Технологические методы ремонта деталей
При ремонте деталей машин применяют технологические методы, которые можно разделить на следующие группы:
1. методы механической обработки;
2. сварка и наплавка;
3. металлизация напылением;
4. электролитические и химические покрытия;
5. применение при ремонте полимерных материалов;
6. методы пластического деформирования;
7. паяние.
Обработка деталей под ремонтные размеры
Обработка деталей под ремонтные размеры преследует цель восстановить качество сопряжения в кинематических парах типа вал – втулка, поршень – цилиндр и др. У более дорогостоящей детали сопряжения неравномерный износ устраняют механической обработкой, а менее дорогостоящую деталь заменяют новой, имеющей измененный (ремонтный) размер.
Рассмотрим методику определения ремонтных размеров на примере сопряжения вал – втулка. На рис. 9.1, а показано сечение нового вала диаметром d п и сечение изношенного вала диаметром d н, имеющего неравномерный износ. Наибольший односторонний износ составляет i В.
Минимальный припуск на одну сторону при обработке вала под ремонтный размер определяют по формуле:
![]() |
Рис.9.1
|

Где Rz – микронеровности изношенной поверхности; Т – толщина дефектного слоя поверхности вала перед ремонтом;
– прогиб вала; Е –неточность базирования вала на станке в связи с повреждениями центровых гнезд, биением центра передней бабки станка.
|
|
Ориентировочно припуск на сторону при чистовой обточке и расточке составляет 0,05–0,1 мм, при шлифовании – 0,03–0,05 мм.
Значение первого ремонтного размера для рассматриваемого случая определится по формуле
(9.2)
Обозначив 2(iв +Zв) через получим:
Величина характеризует ремонтный интервал для вала.
На рис 9.1 б показан первый ремонтный размер Dp1 при восстановлении отверстия втулки; D н – номинальный размер втулки; i а– наибольший односторонний износ отверстия; Za– снимаемый слой металла при обработке отверстия под ремонтный размер.
Ремонтный размер для отверстия втулки
(9.3)
Таким образом, расчётные формулы для определения ремонтных размеров будут иметь вид:
– для наружных цилиндрических поверхностей (валов)
– для внутренних цилиндрических поверхностей (отверстий)
где n – число ремонтных размеров, которое определяют по формулам:
|
|
для валов , (9.4)
для отверстий , (9.5)
где dmin – минимально допустимый диаметр вала, мм; Dmax– максимально допустимый диаметр отверстия, мм.
Применение при ремонте сварки и наплавки
Общие сведения. На ремонтных предприятиях сваркой и наплавкой восстанавливают свыше 50% деталей строительных и дорожных машин. Сварку применяют для заделки трещин, пробоин, сколов и устранения других механических повреждений деталей, наплавку – для восстановления размеров изношенных поверхностей деталей и увеличения их износостойкости.
Широкое распространение при ремонте машин сварки и наплавки объясняется быстротой выполнения операций, относительной несложностью технологического оборудования и экономичностью процессов. Однако сварка и наплавка имеют ряд недостатков: изменение структуры основного металла в зоне термического влияния и появления местных напряжений, приводящее к короблению деталей, снижению усталостной прочности и даже появлению трещин, затруднения при сварке и наплавке деталей из высокоуглеродистых и легированных сталей и изготовленных из чугуна.
|
|
Газовая сварка и наплавка. При газовой сварке и наплавке металл расплавляется теплом, выделяемым при сгорании горючего газа (ацетилена, пропан-бутана, метана и др.) в кислороде. В ремонтном производстве наибольшее распространение получила ацителено-кислородная сварка и наплавка. Используя ацитилено-кислородное пламя, выполняют следующие работы: сварку черных и цветных металлов и сплавов, наплавку твердых сплавов, резку металлов, поверхностную закалку, пайку твердыми припоями, сварку пластмасс.
Разновидности сварочно-наплавочных процессов по степени их механизации:
Сварочно-наплавочные процессы разделяют на ручные и механизированные. Ручные способы сварки и наплавки выполняются сварщиком без применения каких-либо механизмов. При механизированной
сварке и наплавке предусмотрено применение различных механизмов,
облегчающих и ускоряющих выполнение операций.
Ручные способы сварки и наплавки. Эти способы используют при сварке швов незначительной длины и при наплавке небольших поверхностей, т. е. в тех случаях, когда применение механизированных способов неэффективно.
|
|
Дуговая сварка и наплавка стальных деталей. При дуговой сварке используют постоянный и переменный ток. При сварке постоянным током электрическая дуга горит более устойчиво, причем ни положительном полюсе выделяется тепла больше, чем на отрицательном (температура соответственно 4200° и 3500 °С). В связи с этим для деталей из среднеуглеродистых и высокоуглеродистых сталей во избежание образования в результате перегрева закалочных трещин сварку ведут при подключении детали к отрицательному полюсу, т. е. при обратной полярности. На обратной полярности выполняют также сварку деталей небольшой толщины, что позволяет избежать прожога. При требовании повышенной глубины проплавления детали сварку выполняют на прямой полярности, т. е. к детали подключают положительный полюс. При сварке переменным током выделяется примерно одинаковое количество тепла на электроде и детали.
На переменном токе сваривают низкоуглеродистые и низколегированные стали, так как детали из таких сталей малочувствительны к перегреву и хорошо свариваются.
На качество сварки и наплавки деталей большое влияние оказывает правильный выбор электрода и режима работы. Для сварки конструкционных низкоуглеродистых и низколегированных сталей 15Х, 20Х применяют электроды Э−34, Э −38, Э −42, Э −42А, Э –46, а для наплавки поверхностей –электроды ЭН−18Г4−35, ЭН−20Г4−40 и др. Для сварочных работ стержнями электродов обычно является низкоуглеродистая проволока Св.− 08, Св.− 08ГА и др.
Дата добавления: 2020-04-25; просмотров: 125; Мы поможем в написании вашей работы! |
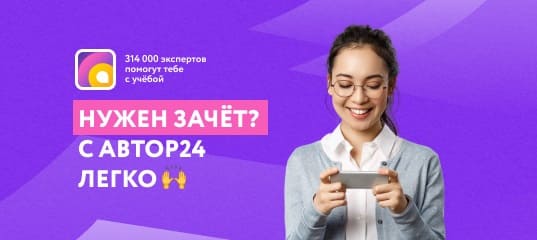
Мы поможем в написании ваших работ!