Нормы для показателей текучести моделировочных восков
Температура , °С | Мягкие | Твердые | Экстра твердые | |||
Мин. | Макс. | Мин. | Макс. | Мин. | Макс. | |
23,0+ 0,1 | – | 1,0 | – | 0,6 | – | 0,2 |
37,0+ 0,1 | 5,0 | 90,0 | – | 10,0 | – | 1,2 |
45,0+ 0,1 | – | – | 50,0 | 90,0 | 5,0 | 50,0 |
При исследовании восков проводят два испытания для каждой температуры указанной в таблице. Для измерения текучести вместо прямого измерения образцов микрометром допускается использовать прибор с измерительным датчиком и стопорным винтом. Под латунную пластину прибора помещают две полиэтиленовые пленки и устанавливают датчик на «0». Помещают образец между двумя полиэтиленовыми пленками в прибор для измерения текучести. Освобождают стопорный винт и прикладывают к образцу осевую нагрузку в течение 1 мин при температуре 23±2°С. Закручивают стопорный винт и записывают показания датчика как первоначальную длину образца. Помещают прибор для измерения текучести с образцом и зажатым стопорным винтом в термостат с водой при испытательной температуре так, чтобы образец погружался на глубину не менее 50мм. Выдерживают систему в течение 20 мин. Прикладывают осевую нагрузку в течение 10 мин, освобождая стопорный винт. Затягивают стопорный винт и вынимают прибор для измерения текучести из термостата. Охлаждают всю систему с затянутым стопорным винтом на воздухе при температуре 23±2°С в течение 30 мин. Освобождают стопорный винт на 30 с и записывают показания датчика как конечную длину образца.
|
|
Если один из двух результатов не соответствует требованиям, то проводят испытания двух дополнительных образцов. Если один из результатов дополнительного испытания не соответствовут требованиям, то базисный воск считают не выдержавшим испытание.
Методы испытания температуры плавления. Температуру плавления базисного воска определяют с помощью прибора Жукова по ГОСТ 4255. Сущность метода заключается в определении температуры, по которой закристаллизовывается основная масса предварительно расплавленного продукта. При испытании используют: прибор Жукова — сосуд Дюара из прозрачного стекла, термометр, секундомер, термостат. Испытуемый воск расплавляют в термостате на 15–25°С выше предполагаемой температуры плавления.
Расплавленный воск перемешивают и заливают в подогретый прибор Жукова на 0,75 его высоты. По достижении температуры продукта на 3–4°Свыше предполагаемой температуры плавления прибор встряхивают и с помощью секундомера наблюдают за понижением температуры, записывают отсчеты через каждую минуту. За температуру плавления принимают температуру, сохранившуюся постоянной не менее чем за три отсчета. За результат испытания принимают среднее арифметическое двух определений.
|
|
Тесты.Моделировочные материалы
1. Базисный воск выпускается производителем в виде:
1) пластинок толщиной 1,5 мм
2) кубиков
3) круглых палочек
4) круглых полосок
5) пластинок округлой формы
2. Для восстановления анатомической формы зуба на гипсовой модели при изготовлении искусственных коронок применяют воск:
1) базисный
2) липкий
3) моделировочный
4) лавакс
5) верно 1) и 2)
3. Какой из видов воска применяется для прокладок на моделях при изготовлении каркасов дуговых протезов и в качестве моделировочного при изготовлении цельнолитых и комбинированных базисов в съемных пластиночных протезах:
1) базисный
2) моделировочный
3) профильный
4) липкий
5) бюгельный
4. Воск, используемый для моделирования стеклокерамических протезов, называется:
1) моделировочным
2) эстетическим
3) профильным (восколит)
4) бюгельным
5) липким
5. Температура плавления выравнивающего моделировочного воска:
1) 120°С
2) 100 °С
3) 140°С
4) 160°С
Ответы на вопросы к главе 6
1) верно 1
2) верно 3
3) верно 5
4) верно 2
5) верно 1
4.3. Формовочные материалы.Требования, предъявляемые к формовочным материалам. Классификация. Химические свойства. Показания к использованию различных видов формовочных материалов.
|
|
Качество литья ажурных конструкций из различных сплавов в ортопедической стоматологии зависит от многих факторов: от свойств стоматологических сплавов и металлов; точности формы для литья; материала формы и его состава, а также технологии формования. Для получения точной отливки по выплавляемой модели необходим качественный формовочный материал.
Формование есть процесс изготовления формы для литья металлов, пластмасс и др., а формовочная масса служит материалом для этой формы.
