МЕТОДЫ ОБЕСПЕЧЕНИЯ ЗАДАННОЙ ТОЧНОСТИ
Метод пробных проходов заключается в последовательном снятии стружки, измерение получаемых размеров. Этот метод трудоёмкий, так как требует много времени на выверку заготовки и на корректировку положения режущего инструмента.
Метод автоматического получения заданного размера заключается в том, что партию заготовок обрабатывают на предварительно настроенном станке с установкой заготовок в приспособлении без выверки их положения, а режущий инструмент при наладке станка устанавливают на определённый размер, называемый настроечным.
Этот метод более производителен, но требует специальных приспособлений и, более того, стабильных по размерам заготовки.
В обоих рассмотренных методах на точность обработки оказывает влияние квалификация рабочего.
6.2 АНАЛИЗ ПАРАМЕТРОВ ТОЧНОСТИ МЕХАНИЧЕСКОЙ
ОБРАБОТКИ МЕТОДОМ МАТЕМАТИЧЕСКОЙ СТАТИСТИКИ
Виды погрешностей. Все погрешности обработки можно разделить на систематические постоянные, систематические переменные и случайные.
Систематическими постоянными погрешностями называют такие, которые при обработке партии заготовок постоянны по значению и знаку.
Систематическими переменными погрешностями называют такие, которые в процессе обработки закономерно изменяются по времени, т.е. в зависимости от числа изготовленных деталей (износ режущего инструмента, тепловые деформации).
Случайными погрешностями называют такие, которые для заготовок данной партии имеют различные значения, предсказать которые невозможно (погрешность установки заготовки и инструмента, упругие отжатия элементов технологической системы).
|
|
Вероятностно-статистический метод оценки точности основан на проведении обработки опытной партии заготовок с замерами интересующего размера.
Результаты замеров математически обрабатывают, после чего строят кривую распределения исследуемого размера. Для этого выявляют предельные значения, определяют разность между наибольшим и наименьшим размерами заготовок в данной партии − размах колебаний или поле рассеяния размеров:
(6.1)
Полученное значение разбивают на равные интервалы и определяют частость повторения отклонений размеров в каждом интервале:
, (6.2)
Где m – число заготовок, фактический размер которых находится в пределах данного интервала;
n – общее число деталей в партии.
Рис. 6.1
Далее строят график (полигон) распределения размеров. Например, на графике, приведенном на рис.6.1, а, общее число деталей в исследуемой партии составляет 100 шт. Поле рассеяния размеров мм. Для построения полигона размеров принято восемь размерных групп с интервалом в 0,02 мм. В первой размерной группе оказалось 5 деталей, т.е. частость
, во второй группе – 13, т.е. частость
Полученные точки соединяют прямыми.
|
|
Экспериментально установлено, что при обработке заготовок на металлорежущих станках способом автоматического получения размеров точность обработки подчиняется закону нормального распределения или кривой Гаусса (рис.6.1 б), уравнение которой
, (6.3)
где среднее квадратичное отклонение; е– основание натуральных логарифмов;
параметр а− является центром группирования значений аргумента (среднее арифметическое).
, (6.4)
Где n – число произведенных измерений; х i – значение текущего измерения; x ср– среднее арифметическое данных измерений:
|
|
(6.5)
Число измерений n следует брать не менее 50. Кривая нормального распределения симметрична. Ордината вершины кривой будет при x = a; она определяется из выражения
Кривая имеет точки перегиба на расстоянии x = .
Их ординаты равны
.
Величина характеризует форму кривой распределения и является мерой точности данного метода обработки. При увеличении
вершина кривой снижается, но ветви кривой растягиваются, т.е. поле рассеяния размеров растет.
На рис.6.2 ,а схематически показаны кривые распределения диаметральных размеров при обработке партии заготовок: предварительное точение (кривая ), чистовое точение (кривая
), шлифование (кривая
).
При правильном построении этапов необходимо условие .
