Исследование структуры и свойств легкоплавких припоев
Министерство образования и науки российской федерации
САНКТ-ПЕТЕРБУРГСКИЙ ГОСУДАРСТВЕННЫЙ
УНИВЕРСИТЕТ СЕРВИСА И ЭКОНОМИКИ
Кафедра «Техническая механика»
МАТЕРИАЛОВЕДЕНИЕ
ТЕХНОЛОГИЯ
КОНСТРУКЦИОННЫХ
МАТЕРИАЛОВ
Лабораторный практикум
для студентов направления 190600.62 «Эксплуатация
транспортно-технологических машин и комплексов»
Санкт-Петербург
2011
Одобрено на заседании кафедры «Техническая механика», протокол № 1 от 09.09. 2011 года.
Материаловедение. Технология конструкционных материалов. Лабораторный практикум для студентов направления 190600.62 «Эксплуатация транспортно-технологических машин и комплексов» – / сост. А.В. Васильева, Д.А. Иванов, С.В. Кириллов, Ю.А. Петренко. СПб.: Изд-во СПбГУСЭ, 2011. - 106с.
Лабораторный практикум содержит общие организационно-методические указания, описание лабораторных работ и предназначен для студентов высших учебных заведений, обучающихся по дисциплине «Материаловедение. Технология конструкционных материалов» по направлению 190600.62 – Эксплуатация транспортно-технологических машин и комплексов
Составители: канд. техн. наук, доцент А.В.Васильева
канд. техн. наук, доцент Д.А.Иванов
канд. техн. наук, доцент С.В. Кириллов
канд. техн. наук, доцент Ю.А. Петренко
Рецензент: канд. техн. наук, доцент В.С. Цепелев
© Санкт-Петербургский государственный университет
|
|
сервиса и экономики
2011 г.
ОБЩИЕ ОРГАНИЗАЦИОННО-МЕТОДИЧЕСКИЕ УКАЗАНИЯ
Главная цель лабораторных работ - практическое освоение студентами научно-теоретических положений раздела дисциплины «Материаловедение. Технология конструкционных материалов». Процесс их выполнения способствует овладению студентами техникой экспериментальных исследований, отработке навыков работы с виртуальными тренажерами, а также обобщения и анализа полученных результатов.
На занятиях лабораторные работы отрабатываются учебными подгруппами. В каждой подгруппе назначается старший, с которым преподаватель решает все организационные вопросы, касающиеся подготовки и проведения занятий.
На каждом из занятий студенты выполняют индивидуальные задания. Объём задания подобран так, чтобы за время занятия студент имел возможность полностью его выполнить, а также оформить отчет и защитить его. Отчет по работе выполняется в рабочей тетради по ходу выполнения задания.
Студенты, пропустившие занятие или не выполнившие задание, обязаны отработать его в консультационное время. Сроки отработки устанавливает преподаватель.
Защита отчета заключается в проверке преподавателем полноты и качества оформления отчета, а также в ответах обучаемых на поставленные преподавателем контрольные вопросы. При этом студент должен показать понимание цели и содержания работы, умение анализировать полученные данные. Результаты защиты оцениваются по пятибалльной системе с выставление оценок журнал учета успеваемости.
|
|
Общие требования мер безопасности
1. Лабораторные работы проводятся под руководством преподавателей и инструкторско-лаборантского состава после изучения ими устройства и правил эксплуатации действующих приборов и правил техники безопасности.
2. Студенты допускаются к работе на приборах после инструктажа по мерам безопасности и только в присутствии преподавателя или лаборанта, обеспечивающих правильность эксплуатации приборов и соблюдение правил техники безопасности.
3. Изучение устройства и правил использования лабораторных приборов производить только при отключенном электропитании.
ОГЛАВЛЕНИЕ
Стр.
