Нисходящая слоевая выемка с твердеющей закладкой
Система применяется для выемки неустойчивых ценных руд, особенно при высокой их возгораемости или при необходимости поддержания земной поверхности. Крутые залежи могут быть любой мощности, пологие должны иметь мощность не ниже средней. Вмещающие породы могут быть любой устойчивости.
Блок отрабатывают слабо наклонными слоями, начиная с верхнего (рис. 4.6). Слои вынимают заходками, которые затем заполняют твердеющей закладкой. Работы ведутся под защитой закладочного массива.
Высота слоя 3—4 м, ширина заходок 3,5—7 м в зависимости от устойчивости кровли, представленной закладочным массивом. Наклон заходок (4—10°) немного превышает угол растекания закладочной смеси
Рис. 4.6. Нисходящая слоевая выемка с твердеющей закладкой
На бурении и доставке руды используют преимущественно самоходное оборудование легкого типа. При запасе залежи менее 30—50 тыс. т предпочтительнее скреперная доставка руды.
Закладочную смесь подают по трубам по возможности без перерывов для получения монолитного закладочного массива. На границе с заложенной заходкой работы начинают через 5—7 сут, а снизу через две недели.
На глубинах 500—1000 м и более вести выемку без крепления заходок можно лишь при увеличенной прочности закладочных смесей и при образовании в нижней части слоя железобетонной конструкции за счет укладки в заходку металлических элементов перед заполнением ее закладочной смесью. Эти элементы могут быть подвешены к металлическим лежням вышележащего слоя.
|
|
При разработке небольших обособленных залежей руд средней крепости с применением легких ПДМ и площади блока 1000—1500 м2 производительность блока составляет 7—10 тыс. т/мес; производительность труда забойного рабочего 30—60 т/смену; расход подготовительно-нарезных выработок 8—12 м на 1000 т; потери руды
3—5 %, разубоживание 8—10 %.
Требования ПТЭ к системам с закладкой:
Общие требования к системам с закладкой:
- Системы с закладкой можно применять при отработке рудных тел любой мощности с любым углом падения. Руда должна быть от средней устойчивости до устойчивой, не склонной к обрушениям, вмещающие породы, как правило, средней устойчивости, требующие искусственного их поддержания.
- Область применения систем с закладкой может быть расширена в случае разработки ценных или пожароопасных руд, необходимости сохранения поверхности, а также в случаях высокого горного давления и опасности горных ударов.
- В зависимости от горнотехнических условий могут применяться следующие виды закладки: сухая, сухая с иньектированием вяжущих растворов, гидравлическая, твердеющая. Система может предусматривать применение нескольких видов закладочного материала.
- При отработке тонких рудных тел рекомендуется вести раздельную выемку руды и породы. В зависимости от крепости и устойчивости руды и породы в начале может отбиваться руда, а затем пород или наоборот. Подрываемые породы оставлять в выработанном пространстве в качестве закладки. При излишнем отбиваемых пород часть их выдавать из блоков; при недостаточном - увеличить объем подрываемых вмещающих пород для заполнения выработанного пространства. При отработке пологих и наклонных рудных тел для повышения эффективности очистной выемки рекомендуется использовать силу взрыва при отбойке для отброса пустой породы в выработанное пространство.
- При необходимости поддерживать кровлю временной крепью (стойки, крепежные рамы и др.), ослабленные участки крепи.
- Крепление рудоспусков в закладке должно исключать потери руды.
- Расстояние между рудоспусками устанавливается проектом. При необходимости в закладке выкреплять ходовые восстающие.
- При отработке крутопадающих рудных тел камеры, как правило, располагать по простиранию. Если предельно допустимая ширина камеры меньше мощности рудного тела, камеры располагать вкрест простиранию. При отработке мощных пологих пород и наклонных рудных камер можно располагать по простиранию, вкрест простирания и по восстанию.
Требования к системам с однослойной выемкой и закладкой:
|
|
|
|
- Сплошную и столбовую системы с однослойной выемкой на всю мощность и закладкой целесообразно применять для отработки пологих и наклонных ( до 35 ) рудных тел мощностью менее 3 м. при рудах любой устойчивости, залегающих в устойчивых породах.
- При сплошной системе панель (этаж)отрабатывать на всю ширину (высоту),при столбовой - разделять на столбы (подэтажи).Очистную выемку вести лавами по простиранию или заходками по восстанию.