Известны различные рецептуры и технологии применения формовочных масс, но во всех случаях неизменными составляющими остаются связующие вещества и огнеупорная основа, в подавляющем большинстве — порошок.
В зубном протезировании до применения никелехромовых и кобальтохромовых сплавов, обладающих высокой температурой плавления, в качестве формовочной массы применялся отмученный порошок глинозема А12O3, смешанный с гипсом и замешанный на воде, т.н. «минутник».
С развитием технологии литья по выплавляемым моделям с применением нержавеющих сталей, в частности кобольтхромовых, возникла необходимость создания специального состава формовочных материалов. В связи с этим потребовалось соблюдение основных требований технологического характера.
|
|
Основные требования к формовочным материалам:
· воспроизведение поверхности отлитого изделия для обеспечения качественной поверхности отливки, в связи с чем огнеупорный порошок должен иметь высокую дисперсность;
· легкое отделение формовочного материала от отлитого изделия, т.е. поверхность формы не должна «пригорать» к отливке;
· время затвердевания должно быть в пределах 7–10 мин;
· формовочный материал в отвержденном виде должен создавать газопроницаемую оболочку, которая будет в состоянии поглощать газы, образующиеся при заливке расплавленного металла;
· иметь величину коэффициента температурного расширения, достаточную для компенсации усадки затвердевающего металла.
В современном литейном производстве используют гипсовые, фосфатные и силикатные формовочные материалы.
Гипсовый формовочный материал состоит из гипса (20–40%) и окиси кремния. Гипс в этом случае является связующим. Окись кремния придает массе необходимую величину усадочной деформации и теплостойкость. В качестве регуляторов скорости затвердевания и коэффициента теплового расширения в смесь добавляется 2–3% хлорида натрия или борной кислоты. Замешивается масса на воде при температуре 18–20 °С. Номинальная температура разогревания формы подобного состава до заливки металла составляет 700–750 °С. Эти формы непригодны для получения отливок из нержавеющей стали, температура плавления которой 1200–1600 °Сиз-за разрушения гипса, и поэтому их используют для литья изделий из сплава золота.
Для изготовления вкладок, кламмеров, дуг, искусственных зубов применяется формовочная масса, состоящая из гипса и кремнезема, в соотношении 3 : 1. Замешивание производят на воде, время схватывания — до 30 мин. Для получения высокоточного литья из сплавов благородных металлов формовочная масса должна обладать техническими параметрами, которые гарантируют сохранение объема в критическом температурном интервале 200–300 °С.
Фосфатные формовочные материалы состоят из порошка (цинкфосфатный цемент, кварц молотый, кристоболит, окись магния, гидрат окиси алюминия и др.) и жидкости (фосфорная кислота, окись магния, вода, гидрат окиси алюминия).
Такие формовочные материалы компенсируют усадку при охлаждении нержавеющих сталей, которые имеют температурный коэффициент объемного расширения примерно 0,027 °С-1. Усадка золотых сплавов составляет около 1,25%, и эту усадку компенсирует только гипсовая форма. Схватывание фосфатных форм в зависимости от состава продолжается 10–15 мин. Они применяются для литья высокоплавких хромокобальтовых сплавов. Известны универсальные формовочные фосфатные массы на основе фосфатного вяжущего материала, кварца и кристобалита, а также массы с самыми чистыми сортами кварца и жаростойкого вяжущего материала. Зернистость формовочной массы влияет на продолжительность затвердевания, прочность формы после обжига и изменение объема. Для замешивания можно использовать воду в соотношении 1 : 1 с обязательным применением бумажной манжеты для предотвращения возможной деформации формы. В настоящее время для замешивания формовочного материала используют золь кремниевой кислоты, благодаря чему повышается прочность формы, и соответственно повышается ее устойчивость при нагревании и обеспечивается компенсация температурных изменений сплава. Тонкозернистые формовочные материалы для литья неблагородных сплавов обеспечивают быстрое выгорание и создают безопочным методом качественную литьевую форму. Такие материалы воска выдерживают относительно быстрый подъем температуры, при этом получаемые отливки имеют достаточно высокую чистоту поверхности.
Для смешивания формовочного материала и жидкости важно использование смесителя — вакуммиксера.
