Исследование процесса закалки
И отпуска стали
6.1. Учебные цели:
1. Провести виртуальную термическую обработку
2. Исследовать влияние вида термической обработки на структуру и механические свойства углеродистой стали.
3. Сформировать практические умения по выбору режима и выполнению закалки и отпуска углеродистых сталей.
6.2. Учебные вопросы:
1. Выбор режима термической обработки стали.
2. Закалка и отпуск стали.
3. Специальные методы закалки (ступенчатая, изотермическая).
Учебно-справочные материалы по термообработке сталей
Выбор режима термической обработки сталей
Термической обработкой (термообработкой) называется совокупность операций нагрева, выдержки при высокой температуре и охлаждения сплавов. Цель термообработки – изменение свойств сплавов в нужном направлении. Изменение свойств при этом происходит только за счет изменения структуры сплавов.
Термическая обработка сталей связана с процессами их перекристаллизации в твердом состоянии, которые происходят при определенных температурах. Эти температуры называются критическими температурами или критическими точками сталей.
Согласно диаграмме Fe-Fe3C перекристаллизация углеродистых сталей происходит на линиях PSK, GS, и SE. В реальных условиях для превращения при нагревании температура должна быть несколько выше равновесной, а при охлаждении – ниже. Критические температуры при нагреве обозначают на линии PSK – Aс1, GS – Ас3, SE - Асm, при охлаждении – соответственно Ar1, Ar3, и Arm. Численные значения этих температур для каждой марки приводятся в справочной литературе.
|
|
В настоящей виртуальной работе изучаются два основных вида термообработки: закалка и отпуск стали.
Закалка – это вид термической обработки, при котором сталь нагревается на 30-50°С выше критической температуры, выдерживается при этой температуре, после чего быстро охлаждается (со скоростью выше критической). Цель закалки – максимально возможное повышение твердости и прочности стали. Однако при этом резко снижается ее пластичность и ударная вязкость.
Наиболее часто применяется обыкновенная закалка, при которой сталь охлаждается в специальных закалочных баках, заполненных каким-либо охладителем: водой, маслом, растворами солей и щелочей. Такая закалка называется закалкой в одном охладителе.
Основными параметрами режима обыкновенной закалки являются температура закалки, время выдержки и скорость охлаждения.
Температура закалки определяется по формулам:
· для доэвтектоидных сталей:
,
· для эвтектоидных и заэвтектоидных сталей:
При таких температурах доэвтектоидные и эвтектоидные стали приобретают структуру аустенита, а заэвтектоидные – аустенита + цементита вторичного.
|
|
Выдержка при температуре закалки необходима для завершения процесса образования аустенита и выравнивания его химического состава.
Разделить время выдержки при высокой температуре и время нагрева чрезвычайно трудно. Поэтому в качестве временного параметра при термообработке используют общее время пребывания в печи τ. Оно зависит, главным образом, от размеров и конфигурации деталей, типа нагревательных печей, расположения деталей в печах. Обычно зависимости для определения этого времени определяются опытным путем и представляются в справочной литературе. Для образцов, используемых в данной работе и условий их нагрева в лабораторных печах рекомендуются следующие нормы: 1 минута на 1 мм диаметра или толщины образца.
Например, при закалке образцов для определения ударной вязкости, толщина которых равна 10 мм:
, мин.
Скорость охлаждения Vохл при обыкновенной закалке должна быть равной или большей критической скорости закалки Vкр:
Vохл ≥ Vкр.
Для углеродистых сталей Vкр≈2000С/с. Такая скорость достигается охлаждением сталей в воде, которая обеспечивает охлаждение деталей со средней скоростью Vохл=2700С/с..
|
|
При скоростях охлаждения Vохл≥Vкр диффузионные процессы не происходят. В результате сталь приобретает особую структуру, которая получила название мартенсит.