- Ширина очистного пространства (заходки) определяется в зависимости от устойчивости руды и пород, а также применяемого оборудования и устанавливается проектом.
Требования к системе горизонтальных слоев с закладкой
- Систему горизонтальных слоев с закладкой можно применять для отработки круто падающих рудных тел любой мощности и мощных рудных тел с любым углом падения, при рудах средней устойчивости (маломощные рудные тела) и устойчивых, залегающих в породах средней устойчивости.
- При отработке крутопадающих рудных тел мощностью до 3 м. с устойчивыми рудами, а также при отработке рудных тел большей мощности и полевой подготовке выемку можно вести блоками (камерами) без оставления междукамерных (междублоковых) и междуэтажных целиков.
- При одновременной работе в двух и более блоках без оставления между ними целиков соблюдать предусмотренное проектом опережение линии забоев в смежных блоках.
- Выемку руды в камере (блоке) допускается осуществлять горизонтальными слоями в направлении снизу вверх или сверху вниз в зависимости от горнотехнических условий по проекту. При неустойчивых рудах выемка должна производиться слоями сверху вниз с обязательным применением твердеющей закладки.
- Закладку подавать в блок (камеру) с верхнего горизонта по закладочному восстающему, расположенному, как правило, в середине блока (камеры). Закладку в слое размещать с использованием механизмов (скреперных лебедок, закладочных машин, самоходного оборудования и др.) или самотеком (при гидравлической и твердеющей закладке).
- При отработке маломощных рудных тел допускается закладывать выработанное пространство породой, добываемой из выработок, проходимых специально для этих целей в висячем или лежачем боку (горные мельницы).
- Очистные работы при системе горизонтальных слоев с закладкой начинать с выемки подсечного слоя от восстающих и рудоспусков.
- Если устойчивость руды и вмещающих пород не позволяет осуществлять одновременную подсечку слоя по всей площади блока, выемку руды вести вертикальными прирезками. В одновременной работе должно быть не более двух смежных прирезок. Отставание одной прирезки от другой по вертикали должно обеспечивать безопасность работы.
- При сухой и гидравлической закладке на почве подсечного слоя или над крепью штрека делать плотный настил. При твердеющей закладке применение настила не обязательно.
- При разработке маломощных рудных тел с устойчивыми рудами и вмещающим породами допускается частичное магазинирование руды.
- В случае применения сухой и гидравлической закладки на ее поверхности укладывать настил или слой бетона, исключающий возможность попадания отбитой руды в закладку и закладки в руду при отбойке и доставке руды к рудоспуску. В отдельных случаях, определяемых проектом, допускается работа без настила. Закладочный массив со стороны целиков (массива руды), должен быть изолирован для предотвращения высыпания закладки из выработанного пространства при выемке смежного блока или целика.
- При использовании самоходного оборудования высоту (ширину) очистного пространства определять проектом в зависимости от типа применяемого оборудования и средств контроля за состоянием очистного пространства.
- Во избежание обрушения кровли очистных забоев при выемке последних слоев под выработанным и заложенным блоком (камерой) очистное пространство отрабатываемых слоев необходимо крепить. Выемку последних слоев в рудах средней устойчивости в основном следует производить прирезками, перпендикулярными к длинной оси блока (камеры) с креплением и полной закладкой. При устойчивых рудах выемку верхних слоев можно производить в отступающем порядке по длине блока (камеры).
- При выемке последнего слоя в блоке настил, на котором находится закладка вышележащего отработанного блока, должен подхватываться крепью, чтобы закладка не прорывалась в рабочее пространство. При перепуске закладки из вышележащего блока не допускать смешивания руды с породой.
Требования к системам с камерной выемкой и закладкой:
|
|
- Систему с камерной выемкой руды с последующей закладкой выработанного пространства рекомендуется применять для сплошной отработки рудных тел средней и выше средней мощности с любым углом падения, при рудах и вмещающих породах, обеспечивающих устойчивость камер в период очистной выемки и закладки. Систему применять при разработке пожароопасных месторождений или ценных руд, а также при необходимости сохранения поверхности.
- Блок (очистную панель) вынимать несколькими камерами в определенной последовательности, обеспечивающей полноту выемки руды и сохранность массива налегающих пород. Количество камер в блоке, их параметры, последовательность отработки и закладки определяются проектом в зависимости от конкретных горнотехнических условий.