Силикатные формовочные материалы отличаются высокой термостойкостью и прочностью. Их внедрение вызвано применением высокотемпературных кобольтохромовых нержавеющих сталей. Кроме гипса и фосфатов, в качестве связующих здесь используют кремниевые гели. Из органических соединений кремния чаще применяется тетра-этилортосиликат Si(OC2H7)4, который легко гидролизуется с образованием при прокаливании конечных продуктов в виде двуокиси кремния. Вяжущая жидкость силикатной формовочной массы состоит из смеси этилового спирта, воды и концентрированной соляной кислоты, куда постепенно (по каплям) введен этилсиликат. В качестве огнеупорной составляющей (порошка) чаще применяются кварц, маршаллит, корунд, кристоболит и другие вещества. Силикатные формовочные массы отличаются большим коэффициентом термического расширения. Для обеспечения точности отливки необходимо соблюдать правильное соотношение между порошком и жидкостью (вяжущим раствором). Оптимальное соотношение, обеспечивающее компенсацию усадки формы, составляет 30 г жидкости и 70 г порошка. Время схватывания материала до 30 мин. Материал, содержащий молотый пылевидный кварц, формовочный песок и борную кислоту, может быть использован для отливки деталей протезов из нержавеющей стали. Для литья сплавов золота применим формовочный материал на основе кристобаллита и технического гипса, замешанный на воде. Материал обладает необходимой прочностью и чистотой поверхности.
Литье каркасов современных съемных и несъемных протезов из высокотемпературных сплавов требует от формовочного материала высоких компенсационных и прочностных показателей. В состав таких материалов входят кварцевый песок, фосфаты, периклаза, замешивание проводят на силиказоле в резиновой чашке на вибростолике в течение 40 c в соотношении порошок–жидкость 100 : 18–20. Затвердевание после заполнения кюветы с восковой заготовкой начинается через 10–15 мин и заканчивается через 30 мин после замешивания.
Для литья благородных сплавов иногда применяют формовочные массы, наполненные графитом и без графита, с расширением 2,15% и 2,45%, замешиваемые на дистиллированной воде или специальных жидкостях, от концентрации которых зависит степень расширения материала.
Формовочные материалы в зуботехническом производстве имеют первостепенное значение для получения точной, соответствующей необходимым требованиям отливки и предназначены для покрытия восковой модели. В отдельных случаях до паковки модель необходимо покрыть облицовочным слоем. Для облицовочного слоя используется материал (порошок), состоящий из смеси кальцинированного гипса, двуокиси кремния (кремнезема) и некоторых модифицирующих агентов. Такой порошок, замешанный в соответствующей пропорции с водой и нанесенный на восковую модель при последующем обжиге, должен отвечать требованиям, необходимым для получения качественной отливки. К этим требованиям относятся:
· порошок должен состоять из частиц высокой дисперсности;
· время отвердевания (схватывания) массы должно быть не меньше 5–25 мин;
· предел прочности формы при сжатии не менее 2,5 МПа;
· температурный коэффициент объемного расширения при отвердевании оболочковой формы должен быть в пределах ± 0,001 К-1;
· материал оболочковых форм не должен отрицательно влиять на качество поверхности отливки и быть причиной образования поверхностных дефектов и шероховатостей.
Быстронагревамые паковочные массы для изготовления бюгельных протезов. Массы быстрого прогрева значительно сокращают время предварительного нагревания. У таких масс, по сравнению с обычными, расширение в процессе затвердевания больше, чем термическое. Благодаря этому не повышается давление, возникающее дополнительно при предварительном нагреве за счет термического расширения и выделения водяного пара и аммиака.
Для обычных масс при прогреве необходимы стадии выдержки, чтобы снизить давление при термическом расширении кристобаллита и кварца. Интервалы способствуют медленному удалению остатков влаги.
У масс быстрого прогрева (опоки через 20 мин после паковки ставят в муфельную печь) температура при помещении в муфельную печь намного выше (700–1000 ºС), чем температура, при которой происходит кристобаллитовый или кварцевый скачок наполнителей.
Высокая мелкозернистость улучшает текучесть при паковке и обеспечивает очень гладкую поверхность моделей, уменьшается образование оксидного слоя, отлитый объект легче извлекается их паковочной массы.
Тесты. Формовочные материалы
1. В современном литейном производстве используют следующие виды формовочных материалов:
1) фосфатные
2) гипсовые
3) силикатные
4) верно 1–3
2. Продолжите определение: формование — это процесс ….
3. Основные требования к формовочным материалам:
1) высокая дисперсность порошка
2) легкое отделение формовочного материала от отлитого изделия
3) время затвердевания должно быть в пределах 7–10 мин
4) иметь величину коэффициента температурного расширения, достаточную для компенсации усадки затвердевающего металла
5) верно 1)–4)
4. Какие формовочные массы применяются для литья высокоплавких хромокобальтовых сплавов?
1) гипсовые
2) фосфатные
3) силикатные
5. Время схватывания материала силикатных формовочных материалов
1) до 30 мин
2) до 1 ч
3) 10–15 мин
4) 5–10 мин
Ответы на вопросы к главе 8
1) верно 4
2)[U47] Формование есть процесс изготовления формы для литья металлов, пластмасс и др.
