих же изделий в качестве добавок к исходному сырью (10... 15 %) или, если это разрешено техническими условиями, для производства неответственных изделий другого назначения.
При использовании отходов для изготовления тех же изделий целесообразно их переработку организовать непосредственно у литьевых машин и дробленые отходы добавлять к исходному сырью.
2.5. Оборудование предприятий сервиса
Средствами выполнения технологического процесса являются технологическое оборудование и технологическая оснастка. Технологическим оборудованием называются орудия производства, в которых для выполнения определенной части технологического процесса размещаются материалы или заготовки, средства воздействия на них и при необходимости источники энергии.
Каждому виду обработки изделия соответствует свой тип технологического оборудования, который имеет свое конструктивное построение, обусловленное применением специальных рабочих органов, работающих на определенных принципах действия, при определенных режимах.
Технологическая оснастка — средства, с помощью которых выполняется технологический процесс.
Оборудование, эксплуатируемое на предприятиях сервиса, выполняет различные технологические процессы и операции. Исходя из характера технологических процессов и операций, структуры и типа предприятий, а также объема услуг, оказываемых населению, оборудование может подразделяться на основное, вспомогательное и энергетическое.
Одним из основных резервов повышения эффективности предприятий сервиса, снижения себестоимости и повышения качества услуг, оказываемых населению, снижения затрат ручного труда, является использование вспомогательного оборудования. Вспомогательное оборудование широко применяется для метки, упаковки, транспортирования, механизации погрузочно-разгру-зочных, подъемно-транспортных и складских работ, а также других операций.
Различные технологические операции, эксплуатация оборудования требуют расхода двигательной и тепловой энергии, основными источниками которой на предприятиях служит энергетическое оборудование, снабжающее предприятия паром, горячей водой, сжатым воздухом, вакуумом. Электроэнергию для этих целей предприятия получают от централизованных источников через трансформаторные подстанции.
Парк технологического оборудования предприятий весьма разнообразен. В то же время имеются группы оборудования с одинаковыми признаками, которые могут быть положены в основу классификации. К этим признакам относятся: характер воздействия на обрабатываемый объект (изделия, основные и вспомогательные материалы); род действия оборудования; степень автоматизации; сочетание отдельных видов оборудования в производственном потоке. Кроме того, технологическое оборудование можно классифицировать в зависимости от его функционального назначения.
По характеру воздействия на объект оборудование можно разбить на две группы: машины и аппараты. В машинах объект обработки (изделие) подвергается механическому воздействию, может изменять форму, размеры и другие качественные и количественные показатели. В аппаратах изделия подвергаются воздействию тепловой, химической, световой энергии, в результате которого изменяются их физические и химические свойства.
По принципу действия оборудование можно классифицировать на оборудование периодического, непрерывно-поточного и
непрерывно-циклического действия. В машины и аппараты п е-риодического действия изделия загружают определенными партиями, причем каждая последующая партия изделий загружается после обработки и выгрузки из машины предыдущей. Режим работы таких машин и аппаратов во время работы изменяется во времени.
В машины непрерывно-поточного действия изделия подаются непрерывно и непрерывно обрабатываются. Режим работы такого оборудования во времени постоянен.
В машинах непрерывно-циклического действия технологический процесс осуществляется непрерывно, но циклически. Подача изделия в машину может быть поштучной или партионной. В определенной зоне обработка прерывается, а затем после автоматического перемещения изделия начинают обрабатываться в новой зоне.
По степени автоматизации машины подразделяются на неавтоматические, полуавтоматические и автоматические.
В машинах неавтоматическогодействия вспомогательные операции (загрузка, контроль, выгрузка) и некоторые другие выполняют вручную. В машинах полуавтоматического действия только основные операции — технологические и некоторые вспомогательные (например, контрольные) — выполняются без участия оператора.
В машинах автоматического действия все операции (контроль, управление, регулирование) выполняются автоматическими устройствами.
По принципу сочетания в производственном потоке различают машины отдельные, агрегатные, комбинированные и системы машин — линии.
Отдельные (частные) машины могут выполнять только отдельные технологические операции.
