Проведение дефектовки термостата.
После очистки от загрязнений и мойки детали подвергают дефектации с целью обнаружения в них дефектов и сортировки на годные для дальнейшего использования, требующие ремонта и негодные. Разбраковку ведут в соответствии с техническими условиями на контроль и сортировку деталей, выполненными в виде карт. В карту вносят следующие данные: общие сведения о детали; перечень возможных дефектов; способы обнаружения дефектов; указания о допустимости дефектов и рекомендуемые способы их устранения.
К деталям, годным для дальнейшего использования, относят те, которые имеют допустимые размеры и шероховатость поверхности, согласно чертежу, и ж имеют наружных и внутренних дефектов. Такие детали отправляют на склад запасных частей или в комплектовочное отделение.
Детали, износ которых больше допустимого, но годные к дальнейшей эксплуатации, направляют на склад накопления деталей, а далее — в соответствующие ремонтные цехи для восстановления.
Негодные детали отправляют на металлолом, а вместо них со склада выписываются запасные детали.
Задача термостата проста – по достижении определенной температуры охлаждающей жидкости он начинает открываться и пускать часть охлаждающей жидкости через радиатор (т.е. часть жидкости идет уже по большому кругу), по достижении температуры полного открытия (она иногда выбита на нем или указана в мануале) вся охлаждающая жидкость идет через радиатор (малый круг уже закрыт). Рабочим элементом термостата является “упругое тело”, которое в зависимости от температуры в большей или меньшей степени расширяется. Из этого следует 2 основных дефекта – а) не открывается или открывается малопоздно, б) – открывается рано, т.е. температура полного открытия уменьшилась или не закрывается вообще. Есть еще 3-й дефект (встречается намного реже) – механическая поломка, последствия могут быть различны.
|
|
С первым дефектом все просто – машина “кипит”, при этом радиатор либо холодный, либо мало прогрет. Так как охлаждающая жидкость в малом контуре мало, а теплообмен с окружающей средой минимален, то от момента запуска холодного мотора до его закипания проходит совсем немного времени.
Различие в следующем – при пробое система охлаждения работает так, как ей и положено, т.е. термостат откроется, охлаждающая жидкость пойдет через радиатор, включится вентилятор, но её возможности по “сбросу” избыточного тепла ограниченны (а его количество резко возрастает). Тут возможны различные сценарии, в зависимости от степени “пробоя”. Если пробой “классический”, т.е. сильный – кипение наступит даже на 80, несмотря на усиленно работающий вентилятор. Однако, чаще пробой слабый, и на 80 вроде бы все в порядке, а на оборотах мотор начинает перегреваться. Это может (но не обязательно) сопровождаться “троением”, паром из выхлопа, а при наличии катализатора очень резким и едким его запахом. Аналогично поведут себя и более экзотические дефекты, например трещина в головке.
|
|
Второй дефект встречается намного чаще и обычно его начинают замечать осенью, при первых похолоданиях. Симптомы такие – на 80 и при езде в городе на малых скоростях – все хорошо. При движении же по трассе температура начинает падать и тем больше, чем холоднее. Падение может доходить до 50 градусов. Механическая поломка термостата обычно ведет себя также. Также этот дефект сопровождается относительно долгим прогревом мотора.
Термостаты могут иметь и другие неисправности: отрыв трубок; трещины между гофрами; изгиб пластин подвески термостатов.
Оторванные трубки припаивают мягким припоем. При наличии трещины в первом углублении от крышки или донышка цилиндра термостата цилиндр обрезают по трещине и донышко или кромку припаивают к следующему выступу. При наличии трещин в других углублениях или при наличии трещин на выступах термостат выбраковывают. Изогнутые пластины подвески выправляют.
|
|
В соответствии с техническими условиями процесс дефектации проводится в следующем порядке. Сначала внешним осмотром обнаруживают повреждения: видимые трещины, пробоины, задиры, риски, коррозию и т. ^ оценивают состояние трущихся поверхностей и соответствие их нормальному процессу эксплуатации. Далее детали, прошедшие внешний осмотр, проверяются на соответствие их геометрических параметров и физико-механических свойств с заданными по чертежу. Из числа геометрических параметров устанавливаются действительные размеры деталей, погрешности формы (овальность, конусность, прогиб), погрешности расположения (биение, несоосность, непараллелыюсть и др.).
