Оценка потерь при сносе зданий. 12 страница
Согласно технико-экономическим расчетам увеличение прочности бетона до 800—900 кг/см2 эффективно в конструкциях, воспринимающих большую нагрузку. Это позволяет снизить объем бетона на 30—35 % и в целом на 10— 15 % уменьшить приведенные затраты.
Поскольку для конструкций, не несущих большие нагрузки, размер сечения элементов зданий мало зависит от прочности бетона, дальнейшее наращивание прочности в этом случае экономически нецелесообразно.
Лучше всего снизить массу таких конструкций, применяя легкие бетоны на пористых заполнителях и ячеистые бетоны. Эти конструкции особенно эффективны в наружных стенах зданий.
В настоящее время в стране более 60 % крупнопанельных зданий возводится из однослойных легкобетонных панелей.
В качестве легких заполнителей применяются керамзитовый щебень, аглопорит, перлит, шлакобетон и некоторые другие. Особенно большое развитие получил керамзитобетон, который применяется не только для стеновых панелей, но и для покрытий и перекрытий, лестничных маршей и площадок и других изделий.
В общем объеме производства легких бетонов керамзитобетон занимает около 60 %.
В табл. 15.5 приведено сопоставление технико-экономических показателей конструкций наружных стен из легкобетонных панелей с показателями по трехслойным железобетонным панелям с утеплителем.
Как видно из табл. 15.5, все легкобетонные конструкции наружных стен значительно эффективнее аналогичных конструкций из слоистых бетонных панелей, поскольку последние обладают большей плотностью и требуют большего расхода металла. Применение же легких бетонов в конструкциях внутренних несущих стен, где не используются их теплозащитные свойства, экономически менее целесообразно. Однако легкие бетоны обеспечивают лучшую звукоизоляцию, и в этом случае применение конструкций из них оправдано.
|
|
Характерная тенденция совершенствования сборного железобетона — увеличение в его общем выпуске доли деталей и конструкций с предварительно напряженным армированием. Они отличаются высокой долговечностью и трещиностойкостью, меньшей массой и большей жесткостью, наиболее рациональным расходом металла. Предварительное напряжение арматуры дает возможность применять в железобетоне высокопрочную сталь, что, в свою очередь, на 30—35 % уменьшает ее расход и затраты на металл. Высокая жесткость предварительно напряженного железобетона (меньшие прогибы конструкций) позволяет использовать его в изделиях большей длины, а высокая трещиностойкость — в изготовлении труб и резервуаров.
Внедрение сборного железобетона позволило в кратчайшие сроки изменить организацию строительного производства, перевести его на индустриальные рельсы. Вместе с тем строительство из сборного железобетона имеет и ряд недостатков. На создание и освоение новых, а также на реконструкцию действующих предприятий этой отрасли требуются значительные капитальные вложения и время — до 3—5 лет и более, что не способствует оперативной реализации новых проектных решений, отражающих технический и социальный прогресс. Так, по данным Госгражданстроя СССР, изменение номенклатуры изделий, вызванное применением улучшенной планировки в проектах жилых домов, за последние годы потребовало капиталовложений на переоснащение предприятий сборных железобетонных изделий в размерах, равных потере действующих мощностей на 19—25 %. Такое же изменение проектных решений при выполнении их в традиционных материалах (кирпич, блоки и др.) либо в монолитном бетоне не вызвало бы необходимости в существенном преобразовании производственной базы этих материалов.
|
|
В общей сумме затрат на сборное строительство значительную долю составляет транспортировка сборных железобетонных конструкций от завода на строительную площадку. При этом требуются специальные транспортные средства, а следовательно, и затраты на их производство. Как правило, малоэффективно применение сборных конструкций взамен местных материалов в сельском строительстве, где возникают дополнительные сложности с доставкой монтажных механизмов и пр. При строительстве многоэтажных промзданий и промзданий с пространственными большепролетными покрытиями более эффективным оказывается применение конструкций из монолитного бетона, изготовленных на строительной площадке.
|
|
Следовательно, применение сборных железобетонных конструкций и расширение их производства экономически, безусловно, оправдано, когда строительство ведется в больших объемах и достаточно продолжительное время.
В связи с экономически целесообразным расширением использования других взаимозаменяемых конструкций, а также монолитного железобетона, расход сборного железобетона в некоторых конструктивных элементах зданий и сооружений в последующей перспективе (до 2000 г.) несколько снижается. Однако следует подчеркнуть, что и в перспективном периоде сборный железобетон останется основным конструктивным материалом и в целом масштабы его применения будут увеличиваться.