3)верно 5
4)верно 2
5)верно 1
4.4. Абразивные материалы
4.4.1. Основные свойства абразивных стоматологических материалов применяемых в ортопедической стоматологии
Абразивными материалами, применяемыми в стоматологии, являются материалы для шлифования и полирования стоматологических, т.н. реставраций, иными словами пломб, а также окончательной обработки (отделки) ортопедических конструкций, таких как вкладки, виниры, съемные и несъемные зубные протезы из различных конструкционных, в т.ч. и облицовочных материалов. Под окончательной обработкой понимаются заключительные последовательные процессы шлифования и полирования ортопедических конструкций протезов и ортодонтических аппаратов.
Шлифование — обработка по удалению шероховатостей и неровностей с поверхности обрабатываемых стоматологических конструкций зубных протезов и аппаратов.
Полирование — конечный процесс обработки с целью получения гладкой, блестящей поверхности зубных протезов и аппаратов.
Известно, что различные шероховатости, отсутствие гладкой, хорошо отполированной поверхности зубного протеза, может вызвать у пациента значительный дискомфорт и осложнить гигиену полости рта. На таких поверхностях, в агрессивной среде полости рта, происходит формирование зубного налета и в последствии — твердых зубных отложений, которые способствуют появлению неприятного запаха изо рта, раздражению слизистой оболочки полости рта и в большинстве случаев способствуют возникновению ряда заболеваний, как стоматологического характера, так и общего. Все это является причиной снижения процесса адаптации, в т.ч. и к зубным протезам.
В тоже время, качественная обработка поверхности протезов в значительной степени устраняет вышеперечисленные осложнения, при этом способствуя повышению эстетических показателей зубных протезов, их прочности и долговечности. Гладкая поверхность композитных, пластмассовых, комбинированных протезов и аппаратов лучше противостоит процессам деструкции — старения и разрушения — в результате воздействия продуктов жизнедеятельности микроорганизмов, перепада температур и др. Гладкая, зеркально отполированная поверхность способствует коррозионной устойчивости сплавов и повышению физико-механических свойств пластмасс.
Материалы, используемые для шлифования и полирования, являются, прежде всего, абразивами, получившими свое название от слова абразия —процесс стирания.
Абразия зависит от физических и механических свойств, как образива, так и материала, подвергаемого обработке. При этом важное значение имеют такие свойства материалов, как твердость, прочность, гибкость и теплопроводность.
Абразивные материалы состоят из мелкозернистых веществ, превышающих по твердости материалы, подлежащие шлифованию и полированию. Применение абразивных материалов предполагает движение их по обрабатываемой поверхности. При этом каждое зерно абразивного материала совершает режущее, скоблящее действие. Однако они отличаются от стоматологических режущих инструментов тем, что режущие края абразивов не расположены в определенном порядке, как у инструментов, например, предназначенных для препарирования твердых тканей зубов. Каждый острый край абразива действует как отдельный режущий инструмент и удаляет некоторую часть материала с поверхности. Характер действия зерна абразива зависит от его размера, формы, количества, состава и свойств.
Процесс шлифования и качество обрабатываемой поверхности зависят от многих факторов. При этом важное значение имеют такие факторы, как:
- размер абразивных частиц;
- давление абразива на материал и его теплопроводность;
- скорость, с которой абразивные частицы движутся по поверхности, подвергаемой абразии.
Все эти факторы необходимо контролировать.
Первый важный фактор для скорости абразии поверхности — размер абразивных частиц.Зерна для шлифования сортируются по величине при помощи фракционного просеивания. По зернистости абразивные материалы делят, как правило, на 3 группы: шлифзерно; шлифпорошки; микропорошки. Чаще применяются зерна размером 0,15–0,75мм. Однако для грубого шлифования могут использоваться и более крупные зерна, размер которых доходит до 1,5–2 мм.Частицы большого размера создают более глубокие бороздки в материале и вызывают стирание поверхности с большей скоростью. Использование грубого абразива показано на поверхности с многими участками шероховатости или неровностями. Затем, чтобы удалить царапины, вызванные грубым абразивом, используют более мелкозернистые абразивы.
Второй важный фактор — давление абразива на обрабатываемую поверхность. Приложенное давление должно быть умеренным, чтобы не привести к поломке протеза или инструмента. Кроме того, излишнее давление приводит к нагреванию инструмента и поверхности обрабатываемого объекта, подвергающегося шлифованию. Причиной образования тепла при шлифовании является трение абразивных зерен о поверхность.