Мартенсит (М) – пересыщенный твердый раствор углерода в α-железе. Концентрация углерода в мартенсите такая же, как в исходном аустените. Вследствие этого кристаллическая решетка мартенсита сильно искажается, и он приобретает высокую твердость, но практически нулевую пластичность. Твердость мартенсита HRC60-65, т.е. практически равна твердости цементита. Именно мартенситная структура обеспечивает высокую твердость закаленной стали.
В структуре заэтектоидной стали при температуре закалки присутствует аустенит и цементит вторичный. При резком охлаждении аустенит превращается в мартенсит, а цементит никаких превращений не претерпевает. Такая сталь в результате закалки приобретает структуру мартенсит + цементит вторичный. Обе эти структурные составляющие обладают высокой твердостью, что и обеспечивает высокую твердость закаленной заэвтектоидной стали.
Закалка заэвтектоидных сталей от температуры не применяется, так как при этом образуется грубоигольчатый мартенсит и в структуре стали сохраняется много остаточного аустенита. При этом твердость стали существенно снижается.
|
|
Все закаленные стали имеют неравновесную структуру. В них действуют высокие внутренние напряжения, которые сильно снижают работоспособность деталей и даже могут привести их к самопроизвольному разрушению. Поэтому, непосредственно после закалки такие детали подвергаются отпуску.
Отпуск – это вид термообработки закаленных сталей, при котором они нагреваются до температуры ниже критической Ac1, выдерживаются при этой температуре, и затем охлаждаются. Цель любого отпуска снижение неравновесности структуры и уменьшение внутренних напряжений, действующих в стали. Внешне это проявляется в снижении твердости, повышении пластичности и ударной вязкости стали.
Различают три вида отпуска: низкий, средний и высокий.
Низкий отпуск производится при температуре . При таком отпуске снижаются внутренние напряжения, повышается пластичность и ударная вязкость стали. Твердость ее при низком отпуске так же снижается, но незначительно. Сталь приобретает структуру отпущенного мартенсита, который по сравнению с мартенситом закалки имеет менее искаженную кристаллическую решетку.
Низкому отпуску подвергают детали подшипников качения, режущий и измерительный инструмент.
Средний отпуск производится при температуре . При таком отпуске мартенсит превращается в высокодисперсную феррито-цементитную смесь, зернистого строения, которая называется трооститом отпуска. Внутренние напряжения при среднем отпуске существенно снижаются. При этом твердость уменьшается до
, пластичность и ударная вязкость растут. Сталь приобретает высокие упругие свойства.
Среднему отпуску подвергают детали, основным требованием к эксплутационным свойствам которых является высокая упругость: пружины, рессоры, торсионы, мембраны, диски трения.
Высокий отпуск происходит при температуре . Выдержка при таких температурах приводит к образованию дисперсной феррито-цементитной смеси зернистого строения. Такая структура получила название сорбит отпуска. При высоком отпуске внутренние напряжения практически полностью снимаются, пластичность и ударная вязкость стали увеличиваются, а твердость уменьшается, но сохраняется достаточно высокой HRC25-30.
Совокупность закалки и высокого отпуска обеспечивает наилучшее сочетание прочности, твердости, пластичности и ударной вязкости стали и называется улучшением.
Улучшению подвергают детали, испытывающие при эксплуатации высокие знакопеременные и ударные нагрузки: валы, оси, шатуны, элементы зубчатых передач.
Процессы, протекающие в сталях при всех видах отпуска – диффузионные. Поэтому, полнота их протекания зависит от времени выдержки при высокой температуре. Опытным путем установлено, что это время должно составлять:
· при низком отпуске tотп ≈ 60 мин;
· при среднем отпуске tотп ≈ 40 мин;
· при высоком отпуске tотп ≈ 30 мин;
Скорость охлаждения при отпуске имеет второстепенное значение. Обычно охлаждение осуществляется на воздухе, иногда в масле или воде.
