Нагревательно-фракционирующая часть (НФЧ).
Продукты крекинга из реактора Р-1 в смеси с водяным паром поступают под первую тарелку контактной зоны ректификационной колонны К-1.
Колонна К-1:
- температура верха - не более 130 °C;
- температура низа отстойной части - не более 350 °C;
- давление верха - до 0,9 кгс/см2.
Для осаждения катализаторной пыли, увлеченной парами крекинга из реактора Р-1, на верхнюю тарелку контактной зоны К-1 подается декантат - фракция выше 350 °C.
Декантат из отстойной зоны колонны К-1 забирается насосом Н-4, 4а, проходит трубные пучки подогревателя Т-9, теплообменник сырья Т-10 и возвращается на верхнюю каскадную тарелку контактной зоны колонны К-1.
Схемой предусмотрена возможность дополнительного охлаждения декантата в холодильнике Х-18 для снижения температуры ввода Декантат в колонну К-1.
Декантат стекает с каскадных тарелок в нижнюю отстойную зону колонны К-1, при этом часть паров крекинга конденсируется, а остальная часть, очищенная от катализаторной пыли, поступает в ректификационную зону колонны К-1.
Для поддержания коксовой нагрузки регенератора Р-2, схемой предусмотрена возможность подачи в качестве рисайкла части декантата с нагнетания насосов Н-4, 4а в сырье перед узлом смешения с катализатором.
С низа отстойной зоны К-1 шлам насосами Н-3, 3а, 3б подается в Р-1.
На приемных трубопроводах шлама из К-1 к Н-3, Н-3а, Н-3б смонтированы фильтры для предотвращения забивки шламовых форсунок реактора Р-1 мехпримесями.
|
|
Для стабильной работы шламовых насосов предусмотрена периодическая промывка последних тяжелым газойлем от насоса Н-6.
Схемой предусмотрена возможность вывода части кубового продукта колонны К-1 по линии периодической промывки шламовых насосов через выкидной коллектор насоса Н-6 в линию тяжелого газойля с установки.
Для предотвращения слёживания катализаторной пыли в нижней части К-1 предусмотрена подача декантата в маточник, расположенный вокруг “стакана” вывода шлама из колонны К-1.
Несконденсирующиеся пары продуктов реакции из контактной зоны через полуглухую тарелку поступают в ректификационную зону колонны К‑1.
C полуглухой тарелки К-1нефтепродукт (тяжелый газойль) забирается насосами Н-5,5а и подается по следующим направлениям:
а) для регулирования температурного режима низа ректификационной зоны К-1, в качестве первого промежуточного орошения (далее 1 ПЦО) прокачивается через трубное пространство теплообменника Т-7, рибойлера Т-8, холодильника Х-33 и возвращается на 5,7 тарелки колонны К-1.
б) в целях промывки нижней части отстойной зоны К-1 схемой предусмотрена подача части продукта 1 ПЦО с выкида Н-5,5а на «промывочное» кольцо с целью исключения отложений механических примесей и катализаторной пыли в кубе колонны К-1.
|
|
в) избыток продукта (тяжелый газойль) насосами Н-5,5а через трубное пространство теплообменников Т-23, холодильников Х-14, Х-14а (по межтрубному) откачивается с установки. При необходимости возможно дополнительное охлаждение тяжелого газойля после теплообменника Т-23 в холодильнике Х-18. Технологической схемой предусмотрена возможность откачки тяжелого газойля с полуглухой тарелки К-1 насосом Н-6 при низкой производительности по сырью. Технологической схемой предусмотрена возможность подачи части тяжелого газойля в линию ввода сырья в Р-1 с целью регулирования коксовой нагрузки.
Для регулирования температурного режима средней зоны ректификационной колонны К-1 применяется 2-ое промежуточное циркуляционное орошение (2 ПЦО).