Организационно-методические указания…………….................3 Общие требования мер безопасности...........................................4 Лабораторная работа №1. Определение твердости металлов методами вдавливания...................................................................6 Лабораторная работа №2. Испытание на растяжение. Исследование влияния углерода на механические свойства стали…….......................................................................................14 Лабораторная работа №3. Исследование структуры и свойств легкоплавких припоев ….............................................................21 Лабораторная работа №4. Исследование микроструктуры сплавов в отожженном состоянии……......................…………37 Лабораторная работа №5. Изучение технологических процессов сплавления компонент и термической обработки сплавов по диаграмме состояния железо-углерод....................43 Лабораторная работа №6. Исследование процесса закалки и отпуска стали.................................................................................51 Лабораторная работа №7. Легированные стали: термическая обработка, структуры и свойства................................................60 Лабораторная работа №8. Закалка и старение алюминиевых сплавов...........................................................................................69 Лабораторная работа №9. Свойства металлов и сплавов после холодной пластической деформации и последующего отжига............................................................................................78 Лабораторная работа № 10. Определение величины и вида деформации термопластов.............................................87 Лабораторная работа №11. Определение вида пластмасс экспресс методами.......................................................................94 |
|
|
|
|
ЛАБОРАТОРНАЯ РАБОТА № 1
Определение твердости металлов методами вдавливания.
1.1. Учебные цели:
1. Произвести испытание по определению твердости.
2. Исследовать зависимость твердости стали от содержания в ней углерода.
3. Научить студентов методам анализа полученных результатов.
1.2. Учебные вопросы:
1. Определение твердости методом Бринелля.
2. Определение твердости методом Роквелла
3. Исследование влияния углерода на твердость стали.
1.3.Учебно-справочные материалы определения твердости.
Под твердостью понимается сопротивление, оказываемое внедрению в материал другого, более твердого тела.
Твердость конструкционных и инструментальных материалов в большинстве случаев определяется методом вдавливания в них специальных наконечников (инденторов). Чем глубже наконечник проникает в материал, тем твердость этого материала меньше.
Наконечники изготавливаются из малодеформирующихся материалов (закаленная сталь, алмаз, твердые сплавы). Их форма и размеры стандартизированы. Стандартизированы также сила и время вдавливания.
Испытания на твердость получили широкое применение благодаря простоте, быстроте и портативности оборудования. Жестких требований к форме используемых образцов не предъявляется. Они изготавливаются так, чтобы их рабочая поверхность могла быть установлена перпендикулярно оси наконечника. Для выполнения этого условия часто используются различной формы приспособления, входящие в комплект твердомеров. В последние годы широкое применение нашли переносные твердомеры, с помощью которых можно определять твердость материалов непосредственно на крупногабаритных изделиях.
Наибольшее распространение для определения твердости материалов получили методы Бринелля и Роквелла.
Определение твердости методом Бринелля
Схема испытаний при определении твердости методом Бринелля приведена на рис. 1.1.
Рис. 1.1. Схема испытаний по методу Бринелля
Стальной шарик диаметром D, силой P вдавливается в образец в течение времени τ. В результате на образце образуется сферический отпечаток (лунка) диаметром d.
Характеристикой твердости является число твердости, которое определяется по формуле и обозначается НВ:
HB = P/F,
где F – площадь поверхности отпечатка (шарового сегмента).
Если поверхность отпечатка выразить через D и d, то:
, МПа (кгс/мм2).
Результаты измерений записываются: НВ2000МПа, НВ1500МПа и т.д. При использовании технической системы, единицы измерения не пишут: НВ200, НВ150и т.д.
Достоверность результатов определения твердости обеспечивается правильным выбором условий испытаний (табл. 1.1).
Таблица 1.1
Выбор нагрузки и диаметры шарика
Толщина испытуемого образца, мм | Диаметр шарика D,мм | Нагрузка, Р | ||
Чугун, сталь | Медь 10D2 | Алюминий 2,5D2 | ||
>6 | 10 | 3000 | 1000 | 250 |
от 3 до 6 | 5 | 750 | 250 | 62,5 |
3 | 2.5 | 187,5 | 62,5 | 15,6 |
Диаметры полученных отпечатков должны находиться в пределах . Кроме того, боковые стороны образца не должны заметно деформироваться. В противном случае испытание считается недействительным.
Испытания производятся на твердомерах типа ТШ (твердомер шариковый), которые часто называют прессами Бринелля. Схема твердомера приведена на рис. 1.2.
В верхней части станины 5 твердомера расположен шпиндель 1, в который вставляется наконечник (индентор) (2) с шариком. В нижней части станины находится винт со столиком 3, на котором устанавливается образец. При вращении маховика 4 по часовой стрелке винт перемещается вверх, поднимает столик 3 и прижимает образец к шарику 2. Грузами 7, расположенными на подвеске 8, создается необходимая нагрузка, вдавливающая шарик в образец. Величина нагрузки устанавливается подбором числа грузов. Приложение и снятие нагрузки производится автоматически с помощью электродвигателя 6, снабженного реле времени.
