Производство воздушной извести
Воздушной или строительной известью называется бессиликатный вяжущий материал на основе оксида и гидроксида кальция. Различают три вида воздушной извести: кипелка (негашеная известь) – оксид кальция СаО, пушонка (гашеная известь) – гидроксид кальция Са(ОН)2, известковое тесто, получаемое гашением пушонки избытком воды, состава Са(ОН)2·nН2О.
Помимо строительства кипелка и пушонка используются в производстве хлорной извести, для умягчения воды и очистки продукции в сахарном производстве.
Схватывание и затвердевание известкового теста (раствора) состоит из двух одновременно протекающих процессов: испарения воды и кристаллизации гидроксида кальция с образованием сростков кристаллов, и карбонизации гидроксида кальция до карбоната кальция:
Са(ОН)2 + СО2 = СаСО3 + Н2О.
Скорость реакции карбонизации возрастает при повышении концентрации оксида углерода(IV) в воздухе, что используется на практике для ускорения процесса схватывания известкового раствора. Схватывание в обычных условиях протекает весьма медленно, так как образующийся на поверхности слой карбоната кальция препятствует диффузии воздуха.
Сырьем для производства воздушной извести служат кальциево-магниевые карбонатные породы: мел, известняк, доломит. Технологический процесс производства извести состоит из операций обжига сырья, гашения продукта обжига (кипелки) и утилизации выделяющегося при обжиге оксида углерода(IV).
|
|
Обжиг карбонатного сырья представляет обратимый гетерогенный эндотермический процесс термической диссоциации карбоната кальция, описываемый уравнением:
СаСО3 ↔ СаО +СО2 + ΔН, ΔH = 177.9 кДж.
На практике, для ускорения процесса, обжиг ведут при температуре около 1200 оС.
Для обжига карбонатного сырья используют печи различной конструкции: шахтные, в которых сырье смешивается с твердым топливом (кокс), вращающиеся трубчатые, циклонно-вихревые и кипящего слоя, обогреваемые сжиганием газообразного топлива. Производительность печей различна. Максимальной производительностью обладают трубчатые (1000 т/сутки) и шахтные (600 т/сутки).
Гашение кипелки (оксида кальция) представляет гетерогенный экзотермический процесс, протекающий по уравнению:
СаО + nН2О = Са(ОН)2 (n - 1)Н2O.
В зависимости от соотношения оксида кальция и воды могут быть получены два продукта гашения: при n - 1 – гидроксид кальция (пушонка), при п > 1 - известковое тесто.
Тепловой эффект реакции гашения до пушонки составляет 53.2 кДж. Для гашения извести используются в этом случае известегасильные агрегаты-гидрататоры барабанного типа периодического и непрерывного действия.
|
|
Утилизация оксида углерода(IV) в производстве воздушной извести экономически целесообразна потому, что газ обжиговых печей содержит до 30 % оксида углерода, что при значительном объеме производства воздушной извести позволяет получить значительное количество ценного побочного продукта. Для этой цели обжиговый газ после очистки обрабатывают раствором карбоната калия, поглощающим оксид углерода:
СО2 + К2СОЗ + Н2О = 2 КНСО3
Образовавшийся гидрокарбонат калия разлагают нагреванием до 80 оС:
2 КНСО3 = К2СОЗ + СО2 + Н2О.
Выделившийся оксид углерода(IV) сушат и используют в газообразном, жидком или твердом состоянии, а регенерированный раствор карбоната калия вновь направляют на хемосорбцию оксида углерода.
Производство стекла
Стеклами называются переохлажденные расплавы смесей оксидов и бескислородных соединений с высокой вязкостью, обладающие после охлаждения механическими свойствами твердого тела.
В структуре стекла существуют аморфная и кристаллическая фазы, находящиеся в состоянии неустойчивого равновесия. Вследствие весьма высокой вязкости стеклянного расплава скорость кристаллизации его мала и равновесие почти полностью сдвинуто в сторону аморфной фазы, то есть стекло имеет преимущественно аморфную структуру. Поэтому стеклам присущи специфические свойства, характерные для аморфных тел: отсутствие четкой температуры плавления и переход из твердого состояния в жидкое в некотором интервале температур, который характеризуется температурой размягчения, а также изотропность оптических свойств.
|
|
Состав силикатных стекол может быть выражен общей формулой:
nR2О · mRO · рR2О3 · qRО2,
где: n, m, р, q – переменные величины; R2О – оксиды щелочных металлов (Na2О, К2О, Li2O); RO – оксиды щелочноземельных и других двухвалентных металлов (СаО, ВаО, MgO, РbО, ZnO, SrО, FeO); R2O3 – кислотные оксиды (Аl2О3, В2О3, Fе2O3); RO2 – оксид кремния SiO2, составляющий до 75 % массы.
Всем стеклам присущи некоторые общие свойства: прозрачность, низкая теплопроводность, диэлектрические свойства, высокая химическая стойкость к кислотным реагентам. Cвойства стекол зависят от их состава, от соотношения основных и кислотных оксидов.