Измерение некоторых параметров приводится на рис. 3, 4,5.
Рис. 3. Измерение овальности.
Рис. 4. Измерение конусности.
Рис. 5. Изменение биения (а) и непрямолинейности(б).
Полученные результаты измерений сравниваются по чертежу. Они позволяют установить годность деталей и дают возможность прогнозирования остаточного ресурса пары трения, например по разности размеров:
Где dдейст. и dпред. —действительный измеренный и предельный размеры детали.
|
|
Величина ∆ d с учетом величины износа должна обеспечить нормальную работу пары трения до следующего ремонта.
В процессе эксплуатации автомобиля происходят изменения физико-механических свойств деталей. Контроль за изменением свойств осуществляется по величине твердости, измерение которой производится твердомерами. Твердость детали должна быть не ниже указанной на чертеже или в технических условиях.
Потерю жесткости рессор и пружин оценивают по величине прогиба при определённой нагрузке на специальных приспособлениях.
Окончательное заключение о годности деталей делается после контроля дефектов.
Под дефектом понимается недопустимая несплошность металла детали.
К числу дефектов, встречающихся в термостате автомобиля, относятся Трещины различного происхождения (сварочные, усталостные, закалочные, шлифовочные, водородные и др.), коррозионные изъязвления, поры, неметаллические включения и др. По расположению дефекты бывают поверхностными и внутренними. Известно большое разнообразие методов установления дефектов. Из них в авторемонтном производстве наибольшее применение нашли такие методы неразрушающего контроля как магнитный, капиллярный и ультразвуковой.
Сущность магнитного метода контроля состоит в том, что при намагничивании контролируемой детали дефекты создают участок с неодинаковой магнитной проницаемостью, вызывающей изменение величины и направления магнитного потока. Магнитные силовые линии проходят через деталь и огибают дефект, как препятствие с малой магнитной проницаемостью.
Для выявления дефектных мест деталь сначала намагничивают, а затем поливают суспензией или наносят равномерный слой сухого магнитного порошка. Суспензия представляет собой смесь керосина и трансформаторного масла в одинаковом соотношении, в котором во взвешенном состоянии находятся частицы магнитного порожка (оксид железа). Магнитный порошок под действием магнитного поля будет притянут краями дефекта и четко обрисует его границы.
После контроля детали необходимо размагнитить, для чего при переменном токе деталь медленно выводят из соленоида, а при достоянном токе меняют полярность, постепенно уменьшая ток.
Метод магнитной дефектоскопии обеспечивает высокую производительность и дает возможность обнаружить трещины шириной до 0,001 мм на глубине до 6 мм. Применяется метод для контроля деталей, изготовленных из ферромагнитных материалов (сталь, чугун).
Для контроля деталей из цветных металлов и сплавов, пластмассы и других материалов применяют капиллярный метод дефектоскопии.
Сущность капиллярной дефектоскопии заключается в том, что на контролируемую поверхность наносят слой специального цветоконтрастного жидкого индикаторного вещества.
Поверхностные дефекты представляют собой капиллярные сосуды, способные «всасывать* смачивающие их жидкости; в результате такие дефекты оказываются заполненными индикаторным веществом. Избыток индикаторной жидкости удаляют с поверхности. Затем с помощью проявителей индикаторную жидкость извлекают и на поверхности появляются очертания дефекта.
Одним из способов капиллярного метода контроля является «керосиновая проба». На поверхность детали наносят керосина и выдерживают в течение 15—20 мин. Затем ветошью тщательно протирают поверхность насухо. Далее на поверхность наносят проявитель, представляющий собой водно-меловой раствор. При высыхании мел вытягивается и на поверхности появляется керосиновое пятно. Способ весьма прост, но образующееся пятно не дает полных сведений о форме и размерах дефекта.