Рис. 1.2. Твердомер типа «ТШ»
Диаметр лунки измеряется с помощью специальной лупы, имеющей измерительную шкалу с ценой деления 0,05 мм. Измерения производятся в двух взаимно перпендикулярных направлениях. Твердость определяется по среднему значению d по вышеприведенной формуле или по таблице 2 приложения.
Достоинства метода:
1. Высокая точность.
2. Линейная зависимость между НВ и σв для пластичных материалов. Приблизительно σв =НВ/3.
Недостатки метода:
1. Ограниченный диапазон испытаний. Методом Бринелля можно испытывать материалы с НВ < 4500 МПа.
2. Невозможность испытаний тонких образцов (< 2 мм).
3. Значительный диаметр отпечатка, нарушающий поверхность детали и являющийся концентратором напряжений.
Определение твердости методом Роквелла
При определении твердости методом Роквелла в образец вдавливается либо стальной шарик диаметром 1/16 дюйма (1,59 мм), либо алмазный конус с углом при вершине120°. Иногда вместо алмаза конус изготавливают из твердых сплавов. Шарик используется при испытании относительно мягких материалов (НВ < 2300 МПа), конус – твердых (НВ > 2300 МПа).
Схема испытаний по методу Роквелла приведена на рис. 1.3. Вначале к наконечнику прикладывается предварительная нагрузка Р0 = 98,1Н (10кгс). Она необходима для устранения влияния неровностей поверхности образца. Затем к предварительной плавно добавляется основная нагрузка: Р1 = 882,9Н (90 кгс) при испытании шариком, и Р1 = 1373,4Н (140 кгс) при испытании конусом.
Рис. 1.3. Схема испытаний по методу Роквелла
Таким образом, шарик вдавливается общей нагрузкой Р = Р0 + Р1 = 981Н (100 кгс), конус – Р = Р0 + Р1 = 1471,5Н (150 кгс).
Твердость по Роквеллу обозначается буквами HRB при испытании шариком и HRC – при испытании конусом. В обоих случаях после букв ставятся цифры чисел твердости: HRB72, HRC60 и т.д.
Твердость по Роквеллу измеряется условными единицами, характеризующими глубину внедрения наконечника в материал образца. Число твердости определяется по формулам:
HRB = 130 - e и HRC = 100 – e.
Величина e определяется по формуле:
e = (h – h0)/0,002,
где h – глубина внедрения наконечника, измеренная после снятия основной нагрузки;
h0– глубина внедрения наконечника под воздействием предварительной нагрузки;
0,002 – глубина внедрения наконечника, принятая за единицу твердости.
Испытания проводятся на твердомерах типа «ТК» (твердомер конусный), которые часто называют приборами Роквелла (рис. 1.4).
Рис. 1.4. Твердомер типа «ТК»
Контроль правильности величины предварительной нагрузки и отсчет чисел твердости производится с помощью механического индикатора (рис. 1.5), фиксирующего глубину внедрения наконечника.
Рис. 1.5. Индикатор
Для контроля предварительной нагрузки на индикаторе предусмотрена малая стрелка. Вращением ходовой гайки (рис. 1.5) эту стрелку необходимо совместить с красной точкой на шкале индикатора.
Для отсчета результатов измерений на индикаторе предусмотрено две шкалы и большая стрелка. При использовании конуса число твердости считывается по наружной черной шкале (шкале С), шарика – по внутренней красной (шкале В). Соответственно схеме испытаний результаты считываются после снятия основной нагрузки.
Для правильного отсчета, после приложения предварительной нагрузки, необходимо вращением циферблата индикатора за ободок совместить нуль внешней (черной) шкалы с большой стрелкой индикатора.
Условия испытания по методу Роквелла (шкалы, наконечники и нагрузка) можно выбрать по данным табл. 1.2.
Таблица 1.2
Шкалы, наконечники и нагрузка
Шкала | Индентор | Полная нагрузка, кгс |
HRA | Алмазный конус | 60 |
HRC | Алмазный конус | 150 |
HRB | Стальной шарик | 100 |
Метод Роквелла позволяет испытывать и очень твердые материалы. Твердость таких материалов определяют с помощью алмазного конуса при общей нагрузке Р=588,6Н (60 кгс). Отсчет при этом также снимается по внешней (черной) шкале, но обозначают HRA. Сниженная нагрузка применяется для предупреждения выкрашивания материала конуса.
