Основы технологии светолучевой обработки
Технологические генераторы когерентного светового излучения (в основном газовые и твердотельные) имеют мощность непрерывного излучения до нескольких сотен киловатт и энергию отдельного импульса до нескольких сотен джоулей.
Технологические преимущества светолучевой обработки:
1) возможность передачи энергии в виде светового луча на расстоянии в любой оптически прозрачной среде;
2) отсутствие механического и электрического контакта между источником энергии с изделием в месте обработки;
3) наличие высокой концентрации энергии в пятне нагрева;
4) возможность плавной регулировки плотности лучистого потока в пятне нагрева изменением фокусировки луча;
5) возможность получения как импульсов энергии весьма малой длительности (до 10-9 с), так и непрерывного излучения перемещением луча с высокой точностью и скоростью с помощью систем развертки при неподвижном объекте обработки.
Особенностью лазерной обработки является интенсивный локальный разогрев обрабатываемого материала. Интенсивность нагрева определяется глубиной проникновения излучения в материал δ и толщиной прогретого путем теплоправодимости слоя , где а - температуропроводность материала; τ - длительность воздействия лазерного излучения.
В зависимости от назначения в состав лазерной технологической установки кроме лазера могут входить оптико-механический блок устройство управления лазерным излучением, устройство измерения и стабилизации параметров излучения, блок охлаждения, устройство автоматики, сигнализации и т.д. (рис. 9.13).
|
|
![]() |
Мощные лазеры применяются в технологических процессах обработки различных материалов. В частности, с их помощью производят сварку, закалку, резку и сверление различных материалов без возникновения в них механических напряжений и с очень большой точностью, вплоть до нескольких длин световых волн. Лазерами обрабатывают материалы практически любой твердости, металлы, алмазы, рубины и т.д.
Тема 9 Электрохимические технологии
9.1. Основы электрохимической обработки. Электрохимия изучает поведение ионов в растворах и явления на границе между твердым телом и раствором. Она основана на применении электролитов.
Электролитами называются вещества, растворы и расплавы которых могут проводить электрический ток ионами, образующимися в результате электролитической диссоциации. В отличие от металлов и полупроводников растворы и расплавы электролитов обладают ионной проводимостью.
|
|
Согласно теории электролитической диссоциации молекулы некоторых веществ — солей, щелочей, оснований и др. - являются полярными, т. е. состоящими из двух ионов, обладающих противоположными и равными по значению зарядами. Силы притяжения между ними обеспечивают целостность молекулы. Если такие молекулы находятся между молекулами растворителя (воды), то связи между ионами значительно ослабевают. В этих условиях столкновение между молекулами при их тепловом движении приводит к распаду молекул на ионы, т. е. к их диссоциации. Следовательно, электролитической диссоциацией называется процесс распада вещества на разноименно заряженные ионы при его растворении или расплавлении. Число положительных и отрицательных ионов, возникающих в процессе электролитической диссоциации, одинаково. Положительные ионы представляют собой атомы или молекулы, потерявшие один или несколько электронов, отрицательные ионы — атомы или молекулы, имеющие один или несколько лишних электронов.
|
|
Так, при растворении поваренной соли в воде ее молекула распадается на два иона - натрий Nа+ и хлор Сl-. Иногда ионами являются не отдельные атомы, а группы атомов, несущие заряд. Например, при растворении в воде сернокислого цинка образуется два иона - положительный Zn2+ и отрицательныйSO42-.
Часть молекул растворителя также может диссоциировать.
В электролитах наряду с процессом диссоциации протекает обратный процесс воссоединения ионов в отдельные молекулы - м oлизация. В результате одновременного протекания этих двух процессов в растворе устанавливается подвижное равновесие между числом вновь образующихся ионов и числом ионов, воссоединяющихся в молекулы.
Если электрод поместить в раствор, то в системе электрод - электролит устанавливается равновесное состояние, при котором через границу металл - раствор внешний ток отсутствует, поскольку электрод не включен во внешнюю электрическую цепь.