Оксиды щелочных металлов снижают вязкость, температуру размягчения, механическую прочность и твердость стекол. Оксиды щелочноземельных металлов позволяют регулировать вязкость стеклянных расплавов в заданных пределах. Кислотные оксиды повышают механическую прочность, термическую и химическую стойкость стекол.
|
|
По назначению стекла делятся на строительное, тарное, бытовое, художественное (хрусталь, цветное стекло), химическое, оптическое и специального назначения. Простейшее силикатное стекло имеет состав, описываемый формулой: Na2О·СаО·6SiO2. В табл. 11.2 приведен состав некоторых сортов стекол.
Таблица 11.2
Состав стекол
Тип стекла | Содержание оксидов, % масс. | ||||||
SiO2 | Аl2О3 | СаО | MgO | Na2О | К2О | РbО | |
Строительное | 70-73 | 1.5-2 | 8-10 | 3-4 | 14-15 | - | - |
Тарное | 69-72 | 3-4 | 9-10 | 2-4 | 15-16 | - | - |
Химическое | 68-70 | 3-5 | 6-8 | 1-2 | 8-10 | 5-6 | - |
Оптическое | 47-65 | - | - | - | - | 6 | 45 |
Хрусталь | 55-77 | - | - | - | - | 10-13 | 30-35 |
Пирекс | 81 | 2 | 0.5 | - | 4.5 | - | - |
Сырьем для производства стекол служат разнообразные природные и синтетические материалы. По их роли образовании стекла они делятся на пять групп:
Стеклообразователи, создающие основу стекла: оксиды кремния и свинца(II), карбонаты натрия, калия и кальция, сульфаты натрия и бария, борная кислота, бура, оксид алюминия.
Красители, придающие стеклу необходимый цвет: оксиды и соли металлов, образующие в стекле коллоидные растворы: меди(I), железа(II), кобальта(II), хрома(III), хлорида золота; сульфата меди(II) и др.
Глушители, делающие стекло матовым и молочным: оксиды мышьяка(III), олова(IV), сульфид олова(II) и др.
Обесцвечиватели, устраняющие желтую и зеленоватую окраску стекла: оксид марганца (IV) и др.
Осветлители, удаляющие из стекломассы газовые включения: нитрат натрия, хлорид аммония, оксид мышьяка(III) и др.
В химическое стекло и в стекло пирекс входит также оксид бора(III).
Процесс производства стеклянных изделий показан на рис. 11.5.
Рис. 11.5. Принципиальная схема производства стеклянных изделий
В подготовку компонентов сырья входят операции промывки, сушки, измельчения, классификации и брикетирования веществ. Подготовленные таким образом материалы смешивают в нужных пропорциях для образования однородной смеси – шихты, поступающей на стадию высокотемпературной обработки – варку стекломассы. Все материалы, используемые в стекловарении, должны быть чистыми, однородными по химическому составу и не превышать допустимого предела влажности.
Варка стекломассы – это совокупность сложных физико-химических процессов, протекающих в гетерогенной системе через стадии собственно варки, осветления (гомогенизации) массы и ее охлаждения. Эти процессы начинаются в твердой фазе до расплавления шихты и продолжаются в расплаве. Скорость процесса варки в значительной степени зависит от скорости диффузии компонентов как в твердой, так и в жидкой фазах. В твердой фазе протекают реакции образования силикатов, в жидкой при температуре 1200-1240 оС – процессы стеклообразования, В табл. 11.3 представлена последовательность процессов, протекающих при варке стекломассы с изменением температуры.
Таблица 11.2
Процессы при варке стекломассы
Температура, оС | Процессы, протекающие в шихте |
до 300 | Удаление влаги и органических веществ |
до 400 | Образование двойных солей из карбонатов: СаСО3 + Na2CO3 ↔ CaNa2(CO3)2, MgCO3 + NaCO3 ↔ MgNa2(CO3)2 |
340-900 | Силикатообразование: MgNa2(CO3)2 + 2SiO2 = MgSiO3 + Na2SiO3 + 2CO2 MgCO3 + SiO2 = MgSiO3 + CO2 CaNa2(CO3)2 + 2SiO2 = CaSiO3 + Na2SiO3 + 2CO2 |
780-880 | Появление жидкой фазы за счет образования эвтектик различного состава: Na2SiO3· SiO2, MgSiO3· SiO2, CaNa2(CO3)2· Na2(CO3), MgNa2(CO3)2· Na2(CO3) |
980-1150 | Образование жидкой стекломассы за счёт растворения в расплаве образующихся силикатов магния и кальция: MgO + SiO2 = MgSiO3, CaO + SiO2 = CaSiO3 |
1200-1240 | Стеклообразование |
1400-1500 | Гомогенизация и осветление, удаление газов |
1200 | Охлаждение (стужка) стекломассы до приобретения ею нужной вязкости |
Для варки стекломассы используют стекловаренные печи различной конструкции. Максимальной производительностью обладают ванные печи пламенного типа непрерывного действия. В них шихта разогревается факелами пламени сгорающего в печи газа, направленными перпендикулярно движению шихты.