Достоинства метода:
1. Широкий диапазон измерений, охватывающих твердость практически всех материалов.
2. Возможность испытывать очень тонкие образцы, и даже поверхностные слои материала деталей.
3. Малые размеры отпечатка.
4. Оперативность измерений.
Недостатки метода:
1. Сравнительно невысокая точность.
2. Сложная зависимость твердости от прочности.
3. Отсутствие размерности.
Исследование влияния углерода на твердость стали
В процессе испытаний, определяется твердость образцов стали с различным содержанием углерода. Полученные данные вносятся в сводную таблицу испытаний. По этим данным строится зависимость твердости стали от содержания в ней углерода, и производится её анализ.
Порядок выполнения работы
1. Изобразить схему и определить условия испытания опытных образцов по методу Бринелля (рис. 1.1, табл. 1.1).
2. Произвести виртуальные испытания опытных образцов на твердомере «ТШ».
3. Внести результаты в сводную таблицу испытаний.
4. По результатам испытаний построить зависимость твердости стали от содержания в ней углерода.
5. Изобразить схему и определить условия испытаний по методу Роквелла (рис. 1.3, табл. 1.2).
6. Произвести испытания опытных образцов на твердомере «ТК».
7. Внести результаты в сводную таблицу испытаний.
8. По результатам испытаний построить зависимость твердости стали от содержания в ней углерода.
9. Сформулировать выводы по работе, в которых отразить влияние углерода на твердость стали, достоинства и недостатки методов Бринелля и Роквелла.
Контрольные вопросы
1. Что называется твердостью материала?
2. Как выбирается диаметр шарика и величина нагрузки при определении твердости по Бринеллю?
3. Приведите формулу для определения твердости по Бринеллю.
4. Укажите условия испытания на твердость по Роквеллу для двух шкал (наконечник и величину нагрузки).
5. В каких единицах измеряется твердость по Бринеллю и Роквеллу?
6. Укажите рациональные области применения испытаний по Бринеллю и Роквеллу.
7. С какой целью применяют предварительную нагрузку?
8. Как влияет содержание углерода в стали на её твёрдость?
9. Как обозначается твердость по Бринеллю и Роквеллу?
Литература для самостоятельной работы:
1. Солнцев Ю.П., Пряхин Е.И., Ф.Войткун Материаловедение. СПб, Химиздат, 2002 с.81-84.
ЛАБОРАТОРНАЯ РАБОТА № 2
Испытание на растяжение. Исследование
влияния углерода на механические свойства стали
2.1. Учебные цели:
1. Освоить методику определения основных характеристик механических свойств стали по экспериментальной диаграмме растяжения.
2. Научить студентов методам анализа полученных результатов.
2.2. Учебные вопросы:
1. Испытание образцов на разрывной машине.
2. Определение характеристик прочности и пластичности стали.
3. Исследование влияния углерода на механические свойства стали.
2.3. Учебно-справочные материалы испытаний на растяжение
Испытания образцов на разрывной машине
Статические испытания на растяжение являются распространенным методом определения механических свойств металлов. Они проводятся путём плавного растягивания образцов на стандартных разрывных машинах, конструкции которых обеспечивают определённые скорости деформации.
Форма и размеры образцов для испытаний регламентированы ГОСТ 1497-84. Они могут быть плоскими или цилиндрическими, нормальными и пропорциональными. В нормальных образцах регламентированы абсолютные размеры, в пропорциональных – соотношение размеров.
В данной работе используются наиболее употребительные цилиндрические пропорциональные образцы с (рис. 2.1). Такие образцы называют короткими или пятикратными. В ряде случаев испытываются и длинные или десятикратные образцы с
. Во всех случаях расчетная длина рабочей части образца выделяется точками или штрихами.
Рис. 2.1. Цилиндрический образец для испытаний на растяжение:
а – до испытания; б – после испытания
Испытания проводятся на разрывной машине УТС 110-50.01. (рис. 2.2). Принцип работы машины основан на принудительном деформировании образца при одновременном измерении нагрузки, прикладываемой к образцу, и соответствующей ей величины деформации образца. В машину входят:
- установка испытательная 1 с захватами 2 и 3 или опорными плитами в зависимости от выбранного вида испытания для установки испытуемого образца;
- пульт оператора 4, в котором расположены блок центрального процессора, клавиатура 6 для ввода информации в режиме диалога и управления машиной при испытании, а также жидкокристаллический графический дисплей 5 для отображения деформации.