Монолитный железобетон. Перед строителями и проектировщиками стоят задачи повышения экономической эффективности капитальных вложений при одновременном улучшении качества строительства и достижении большей архитектурной выразительности массовой застройки. В этой связи все больший интерес вызывает проектирование жилых и общественных зданий из монолитного железобетона с применением инвентарной опалубки. Строительство из монолитного железобетона позволяет не только возводить здания, индивидуальные по внешнему облику и с разнообразными обьемно-планировочными решениями, но и вести массовое жилищное строительство в районах, где недостаточно развита или отсутствует база заводского домостроения, а также имеют место сложные условия транспортировки.
|
|
Под монолитным домостроением понимается такой вид строительства, в котором в качестве основного материала применяется монолитный бетон, формирование конструкций осуществляется в инвентарной или оборачиваемой опалубке, процессы приготовления, транспортирования и укладки бетонной смеси в основном механизированы.
В ряде случаев применение монолитного железобетона более экономично, чем сборного. Это относится в первую очередь к гидротехническому строительству, сооружениям элеваторов, резервуаров, а также уникальных общественных зданий, т. е. к объектам, требующим пластичности конструкций, которые при выполнении их в сборном железобетоне оказываются значительно более трудоемкими и часто не могут обеспечить требуемых эксплуатационных качеств. Кроме того, и многие несущие конструкции оказываются в монолитном варианте более экономичными. Так, затраты на монолитные фундаменты на 25—50 % ниже, чем на сборные. По сравнению со сборными конструкциями на монолитные расходуется металла на 5—15 %, и электроэнергии в 3—4 раза меньше.
Достоинствами монолитного домостроения по сравнению со сборным являются также: меньшие размеры удельных капитальных вложений в создание и развитие производственной базы строительства (на 50—55 %); снижение затрат на транспортировку товарного бетона для изготовления
конструкций почти вдвое против затрат на транспортировку сборных железобетонных изделий; обеспечение более низких эксплуатационных затрат в связи с отсутствием стыков и швов по фасадам.
Наиболее существенным недостатком монолитного домостроения по сравнению с полносборным является более высокая трудоемкость на строительной площадке. Построечная трудоемкость строительства из штучных материалов (кирпич, мелкие блоки, естественный камень) еще более высока.
Индустриализация строительства из монолитного бетона осуществляется путем широкого внедрения эффективных видов опалубки заводского изготовления. Применение унифицированной, многократно оборачиваемой и легкой, изготовленной из новых легких материалов и специальных профилей объемно-переставной опалубки значительно уменьшает трудозатраты на ее установку по сравнению с ранее применяемой неинвентарной опалубкой. Индустриализация монолитного домостроения обеспечивается также максимальной механизацией монтажных и демонтажных работ.
В жилищном строительстве эффективность монолитной застройки особенно выявляется в сейсмических условиях. Так, в расчете на 1 м2 общей площади в монолитных домах расход стали на 12—14 кг, а сметная стоимость на 7—10 руб. меньше, чем в домах из сборного железобетона.
Особое место среди методов монолитного домостроения занимает подъем этажей и перекрытий. Неразрезное исполнение перекрытий, величина которых соответствует размерам здания в плане, обладает достоинством монолитной конструкции, в то же время эти конструкции после их формования поднимаются на проектную отметку гидравлическими домкратами, которые устанавливаются на сборных колоннах, наращиваемых по мере подъема, или на монолитных ядрах жесткости, предназначенных для коммуникаций. Вертикальные наружные и внутренние ограждающие конструкции выполняются при этом из крупноразмерных или мелкоразмерных сборных элементов. Наибольшие объемы жилищного строительства с использованием метода подъема перекрытий выполняются в Ереване. Строительство общественных зданий методом подъема этажей ведется также в Ленинграде и других городах.
Разрабатываются и уже возводятся здания смешанных конструктивных схем с применением монолитных ядер жесткости в сочетании с облегченными элементами каркаса. Имеются проектные предложения использования в таких сочетаниях крупнопанельных конструкций, что позволяет освободить панели внутренних стен от горизонтальных воздействий, и, как следствие, значительно уменьшить их армирование и снизить марку бетона.
Такое сочетание сборно-монолитных конструкций дает возможность использовать преимущества как того, так и другого типа конструкций зданий. Особенно эффективны такие проектные решения для строительства жилых домов повышенной этажности.
Таким образом, монолитное домостроение может и должно обеспечивать выполнение массовых объемов строительства жилых зданий в районах с обычными и сейсмическими условиями, дополняя полносборное домостроение.
Минеральные вяжущие материалы. Повышение экономической эффективности применения в строительстве любого вида бетона, как сборного, так и монолитного, возможно при постоянном совершенствовании физико-механических свойств и определении оптимальных путей производства и применения минеральных вяжущих материалов. Основным типом такого материала в настоящее время является цемент.