Рис. 6.2
Если обрабатываются две партии одноимённых заготовок, то появляется систематическая постоянная погрешность, связанная с погрешностью настройки станка и инструмента на размер. В этом случае кривые распределения погрешностей при обработке двух партий будут смещены одна относительно другой на размер постоянной погрешности . (рис.6.2, б)
|
|
Изучение кривых распределения погрешностей позволяет выявить соотношение между числом годных и бракованных деталей.
Предположим, что на обработку заготовок установлен допуск . На оси абсцисс (рис.6.2, в) этот допуск определяется величинами х1 и х2 от границ центра группирования. Заштрихованный участок соответствует числу заготовок, находящихся в пределах поля допуска.
Отношение этой площади этого участка к общей площади ограниченной кривой, определяет вероятность получения годных заготовок.
; (6.6)
. (6.7)
Если принять , то эти интегралы можно представить в виде функции Ф(z):
; (6.8)
; (6.9)
Вся площадь, ограниченная кривой, равна 1. Значения величин меньше единицы. Значения функций Ф(z) через десятую долю аргумента приведены в табл. 6.1.
Таблица 6.1
z | Ф( z) | z | Ф( z) | z | Ф( z) |
0 | 0 | 1,2 | 0,7699 | 2,4 | 0,9836 |
0,1 | 0,0797 | 1,3 | 0,8064 | 2,5 | 0,9876 |
0,2 | 0,1585 | 1,4 | 0,8385 | 2,6 | 0,9907 |
0,3 | 0,2358 | 1,5 | 0,8664 | 2,7 | 0,9931 |
0,4 | 0,3108 | 1,6 | 0,8904 | 2,8 | 0,9949 |
Окончание табл. 6.1
0,5 | 0,3829 | 1,7 | 0,9109 | 2,9 | 0,9963 |
0,6 | 0,4515 | 1,8 | 0,9281 | 3 | 0,9973 |
0,7 | 0,5161 | 1,9 | 0,9426 | 3,1 | 0,99806 |
0,8 | 0,5763 | 2 | 0,9545 | 3,2 | 0,99862 |
0,9 | 0,6319 | 2,1 | 0,9643 | 3,3 | 0,99903 |
1 | 0,6827 | 2,2 | 0,9722 | 3,4 | 0,99933 |
1,1 | 0,7287 | 2,3 | 0,9786 | 3,5 | 0,99953 |
Из табл. 6.1 видно, что в интервале z= , т.е. при X=
, площадь, ограниченная этим участком кривой, составляет 0,9973 всей площади.
Это означает, что 99,73% всех обработанных заготовок, находящихся в интервале 6 , будут годными и процент брака не превысит 0,27%.
Таким образом, определив для исследуемого процесса значение , можно установить точность данного метода обработки по величине 6
(правило «шести сигм»). Если принять для расчёта, например, величину 5
, то процент брака возрастёт до 1,24 (см. табл.6.1).
Правило «шести сигм» является достаточно точным для практических расчётов.
Пример: Установить вероятность брака деталей, если среднее квадратичное отклонение для исследуемого процесса мм, а границы поля допуска (рис.6.2) расположены от центра группирования на расстоянии
Решение. Определяются значения Z1 и Z 2:
;
По таблице 6.1 определяются :
Вероятность брака (в процентах)
.
7. Влияние качества поверхности
на эксплуатационные свойства детали
Шероховатость обработанной детали, наклёп и остаточные напряжения в поверхностном слое детали значительно влияют её эксплуатационные свойства: износостойкость, коррозийную стойкость, усталостную прочность, стабильность посадок.
Шероховатость поверхности уменьшает площадь фактического контакта двух сопрягаемых поверхностей, поэтому в начальный период работы возникают значительные удельные давления и более интенсивный износ.
Грубо обработанные поверхности более подвержены коррозии, особенно в атмосферных условиях, так как коррозия наиболее интенсивно протекает на дне микронеровностей и мелких царапин.
Установлено, что прочность стальных деталей, обработанных резанием, по сравнению с полированными деталями в условиях знакопеременной нагрузки составляет 40…50%.