При испытании на растяжение испытуемый образец устанавливается в захваты 2 и 3, подвижная траверса 11 получает вертикальное перемещение вверх от ходового винта. При этом образец нагружается, нагрузка передается на упругий элемент датчика силы 12. При разрушении образца нагрузка регистрируется на дисплее пульта оператора. После разрушения образца, подвижная траверса 11 автоматически или по команде оператора возвращается в исходное положение.
12 |
11 |

Рис. 2.2. Схема разрывной машины УТС 110-50.01
Определение характеристик прочности и пластичности углеродистой стали
На диаграмме растяжения образца стали с малым содержанием углерода (рис. 2.3) можно выделить несколько характерных участков.
Рис. 2.3. Диаграмма растяжения материалов:
а – с площадкой текучести; б – без площадки текучести
На участке 0-1 удлинение образца пропорционально растягивающей нагрузке. Это свидетельствует о том, что металл испытывает только упругую деформацию. По ординате точки 1 определяется Рпц.
При нагрузке Рт, соответствующей точке 2, на диаграмме наблюдается горизонтальный участок 2-3. На этом участке материал деформируется при постоянной нагрузке – «течёт». Горизонтальный участок диаграммы получил название площадки текучести.
При дальнейшем растяжении увеличение деформации сопровождается ростом растягивающей нагрузки, что свидетельствует о постепенном упрочнении материала.
Наибольшее упрочнение наблюдается в точке 4 (нагрузка Рmax ). Начиная с Рmax, в образце развивается местная пластическая деформация, которая приводит к образованию «шейки» – местного утонения наиболее слабого участка образца. После точки 4 растягивающая нагрузка постепенно уменьшается (участок 4-5), и в точке 5 образец разрывается.
Для материалов, на диаграмме растяжения которых площадка текучести отсутствует, вместо Рт определяется Р0,2 – нагрузка, после снятия, которой остаточная деформация составляет 0,2% от ℓ0.
Для определения Р0,2 вычисляют соответствующее остаточное удлинение Δℓпл=0,002ℓ0. Найденное значение откладывают по оси абсцисс вправо от начала координат, с учетом масштаба диаграммы. Из полученной точки Е проводят прямую, параллельную начальному участку диаграммы. Ордината точки пересечения этой прямой с кривой растяжения определяет искомую нагрузку Р0,2.
В данной работе определяются три характеристики прочности: предел пропорциональности –σпц, предел текучести –σт или условный предел текучести –σ0,2 и временное сопротивление (предел прочности) –σв.
Предел пропорциональности σпц – наибольшее напряжение, до которого сохраняется пропорциональная зависимость между нагрузкой и деформацией (удлинением):
σпц = Рпц/F0, МПа (кгс/мм2).
Предел текучести σт – напряжение, при котором происходит рост деформации без заметного увеличения растягивающей нагрузки:
σт = Рт/F0, МПа (кгс/мм2).
У большинства материалов площадка текучести отсутствует (см. рис. 2.3, б). В таких случаях вместо σт определяется условный предел текучести σ0,2 – напряжение, при котором остаточная деформация составляет 0,2% от начальной длины образца ℓ0:
σ0,2 = Р0,2/F0, МПа (кгс/мм2).
Временное сопротивление σв – напряжение, соответствующее максимальной растягивающей нагрузке:
σв = Рmax/F0, МПа (кгс/мм2).
Характеристиками пластичности материалов являются относительное удлинение и относительное сужение.
Относительное удлинение δ определяется по формуле:
δ = 100(ℓк - ℓ0)/ℓ0 = 100Δℓпл/ℓ0, %
где ℓк – длина расчетной части образца после разрыва, мм;
Δℓпл – абсолютное удлинение (пластическая деформация) рабочей части образца за время испытаний, мм.
Величина ℓк может быть измерена непосредственно на образце, если сложить его части. Величину Δℓпл = ℓк - ℓ0 можно определить по диаграмме растяжения как расстояние от начала координат до точки пересечения с осью абсцисс прямой, проведенной через точку разрыва образца параллельно участку пропорциональности (рис. 2.3, а).
