ТЕХНОЛОГИЯ ИЗГОТОВЛЕНИЯ СТАТОРОВ
Статор является наиболее ответственной деталью двигателя, во многом определяющей его характеристики и срок службы.
В процессе создания конструкции двигателя изучались возможности использования в качестве материала обкладки статора различных полимеров, однако резина оказалась практически единственным материалом, отвечающим как условиям эксплуатации, так и требованиям технологичности. Этому способствовал ряд важных свойств резины как конструкционного материала.
Впервые резина была использована как подшипниковый материал в качестве опор гребных валов и сразу зарекомендовала себя как эффективный антифрикционный материал, способный работать на водной смазке даже при наличии в ней абразивных частиц.
Впоследствии резинометаллические подшипники нашли широкое применение в конструкциях турбобуров [96].
Наряду с этим в нашей стране и за рубежом имелся большой опыт по использованию резины в качестве материала для обкладки статоров одновинтовых насосов [22, 133]. Эти соображения предопределили выбор резины как материала статора ВЗД, несмотря на его особые условия работы. Если в резинометалличе-ском подшипнике шейка вала находится в непрерывном контакте с резиновым вкладышем, т.е. имеет место чистое скольжение при относительно невысоких удельных нагрузках (1,5-2,0 МПа), то в статоре ВЗД происходит сочетание качения со скольжением с относительно невысокими скоростями (2-2,5 м/с) и большими удельными нагрузками (7-8 МПа).
|
|
Резиновая обкладка статора является элементом зубчатой пары, что предъявляет высокие требования к ее физико-механическим показателям. Кроме того, материал обкладки статора должен быть стойким к воздействию углеводородов и щелочей и иметь высокие литьевые свойства.
Конструктивно статор ВЗД представляет собой резинометал-лическую деталь, состоящую из стальной арматуры (остова) и привулканизированной к ней изнутри резиновой обкладки с внутренней винтовой поверхности.
В процессе работы обкладка статора воспринимает циклически изменяющиеся нагрузки, реактивный момент и радиальные силы, что предъявляет повышенные требования к прочности крепления резины к арматуре.
Технология изготовления статора должна обеспечить в заданных допусках диаметральные размеры винтового канала и его прямолинейность.
Трудности освоения технологии изготовления статора усугубились отсутствием в отечественной резинотехнической промышленности опыта изготовления подобных деталей и необходимого оборудования.
Способ изготовления статоров.Из всех известных способов изготовления подобных изделий был выбран способ литьевого формования в закрытой пресс-форме (рис. 11.4) [128].
|
|
Основной технической проблемой оказалась значительная длина резиновой обкладки (до 2-2,5 м) при сравнительно малой ее толщине, что потребовало значительных усилий при литье резины.
При заливке статора в литьевой камере пресса развивается давление до 200 МПа. Время заливки колеблется от 5 до 15 мин в зависимости от размера статора и технологических факторов (мощности литьевого пресса, конструкции пресс-формы, а также степени разогрева резиновой смеси и пресс-формы).
В первые годы использовали модернизированные гидравлические прессы для литья пластмасс с усилием не менее 4000. Последние разработки, внедренные в серийное производство, пре-
Рис. 11.4. Пресс-форма для заливки статора:
1- шайба опорная;2 - головка заливочная;3 - сердечник;4 - остов статора;5 -подогреватель
дусматривают оригинальную конструкцию пресса (рис. 11.5), позволяющую устанавливать пресс-форму вертикально и тем самым уменьшать гидравлические потери при литье резины, а также устранять факторы, вызывающие прогиб формующего стержня [125].
Рис. 11.5. Модернизированный пресс для заливки статора ВЗД
1-колонна;2 - ползун;3 - пресс-форма;4 - термопара;5 – литьевая камера ; 6 - стол подвижной;7 – траверса
|
|
Технологический процесс изготовления статора включает [128]: химическое обезжиривание арматуры, монтаж подвесок, электрохимическое обезжиривание, декапирование, латунирование, промывку и сушку, покрытие лейконатом, сушку и покрытие резиновым клеем, сборку пресс-формы, подогрев пресс-формы, заливки резиновой смеси, вулканизацию, разборку пресс-формы.