Фракция свыше 195 °С с 14 и 16 тарелок колонны К-1 самотеком поступает в колонну К-3. Колона К-3 является буфером-накопителем фракции свыше 195 °С и предназначена для обеспечения стабильной работы подающих в К-1 второе промежуточное циркуляционное орошение (2ПЦО) насосов Н-10, 10а. Углеводородные пары из К-3 через «дыхательную линию» возвращаются под 13 тарелку К-1.
Нефтепродукт из К-3 поступает на прием насосов Н-10, 10а, прокачивается через сырьевой теплообменник Т-6 (трубное пространство), АВО-7 и в качестве 2 ПЦО возвращается на 19 тарелку К-1. Легкий газойль (фракция (195-310) °C) с 20, 22 тарелок колонны К-1 поступает в отпарную колонну К-2, где водяным паром отпариваются более легкие фракции, которые возвращаются обратно в колонну К-1 под 23 тарелку. Для равномерного распределения пар в колонну К-2 подается через маточник
|
|
С низа колонны К-2 легкий газойль поступает на прием насосов Н-7, 7а и подается по следующим направлениям:
а) Прокачивается через трубное пространство теплообменников Т-5,Т-21, в которых происходит нагрев сырья, поступающего на установку, холодильники Х-13, Х-4 и выводится с установки.
б) Прокачивается через теплообменники Т-19, Т-20, Т-22, АВО-7, холодильники Х-34а, Х-15а и подается в качестве абсорбента в повторный абсорбер К-5.
Насыщенный абсорбент из К-5, за счет разности давления в К-5 и К-1, поступает на 21, 23-ю тарелки колонны К-1. Часть охлажденного легкого газойля после Х-4 поступает на прием насосов Н-17, 17а и используется в качестве затворной жидкости на торцевые уплотнения горячих насосов Н-3, 3а, 3б, Н-4, 4а, Н-5, 5а, Н-6, 6а, Н-7, 7а, Н‑10, 10а. С линии выхода легкого газойля с установки (в случае большой коксовой нагрузки в регенераторе Р-2) предусмотрен возврат части легкого газойля на прием сырьевых насосов Н-1,1а,1б.
|
|
Для более четкого регулирования температуры верхней части К-1 схемой предусмотрено верхнее циркуляционное орошение (ВЦО). Бензин с 28 тарелки К-1 поступает на прием насосов Н-11, 11а, охлаждается в АВО-10, 11, холодильнике Х-15 и поступает на 31 тарелку К-1.
Технологической схемой предусмотрена возможность подачи части верхнего циркуляционного орошения (тяжелый бензин) с нагнетания Н-11, 11а в линию стабильного бензина из Т-9 в Т-11. С верха колонны К-1 жирный газ, пары бензина и водяной пар поступают параллельно в аппараты воздушного захолаживания АВО-3, 4, 5, 6, 8, 9 и далее на доохлаждение в конденсаторы-холодильники ХК-1, 1а, 1б, 1в, откуда газожидкостная смесь направляется в газосепаратор Е-1.
Схемой предусмотрена возможность параллельной и последовательной работы АВО-3, 4, 5, 6, 8, 9 и ХК-1, 1а, 1б, 1в.
В газосепараторе Е-1 происходит отстаивание бензина от воды. Водяной конденсат собирается в грязевике Е-1. Нестабильный бензин из газосепаратора Е-1 поступает на прием насосов Н-8, 8а и подается на верх колонны К-1 в качестве острого орошения.
Технологической схемой предусмотрена взаимозаменяемость насосов Н-9, 9а и Н-8, 8а.
Технологической схемой предусмотрена возможность подачи части острого орошения с выкида насосов Н-8,8а (Н-9,9а) в линию ВЦО перед К-1.
Газофракционирующая часть (ГФЧ)
Балансовый избыток нестабильного бензина из газосепаратора Е-1 забирается насосами Н-9, 9а и подается на верхнюю 26, 30 тарелку фракционирующего абсорбера К-4. Схемой предусмотрена возможность подачи нестабильного бензина на нижнюю 8 тарелку отпарной зоны и среднюю 12 тарелку абсорбционной части колонны К-4.
