Определение основных параметров выемочного блока.
Длина блока. На выбор длины блока для различных систем разработки оказывают влияние многие факторы. Так, например, для систем с открытым очистным пространством решающее значение имеет устойчивость вмещающих пород и наряду с этим учитывается необходимая интенсивность очистной выемки, а также стоимость проходки восстающих.
Эти же факторы определяют длину блока при системе с магазинированием руды и шпуровой отбойкой из магазина. При отбойке глубокими скважинами длина блока ограничивается эффективной глубиной взрывных скважин и выдержанностью контуров рудного тела.
При системах разработки горизонтальными слоями с закладкой длину блока, т. е. расстояние между закладочными восстающими, выбирают с учетом следующих факторов: способа размещения закладки в блоке, мощности рудного тела, стоимости проходки восстающих и потерь руды в междублоковых целиках.
Длину блока для систем слоевого и подэтажного обрушения определяют с учетом эффективных условий транспортирования руды, интенсивности выемки блока, величины горного давления в слоевых и подэтажных выработках и расходов по их ремонту.
При системах этажного обрушения длина и горизонтальная площадь блока зависят от физических свойств руды и пород, мощности и угла падения рудного тела.
Из сказанного следует, что для разных систем разработки и горно-геологических условий нельзя дать единый метод определения длины блока. Для ее определения можно пользоваться теми конкретными соображениями, которые были приведены при описании каждой системы разработки.
Ширина камер и междукамерных целиков. При камерно-столбовых и комбинированных системах разработки выбор ширины камер и междукамерных целиков является основной задачей конструирования системы.
В связи с тем что выемка камер более производительна и происходит со значительно меньшими потерями, чем выемка целиков, ширину камер принимают как можно большей, а целиков — по возможности меньшей. Ширину камер ограничивает уменьшение устойчивости кровли камер, потолочины и обнаженной поверхности висячего и лежачего боков. Уменьшение ширины междукамерного целика снижает его надежность.
Расчетных методов для определения безопасной ширины камеры нет. Известные в литературе методы расчета размеров междукамерных целиков пригодны только для рудных тел наклонного и пологого падения и не могут быть использованы для крутопадающих.
Из рассмотрения систем разработки известно, что ширину камер принимают, как правило, не менее 8-10 и не более 20-25 м. Редко она достигает 30 м и в порядке исключения 50 м. В этих пределах ширину выбирают с учетом устойчивости руды и вмещающих пород, скорости выемки камер и целиков. Выбранную ширину камер и целиков корректируют исходя из практики применения их на данном руднике.
|
|
|
|
Толщина междуэтажных целиков. Маломощные рудные тела можно разрабатывать системами с открытым очистным пространством, с магазинированием руды, с креплением и закладкой как с оставлением, так и без оставления междуэтажных целиков.
При разработке маломощных жил системами с магазинированием руды, с закладкой и с открытым очистным пространством вместо надштрековых целиков иногда сооружают прочное крепление в кровле штрека. Оставление надштрекового целика часто осложняет нарезку блока и приводит к излишним потерям руды.
Давление отбитой руды и закладки на крепь штрека при небольшой мощности жил невелико и ему может противостоять рамная крепь обычных размеров или распорная крепь.
Толщину (высоту) надштрекового целика обычно определяют графическим построением, принимая высоту рудоспуска 1 м и угол наклона воронок 45°. Если оставляют плоский целик (не в форме воронки), то толщину его принимают 1,5-3 м.
Подштрековый целик в маломощных жилах оставляют в том случае, если верхний штрек необходимо сохранить для откатки или вентиляции. Толщина целика от 1 до 2 м, редко 3 м. При очень малой мощности жилы в устойчивых боках вместо целика на уровне подошвы верхнего штрека устанавливают ряд распорной крепи, которую покрывают настилом.
В мощных рудных телах толщину надштрекового целика (днища) обычно определяют графическим построением с учетом необходимой длины и емкости рудоспусков между основным горизонтом и рудоприемными воронками, принятого расстояния между рудоспусками, применяемой системы разработки и способа выемки целиков. Общих правил и рекомендуемых значений при любых системах разработки привести нельзя. Конкретные примеры построения надштрековых целиков, которыми можно руководствоваться, были приведены в описании отдельных систем разработки.
