Применение электрохимической обработки материалов в машиностроении.
Электрохимическими способами обработки материалов условно принято называть группу новых методов электротехнологии, которые применяются для удаления материала с обрабатываемых поверхностей, его переноса, формообразования деталей или структурных преобразований, осуществляемых с помощью электрической энергии, вводимой непосредственно в зону обработки.
В большинстве новых методов используется преимущественно процесс анодного растворения, т. е. перехода металла, помещаемого в электролизер в качестве анода, из металлического состояния в различные неметаллические соединения. При этом вначале металл анода переходит из металлического состояния в ионное путем отдачи металлом электронов:
Мe0+nе→Меn+,
где n - число единичных зарядов.
Затем происходит образование различных металлических соединений, состав которых определяется химическим составом электролита или продуктов электролиза. В растворах кислот
Men++nR-→Me(R)n,
где R - кислотный остаток (анион), например С1-, SO42- и т. д.
При растворении железа в соляной кислоте
Fe2++2Cl-→FeCl2
В нейтральных и щелочных растворах
Меn++nОН-→ Ме (ОН)n .
Например,
Fe2++2OH-→Fe(OH)2
Анодное растворение в нейтральных электролитах сопровождается образованием гидратов оксида металла Ме(ОН)n, которые практически не растворяются в электролите, выпадают в осадок, пассивируют растворяемую поверхность и забивают межэлектродный промежуток. Для удаления из зоны обработки выпавшего осадка электролиту придается большая скорость движения в межэлектродном промежутке, что позволяет выполнять обработку при повышенных плотностях тока (до сотен ампер на квадратный сантиметр), поскольку при этом происходит интенсивное охлаждение электролита.
|
|
При электрохимической обработке металлов в кислых растворах, когда продукты реакции достаточно хорошо растворимы в электролите, плотности тока относительно невелики (2…3 А/см2) и обработка производится в стационарном либо медленно перемешиваемом электролите.
По этим признакам операции электрохимической обработки подразделяют на две группы:
- электрохимическая обработка при невысокой плотности тока в стационарном электролите;
- электрохимическая обработка при высокой плотности тока в протечном электролите.
На рис. 9.3 показана схема электрохимической обработки в стационарном электролите для наиболее типичной операции - электролитического шлифования или полирования.
При прохождении электрического тока через электролит 3 и электроды 8 и 5 происходит растворение поверхности анода в электролите и образование продуктов растворения 6. Они задерживаются в углублениях поверхности анода и изолируют ее от прохождения тока по всей поверхности, сосредоточивая силовые линии тока 7 на незащищенных участках поверхности анода. Выступы растворяются быстрее впадин, в результате чего происходит сглаживание поверхности изделия - ее полирование.
|
|
Рис. 9.3. Схема электрохимической обработки в стационарном электролите:
1-источник питания; 2-регулятор тока; 3-электролит; 4-ванна; 5-обрабатываемое изделие; 6-продукты растворения; 7-линии тока; 8-электрод.
Принципиальная схема процесса электрохимической обработки в проточном электролите (рис. 9.4) работает следующим образом. Обрабатываемую деталь 1 устанавливают относительно электрода-инструмента 2 с зазором, через который прокачивается электролит. Деталь подключена к положительному полюсу и является анодом, а электрод-инструмент - катодом.
![]() |
При прохождении электрического тока по цепи электрод - инструмент - электролит - анод последний под действием происходящих электрохимических процессов растворяется, при этом на нем осуществляется копирование формы электрода-инструмента.
|
|
Электрохимическим способом могут проводиться следующие операции:
- очистка поверхности металла анодным травлением от оксида ржавчины, жировых пленок и других загрязнений. Ее производят путем анодного растворения поверхности изделия.
- заострение и затачивание режущего инструмента, изготовление игл из цилиндрических прутков. Это выполняется за счет создания на режущем лезвии и острие повышенных плотностей тока.
- профилирование металлических заготовок. При этом способе обрабатываемое изделие помещено внутрь катода. Анодное растворение происходит интенсивнее в участках, более близких к катоду.
- гравирование и маркирование по металлам. На изделие, которое является анодом, наносят слой воска, лака или другого изолирующего вещества. Анодное растворение происходит в тех местах, где металл обнажен.
- изготовление сеток (аналогично электрохимическому гравированию). Сетку-рисунок наносят изолирующим составом на поверхность анода. Она предохраняет металл от растворения. Обнаженные участки внутри лаковой сетки растворяются.
- изготовление листового металла малой толщины путем анодного растворения.
9.10. Нанесение металлопокрытий и анодирование. Процесс нанесения металлопокрытий на поверхность изделий методом электролиза называется гальванотехникой. В свою очередь, гальванотехника подразделяется на гальваностегию и гальванопластику.
|
|
Гальваностегия — электрохимическое нанесение металлов на металлические изделия с целью повышения их механической прочности, антикоррозионных свойств и декоративных качеств.
Гальванопластика — электрохимический процесс нанесения металлов на шаблоны, применяемые при изготовлении штампов различных изделий (музыкальные пластинки-диски, типографские клише, статуи и т. д.). При нанесении металлов шаблоны (из воска, гипса, дерева и т. п.) предварительно покрывают слоем графита для придания их поверхностям электропроводности.
Анодирование - процесс получения оксидных антикоррозионных покрытий на поверхности металлических изделий путем их анодной обработки в соответствующих растворах. Оно широко применяется для защиты от коррозии изделий из алюминия, магния и их сплавов. При анодировании на поверхности алюминия образуется двойной оксидный слой: верхний - толстый пористый слой и нижний - тонкий плотный. Алюминиевая оксидная пленка обладает хорошими антикоррозионными и электроизолирующими свойствами.
Для обеспечения достаточной прочности сцепления металлопокрытия с основным металлом поверхность последнего подвергается специальной очистке различными методами: механическим (шлифование, полирование), электрохимическим (обезжиривание, травление), а также ультразвуковой обработке.
Ванны для металлопокрытий изготовляют из стали и изнутри футеруют пластмассами. По бортам ванн на изоляторах монтируют анодные и катодные шины, присоединяемые к источнику питания постоянного тока. На катодные шины подвешивают изделия, на анодные - пластины металла, которым покрывается изделие. Находящийся в ванне электролит подогревается установленным на дне ванны змеевиком, по которому циркулирует горячая вода. Иногда ванны изготовляются с двойной стенкой - паропроводящей рубашкой.
Ванны могут быть включены в цепь последовательно, если для процесса электролиза требуется одинаковый ток. В этом случае контроль за работой ванн осуществляется с помощью одного амперметра. Если же ванны работают с переменной нагрузкой, то каждая из них подключается к источнику питания параллельно и каждая снабжается амперметром.
Дата добавления: 2021-07-19; просмотров: 124; Мы поможем в написании вашей работы! |
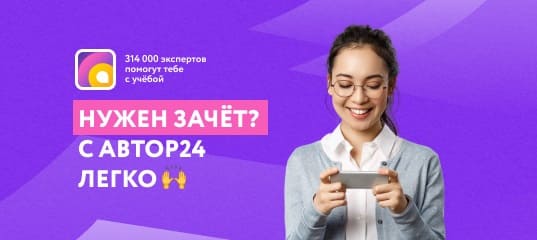
Мы поможем в написании ваших работ!