Разновидность технологического процесса: вместо латунирования и клея "лейконат" применяется пескоструйка поверхности и клей 51К-20.
В качестве материала обкладки статора в большинстве случаев применяется резина ИРП-1226, физико-механические показатели которой приведены ниже [80]:
Прочность при разрыве, МПа..................................................... 20
Удлинение, %:
относительное при разрыве...................................................... 300-350
остаточное............................................................................. 7
Сопротивление разрыву, Н/см................................................... 600
Показатель истирания, см3/(кВтч):
при нормальных условиях....................................................... 200
после старения в нефти (120 С
5 сут)................................... 450
после старения в воде (120 °С 5 сут)..................................... 360
|
|
Твердость по Шору, усл.ед......................................................... 70-80
Термостойкость, С, не более...................................................... 100
Зарубежные производители статоров ВЗД имеют более мощные литьевые машины (прессы), а также широкий выбор эластомеров, характеризующихся повышенной термостойкостью (150 °С) и сопротивляемостью различным буровым растворам.
Заводы компаний "Robbins & Myers", "Roper Pumps" (США) и PCM (Франция) выпускают монолитные статоры длиной до 5 м и наружным диаметром до 285 мм на специальных автоматизированных прессах.
Система контроля. Изготовленные статоры должны удовлетворять техническим требованиям ТУ 38.105.1419-86.
В процессе изготовления статора контролируется:
состояние расточки остова статора;
резиновая смесь (химический состав, твердость) и клей
Рис. 11.6. Схема контроля за диаметром De выступов статора с помощью
Гладкого калибра
внутренний диаметр De винтовой поверхности обкладки (с помощью набора цилиндрических калибров) (рис. 11.6);
прямолинейность канала статора (с помощью оптического прибора 4КРСМ или длинномерного цилиндрического калибра);
крепление обкладки к металлу (с помощью ультразвукового дефектоскопа типа ДУК-66 или УДМ-3). Датчиком прибора скользят по наружной поверхности статора вдоль его образующей в двух диаметрально противоположных плоскостях. При наличии отслоенной резины на экране осциллографа дефектоскопа появляется характерный всплеск. Если такой дефект не носит локального характера - статор отбраковывают.
Комплектация пар ротор - статор (выбор натяга) производится селективно в зависимости от условий эксплуатации и забойной температуры.
Дальнейшее совершенствование технологии изготовления ВЗД связано с повышением работоспособности РО и опорных узлов шпинделя. Потребуется разработка новых прогрессивных технологических процессов и инструментов, обеспечивающих изготовление многошаговых роторов с повышенной чистотой и износостойкостью винтовой поверхности. Применение новых эластичных материалов для обкладки статора и совершенствование технологического процесса его изготовления позволят расширить области применения ВЗД и повысить их технические показатели.
Глава 12
РАБОТОСПОСОБНОСТЬ ВЗД
Работоспособность ВЗД определяется техническим состоянием, при котором двигатель выполняет заданные функции в соответствии со своим назначением. Двигатель считается работоспособным, если его основные показатели находятся в пределах, предусматриваемых технической документацией. Работоспособное состояние двигателя нарушается вследствие отказов или катастрофического износа деталей.
Дата добавления: 2018-02-18; просмотров: 2723; Мы поможем в написании вашей работы! |
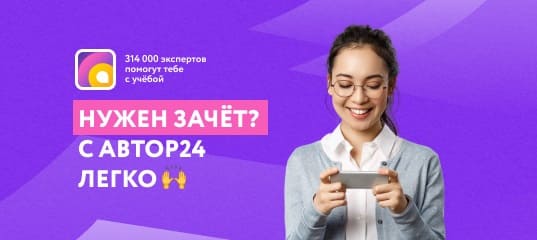
Мы поможем в написании ваших работ!