В системе электрод-электролит и в металле, и в электролите находятся одни и те же ионы. В металле они размещаются в узлах кристаллических решеток, а в электролите связаны с молекулами растворителя. Для перехода иона из узла кристаллической решетки в электролит необходимо затратить энергию, которая называется работой выхода иона из металла. Для выхода же иона из электролита в металл необходимо затратить работу, равную энергии гидратации.
|
|
На поверхности электрода, помещенного в электролит, протекает обратимая электрохимическая реакция
Ме ↔ Меn++ne, (9.1.)
где n - валентность металла; Меn+ - ион в растворе.
В общем случае энергия иона Меn+ в растворе и энергия атома Ме в кристаллической решетке не равны. Так как через границу раствор - металл переходят заряженные частицы, то неравенство указанных энергий определит наличие равновесного электрического потенциала φр металла относительно раствора.
Так как энергия связи ионов в кристаллической решетке металла больше энергии гидратации, то в первый момент ионы металла будут переходить из раствора в кристаллическую решетку. Избыточные электроны из внутренних слоев металла приблизятся к его граничной поверхности, а положительные ионы из глубины раствора переместятся к той же граничной поверхности и создадут двойной электрический слой.
В условиях равновесия скорость прямой и обратной реакций по схеме (9.1) одинакова, т. е. соответственно скорость окисления атомов Ме и восстановления ионов Меn+ (осаждения).
9.2. Прохождение электрического тока через электролит. В электролитах ионы, как и молекулы, движутся хаотически. Если же к опущенным в электролит электродам приложить электрическое поле, то кроме хаотического теплового движения возникает направленное движение ионов. Положительные ионы (катионы) направляются к катоду, а отрицательные (анионы) — аноду. Дойдя до соответствующих электродов, ионы отдают им свои заряды и, став обычными атомами или молекулами, выделяются на электродах или вступают в химические реакции с материалом электрода.
Итак, электрический ток в электролитах представляет собой направленное движение ионов в электрическом поле. В отличие от металлов и полупроводников прохождение электрического тока через электролит сопровождается переносом массы вещества.
Количество вещества g, выделившееся на электроде при прохождении электрического тока через раствор электролита, определяется законом Фарадея
g = α I τ (9.2.)
где α - электрохимический эквивалент, г/Кл; I - ток, А; τ - время прохождения тока, с.
Электрохимический эквивалент α - количество вещества, выделившееся из электролита при прохождении одного кулона электричества. Численно он равен отношению химического эквивалента вещества к числу Фарадея. Число Фарадея Fф - количество электричества, требующееся для выделения одного грамм-эквивалента вещества [ Fф=96485 Кл/(г·экв)].
Процессы в электролитах подчиняются законуОма. Для доказательства этого рассмотрим движение ионов в электролите под действием электрического поля.
Ион, движущийся под действием поля в электролите, непрерывно испытывает тормозящее действие со стороны молекул жидкости. При этом он увеличивает хаотическое движение молекул, передавая им полученную в электрическом поле энергию, что проявляется в нагревании электролита.
Так как у иона нет «длины свободного пробега», то среда действует на него в течение всего времени его движения. Действующая на ион сила сопротивления (сила вязкого трения) пропорциональна первой степени скорости упорядоченного движения Fт= kv (k - коэффициент трения). По направлению движения электрона действует электрическая сила Fэ=еЕ, где е - заряд иона.
Если в первый момент скорость иона v мала, то сила Fэ увеличивает ее, причем возрастает и сила трения. Эти силы выравниваются в течение всего времени движения иона.
Среднюю скорость упорядоченного движения определим из соотношения Fт= Fэ, т.е. еЕ= kv, отсюда
v= e· E/ k= μ· E. (9.3.)
Здесь μ=e/k - подвижность иона. Плотность тока, проходящего через электролит,
J= e· n· v= e· n· μ· E (9.4.)