Высокие температуры, хотя их воздействие и кратковременно, способны привести к изменению структуры металла (сплава) или деформациям пластмасс. Все это сказывается на снижении прочности и износоустойчивости шлифуемого изделия. Перегрева нужно и можно избежать, соблюдая правильный режим шлифования.
Третьим фактором, который определяет скорость абразии, — скорость движения абразива вдоль обрабатываемой поверхности. Чем медленнее движется абразив, тем большую стружку снимает зерно абразива и, следовательно, тем больше разрушающее усилие испытывает абразивное зерно. При быстром движении по поверхности обрабатываемого изделия абразив снимает меньшую стружку и поэтому испытывает меньшее сопротивление, а, следовательно, меньше изнашивается. При одинаковой скорости перемещения грубые абразивные частицы снимают больше материала с обрабатываемого изделия, оставляя более глубокие трассы (царапины). Оптимальная скорость абразива с сохранением его эффективной абразивной способности зависит от вида абразивного материала. Для большинства из них оптимальная скорость равна 25–30 м/с.
4.4.2. Классификации абразивных материалов и инструментов
Абразивные инструменты, применяемые в ортопедической стоматологии, подразделяют по назначению на:
· шлифовочные;
· полировочные.
Для скрепления абразивных зерен, их связки применяют неорганические и органические материалы.
К неорганическим материалам относят:
- керамические;
- силикатные;
- магнезитовые.
К органическим материалам относятся:
- бакелитовые;
- вулканитовые;
- пасты на основе органического связующего.
Керамические связующие материалы основаны на применении смеси глины с полевым шпатом, тальком и другими веществами, например кварцем. Эта связка огнеупорна и обладает высокой механической прочностью. Применяется для изготовления различного рода шлифовальных кругов. Недостатками изделий на этой основе являются хрупкость и высокая чувствительность к ударам. Поэтому изделия на керамическом связующем материале применяют в установках с малыми оборотами.
Достоинства подобной связки: влагостойкость и равномерная твердость.
Бакелитовые связующие материалы готовятся на основе лака бакелита, реже — каучука и различных клеевых композиций. Бакелит — искусственная смола, образующаяся при взаимодействии фенолов или крезолов с формальдегидом. После наполнения абразивом и горячего прессования получается достаточно прочный абразивный инструмент. Он нашел широкое применение в зубопротезной технике. Круги либо иные формы абразивов на этой основе отличаются упругостью, ударостойкостью, гладкой поверхностью. Этот вид связки применяется также для изготовления наждачной или стеклянной бумаги, а также наждачного полотна.
Недостаток данной связки — меньшая прочность сцепления с абразивными зернами по сравнению с керамическими материалами.
Вулканитовые связующие материалы основаны на применении смеси каучука с серой, которая после введения абразивного порошка подвергается вулканизации. Указанные связки обладают еще большей упругостью и плотностью, чем бакелитовые, и отличаются большей эластичностью.
Круги с вулканитовой связкой незаменимы при шлифовании, когда от круга требуется не только шлифующее, но и полирующее действие. Последнее объясняется размягчением связки при температуре около 150°С и вдавливанием абразивных зерен в эту размягченную связку. Абразивный инструмент на бакелитовой и вулканитовой связке очень прочен и дает хорошие результаты обработки.
В промышленности из зерен абразива чаще изготавливают разнообразные инструменты. При этом абразивные инструменты характеризуются:
1) родом абразивного материала (Э— электрокорунд; Е— корунд естественный; КЧ— карборунд [U48] черный);Да
2) номером зернистости (от 10 до 320— порошки, от 10 до 45— микропорошки);
3) классом твердости (ЧМ— чрезвычайно мягкий; ВМ— весьма мягкий; М— мягкий; СМ— средне мягкий; С— средний;СТ— средне твердый; Т— твердый; ВТ— весьма твердый; ЧТ— чрезвычайно твердый);
4) родом связки (К— керамическая; Б— бакелитовая; В— вулканитовая; С— силикатная; М — магнезитовая).
Абразивные инструменты, применяемые в стоматологической практике и зубопротезной технике, должны обладать определенными свойствами:
1) быть прочными;
2) не сыпучими во время обработки;
3) при умеренном нагревании не изменять своих качеств;
4) обладать режущими, шлифовальными качествами;
5) подвергаться стерилизации;
6) быть доступными в ценовой характеристике.
Абразивный инструмент имеет большую вариабельность по форме и фасону. Различается по форме инструмента. Это могут быть круги, фрезы, головки различных размеров и форм: тарельчатые, чашечные, чечевичные, грушевидные, конусовидные и др. К абразивному инструменту также относится наждачное полотно и наждачная бумага.