Толщину подштрековых целиков (потолочин) принимают в зависимости от ширины камеры, устойчивости руды, вмещающих пород и прочности их контакта.
Можно рекомендовать следующие примерные соотношения толщины потолочины hп и ширины камеры b:
- наиболее благоприятные условия (очень устойчивая руда и бока, прочные контакты) hп/b = 0,2÷0,3;
- средние условия (руда и бока устойчивы, но с местными ослаблениями, контакты средней прочности) hп/b = 0,3÷0,5; неблагоприятные условия hп/b = 0,5÷0,7.
Высота подэтажа, выемочного слоя и уступа. Размеры этих конструктивных элементов определяются принятым вариантом системы разработки, способом бурения и глубиной шпуров (скважин), способом крепления очистного пространства.
При выборе размеров прежде всего имеют в виду обеспечение безопасности работ; снижение потерь и разубоживания; достижение наиболее высокой производительности труда и необходимой интенсивности очистной выемки.
Вез проведения специальных опытных работ или без производственного опыта в конкретных условиях окончательно выбрать размеры конструктивных элементов системы невозможно. Принятые в практике высоты подэтажа, слоя и уступа при различных горно-геологических условиях и разных вариантах систем были приведены в описании последних.
|
|
|
|
67. Общий порядок расчета системы разработки.
68. Система разработки приемлемые по постоянным фактором.
69. Ограничение в выборе системы разработки по переменным факторам.
70. Критерии технико-экономической оценки систем разработки.
71. Расчет воронок обрушения при системах с массовым обрушением.
72. Горнотехнические факторы выбора схем КРМ.
73. Основные принципы и закономерности сдвижения земной поверхности от ведения подземных горных работ.
74. Последствия неправильного ведения взрывных работ при КРМ.
75. Особенности проветривания при КРМ.
76. Буровзрывные работы в карьере для погашения пустот под уступами.
77. Возможность выброса горной массы в карьер при массовых взрывах.
78. Предотвращение проникновения газов при взрывных работах в карьере в подземные выработки.
79. Классификация способов вскрытия при КРМ.
80. Использование самоходного оборудования для доставки добытой руды в карьер.
81. Отработка рудных залежей системами с закладкой и обрушением.
82. Использование подземных горных выработок при эксплуатации карьера.
83. Использование карьерного пространства для подземной добычи.
84. Достоинства и недостатки всасывающего и комбинированного способов проветривания.
85. Рациональные схемы проветривания в районе аэродинамических связей с поверхностью.
86. Расчет параметров взрывных работ при КРМ.
87. Управление геомеханическими процессами при комбинированной разработке угольных месторождений.
88. Стадийность и направление совершенствования комбинированного способа разработки угольных месторождений.
89. Рациональные и безопасные параметры комбинированной отработки угольных месторождений.
90. Комбинированные схемы вскрытия шахтного и карьерного полей с использованием подземных выработок.
91. Классификация способов вскрытия и пути совершенствования.
92. Методы гравитационного перемещения горной массы.
93. Системы комбинированной разработки карьерного и шахтного полей.
94. Расчет предельно допустимых параметров карьера.
95. Определение места заложения вертикального ствола при КРМ.
96. Особенности ведения очистных работ при КРМ.
97. Определение предельной глубины карьера при КРМ.
98. Определение среднего расстояния подземной транспортировки при КРМ.
99. Условия безопасного ведения горных работ при КРМ.
100. Повторная отработка месторождений.
101.Классификация комбинированной разработки месторождений по Вовку А.А.
Классификация А.А. Вовка и Г.И. Черного [8] является развитием классификации Б.П. Юматова, дополнительно содержит требования к методам и сие- * темам ведения открытых и подземных работ. Все возможные виды комбиниро-ванной разработки разделены на 6 классов (табл. 1.2) в зависимости от направления развития горных работ во времени и в пространстве и с учетом вида применяемого оборудования.
В классификацию введены способ шнекобуровой выемки из карьера и способ ведения подземных очистных работ из карьеров или въездных траншей. : Последний предполагает вскрытие и отработку запасов штольнями из карьера и использование карьерных транспортных путей для вывоза полезных ископае- мых из зоны подземных работ, а карьерного пространства - для вентиляции подземных выработок.