- В зависимости от устойчивости руд и вмещающих пород очистную выемку в камерах вести одной из систем с открытым выработанным пространством или с магазинированием руды. При этом руководствоваться требованиями, предъявленными к этим системам.
- При применении твердеющей закладки рекомендуется производить отбойку руды глубокими скважинами уменьшенного диаметра. Расположение скважин, порядок, взрывания и масса одновременно взрываемого заряда ВВ должны исключать откольные явления в закладочном массиве.
- При применении твердеющей закладки допускается выемка камер без оставления междуэтажных (междупанельных) целиков.
- При применении твердеющей закладки стенки камер должны быть относительно ровными и вертикальными с тем, чтобы обеспечить максимальное извлечение руды и минимальное ее разубоживание при отработке смежных камер.
27. Закладочные материалы, изготовление и способы транспортирования.
28. Технология закладки.
Представленная классификация закладки основана на различиях, связанных с количеством воды (%), используемым в процессе приготовления, транспортирования и укладки закладочной смеси. По этому признаку выделяются три класса закладки: сухая, пульповая и водная.
По нарастанию содержания воды, участвующей в процессах транспортирования и формирования, определены группы закладки в указанных классах (табл. 5.3).
Сухая закладка представлена следующими группами: породной; бутовой, имеющей воду в растворах для кладки; консолидированной, предполагающей обработку водой или химическими растворами; инъекционной — породной, обработанной инъекционными растворами.
Практически консолидированную, инъекционную и льдопородную закладки можно определить как комбинированные технологии.
Пульповую закладку можно разделить на группы, используя различия в плотности раствора при его транспортировании, а как уточняющий признак — определить наличие вяжущего и его вид. Водная закладка предполагает намораживание закладочного массива . По способу подачи закладочного материала в выработанное пространстве различают самотечную, механическую, пневматическую закладку.
При самотечном способе подачи закладочный материал заполняет выработанное пространство камеры под действием собственной массы сверху, как в бункер. При этом используются: вмещающие породы, получаемые попутно при проведении полевых подготовительных и вскрывающих выработок; породы, специально для этого добываемые на поверхности и спускаемые под землю; породы, выделенные из рудной массы при подземной предконцентра-ции (породоотборке). Иногда закладочный материал получают из камер, создаваемых в контактирующих с рудным телом вмещающих породах. Самотечная закладка — самый дешевый вид закладки, но она имеет и существенный недостаток: значительную (до 20—35 %) усадку закладочного материала.
При сухой закладке закладочный материал размещают в выработке под действием собственной массы либо при помощи машин механического действия. Для заполнения пространства, как правило, используют пустую породу от проведения выработок. В перспективе эта технология будет применяться как составная часть при бутовой закладке и при возведении искусственных массивов инъекционным способом, а также при формировании монолитного массива под действием нагрузок или других физических процессов при консолидированной закладке.
Сухую закладку могут распределять в выработанном пространстве механическим способом. Как правило, эту технологию применяют при отработке очистного блока горизонтальными или слабонаклонными слоями, начиная с нижнего. В выработанное пространство закладочный материал поступает самотеком по восстающим. Для распределения по выработанному пространству используют скреперные установки или самоходное оборудование. Коэффициент усадки механической закладки тоже сравнительно высок (до 15-—25 %), под кровлей остается незаполненное пространство высотой не менее 0,5—1 м.
На отдельных рудниках при механическом способе применяют конвейеры и метательные машины. Однако из-за очень жестких требований к крупности и абразивности закладочного материала, необходимости частых перестановок конвейера или его секций и небольшой дальности метания закладочных машин эти виды механической закладки широкого распространения не получили.
При пневматическом способе подачи для перемещения закладочного материала по трубам и забрасывания его в выработанное пространство используется энергия сжатого воздуха. Закладочным материалом служат дробленые неабразивные породы крупностью от 5—8 до 60—80 мм с примесью 10—15 % глины. На рудниках обычно применяют переносные пневмозакладочные машины, которые перемещают закладочный материал по трубопроводу на сравнительно небольшое расстояние (до 50—70 м), а иногда только забрасывают его в выработанное пространство на 10—15 м (чуть дальше метательных машин). Достоинством пневмозакладки является небольшая усадка (до 10—15 %). К ее недостаткам можно отнести: весьма значительный износ трубопровода и деталей закладочных машин; сильное пылеобразование; требования к качеству закладочного материала и высокий расход сжатого воздуха (около 150 м"7м3 закладочного материала).