По абразивным свойствам материалы располагаются в следующем порядке: алмаз, корунд, электрокорунд, наждак, гранат.
Естественные абразивные материалы.Алмаз— кристаллическая разновидность углерода, эталон твердости. По шкале Мооса он имеет наивысшую твердость, равную 10. В стоматологии мелкая алмазная крошка применяется для препарирования зубов. Эти инструменты обладают большой износостойкостью, а процедура препарирования зубов становится более быстрой и менее травматичной.
Корунд— естественный материал, кристаллы которого содержат до 90% окиси алюминия. Примеси (оксиды железа и кремния) придают ему различные цветовые оттенки. По шкале Мооса его твердость равна 9.
Наждак — смешанная горная порода, состоящая из 97% корунда, соединений железа и других минералов. Твердость по шкале Мооса 7–8. Для получения высококачественного продукта природный наждак обогащают, т.е. уменьшают количество примесей до 1–2%. Наждачные полотна или диски используют для шлифования.
Гранаты — группа природных минералов, представляющих собой ортосиликаты. Твердость по шкале Мооса6,5–7,5.
Пемза — продукт вулканической деятельности. Основным компонентом ее является кремнезем (60—70%). Пемза очень пористый, твердый, хрупкий материал. В зуботехнической практике мелкий порошок пемзы во взвеси с водой применяют для шлифования пластмассовых зубных протезов.
Искусственные абразивные материалы.Электрокорунд — кристаллическая окись алюминия (А1203) получают из пород, содержащих глинозем. Электрокорунд содержит от 85 до 98% окиси алюминия. Имеет твердость по шкале Мооса около 9. Материал термостойкий, применяется для шлифования твердосплавных металлических и других изделий.
Карборунд — представляет собой соединение кремния с углеродом (SiC), имеет кристаллическое строение, твердость по Моосу 9,5–9,75. Карборунд получают 2 видов. Черный карборунд содержит не менее 95% SiС. В состав земного карборунда входит 97% SiС.
В стоматологии используют оба вида карборунда. Карборундовые инструменты обладают хорошей шлифующей способностью. Зерна карборунда имеют неправильную форму с четко выраженными острыми ребрами, что обеспечивает высокую режущую способность. Карбид кремния термоустойчив.
Карбиды бора и вольфрама представляют собой химические соединения соответствующих металлов с углеродом. Материалы имеют твердость близкую к твердости алмаза.
Карбид бора (В4С) обладает высокой твердостью и хрупкостью, применяется в промышленности для обработки твердосплавных инструментов.
Карбид вольфрама в мелкодисперсном виде употребляется вместо алмазной крошки при изготовлении боров.
Некоторые шлифовальные материалы (пемза, наждак) применяются в виде водной суспензии, которая наносится на обрабатываемую поверхность с применением щеток, войлочных кругов (конусов) и других приспособлений.
4.4.3. Методы шлифования и полирования. Инструменты, используемые для шлифования и полирования.
Методы шлифования и полирования большинства конструкционных стоматологических материалов выполняются по одинаковым принципам. Главное правило успешной обработки стоматологической конструкции является строгое соблюдение рекомендованной последовательности применения абразивов.
Поверхность зубного протеза обрабатывают сначала напильниками, шаберами, штихелями, точильными камнями или с помощью пескоструйного аппарата. За этой грубой обработкой следует шлифовка, т.е. заглаживание оставшихся следов наждачными бумагой или полотном. В большинстве случаев шлифование обеспечивает высокую чистоту поверхности — до 6–10 классов.
Шлифование и полирование должно проводиться по четкой схеме, начиная с достаточно грубых абразивов, чтобы удалить глубокие царапины и неровности. Частицы любого абразива оставляют царапины на поверхности. Использование слишком мелкозернистого абразива сразу после грубого требует значительных затрат времени и не позволяет качественно отполировать поверхность.
Поверхность заглаживается абразивами с последовательным уменьшением размера частиц, при этом до их полного устранения или уменьшения до микроскопического размера.
После окончательной отделки-полирования изделие приобретает блестящую поверхность, что характеризуется чистотой поверхности, равной 12–14 классу.
На каждом этапе шлифования и полирования нужно использовать водяное орошение участков, подвергаемых обработке, чтобы смыть отработанные абразивные частицы, т.к. остающиеся грубые частицы могут испортить отполированную поверхность. Не следует использовать абразивное вещество без увлажнения. Сухое полирование может существенно уменьшить эффективность абразивного инструмента и увеличить опасность перегрева поверхности.