Учитывая плотность токов положительных и отрицательных ионов, получим
J= e·( n+· μ++ n-· μ-) (9.5.)
где n+, n-, μ+, μ- - концентрации и подвижности положительных и отрицательных ионов соответственно.
Так как в электролите плотность тока J пропорциональна напряженности электрического поля, то вступает в силу закон Ома.
Проводимость электролита σ= e·( n+· μ++ n-· μ-) увеличивается с ростом концентрации ионов и их подвижности.
С увеличением температуры проводимость электролитов растет, что объясняется увеличением подвижности (уменьшением вязкости жидкости) и возрастанием степени диссоциации.
9.3. Электролиз растворов и расплавов. Явление выделения вещества на электродах при прохождении через электролит тока, а также процессы окисления или восстановления на электродах, сопровождающиеся приобретением или потерей частицами вещества электронов, называются электролизом.
В промышленности электролиз применяется в основном для анодного растворения металла и его катодного осаждения из растворов и расплавов.
Вещества, у которых нормальный потенциал больше -1 по отношению к потенциалу нормального водородного электрода, получают путем электролиза растворов (медь, цинк). Металлы с нормальным потенциалом меньше -1 получить таким способом не удается. Поэтому при их производстве применяют электролиз расплавов солей этих металлов (литий, калий, алюминий, магний).
Если в электролизной ванне процесс происходит с поглощением электрической энергии, ванна называется электролизером. Принципиальная схема электролизера показана на рис. 9.1.
На аноде переход металла из металлического состояния (Ме0) в ионное происходит в результате отдачи металлов электронов Ме0—ne→Men+ (анодное растворение), где n — число единичных зарядов. На катоде ион приобретает электроны и переходит в металлическое состояние Меn++ne→Me0 (катодное осаждение).
![]() |
Напряжение на электролизной ванне можно представить состоящим из трех составляющих: напряжение электрохимического разложения вещества, приэлектродные падения потенциала и падение напряжения в электролите:
U= U1+ Ua+ Uк= I/ l· σ (9.6.)
где: U1 — напряжение электрохимического разложения вещества;
Ua, Uk — анодное и катодное падения потенциала соответственно;
I - сила тока в ванне; l - расстояние между электродами; σ - проводимость электролита.
Мощность, выделяющаяся в электролизной ванне,
Pэ=I(U1+Ua+Uк+I·l/σ) (6.7.)
Только часть этой мощности (I· U1) идет на электрохимическое разложение вещества, остальная же мощность расходуется на нагрев электролита и транспортировку ионов через раствор.
Отношение количества вещества, полученного при электролизе, к теоретически возможному количеству вещества, определенному по закону Фарадея, называют выходом вещества по току Ai (%):
Ai=( q1/ q2)·100, (9.8.)
где q1 - фактически выделившееся количество вещества; q2 - количество вещества, которое должно было выделиться по закону Фарадея при отсутствии электрических потерь. Выход по току указывает, насколько экономично и рационально идет процесс электролиза.
Эффективность электролизного процесса также оценивается величиной, называемой выходом по энергии:
Aэ=( α· A1/ U)·100, (9.9.)
где α - электрохимический эквивалент вещества; A1 - выход металла по току; U - напряжение на электролизной ванне.
Таким образом, выходом металла по энергии следует считать количество металла в граммах, выделенное на 1 Дж затраченной энергии (г/Дж).
Характерной величиной, определяющей интенсивность электролиза, является электродная плотность тока (А/м2):
Jэ= I/ S, (9.10.)
где I - сила тока; S - поверхность погруженной в электролит части электрода.
Образующийся около поверхности электрода двойной электрический слой препятствует подходу к электроду иона, а также выходу иона с электрода. Для его разрушения применяют циркуляцию электролита, питание электролизной ванны импульсным напряжением, а также вибрацию электродов.
Циркуляция электролита помимо разрушения приэлектродных зон преследует цель выравнивания температуры электролита по ванне. При питании электролизной ванны импульсным напряжением нейтрализуется объемный заряд.