Относительное сужение ψ определяется по формуле:
Ψ = 100 (F0 – Fк)/F0, %;
где F0– площадь поперечного сечения образца до испытаний;
Fк – площадь поперечного сечения шейки образца в месте разрыва.
Исследование влияния углерода на механические свойства стали
В процессе испытаний производится определение характеристик механических свойств стали с различным содержанием углерода. Полученные характеристики вносятся в сводную таблицу испытаний, по которым строятся зависимости механических свойств стали от содержания в ней углерода и проводится анализ.
Порядок выполнения работы
1. Измерить расчетную длину ℓ0 и диаметр рабочей части d0 образца. Величина ℓ0 измеряется штангенциркулем с точностью 0,1 мм. Диаметр d0 измеряется микрометром с точностью 0,01 мм в трёх сечениях (в середине и по краям рабочей части). По наименьшему значению d0 рассчитать площадь поперечного сечения рабочей части образца F0 =πd02/4.
2. Произвести испытание образцов в порядке, указанном преподавателем.
3. Измерить диаметр рабочей части образца в месте разрыва dк и вычислить площадь F0 =πdк2/4. Измерение dк производить штангенциркулем с точностью до 0,1 мм.
4. По диаграмме растяжения определить нагрузки Рпц, Рт(Р0,2) и Рmax, а также остаточную деформацию Δℓпл.
5. Рассчитать характеристики прочности σпц, σт(σ0,2), σв, и пластичности δ и ψ материала образцов.
6. Сравнением рассчитанных характеристик прочности и пластичности с аналогичными характеристиками, приведенными в ГОСТ 1050-88, 14959-79 и 1435-74 (таблица 1 приложения) определить марку испытанной стали и содержание в ней углерода. Привести примеры применения данной стали.
7. Внести полученные сведения в сводную таблицу испытаний.
8. По данным сводной таблицы испытаний построить графики зависимостей характеристик прочности и пластичности стали от содержания в ней углерода.
9. Сформулировать выводы по работе, в которых отразить влияние содержания углерода на механические свойства стали.
Контрольные вопросы
1. Какие образцы применяются при испытаниях на растяжение?
2. Изобразите схему диаграммы растяжения для низкоуглеродистой и среднеуглеродистой стали.
3. Укажите на диаграмме растяжения точку начала образования на образце шейки.
4. Укажите на диаграмме точки, по которым определяются характеристики прочности.
5. Приведите формулы для определения характеристик прочности и пластичности.
6. Дайте определение предела пропорциональности, предела текучести, условного предела текучести, временного сопротивления.
7. Как обозначаются и в каких единицах измеряются характеристики прочности и пластичности?
8. Как по диаграмме растяжения определить величину пластической деформации образца?
9. Как влияет содержание углерода на характеристики прочности стали?
10. Как влияет содержание углерода на характеристики пластичности стали?
Литература для самостоятельной работы:
1. Солнцев Ю.П., Пряхин Е.И., Ф.Войткун Материаловедение. СПб, Химиздат, 2002 с.80-81
ЛАБОРАТОРНАЯ РАБОТА № 3
Исследование структуры и свойств легкоплавких припоев
3.1. Учебные цели:
1. Ознакомиться с методикой проведения термического анализа сплавов и экспериментального построения диаграмм состояния.
2. Определить значения критических температур для сплавов
3. Построить приближенную диаграмму состояния для свинцово-сурьмянистых и медно-никелевых сплавов.
4. Изучить правило фаз и отрезков.
5. Изучить структурный состав припоев по диаграмме Pb-Sn.
3.2. Учебные вопросы:
1. Диаграмма состояния с эвтектикой и с неограниченным твердым раствором.
2. Основные линии и области диаграммы.
3. Значение диаграммы состояния для решения практических задач.
Дата добавления: 2018-02-15; просмотров: 890; Мы поможем в написании вашей работы! |
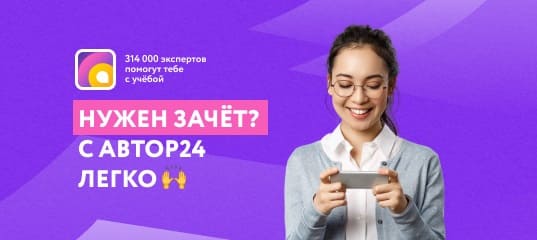
Мы поможем в написании ваших работ!