ГОРИЗОНТАЛЬНО-РАСТОЧНЫЕ СТАНКИ
(4.6)
Где ; K Т – см. табл.5.1; K С K П K КП – коэффициенты упрощения конструкции станка;
K С =0,9 – без задней стойки; K П = 0,9 – без планшайбы и радиального суппорта; K кп =0,9 без механической коробки подач; при наличии данных узлов коэффициенты равны 1,0; K мр – коэффициент массы станка (табл.4.8); K 1 =0,08; K 2=0,006; K 3=0,003; K 4=0,001; D шп. – диаметр выдвижного шпинделя, мм; H бс - вертикальное перемещение шпиндельной бабки, мм; Sc – продольное перемещение передней стойки, мм; S пс – продольное перемещение передней стойки, мм; вс – поперечное перемещение стола, мм; впс−поперечное перемещение передней стойки, мм; R бг− ремонтносложность механизма бесступенчатого регулирования частоты вращения шпинделя и величины подачи:
,
где Хвг− число механических вариаторов.
Таблица 4.8
Масса станка, т | Kмр | Масса станка, т | Kмр |
До 10 | 1,0 | 30−100 | 1,4 |
10−30 | 1,25 | Св. 100 | 1,8 |
КРУГЛОШЛИФОВАЛЬНЫЕ СТАНКИ
, (4.7)
где ;
K Т – см. табл.4.1; K ск = 1, для наружного шлифования; Kск= 1,1 для внутреннего шлифования;
K ак – коэффициент автоматизации:
Станок с ручным управлением--------------------------1,0
Полуавтомат-------------------------------------------------1,2
Автомат-------------------------------------------------------1,3
|
|
K 1= 0,015; K 2 = 0,003; do – см. формулу (4.1); L ш – наибольшая длина шлифования, мм;
R ом = R ПП + R сд ;
R ПП – ремонтносложность механизма автоматической поперечной подачи шлифовальной бабки; R ПП = 0,5;
R сд – ремонтносложность механизмов, не входящих в основной комплект станка (см. табл.4.4)
ВЕРТИКАЛЬНО-ГОРИЗОНТАЛЬНО-ФРЕЗЕРНЫЕ СТАНКИ
, (4.8)
где ;
K Т – см. табл. 4.1; Киф − коэффициент исполнения:
вертикальные и горизонтальные---------------------------1,0
универсальные и вертикальные с поворотной головкой------------------1,2
широкоуниверсальные и бесконсольные -------------------------------------1,25
K ПФ− коэффициент частоты вращения шпинделя;
K ПФ= 1,0 при частоте < 2000 об/мин, KГФ = 1,1 при частоте > 2000 об/мин,
K 1 = 0,03; K 2 = 0,125;
Всф – ширина стола, мм; n 3 – число ступеней скоростей шпинделя;
R ом = R гф + R ,
R гф – ремонтносложность гитары сменных зубчатых колес для станков не имющих коробки скоростей;
R гф = 0,4; R бм – ремонтносложность механизма бесступенчатого регулирования скорости шпинделя: R = 1,8.
КОНСТРУКТОРСКАЯ И ТЕХНОЛОГИЧЕСКАЯ ПОДГОТОВКА
Конструкторская подготовка ремонтных работ состоит в заблаговременном приобретении или изготовлении чертежей на подлежащие замене и восстановлению деталь.
|
|
Технологическая подготовка ремонта включает:
§ приобретение или разработку типовых технологических процессов разборки и сборки агрегатов;
§ приобретение или разработку новых типовых технологических процессов изготовления заменяемых деталей и восстановления незаменяемых деталей;
§ приобретение чертежей либо конструирование и изготовление технологической и контрольно-поверочной оснастки, специального инструмента и средств механизации ремонтных работ;
§ составление дефектно-сметных ведомостей на оборудование, проходящее в планируемом году капитальный ремонт.
Составление дефектно-сметной ведомости разделяют на два этапа. Предварительную форму заполняют при полном осмотре, предшествующем капитальному ремонту, по данным визуальной проверки вскрываемых узлов и инструментального замера износа отдельных деталей.