При проведении промышленных процессов электролиза не удается достичь теоретических значений выделения веществ на электродах. Такое явление обусловлено следующими основными причинами: перезарядкой ионов; наличием в электролитах ионов разной валентности; взаимным разрядом ионов; взаимодействием продуктов электродных реакций между собой или с электролитом, а также катодным восстановлением продуктов.
9.4. Электролиз меди. Целью электролиза меди является снижение содержания примесей в черновой меди, полученной плавкой в отражательных печах, извлечение находящихся в ней благородных и других ценных металлов и получение чистой электролитической меди.
Процесс ведут в электролизных ваннах ящичного типа. В ванне устанавливаются литые аноды черновой меди, между которыми подвешиваются тонкие пластины чистой меди (катоды). После этого в ванну подают электролит, который представляет собой водный раствор медного купороса, подкисленный серной кислотой для уменьшения сопротивления.
Отлитые из черновой меди аноды представляют собой плиты прямоугольной формы толщиной 35-45 мм и массой около 300 кг. Катоды изготовляют из листовой электролитической меди толщиной 0,6-0,7 мм. Катоды имеют ушки для надевания на штанги при подвешивании в ванны, расстояние между поверхностями соседних анодов и катодов составляет 35-40 мм.
При пропускании через ванну постоянного электрического тока происходит растворение черновой меди анодов и осаждение чистой меди на катодах. Благородные металлы и некоторые примеси в виде шлама выпадают в осадок, некоторые другие примеси (никель) переходят в раствор.
В электролизере при этом происходят следующие электрохимические процессы:
на аноде Cu—2e→Cu2+
на катоде Cu2++2e→Cu
в растворе CuSO4↔Cu2++SO42-;
H2O↔H++OH-
H2SO4↔2H++SO42-
Процесс электролиза начинается при напряжении на ванне 0,3-0,35 В. Плотность тока ограничивается условием получения мелкозернистого, плотного и гладкого осадка катодной меди. В зависимости от состава черновой меди плотность тока колеблется в пределах 180—270 А/м2. Фактический выход по току составляет 92—98%. Удельный расход электроэнергии составляет 200— 379 кВт·ч/т чистовой меди.
Катоды и аноды в ваннах включают параллельно, а ванны последовательно (система мультипль). Последовательное включение электродов в ванне (система серий) применяется крайне редко. В процессе электролиза изменяется концентрация ионов в электролите в различных частях ванны, что может привести к увеличению расхода электроэнергии. В целях выравнивания концентрации ионов меди у электродов и обеспечения необходимой температуры применяется прямая циркуляция электролита, при которой он подается снизу ванны и сливается сверху.
Температура электролита поддерживается на уровне 333±3 оК. Необходимый подогрев электролита осуществляется с помощью теплообменников из графита, титана или нержавеющей стали.
При проведении электролиза в электролизных ваннах стремятся к максимальному выходу меди по току, снижению удельного расхода электроэнергии и увеличению их производительности.
Снижение выхода металла по току является следствием утечки тока, появлению которой способствуют неблагоприятные условия в электролизных цехах: повышенные кислотные испарения; сырость деревянных частей ванны; отложение солей на деталях ванн; сравнительно высокий потенциал ванн относительно земли.
Путями утечки тока на электролизных установках могут быть:
- циркуляционные магистрали электролита;
- магистрали воды и пара;
- изоляция ванн от земли;
- изоляция между ваннами;
- проводящая футеровка ванн;
- короткие замыкания между электродами.
9.5. Электролиз цинка. Высококачественный цинк получают путем электролиза водных растворов его солей. В ваннах устанавливаются алюминиевые катоды и свинцовые аноды. Затем они заполняются водным раствором сернокислого цинка ZnSO4 (5—6%), который диссоциирует на катионы цинка Zn2+ и анионы SO42- и серной кислоты H2SO4 диссоциирующей на катионы водорода Н+ и анионы SO42+.