Поэтому более широко для выявления поверхностных дефектов применяется способ красок. В качестве индикаторной жидкости рекомендуются растворы: 50% бензола, 50% Скипидара с краской судан IV (судан III); 40% керосина, 40% зола, 20% скипидара с краской судан IV. Судан прибавляют к индикаторной жидкости в количестве до 1%.
На контролируемую поверхность наносят мягкой кистью индикаторную жидкость и выдерживают 3—5 мин. Затем поверхность очищают от остатков индикаторной жидкости ветошью, смоченной 5 %-ным раствором кальцинированной соды, и протирают насухо. Далее на контролируемую поверхность с помощью пульверизатора наносят проявитель. Состав проявителя: 300 г мела (зубной порошок), 0,5 л воды, 0,5 л этилового спирта.
Первое наблюдение следов дефекта проводится через 3— 5 мин после высыхания мела. Трещины проявляются в виде красных полос, поры — в виде пятен. Второе наблюдение ведется через 20—30 мин. За это время жидкость растекается, ширина полос увеличивается. При ширине дефекта 0,01 мм ширина цветного следа равна 1 мм.
Разновидностью капиллярного метода служит люминесцентный способ контроля дефектов, основанный на свойстве некоторых веществ светиться при облучении их ультрафиолетовыми лучами.
Очищенные и обезжиренные детали помещают на 10— 15 мин в ванну с флюоресцирующей жидкостью, имеющей состав 50% керосина, 25 — бензина и 25% трансформаторного масла с добавкой флюоресцирующего красителя. Жидкость проникает в дефекты и там задерживается. Остатки жидкости смывают холодной водой, деталь сушат сжатым воздухом и припудривают порошком селикагеля. При освещении детали ультрафиолетовым излучением порошок селикагеля, пропитанный флюоресцирующей жидкостью, будет ярко светиться желто-зеленым светом. Трещины будут видны в виде широких полос, поры — в виде пятен.
Люминесцентные дефектоскопы позволяют выявить трещины шириной 0,01 мм.
Ультразвуковой метод дефектоскопии основан на свойстве ультразвука проходить через металлические изделия и отражаться от границы раздела двух сред, обладающих разными акустическими свойствами. Источникам ультразвуковых колебаний служат пластинки кварца, титаната бария, обладающие пьезоэлектрическим эффектом, сущность которого состоит в следующем. Если на пластинку кварца подать электрический ток высокой частоты, то она будет издавать механические колебания той же частоты. И, наоборот, если пластине дать механические колебания, она будет вырабатывать электрический ток той же частоты. По этому принципу устроены импульсные ультразвуковые дефектоскопы.
Метод ультразвуковой дефектоскопии позволяет установить любые дефекты (трещины, поры, неметаллические включения и т. д.), залегающие на глубине 1—2500 мм.
Для обнаружения скрытых дефектов в полых деталях широко применяется Метод гидравлических и пневматических испытаний.
Проводятся такие испытания на специальных стендах. Так, дефекты в блоке и головке блока цилиндров устанавливают гидравлическим испытанием на стенде, обеспечивающим герметизацию всех отверстий. Блок заполняется горячей водой, и в нем создается давление 0,3—0,4 МПа. Наличие дефектов определяют по подтеканию воды
Пневматические испытания позволяют определить герметичность радиаторов, топливного бака и др. путем закачки в них сжатого воздуха под давлением, согласно техническим условиям. Далее агрегаты помещают в ванну с водой и по выделению пузырьков определяют место нахождения дефекта.
Дата добавления: 2018-02-15; просмотров: 3533; Мы поможем в написании вашей работы! |
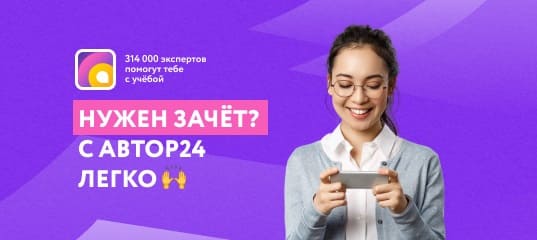
Мы поможем в написании ваших работ!