Установки плазменной резки и сварки металлов
Плазменная резка (рис. 9.4) осуществляется путем выплавления и испарения металла в полости реза за счет энергии, выделяющейся в опорном пятне дуги и вносимой струей плазмы.
![]() |
КПД плазменной резки возрастает с повышением мощности дуги и скорости движения плазмотрона, достигая 80-90%.
Установки плазменной резки разных типов работают на токах до 400-1000 А при напряжении холостого хода до 180-350 В, обеспечивая скорость резки от 3-4 до 10 м/мин.
Плазменную сварку металлов проводят по схеме, приведенной на рис. 9.5.
![]() |
Высокая мощность плазмотрона и динамическое воздействие плазмы позволяют сваривать металлы разных толщин без подачи присадочной проволоки в сварочный шов, заваривать отогнутые кромки состыкованных деталей, сваривать детали без разделки кромок, осуществлять сварку металла большой толщины за один проход.
|
|
В зависимости от рода свариваемого металла применяют аргон, смеси аргона с гелием или водородом.
Установки плазменного нанесения покрытий
Нанесение коррозионно-стойких, жаропрочных и других защитных покрытий осуществляется методами напыления и наплавки.
При напылении плазмой частицы наносимого материала расплавляются и разгоняются до высоких скоростей, а деталь, на которую наносится покрытие-подложка, разогревается до высоких температур. При доведении подложки до состояния плавления процесс напыления переходит в наплавку.
Наносимый на подложку материал может представлять собой электропроводную проволоку или стержни (рис. 9.6), а также неэлектропроводный в холодном состоянии порошок (рис. 9.7).
![]() |
![]() |
При плазменной наплавке изделие и наносимый материал включаются в цепь тока через токоограничивающие сопротивления (рис. 9.8). Скорость подачи материала и перемещения горелки по обрабатываемой поверхности согласуется с тепловой мощностью плазменной струи.
|
|
Рис. 9.8 Схема наплавки с присадочной проволокой: а – изделие под током: б – изделие обесточено; 1 – горелка; 2 – ввод плазмообразующего газа; 3 – канал для ввода защитного газа; 4 – ограничительное сопротивление; 5 – источник питания; 6 – балластное сопротивление; 7 – присадочная проволока.
Дата добавления: 2021-07-19; просмотров: 127; Мы поможем в написании вашей работы! |
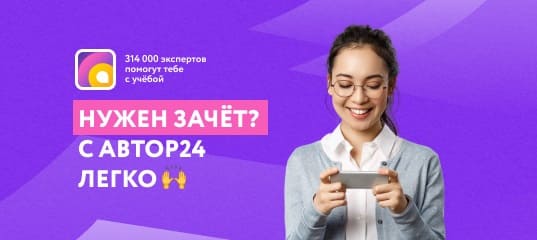
Мы поможем в написании ваших работ!