Колонна К-4:
- давление верха - не более 11 кгс/см2;
- температура верха - не более 47 °С;
- температура низа - не более 127 °С.
Предусмотрена аварийная схема подачи нестабильного бензина с нагнетания Н-9, 9а:
-в стабилизатор К-6 помимо колонны К-4;
-на выход с установки помимо блока ГФЧ.
Технологической схемой предусмотрена взаимозаменяемость насосов Н-9, 9а и Н-8, 8а.
Жирный газ из газосепаратора Е-1 после отделения жидкой фазы последовательно поступает в колонну К-0, емкости Е-6, 6а, а затем на прием газовых нагнетателей В-1а, В-1б для компремирования до давления 1,1 МПа (11 кгс/см2).
Конденсат из К-0, Е-6, 6а забирается насосами Н-19, 19а и откачивается в газосепаратор Е-1.
При необходимости увеличения давления в Р-1, часть газа с нагнетания В-1а, 1б по циркуляционной линии через холодильник Х-16а возвращается обратно на прием компрессоров В-1а, 1б (через Е-6,Е-6а).
При резком повышении давления на приеме В-1а, 1б или их остановке, схемой предусмотрена возможность аварийного сброса газа из Е-1 через гидрозатвор Е-101 на факел ФНД. В гидрозатвор подается оборотная вода 2 системы на проток со сбросом в промканализацию.
Основной поток компримированного газа с выкида газового нагнетателя В-1а, 1б поступает на охлаждение параллельными потоками в холодильник Х-16 и в аппарат воздушного захолаживания АВО-1 (возможно подключение АВО-2), холодильник Х-2. После охлаждения газожидкостная смесь направляется в емкость Е-2, где происходит разделение жидкой и газовой фазы. Для регулирования давления по тракту Р-1, К-1, Е-1 предусмотрена схема возврата углеводородного газа после Х-2 в циркуляционную линию компрессора
Газ из Е-2 поступает на 21 тарелку отпарной части колонны К-4. Схемой предусмотрена также подача охлажденного газа с выкида В-1а, 1б в стабилизационную колонну К-6 при отключенном абсорбере К-4 и байпасировании емкости Е-2.
Фракционирующий абсорбер К-4 состоит из двух зон - абсорбционной и отпарной. В абсорбционной зоне абсорбентом (бензином) из поступающего газа и поднимающихся снизу паров извлекаются углеводороды С3, С4 и частично С5, а в отпарной зоне, за счет подводимого тепла, газом из стекающей жидкости отпариваются легкие углеводороды С1-С2 и Н2S.
Регулирование температуры низа К-4 осуществляется за счет циркуляции части продукта низа К-4 через рибойлер Т-8. Теплоносителем в Т-8 является 1-ое промежуточное циркуляционное орошение колонны К-1, которое насосами Н-5, 5а прокачивается через Т-7, Т-8, Х-33 и возвращается на 5, 7 тарелку колонны К-1.
Кроме того, с целью использования увеличения времени абсорбции и улучшения отпаривания легких углеводородов технологической схемой предусмотрена возможность подачи части газа из Е-2 в линию верхнего перетока из рибойлера Т-8 в К-4.
В качестве орошения в верхнюю часть (30 тарелка) К-4 подается стабильный бензин от насосов Н-12, 12б. Прием бензина на насосы Н-12, 12б осуществляется из линии после холодильника Х-12.
Температурный режим верхней части К-4 регулируется подачей двух циркуляционных орошений насосами Н-16, 16а, 16б.
Нижнее циркуляционное орошение с 7 тарелки К-4 забирается насосами Н-16, 16а, прокачивается через холодильник Х-34 подается на 6 тарелку колонны К-4.