При бутовой закладке используют каменные блоки различного размера и скрепляют их вяжущим раствором (аналогично с кирпичной кладкой). Бутовая закладка применяется на глубоких и сверхглубоких рудниках. Заполняют не все выработанное пространство, а лишь участки, граничащие со смежными блоками, а в оставшуюся часть блока подают породную закладку. Достоинство бутовой закладки — сокращенный до минимума расход воды, что имеет большое значение для снижения относительной влажности рудничной атмосферы. Недостаток — сложность механизации работ.
При консолидированной закладке формируется монолит под воздействием пара или других реагентов на уже размещенную в очистном пространстве сухую закладку.
При инъекционной закладке происходит предварительное заполнение выработанного пространства сухой закладкой в результате проводимых закладочных работ или дробленой породой от самообрушения очистной камеры, а затем производится подача по трубам с поверхности вяжущего раствора. Раствор проникает в пустоты дробленой породы и превращает ее в монолит. Как правило, монолит, образованный таким способом, имеет незначительную прочность. 534
Раствор обычно подают иод давлением 1—1,5 МПа снизу вверх, т.е. методом восходящего потока. Радиус распространения инъекционного раствора в сыпучей закладке достигает 10 м, а иногда и более. Делаются попытки подавать раствор самотеком (сверху вниз) при крупнокусковой самотечной неуплотнившейся закладке.
Достоинства инъекционного способа закладки:
• благоприятные условия трубопроводного транспортирования пульпы;
• возможность прекращения процесса дальнейшего обрушения пород;
• использование для закладки шахтной породы без выдачи ее на поверхность и дополнительного дробления.
Недостатки инъекционного способа закладки:
• сложность управления распространением раствора в сыпучей среде;
• неравномерная прочность участков закладочного массива. Инъекционный способ имеет перспективы для применения в
различных условиях:
• восстановление устойчивости пород, что имеет значение при выемке руды под охраняемой территорией. Это — единственный надежный способ ликвидации последствий самообрушений;
• использование при зонном омоноличивании массива для выемки междукамерных целиков.
Применение постовой закладки началось в середине 80-х гг. XX в. Для обеспечения хорошей транспортабельности данного вида закладки используют фракции минеральных отходов с хорошими коллоидными свойствами, удерживающие воду в количестве, достаточном для цементации закладки. В составе пасты желательно наличие не менее 15 % фракций, размер которых не превышает 20 мкм.
Паста — материал, который содержит воду в поровом пространстве в количестве, достаточном для обеспечения его текучести. При транспортировке пасты по трубопроводу поток разделяется на две фазы: твердую и жидкую, причем жидкая фаза располагается по его периферии. Отметим, что коллоидные свойства пасты могут регулироваться и при помощи химических добавок. Пастовая закладка применяется с добавлением вяжущих компонентов. В их отсутствии она подвержена разжижению и может оставаться в таком состоянии продолжительное время.
Твердеющая закладка — смесь с водой различных вяжущих материалов и заполнителя, способных твердеть как бетон. Предел прочности твердеющей закладки обычно невысокий и равен 1,5— 10 МПа. В состав ее входят песок (песковидные хвосты обогащения), щебень, цемент или другие вяжущие вещества (например, специально обработанные шлаки). Свежеприготовленная смесь имеет жидкую консистенцию и может подаваться в выработанное пространство по трубам как гидравлическая закладка.
Расход вяжущего составляет 100—400 кг/м3. Себестоимость твердеющей закладки с использованием цементного вяжущего высока. Поэтому ее снижают, используя более дешевые вяжущие из местных материалов, добавляя к ним цемент для повышения гидравлической активности. Так, на Гайском руднике для твердеющей закладки используют смесь из молотого доменного шлака (360 кг/м3), цемента (40 кг/м3) и песка с примесью 30 % глины (1200 кг/м3), что существенно снижает себестоимость закладочной смеси. Глина в закладочную смесь добавляется в качестве пластификатора, который улучшает реологические свойства смеси и улучшает транспортабельность.