Специальные способы закалки
Недостатком обыкновенной закалки (в одном охладителе) является опасность коробления деталей и возникновения в них закалочных трещин. Эти дефекты возникают в результате действия в материале деталей высоких температурных напряжений, возникающих при быстром охлаждении. Особенно опасно быстрое охлаждение в интервале температур мартенситного превращения (280-130ºС). Чем сложнее форма деталей и чем выше в стали содержание углерода, тем больше опасность появления таких дефектов закалки. Поэтому для деталей сложной формы, изготавливаемых из высокоуглеродистых сталей часто применяют особые способы закалки, отличающиеся от обыкновенной условиями охлаждения. В качестве примера рассмотрим закалку образцов из стали марки 50 двумя методами: ступенчатым и изотермическим.
Температура нагрева и время выдержки при этих способах закалки принимается так же, как и при обыкновенной закалке, а режим охлаждения назначается с учетом диаграммы изотермического превращения аустенита (рис. 6.1). Диаграмма строится в координатах температура t, ºС, – время τ, сек.
Рис. 6.1. Диаграмма изотермического превращения
аустенита стали марки 50
Кривая 1 соответствует началу выделения феррита из аустенита, 2 – началу превращения аустенита, 3 – окончанию превращения аустенита. Левее кривой 2 находится область переохлажденного аустенита, правее кривой 3 – область продуктов изотермического превращения аустенита. Вид этих продуктов превращения зависит от температуры превращения: при t=650-550ºС – образуется перлит (П), 550-600ºС – сорбит (С), 450-550ºС – троостит (Т). Перлит, сорбит и троостит имеют одинаковое пластинчатое строение и отличаются степенью дисперсности (толщиной пластин). Именно поэтому их относят к перлитным структурам. Средняя толщина пластин в перлите небольшая 0,6-1,0 мкм, в сорбите – 0,3-0,5 мкм, в троостите – 0,1-0,20 мкм. Мартенситное превращение происходит в интервале температур Мн (~270ºС) – начало превращения и Мк (~150ºС) – конец превращения. Между областями трооститного и мартенситного превращений располагается промежуточная зона. В ней образуется своеобразная структура – бейнит. Бейнит представляет собой механическую смесь мартенсита с небольшой концентрацией углерода (~0,2%С) и частиц цементита.
Ступенчатая закалка. На рис. 6.1 этому способу закалки соответствует график охлаждения 1. В качестве охлаждающей среды первой ступени охлаждения в лабораторной работе используется расплав смеси солей (55% KNO3 и 45% NaNO2), температура которого поддерживается равной примерно 300ºС, т.е. выше Мн закаливаемой стали на 30-50ºС.
Нагретый до температуры закалки (~ 850ºС) образец быстро погружают в соляную ванну, где выдерживают в течение времени, необходимого для охлаждения стали до температуры расплава и выравнивания температуры по его объему. Время изотермической выдержки назначается так, чтобы в структуре образца не началось превращение переохлажденного аустенита. Для используемых образцов общее время нахождения в соляной ванне (охлаждение + изотермическая выдержка) τ=10с.
Дальнейшее охлаждение образца осуществляется на воздухе. При этом происходит превращение переохлажденного аустенита в мартенсит, т.е. собственно закалка. При медленном охлаждении на воздухе резко снижаются внутренние напряжения, а, следовательно, возможность коробления деталей и возникновения в них закалочных трещин.
Недостатком способа является ограничение размеров закаливаемых деталей. Из-за низкой скорости охлаждения в сравнительно горячей среде в центральных зонах крупных деталей скорость охлаждения может оказаться ниже критической. Для предупреждения этого явления максимальный диаметр деталей из углеродистых сталей, закаливаемых таким способом, составляет 10 мм.
Ступенчатой закалке обычно подвергают инструмент (метчики, напильники, надфили и т.д.) из сталей У10-У13.