Верхнее циркуляционное орошение с 19 тарелки К-4 забирается насосами Н-16б,16а, прокачивается через холодильник Х-17 подается на 18 тарелку колонны К-4. Конденсат жирного газа из Е-2 насосами Н-15, 15а подается в среднюю абсорбционную часть колонны К-4 (на 4 тарелку). В емкости Е-2 также происходит отстаивание воды.
Газы с верха фракционирующего абсорбера К-4 направляются в повторный абсорбер К-5 для извлечения унесенных углеводородов фракции С3‑С5. В качестве абсорбента в К-5 используется легкий газойль из К-2, подаваемый насосом Н-7, 7а через Т-19, Т-20, Т-22, АВО-7, Х-34а, Х-15а.
Колонна К-5:
- давление верха - не более 11 кгс/см2;
- температура - не более 45 °С.
Насыщенный абсорбент из К-5, за счет разности давлений в К-5 и К-1, поступает на 21, 23 тарелки колонны К-1.
Существует возможность направления газового конденсата установки ГФХ и бензина с установки АГФУ в линию насыщенного абсорбента из колонны К-5 в колонну К-1 или в емкость Е-1. Сухой газ из абсорбера К-5 выводится с установки.
Внизу К-4 отстаивается вода. Нестабильный бензин из Т-8 поступает на прием насосов Н-2, 2а и через трубное пространство Т-11 подается на 14, 16 тарелки стабилизационной колонны К-6.
Колонна К-6:
- давление верха - не более 11 кгс/см2;
- температура верха - не более 80 °С;
- температура низа - не более 215 °С.
Схемой предусмотрена возможность подачи нестабильного бензина от Н-2, 2а в линию рефлюкса с установки.
С верха стабилизационной колонны К-6 выводятся пары углеводородов фракций С3-С4 (головка стабилизации, рефлюкс), конденсируются в аппарате воздушного захолаживания АВО-2 (возможно подключение АВО-1), Х-3 и направляются в рефлюксную емкость Е-3. Из Е-3 головка стабилизации забирается насосами Н-12, 12а, 12б, часть головки стабилизации (рефлюкс) подается на орошение в колонну К-6, избыток откачивается с установки. Предусмотрена линия сброса воды из Е-3 в Е-1.
Регулирование температуры низа стабилизационной колонны К-6 осуществляется за счет циркуляции части продукта низа К-6 через рибойлер Т-9. Теплоносителем является декантат, подаваемый насосами Н-4, 4а из колонны К-1.
Схемой предусмотрена возможность подачи теплоносителя в подогреватель Т-9 параллельно и последовательно.
Стабильный бензин из Т-9 поступает в межтрубное пространство теплообменника Т-11 и охлаждается в холодильниках 32а, 32б, Х-32, Х-12 и выводится с установки. Технологической схемой предусмотрена возможность аварийного сброса газа на факел с насосов Н-2-х, Н-12-х, Н-15-х, Н-16-х.
Факельная система
Аварийный сброс газов с предохранительных клапанов аппаратов блока ГФЧ и сбросы газов при остановке на ремонт осуществляется в закрытую факельную систему высокого давления ФВД. Углеводородный газ с коллектора ФВД проходит через емкость Е-33, где происходит сбор газового конденсата, и выводится с установки в заводской коллектор.
Технологической схемой предусмотрена возможность аварийного сброса газа на факел с насосов Н-33, Н-33б.
В случае пропуска одного или нескольких предохранительных клапанов на аппаратах К-4, К-6, Е-2, Е-3, Е-6, Е-6а, Е-40 и на линии нагнетания газовых компрессоров предусмотрено аварийное переключение на резервные предохранительные клапана.
Аварийный сброс газов с предохранительных клапанов Е-1 и сбросы газов при остановке установки из Е-1 осуществляются в закрытую факельную систему низкого давления ФНД через емкость Е-4.
Конденсат из емкости Е-4 насосами Н-33, 33б откачивается в емкость Е-1.
Углеводородный конденсат из каплеотбойника топливного газа Е-40 сбрасывается на факел ФВД.