Во время электролиза на катоде осаждается металлический цинк, на аноде выделяется газообразный кислород, а в растворе образуется серная кислота H2SO4.
При этом в электролизере происходят следующие процессы:
- на катоде Zn2++2e→Zn;
- на аноде H2O—2e→2H++0,5O;
- в ванне ZnSO4+H2O↔H2SO4+0,5O2
Чтобы обеспечить осаждение цинка на катоде, электролиз ведут при повышенных плотностях тока (400…600А/м2)и добавляют в раствор поверхностно-активные вещества, которые препятствуют выделению водорода на катоде.
В электролизных цехах применяют ванны из сборного железобетона (иногда стальные) с защитой из кислотоупорных материалов. Обортовку ванн и сливные короба выполняют из винипласта. Снаружи ванны покрывают кислотоупорной краской, битумом или резиной (по стали). В дне ванн имеется отверстие для выпуска шлама. Ванны длинными бортами устанавливают рядом, соединяют в блоки по 20-30 ванн.
Для получения высокого выхода по току температуру электролита необходимо поддерживать на уровне 308…313 оК. На практике применяется индивидуальное для каждой ванны охлаждение электролита с помощью алюминиевых или углеродистых змеевиков.
В производстве цинка выход по току составляет обычно 88-94%, расход электроэнергии 3500 кВт-ч на 1 тонну цинка.
Сопротивление электролита определяется его температурой и концентрацией цинка в растворе. Резкое повышение падения напряжения на ванне (до 3,3…3,6 В) указывает на необходимость очистки анодов от шлама.
Аноды изготовляют из свинца с добавкой 1% серебра для снижения коррозии. Толщина анодных пластин 5-8 мм. Катоды изготовляют из листового алюминия толщиной 4 мм.
Сдирку цинка с алюминиевых катодов производят раз в сутки или двое суток. Они подвергаются систематической очистке один раз в 10 дней на катодоочистительной машине. Аноды очищают один раз в 20-25 дней. Износ катодов составляет около 1,5 кг, а анодов - 0,8-1,5 кг на 1 т цинка.
Полученные пластины катодного цинка промывают водой, формуют в пакеты и затем переплавляют в индукционных канальных печах.
9.6. Электролиз алюминия. При нормальном потенциале выделения металла меньше -1 В осадить его на катоде методом электролиза раствора невозможно, так как на катоде будут выделяться в основном водород и содержащиеся в электролите и аноде примеси. Так как нормальный потенциал алюминия -1,67 В, то его получают путем электролиза расплавленных солей. В этом случае электролитом является раствор оксида алюминия Аl2О3 в расплавленном криолите (Na3AlF6).
Поскольку фторидные расплавы являются сильно агрессивными средами, электролиз алюминия ведут с расходуемым угольным электродом, а внутренние поверхности ванн футеруют угольными плитами и блоками.
Электролизеры для получения алюминия можно классифицировать по ряду признаков:
- мощности (силе тока): 40-50 кА - малой мощности; 60-80 кА - средней мощности; 100-160 кА - большой мощности; 200-250 кА- сверхбольшой мощности.
- способу подвода тока: боковой - электролизеры малой и средней мощности; верхний - электролизеры большой мощности.
- конструкции анода: самоспекающийся за счет теплоты ванны и обожженный. Обожженные аноды имеют только верхний подвод тока. Самоспекающиеся аноды устанавливают по одному на каждой ванне.
Принципиальное устройство электролизной ванны для получения алюминия показано на рис. 9.2.
Рис. 9.2. Устройство электролизной ванны для получения алюминия:
1 - цоколь; 2 - подина; 3 - стойка; 4 - домкрат; 5 - глинозем; 6 - алюминий; 7 - газосборочный колокол; 8 - ребра жесткости; 9 - рама; 10 - спеченный анод; 11 - анодные шины; 12 - стальные штыри; 13, 14 - электродвигатели; 15 - колодки; 16 - жидкая анодная масса; 17 - кожух анода; 18 - горелка; 19 - патрубок; 20 - корка электролита; 21 - уровень пола; 22 - электролит; 23 - шины.