Окончательную дефектно-сметную ведомость составляют путём внесения уточнения в форму при разборке и дефектации деталей в процессе капитального ремонта. Ведомость составляют инспектор ОГМ или мастер РМЦ.
|
|
Технологическая подготовка работ по техническому обслуживанию включает:
- разработку карт планового технического обслуживания на конструктивно близкие группы моделей оборудования;
- разработку инструкционно-технологических карт на отдельные операции технического обслуживания;
- разработку типовых инструкций на выполнение операций технического обслуживания с регламентированными переходами.
Обеспечение технической документации РМЦ и ЦРБ возлагается на конструкторско- технологическое бюро ОГМ.
Внедрение типовых технологических процессов создает условия для использования различных приспособлений, значительно облегчающих процессы ремонта.
Типовой технологический процесс предназначен для работников ремонтных служб машиностроительных предприятий при проведении капитального ремонта станков с целью увеличения производительности труда, улучшения качества ремонта и снижения себестоимости ремонтных работ.
Технологический процесс разрабатывается с учётом применения прогрессивных методов ремонта и дает возможность использовать высокопроизводительное оборудование, приспособления и инструмент, а также содержит варианты, дающие возможность ремонтным службам ремонтировать станки различными методами в зависимости от специфических условий и технической вооруженности этих служб.
|
|
Для примера рассмотрим технологический процесс капитального ремонта токарно-винторезного станка, который включает следующие операции:
§ осмотр станка и проверка на точность;
§ демонтаж электроаппаратуры;
§ промывка станка в сборе;
§ разборка станка на узлы, промывка узлов в сборе;
§ дефектация деталей
§ ремонт и изготовление новых деталей
§ ремонт системы охлаждения, окраска деталей станка;
§ сборка узлов и их обкатка;
§ общая сборка станка, испытание станка;
§ окраска станка в сборе.
Испытания станка на холостом ходу, под нагрузкой и в работе производят согласно техническим условиям на ремонт металлорежущего оборудования (ОМТРМ 3312-009-66).
Важное значение придаётся выбору базы при ремонте станины. За основную базу принимаются направляющие поверхности станины.
Технологический процесс ремонта направляющих станины предусматривает четыре варианта: ремонт шлифованием; ремонт строганием; ремонт строганием с последующей термической обработкой и шлифованием; ремонт шабрением. При этом необходимо добиваться следующих показателей: шероховатость Ra= 0,65…1,25 мкм: непрямолинейность направляющих для каретки в вертикальной плоскости не более 0,02 мм на длине 1000мм (только в сторону выпуклости); непараллельность направляющих под каретку не более 0,02 мм на 1000мм.
6. ТОЧНОСТЬ МЕХАНИЧЕСКОЙ ОБРАБОТКИ
И МЕТОДЫ ЕЁ ОБЕСПЕЧЕНИЯ
При изготовлении деталей невозможно достичь абсолютно точных номинальных размеров. В связи с этим при составлении рабочих чертежей деталей назначаются допустимые отклонения от номинальных размеров.
Точность детали характеризуется:
§ допускаемыми отклонениями её действительных размеров от номинальных;
§ допускаемыми отклонениями от геометрической формы деталей (овальность, огранка, неплоскостность, нецилиндричность, непрямолинейность и т.д);
§ допускаемыми отклонениями поверхностей и осей детали от их взаимного расположения.
Отдельным критерием оценки точности детали является шероховатость поверхности.
Под точностью изготовления детали понимается степень соответствия её всем требованиям рабочего чертежа, техническим условиям и стандартов.
Отклонения параметров реальной детали от заданных номинальных называют погрешностью изготовления.
Допуски, проставляемые на рабочем чертеже, носят название конструкторских.
В процессе разработки технологического процесса технолог проставляет допуски на размеры заготовок, которые называют технологическими или операционными.
Дата добавления: 2020-04-25; просмотров: 147; Мы поможем в написании вашей работы! |
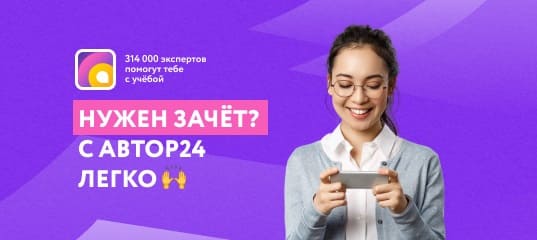
Мы поможем в написании ваших работ!