Дренажная система
Для освобождения аппаратов от нефтепродуктов перед ремонтом на установке предусмотрена закрытая система дренирования светлых и темных нефтепродуктов.
Заглубленная емкость Е-10 предназначена для сбора темных нефтепродуктов. В Е-10 предусмотрено дренирование из следующего оборудования и трубопроводов:
- Т-5, Т-6, Т-7, Т-8, Т-9, Т-10, Х-14, Т-19, Т-20, Т-21, Т-22, Т-23 - трубное пространство;
- Х-4, Х-13, Т-5, Т-6, Т-7, Т-10, Х-14а, Т-20, Т-21, Х‑18, Т-22, Т-23, Х-33, Х-34, Х-34а - корпус;
- трубопровод промежуточного орошения из АВО-7 в К-1;
- приёмы, выкида и корпуса насосов Н-4, 4а, Н-5,5а, Н-6,6а, Н-7,7а, Н-10,10а, Н‑17,17а;
- корпуса насосов Н-1, 1а,1б, Н-14,14а;
- приёмы и выкида насосов Н-3,3а,3б;
Откачка нефтепродукта производится заглубленным насосом Н-34 в приёмные трубопроводы сырьевых резервуаров (в левый и правый поток) или в линию тяжелого газойля с установки.
Сбор светлых нефтепродуктов (бензина, газового конденсата) предусмотрен с оборудования и трубопроводов верхнего блока теплообменников в емкость Е-33, а именно с холодильников: Х-2, Х-3, Х-12, Х-16, Х-16а, Х-32, Х-32а, Х-32б; холодильников-конденсаторов: ХК-1, 1а, 1б, 1в; аппаратов воздушного захолаживания: АВО-1,2; АВО-3¸6, 8, 9.
Откачка бензина и газового конденсата из емкости Е-33 производится насосом Н-33 (Н-33б) в ёмкость Е-1.
Технологическая схема котла
Химочищенная вода (ХОВ) с установок химводоочистки поступает в трубное пространство парового подогревателя Т-27, где нагревается и направляется в верхнюю часть деаэрационных колонок Е-12а, Е-13а, а затем в бак-акуумулятор деаэраторов Е-12, Е-13. Технологической схемой предусмотрена подача пара собственной выработки в Т-27 для подогрева поступающей химочищенной воды. Возврат парового конденсата после Т-27 производится в деаэраторы Е-12, Е-13
Для удаления растворенного кислорода из ХОВ в нижнюю часть деаэрационных колонок подается водяной пар из линии пара после клапана PV-K23. Так же водяной пар подается в барботажное устройство деаэраторов. Барботажное устройство выполняет роль повторной деаэрации, способствующей удалению остатков кислорода.
С узла питания котла вода подается двумя параллельными потоками на смеситель и поверхностный пароохладитель. Оба потока в системе объединяются и далее питательная вода через узел охлаждения подвесок пароперегревателя подается в раздающий коллектор кипящего экономайзера, после чего пароводяная смесь поступает в барабан котла.
Насыщенный пар в барабане котла по 12-ти трубам поступает в пароохладитель, затем в пароперегреватель и камеру перегретого пара. Из камеры перегретого пара, пар отводится с установки в заводскую магистраль. Схемой предусмотрена возможность направления пара в линию пара на комплекс “Ароматика”.
Для горения топлива в П-3 подается воздух вентиляторами В-5, В-5а, а также избыток воздуха от нагнетателей В-2, 2а, 2б.
Топочное устройство котла выполнено в виде двух неэкранированных вертикальных циклонов с верхним выводом газов. Топливный газ в каждый циклон поступает через две газовые горелки из линии топливного газа, подогретого в Т-19.
Для горения топлива в П-3 подается воздух вентиляторами В-5, В-5а, а также избыток воздуха от нагнетателей В-2, 2а, 2б.
Регулирование необходимого солесодержания котловой воды и пара после котла производится непрерывной продувкой из соленого отсека барабана котла в расширитель Е-17.