Процесс полирования производится разными методами:
· механическим;
· электрохимическим.
Процесс полирования проводят в специальных полировочных комнатах, с обязательным наличием вытяжных шкафов, в респираторных масках для предотвращения попадания мелкодисперсной пыли в дыхательные пути.
Полированием предусмотрено снятие минимального слоя материала, для чего вращающиеся щетки или фильцы покрываются специальными абразивными пастами. В состав этих паст входят абразивные и связующие материалы. В процессе полирования применяются инструменты и материалы, аналогичные употребляемым при шлифовании, но с иной, более мелкой, структурой абразивного наполнителя.
Процесс полирования производится войлочными, матерчатыми, кожаными кругами, нитяными и волосяными щетками, укрепленными на валу шлифмотора. Эластические круги различного диаметра изготавливаются из корунда разной зернистости, круглых нитяных, волосяных или капроновых щеток с использованием полировочных паст, представляющих собой композиции из тонких полировочных абразивов, поверхностно активных и связующих веществ. В качестве поверхностно-активных веществ применяют стеарин, парафин, воск, вазелин. По названию основного компонента различают хромовую, известняковую, крокусовую и другие виды паст.
К полировочным абразивам, применяемым в зубопротезной технике, относятся:
- оксид железа(крокус)(Fe2О3[U49] ); Да
- оксид хрома (Сr2О3);
- мелкодисперстный гипс;
- мелкодисперстный мел (СаСО3).
В зуботехническом производстве очень популярны специальные пасты ГОИ, [U50] имеющие разную зернистость, предложенные Государственным Оптическим Институтом, используемые для полировки металлов и сплавов.
Таблица 2
Состав паст ГОИ
Составляющие
| Паста,% | ||
Грубая | Средняя | Тонкая | |
Окись хрома | 81 | 76 | 74 |
Силикагель | 2 | 2 | 1,8 |
Стеарин | 10 | 10 | 10 |
Жир расщипленный | 5 | 10 | 10 |
Олеиновая кислота | – | – | 2 |
Сода двууглекислая | – | – | 0,2 |
Керосин | 2 | 2 | 2 |
Продолжительность обработки, мин | 7–10 | 4–7 | 1–3 |
Окись хрома получают путем прокаливания смеси бихромата калия с серой. Он представляет собой зеленый порошок кристаллического строения, кристаллы в виде многогранников имеют большую прочность и твердость. Связующими материалами этих паст являются: стеарин, парафин, вазелин и др. подобные вещества. Окись хрома применяется в полировочных пастах, используемых для полировки твердых сплавов (нержавеющая сталь, кобальтохромовая сталь)
Окись[U51] ДАжелеза Fe2O3 — это порошок буровато-красного цвета. Кристаллы окиси железа по прочности уступают окиси хрома. Под названием «крокус»окись железа используется в пастах для полирования сплавов на основе золота, серебра, палладия.
4.4.4. Электрополирование
Электрополирование проводится в специальных электрополировальных установках с использованием электролитов для получения зеркальной поверхности металлического каркаса сложных ортопедических конструкций, таких как каркасы бюгельных протезов с замковыми креплениями и опорно-удерживающими кламмерами. В зависимости от сложности оборудования используется определенный режим: в кислоту погружают каркас протеза, фиксированный зажимом на вертикальной штанге, служащим анодом. Время травления составляет несколько минут, при плотности тока от 0,4 до 5А/см2. Для проведения полирования необходима сила тока 3,5–4,5А, а электролит должен быть подогрет до температуры 35–45 °С. Работа подобных установок должна проводиться при достаточной вентиляции.
4.4.5. Алгоритм обработки зубных протезов и аппаратов
Процессы грубой, предварительной и окончательной обработки поверхности стоматологического изделия, будь то металлический каркас протеза, или же несъемная или съемная конструкция протеза или аппарата, в настоящее время достаточно хорошо отработаны и технологически выверены.
На первом этапе грубой обработки металлических поверхностей зубных протезов после процесса литья предполагается очистка поверхности металлического каркаса от окалины и остатков огнеупорной массы. Это возможно выполнить механическим или электролитическим способом.
Механическая очистка каркаса протеза в настоящее время осуществляется с помощью пескоструйного аппарата с различным диаметром сопла и давлением воздуха около 5 атм., а также с использованием специальных абразивных порошков для струйной обработки. Это могут быть абразивные средства металлической и неметаллической природы, разной дисперстности. Для этих целей используются различные фракции порошков: 25мкм, 50, 110,150, 250мкм.