Технический прогресс в строительстве требует неуклонного повышения марки цемента, что позволяет снижать расход строительных материалов на
потребительскую единицу конструкции, и улучшает монтажные и эксплуатационные качества бетонов. Однако выпуск цемента высоких марок требует и увеличения затрат топлива, электроэнергии, трудовых ресурсов, что несколько повышает себестоимость продукции. В то же время дополнительные производственные затраты (на единицу продукции) составляют в среднем лишь '/з экономии, получаемой при использовании высокомарочных цементов. Это происходит за счет снижения расхода вяжущего (на 1 м3 бетона), уменьшения затрат на доставку цемента и складирование, снижения эксплуатационных затрат в производстве железобетонных конструкций.
В связи с ростом применения высокопрочных бетонов и конструктивного асбестоцемента выгодно довести в перспективе выпуск цемента высоких марок до 14—15 % общего производства цемента с опережающим развитием цемента марки 600.
Широкое развитие предварительно напряженных тонкостенных железобетонных конструкций и повышение требований к быстроте распалубки бетона делают экономически целесообразным увеличение выпуска быстро-твердеющего цемента (БТЦ) и особо быстротвердеющего цемента.
Себестоимость БТЦ несколько превышает затраты на изготовление обычного цемента. Однако по сравнению с обычным портландцементом применение БТЦ для получения быстро-твердеющего бетона класса В25 сэкономит до 25—30 % цемента. Кроме того, это содействует ускорению технического процесса в производстве сборного железобетона и снижению удельных капитальных вложений, так как уменьшаются производственные площади, капитальные затраты на термообработку, парк форм и т. д. Заводская себестоимость железобетонных изделий при использовании БТЦ и особого БТЦ снижается на 4—6 %. В целом же достигается еще большее повышение эффективности, поскольку норма расхода вяжущего на 1 м3 железобетона, а значит, и величина транспортных расходов на перевозку вяжущего до потребителя также снижаются.
В ближайшей перспективе наряду с быстрым ростом выпуска обычного портландцемента, шлакопортландцемента высоких марок и увеличения производства БТЦ, экономически целесообразно также развитие производства специальных видов клинкерных вяжущих, в том числе белого и цветного цемента для облицовки фасадов крупнопанельных зданий.
Кроме вяжущих высоких марок строительству требуются и низкопрочные цементы и «местные вяжущие»— известь, гипс, смешанные вяжущие с использованием шлаков, зол и т. п. Их недостаток приводит к перерасходу цемента из-за неполного использования его активности. Нередко цемент марок 300—400 идет на изготовление конструкций, изделий и растворов, где со значительно большей эффективностью могли бы быть применены местные вяжущие марки 150—200, себестоимость которых на 30—40 % ниже, а удельные капитальные вложения в 2—2,5 раза меньше, чем у портландцемента.
Конструкции из бетонов на местных вяжущих. Программа жилищного строительства, намеченная Основными направлениями экономического и социального развития СССР на 1986— 1990 годы и на период до 2000 года, требует выпуска строительных материалов не только в большом количестве, но совершенно новых видов и высокого качества, обеспечивающих экономию материальных ресурсов и повышение эффективности капитальных вложений. В этой связи особенно большое значение приобретает развитие производства материалов и изделий из местного сырья, в частности известково-песчаных изделий автоклавного твердения, называемых силикатобетонными изделиями.
Силикатные бетоны не содержат в своем составе крупного заполнителя —
гравия или щебня, что дает возможность значительно расширить базу для производства индустриальных конструкций. В качестве исходного вяжущего для их изготовления вместо клинкерного цемента применяется известь, организация производства которой требует капитальных вложений на 30— 40 % меньше, а в качестве заполнителей применяются строительный песок, шлак, зола.
Изделиям из известково-песчаных бетонов дает преимущество также автоклавный способ паро-тепловой обработки, в результате которого осуществляется активизация инертных заполнителей и становится возможным превращать инертные вещества в активные вяжущие. При автоклавном способе обработки изделий расход извести на 1 м! силикатного бетона в 1,5—2 раза меньше, чем расход цемента на изготовление цементно-бетонных изделий равной прочности в пропарочных камерах.
Кроме непосредственного снижения себестоимости строительных конструкций (до 20 %) в связи с меньшим расходом и меньшей стоимостью материалов на единицу продукции, значительно уменьшаются удельные капитальные вложения на создание сырьевой базы для заводов сборного домостроения по сравнению с соответствующими затратами для заводов цементно-бетонных изделий.
Исследования и производственный опыт показали возможность изготовления силикатных бетонов плотной и ячеистой структуры с плотностью 300—2200 кг/м3 при прочности 200— 600 кг/см2.