Количество непрерывной продувки регулируется по солесодержанию в паре котла, согласно лабораторных анализов.
Для удаления шлама, окалины, солей из водяного объема котла, предусмотрена периодическая продувка с нижних точек циркуляционных контуров чистого и соленого отсеков, входных коллекторов экономайзера и коллектора подвесок пароперегревателя. Котловая вода вместе со шламом отводится в расширитель Е‑17, а затем дренируется в канализацию.
Газы сгорания из циклонов котла сбрасываются в дымовую трубу Д-2.
ПРИМЕЧАНИЕ: 1.Паровой котел установки работает по вышеописанной схеме, как энергетический, так как утилизация дымовых газов регенератора Р-2 невозможна в связи с повышенной запыленностью последних, что ведет к большой эррозии оборудования.
2. Возможна остановка котла на ремонт при работающей установке 43-103. В этом случае снабжение установки паром осуществляется из общезаводской магистрали.
Таблица 1.2 – Нормы технологического режима процесса каталитического крекинга
Наименование аппаратов и показатели режимов | Единицы измерения | Допустимые пределы |
Реактор Р-1 | ||
1.Расход сырья на установку | м3/ч | 130-240 |
2.Расход сырья в захватное устройство Р-1 | м3/ч | до 300 |
3.Расход сырья на сырьевые форсунки | м3/ч | до 300 |
4.Температура продукта на выходе из баллистического сепаратора | °С | 490-525 |
5.Давление верха Р-1 | кгс/см2 | не более 1,2 |
6.Расход водяного пара в десорбер | кг/ч | 2500-7000 |
7.Расход водяного пара на сырьевые форсунки | кг/ч | 1500-3500 |
8. Уровень слоя катализатора в десорбере | % | 30-80 |
9. Расход водяного пара на шламовые форсунки | кг/ч | 500-1500 |
10. Расход водяного пара в захватное устройство -при срабатывании блокировки по понижению расхода сырья ниже установленной нормы | кг/ч | 500-4000 до 32000 |
11. Расход шлама в Р-1 | м3/ч | до 35 |
12. Перепад давления на шиберной задвижке | кгс/см2 | 0,17-0,58 |
13. Массовая доля кокса на катализаторе | % | не более 1,2 |
Регенератор Р-2 | ||
14.Температура верха “кипящего” слоя | °С | не более 700 |
15.Давление верха | кгс/см2 | не более 1,0 |
16.Расход воздуха в регенератор | м3/ч при н.у. | 60000-125000 |
17.Уровень “кипящего” слоя | % | 70-95 |
18.Перепад давления между Р-1 и Р-2 | кгс/см2 | не более 0,40 |
19.Температура в сборной камере Р-2 | °С | до 700 |
20.Перепад давления на шиберной задвижке | кгс/см2 | 0,07-0,6 |
21.Массовая доля кокса на катализаторе на выходе из Р-2 | % | не более 0,2 |
22.Расход технического воздуха в захватное устройство закоксованного катализатора из Р-1 | м3/ч | до 9500 |
23.Расход технического воздуха в толкатель катализаторопровода из Р‑1 в Р-2 | м3/ч | до 2000 |
24.Расход технического воздуха на реакторный блок | м3/ч | не менее 4000 |
24.Давление технического воздуха | кгс/см2 | не менее 4,5 |
25.Расход технического воздуха на установку | м3/ч | не менее 3000 |
26.Расход технического воздуха в подъемный стояк катализаторопровода из Р-1 в Р‑2 | м3/ч | до 4000 |
Бункеры | ||
27. Давление в Б-1 | кгс/см2 | не более 0,5 |
28 Температура в Б-1 | °С | не более 550 |
29. Давление в Б-2 | кгс/см2 | не более 3,0 |
30. Давление в Б-3 | кгс/см2 | не более 3,0 |
