Проектирование технологических процессов.
Цель разработки технологического процесса – дать подробное описание процессов изготовления деталей с необходимыми технико-экономическими расчетами и обоснованиями принятого варианта из возможных. В результате составления технологической документации инженерно-технологический персонал и рабочие получают необходимые данные и инструкции для реализации разработанного процесса. Технологический процесс включает в себя выбор средств технологического оснащения: режущий и контрольный инструмент, трудоемкость и себестоимость изготовления изделия.
Единичный тех. процесс разрабатывают для единичных изделий, характеризующихся общностью конструктивных и технологических признаков (с одной или несколькими деталями, кот-е ранее не изготавливались на пред-ии).
Унифицированный тех. процесс – создается для группы изделий, кот-е х-зуются общими конструктивными и технологическими признаками. (делится на типовой и групповой)
Припуски на механическую обработку. Состав припуска.
Общим припуском на обработку называется слой мат-ла, удаляемый с пов-ти исходной заготовки в процессе механической обработки с целью получения готовой детали.
Припуск на механическую обработку – слой мат-ла, удаляемый на конкретной операции.
В состав припуска входят:
1) шероховатость на предшествующей операции Rz
2) погрешность установки ξ
3) пространственные отклонения ρ
|
|
4) глубина дефектного слоя Т
расчетные формулы: 2zi min=2(Rzi-1+Ti-1+√ρ2i-1+ε2i) - минимальный припуск
ρd =√ρ2кор+ρ2см
ρкор =∆k*D; ρсм =δв - суммарное значение пространственных отклонений; εу=√ε2б+ε2з - общая погрешность установки
Общий припуск на поверхность
Общий припуск, который удаляют в процессе механической обработки рассматриваемой поверхности, определяется разностью размеров исходной заготовки и детали
Z0=Lз-Lд – для наружных поверхностей
Z0=Lд-Lз – для внутренних поверхностей
n
Z0=∑zi
i=1
zi – припуск на соответствующий переход
n –число технологических переходов
На величину припуска оказывают влияние различные факторы, главнейшими из которых являются:
1) вид заготовки (отливка, штамповка, поковка, прокат);
2) материал заготовки;
3) технологический процесс обработки;
4) сложность конфигурации детали;
5) требуемые точность и чистота обрабатываемых поверхностей и др
Основные методы обработки внутренних цилиндрических поверхностей
Внутренние ц. поверхности (отверстия, канавки) могут быть сквозными, гладкими, глухими
1.Токарная обработка: токарно-винторезные станки, токарно-револьверные, токарные автоматы
|
|
Инструмент: сверла, зенкеры, развертки, расточные резцы
Приспособления: трехкулачковый патрон, трехкулачковый патрон с пневматическим приводом, цанговые патроны
Центры: вращающиеся
2.Шлифовальная обработка: внутришлифовальные станки, хонинговальные станки
Инструмент: абразивные круги, бруски, устанавливающиеся в хонинговальную головку
Поверхностно-пластическая деформация: токарные станки
Инструмент: раскатка
3.Дорование – обработка отверстий: протяжные станки. Предназначена для создания сжимаемых напряжений в отверстии заготовки и повышения класса шероховатости. Циклические отверстия можно осуществить протягиванием
Оборудование: протяжной станок
Инструмент: протяжка
Протягивание: комбинированное, генеративное (профильное)
Основные методы обработки наружных цилиндрических поверхностей
1. Токарная обработка: токарно-винторезные, токарно-револьверные, токарные автоматы
Инструмент: проходные резцы, канавочные, фасонные резцы
Приспособления: трехкулачковый патрон, центры (вращающиеся, неподвижные, рифленые)
2. шлифовальная обработка: круглошлифовальные станки
Инструмент: центры (вращающиеся, неподвижные), люнеты (подвижные, неподвижные)
|
|
3. Отделочная обработка: хонингование(обработка поверхности абразивными брусками), доводка (обеспечивает малые отклонения размеров и формы), суперфиниширование-отделочная обработка абразивными брусками, полирование-уменьшение шероховатости.
4. обработка давлением: обкатывание, выглаживание, накатывание
Детали, имеющие поверхности вращения (цилиндрические, наружные, фасонные и др.) обрабатывают на различных станках: токарной группы (токарно-винторезные, токарно-карусельные, токарно-револьверные, одношпиндельные и многошпиндельные полуавтоматы и автоматы, станки для тонкого точения и др.); шлифовальной группы (круглошлифовальные, бесцентро-шлифовальные, притирочные, полировальные и т.п.)
Дата добавления: 2018-02-15; просмотров: 445; Мы поможем в написании вашей работы! |
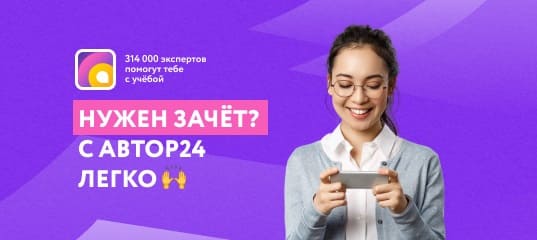
Мы поможем в написании ваших работ!