При запрессовке детали наблюдается сглаживание микронеровностей, приводящие к уменьшению фактического натяга и, как следствие уменьшение прочности соединения.
Создание в поверхностном слое наклепа и остаточных сжимающих напряжений в большинстве случаев повышает усталостную прочность (на 30…80%) и износостойкость (в 2..3 раза), но одновременно в 1,5…2 раза уменьшает коррозийную стойкость.
Шероховатость поверхности зависит от метода и режима обработки, качества применяемого режущего инструмента, жесткости технологической системы, свойств обрабатываемого материала и др.
Каждому методу обработки соответствует свой диапазон получаемой шероховатости поверхности (см. табл. 7.1).
Таблица 7.1
Метод обработки | Соответствующий квалитет точности | Шероховатость поверхности Ra, мкм | Метод обработки | Соответствующий квалитет точности | Шероховатость поверхности Ra, мкм |
Точение: предварительное…
чистовое…..
тонкое, алмазное… | 12-13 | 12,5 | Прошивание (для коротких отверстий)… | 7 | 0,63-0,32 |
10-11 | 2,5-12,5 | шлифование: обдирочное… | - | 2,5-1,25 | |
6-7 | 0,63-0,32 | предварительное.. | 8-10 | 1,25-0,63 |
![]() |
|
Фрезерование: предварительное чистовое тонкое (торцовыми фрезами) | чистовое… | 7-8 | 0,63-0,32 | ||
11-12 | 12,5 | тонкое…. | 6-7 | 0,32-0,08 | |
8-10 | 2,5-1,25 | Хонингование отверстий диаметром до 80 мм… | 6-7 | 0,32-0,08 | |
6-7 | 0,63-0,32 | Развертывание: предварительное. чистовое… тонкое… | |||
Сверление: | 11-12 | 6,3-2,5 | 8-9 | 2,5-1,25 | |
Зенкерование: предварительное… чистовое (после чернового)…. | 7 | 1,25-0,63 | |||
12 | 2,5-12.5 | 6-7 | 0,63-0,32 | ||
11 | 6,3-2,5 |
Рис.7.1
При обработке заготовок лезвийным инструментом шероховатость поверхности в значительной мере зависит от скорости резания и подачи (рис.7.1 а, б)
Кривая 1– соответствует точению стали, кривая 2 – точению чугуна.
При обтачивании стальной заготовки со скоростью до 20 м/ наблюдается наибольшая шероховатость, что связано с активным образованием нароста на режущей кромке резца. При скорости выше указанной образование нароста снижается, кроме того, при высоких скоростях резания значительно уменьшается глубина пластических деформаций, что также снижает шероховатость.
На рис. 7.1 б показана зависимость шероховатости поверхности от подачи при точении заготовки из стали 45 резцом с радиусом при вершине 2,5 мм.
При переходе в область подач свыше 0,2 мм/об микронеровности обработанной поверхности возрастают более интенсивно. С увеличением глубины резания шероховатость поверхности возрастает незначительно и практически её можно не учитывать.
При обработке заготовок абразивным инструментом шероховатость поверхности снижается с уменьшением зернистости и повышением твердости шлифовального круга, повышением скорости резания, уменьшением продольной и поперечной подачи.
При обработке стали с высоким содержанием углерода (C > 0,5%) шероховатость снижается по сравнению с обработкой низкоуглеродистой стали.
Дата добавления: 2020-04-25; просмотров: 683; Мы поможем в написании вашей работы! |
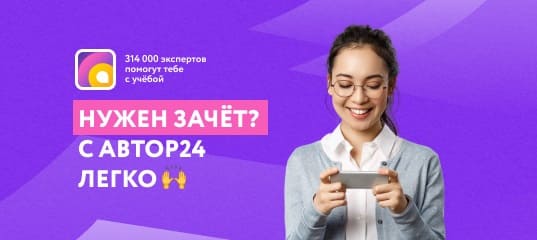
Мы поможем в написании ваших работ!