Печь П-1 | ||
31. Температура сырья на входе | °С | не менее 120 |
32. Температура сырья на выходе | °С | не более 360 |
33. Температура на перевалах | °С | не более 810 |
34. Расход сырья по потокам | м3/ч | не менее 75 |
35. Давление топливного газа | кгс/см2 | не менее 2,0 |
36. Температура жидкого топлива | °С | 90-120 |
37. Температура топливного газа | °С | 80-130 |
38. Температура дымовых газов на выходе из печи | °С | не более 400 |
39. Содержание кислорода в дымовых газах на перевале | % | не более 8 |
40. Разрежение дымовых газов на перевале | кгс/м2 | 2-5 |
Топка под давлением П-2 | ||
41. Температура в камере смешения | °С | не более 550 |
42. Давление в камере сгорания | кгс/см2 | не более 1,7 |
Колонна К-1 | ||
43. Температура верха К-1 | °С | не более 130 |
44. Расход острого орошения от Н-8 (8а) | м3/ч | не менее 50 |
45. Температура паров на входе в К-1 | °С | не более 525 |
46. Температура низа отстойной части | °С | не более 350 |
47. Давление верха К-1 | кгс/см2 | не более 0,9 |
48. Давление низа К-1 | кгс/см2 | не более 1,0 |
49. Расход 2 ПЦО в К-1 (насосами Н-10,10а) | м3/ч | не более 150 |
50. Температура 2 ПЦО | °С | не более 140 |
51. Расход ВЦО в К-1 (насосами Н-11,11а) | м3/ч | не менее 100 |
52. Температура ВЦО | °С | не более 100 |
53. Расход 1 ПЦО в К-1 (насосами Н-5,5а) | м3/ч | 150-250 |
54. Температура 1 ПЦО | °С | не более 280 |
55. Расход НЦО от насосов Н-4 (4а) | м3/ч | не менее 480 |
56. Уровень в К-1 | % | не менее 20 |
Газосепаратор Е-1 | ||
57. Температура | °С | не более 35 |
58. Давление | кгс/см2 | не более 0,58 |
59. Уровень в Е-1 | % | не менее 20 |
Фракционирующий абсорбер К-4 | ||
60. Давление верха | кгс/см2 | не более 11,0 |
61. Температура верха | °С | не более 47 |
62. Температура низа | °С | не более 127 |
63. Расход орошения | м3/ч | 20-40 |
64. Расход верхнего циркуляционного орошения | м3/ч | не более 125 |
65. Температура верхнего циркуляционного орошения | °С | не более 45 |
66. Расход нижнего циркуляционного орошения | м3/ч | не более 125 |
67. Температура нижнего циркуляционного орошения | °С | не более 50 |
68. Уровень Т-8 | % | не менее 20 |
Емкость Е-2 | ||
69. Давление в Е-2 | кгс/см2 | не более 11,0 |
70.Температера в Е-2 | °С | не более 50 |
71. Уровень в Е-2 | % | 20-80 |
Колонна К-5 | ||
72. Давление | кгс/см2 | не более 11,0 |
73. Температура верха | °С | не более 45 |
74. Температура низа | °С | не более 45 |
Стабилизатор К-6 | ||
75.Температура верха К-6 | °С | не более 80 |
76. Температура низа | °С | не более 215 |
77. Давление верха | кгс/см2 | не более 11,0 |
78. Расход орошения | м3/ч | не менее 50 |
79. Уровень в Т-9 | % | не менее 20 |
Емкость Е-3 | ||
80.Давление | кгс/см2 | не более 11,0 |
81.Температура | °С | не более 35 |
82.Уровень | % | не менее 20 |
Колонна К-0 | ||
83.Уровень | % | не более 20 |
Колонна К-2,3 | ||
84. Расход пара в К-2 | м3/ч | не менее 300 |
85. Уровень | % | не менее 20 |
Емкость Е-40 | ||
86. Уровень | % | не более 60 |
Емкость Е-33 | ||
86. Уровень | % | не более 40 |
Емкость Е-10 | ||
88.Уровень | % | не более 80 |
Емкость Е-4 | ||