Ванны имеют прямоугольную форму. Корпус электролизера сварен из стальных листов, может быть с днищем и без днища. Корпус ванны снизу частично заполнен шамотной кладкой для теплоизоляции. На ней устанавливают подовые катодные блоки, к которым крепят специальные токопроводы - блюмсы. Боковые стороны покрывают асбестовым листом, теплоизолируют глиноземовой засыпкой и футеруют угольными плитами. Все швы в угольной кладке заполняют углеродистой массой. С целью ослабления действия магнитных полей на расплавленный алюминий применяется двусторонняя подводка тока.
Размеры анода определяются заданной мощностью ванны и допустимой плотностью тока, которая для ванн средней мощности составляет 0,8…0,95 А/см2, а на мощных ваннах снижается до 0,65…0,7 А/см2. Обожженные аноды работают при плотностях тока 0,75…1,0 А/см2.
Основным достоинством самоспекающихся электродов является экономия затрат на прессование и обжиг электродов. К их недостаткам следует отнести выделение вредных газов в цехе электролиза с каждой ванны, высокое сопротивление, выкрашивание, вследствие чего возникает необходимость снимать с электролита угольную крошку - пену.
Анод подвешивают на подвижной раме, которая перемещается по металлоконструкциям печи. Автоматическое перемещение анода осуществляется в функции потери напряжения в электролите.
Ток к ванне подводится с двух сторон по пакетам алюминиевых шин. От шин к штырям ток подводится по гибким медным токоподводам, а непосредственно в массу анода ток вводится с помощью стальных штырей. В случае верхней подводки тока к аноду штырь и шина соединяются колодкой с пружинным зажимом.
Электролизеры объединяют в серию из 160…170 шт., причем 4-5 из них резервные. Ванны серии обычно устанавливают в двух корпусах в два ряда в каждом. Полы электролизного цеха выполняют электроизолированными.
При электролизе расплавов ток через ванну достигает значений более 100 кА, поэтому ванны включают в серии последовательно без предварительного объединения в блоки. Соединение отдельных ванн или блоков между собой в серии, а также подключение их к источникам питания производится шинопроводами.
При нормальной работе напряжение на ванне составляет 4,2…4,5 В, что достигается поддержанием заданного состава электролита и режимных показателей.
При недостатке глинозема (0,5…1,5%) начинает проявляться анодный эффект. Напряжение на ванне сначала постепенно, а потом резко возрастает до 50…60 В. Эффект сопровождается ярким свечением, обильным выделением газа и паров, перегревом электролита, что влечет за собой потерю фтористых солей и перерасход электроэнергии. Эффект ликвидируют добавкой глинозема в электролит.
Выливку металла из ванны производят с помощью вакуумковша. Вылитый из ванн алюминий поступает в миксеры литейного корпуса, где он после усреднения и отстаивания разливается в слитки.
Производство алюминия является энергоемким. Фактический расход электроэнергии на производство алюминия составляет 14000-16000 кВтּч/т. Выход металла на 1 кВт·ч составляет 60…77 г, что типично для удельного расхода электроэнергии 16000 кВт·ч на 1 т алюминия.
Дата добавления: 2021-07-19; просмотров: 169; Мы поможем в написании вашей работы! |
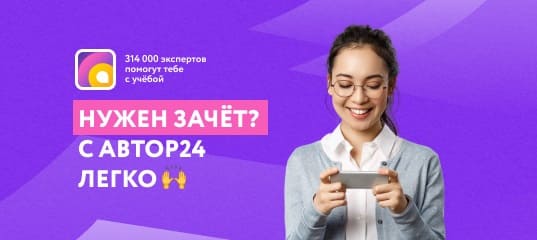
Мы поможем в написании ваших работ!