Плотный силикатный бетон является разновидностью тяжелого бетона и может быть использован как в армированных, так и неармированных изделиях и элементах конструкций.
Армированные элементы из силикатного бетона работают аналогично обычным железобетонным конструкциям. При этом несущая способность изгибаемых элементов из силикатного и цементного бетона одинакова. Жесткость при кратковременном воздействии нагрузки у первых меньше, а при длительном действии нагрузки несколько больше, чем у вторых. Водостойкость и морозостойкость армированных конструкций из плотного силикатного бетона практически не отличаются от показателей железобетонных конструкций.
Ячеистый силикатный бетон автоклавного твердения представляет собой искусственный камень с мелкопористой (ячеистой) структурой, плотностью 300—1000 кг/м3 и с малым коэффициентом теплопроводности.
Автоклавные ячеистые силикатные бетоны делятся на конструктивные плотностью 600—1000 кг/м и теплоизоляционные плотностью 300— 500 кг/м3. Ячеистый силикатный бетон, пористая (ячеистая) структура которого образуется при помощи пены, называется пеносиликатом; ячеистый бетон, пористая структура которого образуется при помощи газообразователя, называется газосиликатом. На практике чаще всего применяются газосиликаты.
В настоящее время выпускаются такие виды индустриальных материалов и конструкций, как пено- и газосиликатные блоки и панели наружных и внутренних стен, плиты для утепления чердачных перекрытий и кровель, армосиликатные панели внутренних стен, перегородок и перекрытий, лестничные марши и площадки, перемычки и прочие детали.
Силикатный бетон с применением в качестве заполнителя крошки щебня, белых и цветных мраморов и других каменных пород может быть использован также в качестве декоративного.
По цвету, фактуре и показателям основных физико-механических свойств такой бетон аналогичен цветному бетону и может с успехом заменить последний.
Экономическая эффективность декоративного силикатного бетона определяется тем, что в нем известь и молотый песок полноценно заменяют
не обычный цемент, а значительно более дорогой и дефицитный белый цемент.
В 70-х гг. на базе силикатобетона строились в основном 4—5-этажные жилые дома, а также школы, детские сады и другие общественные здания массового типа. В настоящее время разработаны проекты и возводятся жилые дома до 9 этажей, а также осуществлен ряд экспериментальных проектов большей этажности, в частности, 16-этажный дом в Черкизове Москва (проект 20-й мастерской Моспроекта).
Однако в Советском Союзе при огромной территории и многообразии местных сырьевых ресурсов не может быть «всеобъемлющих» материалов, самых выгодных во всех условиях, а есть материалы, выгодные при определенных сырьевых и других местных условиях. Это относится и к силикатным бетонам.
Кирпич. В ряду стеновых материалов важнейшее место до настоящего времени занимает и в ближайшие годы будет занимать кирпич. Этот традиционный стеновой материал обладает рядом положительных качеств — большой прочностью на сжатие (до 300 кг/см2), высокой морозо-, водо-, термо- и кислотостойкостью, которые обеспечивают долговечность стеновых конструкций и сравнительно низкий уровень затрат по эксплуатации зданий и сооружений. Сырье для производства кирпича распространено повсеместно, добыча и переработка его технологически не сложна, а затраты на эти цели относительно невелики. Однако этот стеновой материал имеет и ряд недостатков, которые не позволяют считать кирпич (в том виде, как он до последних лет производился) прогрессивным стеновым материалом. Малая размерность кирпича определяет повышенную трудоемкость построечных работ и увеличение их сроков, большая плотность (до 1,9 т/м3) и высокая теплопроводность создают необходимость значительного расхода кирпича на возведение конструкций. Поэтому основным направлением повышения эффективности кирпича и придания ему качеств, соответствующих требованиям технического прогресса, является перевод существующих кирпичных заводов на выпуск конструктивно-лицевой керамики, имеющей размеры, кратные 2,1 стандартного кирпича, с пустотностью 25 %. Стена, выложенная из таких камней, почти на 30 % легче и на 20 % дешевле стен из полнотелого кирпича. Кроме того, на 25 % снижаются суммарные трудовые затраты и вдвое сокращается расход цемента на кладочный раствор.
Дата добавления: 2021-07-19; просмотров: 86; Мы поможем в написании вашей работы! |
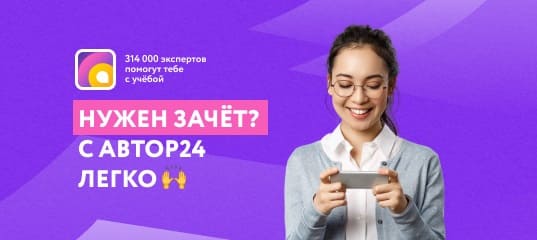
Мы поможем в написании ваших работ!