89.Уровень | % | не более 20 |
Емкость Е-101 | ||
90.Уровень | % | 20-80 |
Емкость Е-6,6а | ||
91.Уровень Е-6 | % | не более 40 |
92.Уровень Е-6а | % | не более 40 |
Температуры продуктов, уходящих с установки | ||
93.Головка стабилизации | °С | не более 40 |
94. Бензин | °С | не более 40 |
95. Легкий газойль | °С | не более 65 |
96. Тяжелый газойль | °С | не более 95 |
97. Сухой газ | °С | не более 40 |
Параметры энергоресурсов | ||
98.Температура оборотной воды на установку | °С | не более 25 |
99. Давление азота на установку | кгс/см2 | не менее 1,5 |
100. Давление обор. воды I системы на установку | кгс/см2 | не менее 2,5 |
101. Давление обор. воды II системы на установку | кгс/см2 | не менее 2,5 |
102. Давление воздуха КИП на установку | кгс/см2 | не менее 3,5 |
Котел-утилизатор | ||
103. Температура ХОВ на установку | °С | не более 30 |
104. Температура воды в Е‑12, Е-13 | °С | не более 104 |
105. Давление в Е-12,Е-13 | кгс/см2 | не более 0,2 |
106. Температура воды из Т‑27 | °С | 60-80 |
107. Давление в барабане котла П-3 | кгс/см2 | не более 24,0 |
108. Температура пара на выходе из котла П-3 | °С | 280-290 |
109. Давление пара на выходе из котла П-3 | кгс/см2 | не более 15,0 |
110. Температура внутри котла П-3 левого и правого циклона | °С | не более 1100 |
111. Давление пара на выходе из редуцирующего устройства | кгс/см2 | не более 5,0 |
112. Температура пара на установку | °С | 280-290 |
113. Давление водяного пара на установку | кгс/см2 | 10-15 |
114.Давление питательной воды от Н-22а, 26, 26а | кгс/см2 | не менее 28,0 |
115.Жесткость питательной воды | мкг-экв/кг | не более 5 |
116.Содержание кислорода в питательной воде | мкг/кг | не более 30,0 |
117. рН питательной воды | ед. рН | 7,5-9,5 |
Охрана труда
Технологический процесс установки 43-103 относится к пожаро, взрывоопасному производству, вследствие ведения процесса при высоких давлениях и температурах, наличия горючих взрывоопасных продуктов.
Установка имеет в своем составе блоки 1, 11 и 111 -ей категорий взрывоопасности.
Кроме того, опасность производства возрастает в связи с:
- образованием в процессе крекирования сырь легковоспламеняющихся
газов и жидкостей, сероводорода;
- использованием для привода насосно-компрессорного оборудования
электроэнергии высокого напряжения;
- возможностью нарушения герметичности аппаратов и трубопроводов из-за коррозии;
- способностью нефтепродуктов накапливать заряды статического
электричества.
Конструктивное оформление технологического процесса, его оснащение системами контроля и управления, наличие необходимых блокировок и сигнализации, обеспечение необходимой герметизации оборудования, исключение непосредственного контакта персонала с исходными материалами в процессе работы, глубокое знание и строгое соблюдение обслуживающим персоналом правил промышленной безопасности, пожарной, газовой безопасности и промсанитарии, гарантирует безопасность работающих и безаварийное ведение технологического процесса.
Дата добавления: 2016-01-03; просмотров: 111; Мы поможем в написании вашей работы! |
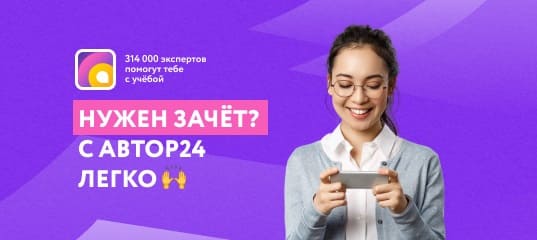
Мы поможем в написании ваших работ!