Изотермическая закалка (линия 2 на рис. 6.1). Принципиальные особенности изотермической закалки сводятся к следующему.
1. Температура среды, в которой производится охлаждение и изотермическая выдержка выбирается в зависимости от структуры, которую должна иметь деталь. При данном способе закалки непосредственно из аустенита можно получить такие структуры, как сорбит, троостит и бейнит. Для этого назначают температуры изотермической выдержки: для получения сорбита ~600ºС, троостита ~500ºС, бейнита ~400ºС.
2. Время изотермической выдержки назначается так, чтобы завершилось превращение аустенита в конечную структуру, т.е. горизонтальный участок кривой охлаждения должен пересекать линии 1 и 2 диаграммы. Для режима, используемого в данной лабораторной работе согласно диаграмме изотермического превращения аустенита необходима изотермическая выдержка τ≥100с. Дальнейшее охлаждение деталей происходит на воздухе. При этом никаких структурных превращений в стали не происходит.
Как и ступенчатая, изотермическая закалка возможна только для деталей с размером поперечного сечения менее 10 и (для изделий из углеродистых сталей).
Наиболее часто такой закалке подвергают пружины.
Порядок выполнения работы:
1. Выбрать параметры режим обыкновенной закалки стали (в одном охладителе).
2. Выбрать параметры режимы отпуска закаленной стали (низкого, среднего и высокого).
3. Изобразить диаграмму изотермического превращения аустенита стали марки 50.
4. Выбрать параметры режима ступенчатой закалки стали марки 50. Проанализировать преимущества и недостатки данного вида закалки.
5. Выбрать параметры режима изотермической закалки стали марки 50. Проанализировать преимущества и недостатки данного способа закалки.
6. Произвести термообработку образцов по выбранным параметрам.
7. Определить механические свойства образцов после термообработки.
8. Построить зависимость механических свойств стали от температуры отпуска.
9. По результатам исследования сформулировать выводы, в которых отразить влияние температуры отпуска на твердость, пластичность и ударную вязкость стали, а также назвать виды термообработки, обеспечивающие наибольшую твердость, упругость, ударную вязкость и наилучшее сочетание механических свойств.
Контрольные вопросы:
1. Что такое термическая обработка? Перечислите основные виды термической обработки, их сущность и для чего их применяют. Как называются получаемые структуры и какими свойствами они обладают?
2. Как выбирают температуру закалки?
3. Что такое мартенсит и какими свойствами он обладает?
4. Что называется улучшением и в каких случаях его применяют?
5. При какой температуре производят отпуск закаленной стали, чтобы получить структуру троостит отпуска?
6. Изобразите график ступенчатой закалки с кривой изотермического превращения аустенита для эвтектоидной стали.
7. Изобразите график изотермической закалки на троостит для эвтектоидной стали?
8. Укажите термическую обработку для режущего инструмента, коленчатого вала, пружины, шарикоподшипника и назовите их структуры в рабочем состоянии.
9. В какой среде наиболее часто закаливают углеродистые стали?
10. Как влияет температура отпуска закаленной стали на ее механические свойства?
Литература для самостоятельной работы:
1. Солнцев Ю.П., Пряхин Е.И., Ф.Войткун Материаловедение. СПб, Химиздат, 2002 с.236-249, 258-275.
ЛАБОРАТОРНАЯ РАБОТА № 7
Дата добавления: 2018-02-15; просмотров: 905; Мы поможем в написании вашей работы! |
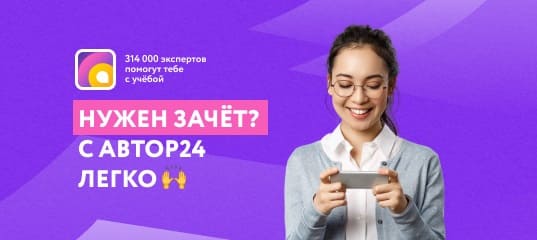
Мы поможем в написании ваших работ!