В классификации В.А. Щелканова [93], получившей наиболее широкое ; распространение, углубляются положения вышерассмотренных классификаций '. и дополнительно вводятся количественные показатели, характеризующие степень совмещения работ во времени, в пространстве, тесноту технологической : взаимосвязи горных работ (табл. 1.3).
За основной признак деления способов комбинированной разработки принят коэффициент совмещения открытых и подземных работ во времени, равный отношению времени одновременного ведения горных работ к общему сроку отработки месторождения. По этому признаку комбинированная отработка
месторождения делится на три группы: с полным совмещением и одновременным ведением открытых и подземных работ, с частичным совмещением, без совмещения во времени (последовательная разработка).
102. Классификация комбинированной разработки месторождений по Зуркову П.Е.
103. Гидрогеологические факторы выбора схем Комбинированной Разработки Месторождений.
104. Организационные факторы выбора схем КРМ.
105. Основные направления снижения сейсмического воздействия взрывов в карьере на подземные горные выработки и целики.
106. Рациональные схемы ведения взрывных работ в карьере при КРМ.
107. Опыт разработки кимберлитовых месторождений Якутии.
Опыт проектирования и разработки кимберлитовых месторождений Якутии показывает, что вопросы подземной отработки подкарьерных запасов трубки самостоятельно и не всегда рационально.
Учитывая опыт разработки, предлагают максимально использовать карьерное пространство для проходки из него вскрывающих выработок, что позволит существенно сократить срок начала подземной добычи кимберлитов.
Разработка и принятие единой схемы вскрытия месторождения обепечат наибольшую экономическую эффективность отработки месторождений, и в целом ритмично спланируют производительность предприятий на весь период отработки.
108. Применение рудоспусков при комбинированной разработке.
Выработки всех видов не крепят (кроме днища и сопряжений ствола рудоспусков). Форма поперечного сечения вертикальных рудоспусков круглая. Диаметр выработки выбирается из условий свободной транспортировки горной массы, производительности и глубины рудоспуска (минимальное его значение не менее 4-5-кратного максимального размера транспортируемых кусков). Вертикальные рудоспуски наиболее надёжны в эксплуатации, в них легче ликвидировать зависания руды, но при большой глубине в нижней части таких выработок происходит сильное самоуплотнение аккумулируемой горной массы. Наклонные рудоспуски (уклон обычно 45-60°) — выработки с арочной или круглой формой поперечного сечения. Они лишены недостатка, присущего вертикальным рудоспускам, однако в этих рудоспусках выше вероятность зависания горной массы и их стенки подвержены сильному износу. Ступенчатые рудоспуски (круглая форма поперечного сечения) применяют в основном для снижения высоты падения кусков руды и соответственно их динамического воздействия на днище и выпускные устройства рудоспуска. В случае необходимости попутного дробления руды при перемещении её по рудоспускам возможно использование коленчатых выработок с дробящими плитами. Для повышения эффективности процесса в рудоспусках предусматривается установка колосниковых грохотов, позволяющих отсеивать мелочь. В нижней части рудоспуска устраиваются наклонное днище, армируемое износостойким металлом, и погрузочные люки (при конвейерном транспорте в подземной выработке днище рудоспуска оборудуется пластинчатым питателем или вибропитателем). На карьерах большой производственной мощности нижнюю часть рудоспуска расширяют с отношением высоты создаваемой камеры к её ширине 1,5-4. Увеличение ширины основания камеры позволяет исключить зависание руды в рудоспуске, увеличить скорость её погрузки в штольне.
109. Перспективы применения комбинированного способа разработки на золоторудных месторождениях Якутии.
110. Специальные мероприятия, обеспечивающие безопасность КРМ.
Дата добавления: 2020-04-08; просмотров: 206; Мы поможем в написании вашей работы! |
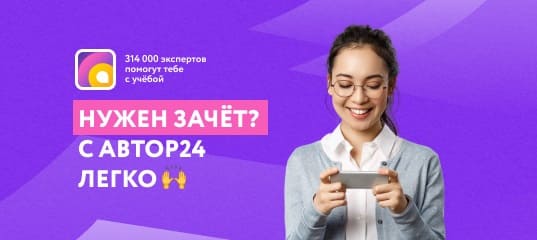
Мы поможем в написании ваших работ!