В зависимости от желаемой степени абразии используют очень крупное зерно корунда (например, для удаления паковочной массы в пескоструйном аппарате с циркуляцией песка) или очень мелкое зерно 25мкм, например, для обработки фиссур на жевательных поверхностях керамических протезов. Более мелким зерном можно обрабатывать керамические поверхности для придания им шероховатостей. Для струйной обработки используется абразивное средство мелкого зернения — для сплавов благородных металлов, грубого — для неблагородных сплавов.
Грубая обработка в основном проводится 24-, 30- и 32-гранными твердосплавными фрезами или борами. Использование алмазного, корундового или карборундового инструмента крайне не желательно в связи с возможным внедрением гранул абразива в металлический каркас, который в дальнейшем будет покрыт керамическим облицовочным материалом. При этом вероятность скола керамической массы очень велика. При облицовывании каркаса композитным материалом или же пластмассой возможно применение любого грубого абразивного инструмента (жесткие шлифкруги, прорезные и отрезные диски и т.п.). При этом поверхность протеза или его заготовки становится чистой от посторонних включений и приобретает матовую поверхность.
На следующем этапе проводится шлифование поверхностей с относительно глубокими рисками, оставшимися после грубой обработки. Оно проводится резиновыми и (или) силиконовыми головками, шлифовальными дисками. При этом поверхности протезов должны приобрести слабо матовый вид с переходом на матовоблестящую поверхность.
Резиновые круги и головки изготавливаются с разной степенью дисперсности абразивного материала. Работать головками необходимо на относительно небольшой скорости с большим количеством воды, не перегревая поверхности, особенно пластмассовых и композитных материалов. Латекс, являющийся одним из связующих, к сожалению, может загрязнять поверхность облицовочного материала протеза.
Силиконовые головки после использования придают «сухой» блеск композиционному или керамическому материалу.
Полирование — заключительный этап отделки протезов, как правило, проводится пастами на жировой или иной основе, редко всухую, без воды. Это первый этап придания блеска поверхности протезов. На втором этапе — придания высокого блеска с классом чистоты около 14 — используются более мелкодисперсные пасты с водой или на жировой основе.
Полировочные диски так же придают «сухой» блеск обрабатываемой поверхности. Они бывают на бумажной, а также на пленочной основе. Диски на пленочной основе более тонкие, гибкие, имеют желто-оранжевую гамму цвета.
Дисками работают на скорости не более 30000об/мин. Высоко абразивные диски применяются на скорости около 10000об/мин, менее абразивные — на больших скоростях.
Абразивные материалы могут использоваться не только для окончательной обработки, но и создания дополнительной шероховатости и улучшения ретенционных характеристик поверхностей.
При полировании пластмассовых изделий — коронок, съемных протезов — абразивный материал используется в виде кашицеобразной массы в смеси с водой. Эту массу наносят на специальные приспособления — фильцы или щетки, укрепленные на конусовидном наконечнике шлифмотора. Полирование проводится на скоростях около 3000 оборотов.
Тесты. Абразивные материалы
1.Продолжите определение: процесс шлифования— это …
2.Продолжите определение: полирование —это …
3.К полировочным абразивам, применяемым в зубопротезной технике, относятся:
1) оксид железа(крокус) (Fe2О3)
2) оксид хрома (Сг2О3)
3) мелкодисперстный гипс
4) мелкодисперстный мел (СаСО3)
5) верно1–4
4.Оптимальная скорость абразива с сохранением его эффективной абразивной способности равна:
1) 25–30 м/с
2) 45–60 м/с
3) 120 м/с
5. Полирование цельнометаллических мостовидных протезов производится с помощью:
1) полировочной пасты
2) шлифовальных эластичных кругов
3) щетинных и нитяных щеток
4) войлочных фильцев
5) все ответы верны
Ответы на вопросы к главе 7
1) обработка по удалению шероховатостей и неровностей с поверхности обрабатываемых стоматологических конструкций зубных протезов и аппаратов.
2)конечный процесс обработки, с целью получения гладкой, блестящей поверхности зубных протезов и аппаратов.
[A52] 3)верно 5
4)верно 1
5)верно 5
Дата добавления: 2021-04-15; просмотров: 192; Мы поможем в написании вашей работы! |
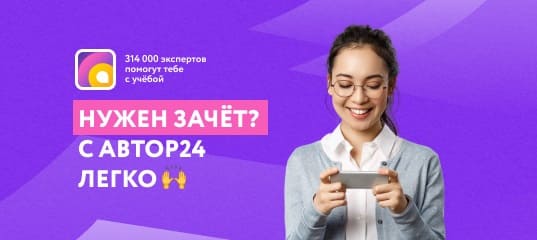
Мы поможем в написании ваших работ!