Теплосодержание газов, выходящих из печи, утилизируется в регенераторах и используется для подогрева воздуха и сгорающего газа. Производительность подобных печей составляет 300 т/сутки. Помимо печей пламенного типа, для варки стекломассы применяют электрические печи сопротивления и печи с комбинированным газоэлектрическим нагревом шихты.
Методы формования стеклянных изделий из стекломассы весьма разнообразны и зависят от их вида и назначения. В каждом методе выбирают определенные температурные и временные условия, обеспечивающие оптимальное значение вязкости стекломассы, которая зависит от температуры и возрастает по мере охлаждения расплава. В зависимости от состава стекломассы формование изделий производят в интервале температур 800-1100 оС.
Важнейшими методами формования изделий являются следующие:
- вытягивание на автоматических машинах лодочного и безлодочного типа со скоростью от 80 до 110 м/час (листовое стекло, трубы);
- выдувание и прессвыдувание на прессвыдувочных машинах (тарная и химическая посуда, колбы электроламп);
- прессование на автоматических прессах (линзы, стеклянные блоки, бытовые изделия);
- отливка в формы (архитектурно-строительные детали, художественные изделия);
- прокат с одновременным отжигом для снятия напряжений и шлифовкой (толстое листовое стекло).
Из специальных видов стеклянных изделий широкое применение нашли следующие:
- закаленное (небьющееся) стекло, получаемое термической обработкой в печах обычного стекла с последующим охлаждением его обдувкой воздухом;
- пеностекло (пористое стекло), получаемое сплавлением стеклянного порошка с порообразователями (MnО2, СаСО3, кокс) при 800 оС и используемое в качестве конструкционного тепло- и звукоизоляционного материала;
- стеклянное волокно (текстильное и теплоизоляционное), получаемое продавливанием стекломассы через фильтры или методом дутья путем расчленения струек стекломассы паром на отдельные волокна.
Стеклянное волокно применяется для изготовления тканей (фильтры, электроизоляция) и теплоизоляции (вата, войлок).
Производство ситаллов
Ситаллами (силикат + кристалл) называются материалы из полностью или частично равномерно закристаллизованного стекла или шлака (шлакоситаллы). Термин предложен И.И. Китайгородским и происходит от сочетания слов «стекло (силикат») и «кристалл». Ситаллы относятся к новым материалам и применяются в промышленных масштабах с начала 60-х годов ХХ столетия.
Ситаллы имеют мелкокристаллическую структуру с размерами кристаллов менее 1 мкм. Содержание кристаллической фазы в них достигает 96 %, а аморфной фазы не более 50 %.
Состав ситаллов весьма разнообразен: наиболее распространены литиевые ситаллы Li2О – Аl2O3 – SiО2, отличающиеся высокой термостойкостью и малым коэффициентом термического расширения; магниевые ситаллы MgO – Аl2O3 – SiО2, обладающие, помимо этих свойств, оптической и радиопрозрачностью, кальциевые, цинковые, кадмиевые и марганцевые ситаллы состава: Ме – Аl2O3- SiО2, где Ме = Са, Zn, Cd, Мn, характеризующиеся высокой диэлектрической постоянной, термостойкостью и прозрачностью для видимого и инфракрасного излучения.
Для всех ситаллов характерны высокая (до 1450 oС) температура плавления, малая пористость и газонепроницаемость, химическая и термическая стойкость, высокая твердость и механическая прочность, по которой некоторые образцы («пирокам») в девять раз превосходят стекла, малый коэффициент термического расширения, износоустойчивость.
Ситаллы и шлакоситаллы применяют для изготовления строительных деталей (плитки, ступени, подоконники), труб, подшипников, работающих без смазки до 500 оС, поршней и цилиндров двигателей внутреннего сгорания, режущих элементов буров, обкладки шаровых мельниц, обтекателей ракет. Получают их теми же методами, что и стекло. Ситаллы (шлакоситаллы) получают регулируемой принудительной кристаллизацией стекла или шлакомассы путем внесения в расплав катализаторов кристаллизации. Катализаторы создают во всем объеме стекломассы центры кристаллизации и вызывают интенсивный и равномерный рост кристаллов в аморфной стекломассе. В качестве катализаторов кристаллизации используются металлы в коллоидном состоянии (золото, медь, серебро, платина), фториды и фосфаты некоторых металлов, оксид титана(IV).
Технологический процесс получения ситаллов (шлакоситаллов) из стекла или шлака складывается из пяти последовательных операций.
Дата добавления: 2018-02-18; просмотров: 1796; Мы поможем в написании вашей работы! |
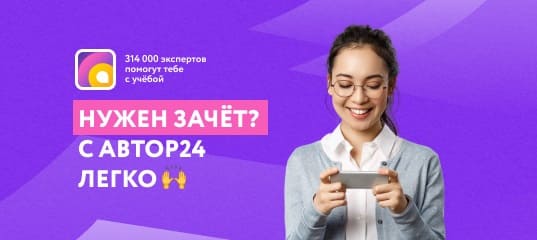
Мы поможем в написании ваших работ!