Агрегатные машины — это машины, объединенные для выполнения нескольких технологических операций или технологического процесса в определенной последовательности. Такие машины ускоряют процесс, экономят производственные площади.
Комбинированные машины — это сочетание нескольких простых машин, соединенных в одну. Такие машины выполняют определенный законченный цикл операций и процессов и являются более совершенными, чем агрегатные.
Система машин — линии — включает в себя как частные, так и комбинированные машины, объединенные на базе комплексной механизации и автоматизации для выполнения сложных многооперационных технологических процессов непрерывно-циклическим или непрерывно-поточным методом.
Основной характеристикой любого оборудования (машины и аппарата), определяющей целесообразность его применения, яв-
ляется производительность, т.е. количество перерабатываемого сырья или получаемого продукта за единицу времени (например, шт./ч, кг/ч, м/ч и т.д.). Единица измерения производительности зависит от функционального назначения оборудования.
При анализе конструкций технологического оборудования необходимо различать производительность теоретическую техническую (технологическую) П и эксплуатационную
Разграничение понятий теоретической, технической и эксплуатационной производительности имеет существенное значение. С точки зрения потребителя важна техническая производительность (например, при выборе технологического оборудования) и эксплуатационная (например, при анализе хозяйственной деятельности предприятий), но они предопределяются теоретической производительностью.
Теоретическая производительность определяется конструктивно-технологическими параметрами и характеризует конструктивные качества, рабочие и технологические параметры оборудования, вид и количество пространственных связей изделия и т.д. Она измеряется количеством изделий (работой), которое можно было бы получить с помощью данного оборудования в единицу времени при условии, что все внецикловые операции, связанные с обслуживанием оборудования, сведены к нулю. В общем теоретическую производительность можно определить по формуле
где — основная продолжительность цикла;
— вспомогательная длительность, не совмещенная с основной продолжительностью цикла;
— длительность рабочего цикла оборудования.
Анализ уравнения показывает, что повышение теоретической производительности может быть осуществлено за счет повышения технологических параметров режима обработки изделий и уменьшения вспомогательной длительности цикла, мерой которой служит степень автоматизации производственного процесса.
Однако ряд практических обстоятельств и неодинаковая воз- можность реализации этих параметров делают их далеко не равноценными в решении проблемы теоретической производительности. Так, материал изделия и его состояние являются факторами, определяющими производительность оборудования, но ими конструктор не управляет. Повышение технологического режима вне связи со вспомогательной длительностью цикла также не всегда приводит к желаемым результатам. Теоретическая производительность оборудования характеризуется условиями его работы, технологическими и конструктивными параметрами, а также характером обрабатываемых изделий (материалов).
Техническая производительность отличается от теоретической тем, что она отражает потери времени, связанные с техническим обслуживанием.
Эксплуатационная производительность определяется количеством продукции, производимой в единицу времени, с учетом потерь времени на выполнение всех вспомогательных работ, устранение отказов и простои из-за неудовлетворительной организации производства:
где — длительность останова оборудования соответ-
ственно для технического обслуживания, для организационного обслуживания, на отдых; — длительность подготовительно-заключительного периода;
— длительность неучтенных потерь в работе.
Если обозначить символом о отношение продолжительности производительной работы оборудования к полной продолжительности работы оборудования, то эксплуатационная (действительная) производительность выразится формулой
Отношение эксплуатационной производительности к технической будет показывать коэффициент использования технической производительности:
Повышение эксплуатационной производительности при эксплуатации оборудования достигается прежде всего за счет оптимальный организации производственного процесса на предприятии.
Дата добавления: 2015-12-17; просмотров: 10; Мы поможем в написании вашей работы! |
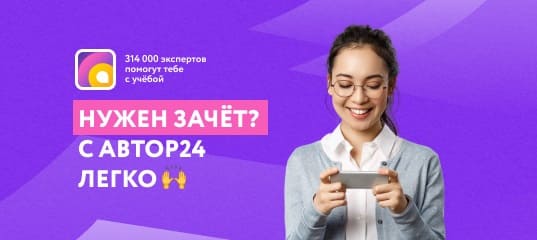
Мы поможем в написании ваших работ!