Закладка достигает нормативной (необходимой в данных горно-технических условиях) прочности в период от нескольких дней до нескольких недель. Нормативная прочность затвердевшего закладочного массива относительно небольшая (2,5—7 МПа), но устойчивость его весьма высока. Горизонтальный пролет обнажения закладочного массива без крепления составляет 3—8 м, что позволяет вести очистную выемку слоями сверху вниз под прикрытием искусственной кровли из затвердевшей закладки. Вертикальные устойчивые обнажения закладки достигают площади 50x50 м2 и более.
Существуют различные схемы приготовления и транспортирования твердеющих закладочных смесей, одна из них представлена на рис. 5.34.
При значительных объемах закладочных работ строится центральный закладочный комплекс на поверхности с трубопроводным транспортом литой гидросмеси до мест укладки в очистные блоки. Самотеком гидросмесь может перемещаться на расстояние по горизонтали, в 3—4 раза превышающее вертикальный столб смеси в трубопроводе. При больших расстояниях транспортирования через 50—60 м по длине в 1рубопровод врезаются форсунки сжатого воздуха, обеспечивающие пульсирующий пневмотранспорт гидросмеси. Диаметр труб 150—200 мм, толщина стенок 8—12 мм. Время пребывания смеси в трубопроводе не должно превышать 1 ч. Если объемы закладочных работ на руднике менее 30—50 тыс. м3/год, то применяют и подземные закладочные комплексы, обычно участковые.
Используется и раздельный способ подачи твердеющей закладки, когда вяжущий раствор и заполнитель (дробленую породу) подают к месту закладочных работ раздельно и смешивают их в процессе подачи в выработанное пространство. Твердеющая закладка — наиболее дорогостоящий способ, однако использование ее позволяет вести сплошную выемку руды с минимальными потерями. Поэтому ее применяют при разработке ценных руд, при необходимости сохранения целостности налегающей толщи пород или в условиях повышенного горного давления.
Рис. 5.34. Технологическая схема закладочного комплекса для приготовления твердеющей смеси:
/ траншейный склад для гранулированного доменного шлака; 2 — загрузочные
бункера; 3 — конвейер: 4 — шаровая мельница; 5 — насосы; 6 — гидроциклоны; 7 — вакуум-фильтр; 8 — склад цемента; 9 — смеситель; 10 — закладочный трубопровод; // — весы; 12 — склад заполнителя
Твердеющая закладка широко распространена на подземных рудниках. Применение ее позволяет:
• разрабатывать месторождения комбинированным способом;
• отрабатывать руды, склонные к самовозгоранию;
• сохранить поверхность от деформаций под водоемами и городами;
• отрабатывать ранее оставленные целики ценных руд, в том числе даже запасы руды в охранных целиках стволов шахт;
• осуществлять опережающую выемку очень ценных руд практически без всякого нарушения окружающих более бедных руд, что позволит в будущем достаточно эффективно отработать и эти бедные руды.
При гидравлической закладке смесь раздробленного материала с водой (пульпа) перемещается к выработанному пространству по трубам и растекается по нему (рис. 5.35.). Вода через фильтрующие перемычки дренирует из закладочного массива и откачивается на поверхность. Максимальный размер кусков закладочной смеси составляет 50—70 мм. Объем мельчайших (глинистых) частиц крупностью менее 0,05 мм не должен превышать 10—15 %, так как иначе закладочный массив будет очень плохо отдавать воду. При приготовлении пульпы для гидрозакладки ранее применяли естественные пески с небольшой примесью глины, гранулированные доменные шлаки или, реже, дробленые скальные породы. В последнее время чаще используют хвосты обогатительных фабрик, обезвоженные и обесшламленные.
Трубопроводы при гидрозакладке собирают из толстостенных (с толщиной стенки 8—10 мм) стальных труб, имеющих быстроразъ-емные соединения. Закругления футеруют вкладышами из хромни-келевой или марганцевистой стали, а иногда из литого базальта, плотной резины и других износоустойчивых материалов.
Закладочный массив намывают по площади слоя с помощью резинового шланга, соединенного с трубопроводом. Пульпа растекается в выработанном пространстве под углом от 5 до 15° к горизонту. В примыкающих к выработанному пространству горных выработках устанавливают перемычки (фильтрующие или глухие). Для улучшения дренажа в закладываемом пространстве не-
Рис. 5.35. Схема гидрозакладочного комплекса:
/ гидромонитор; 2 — бункер; 3 — смесительный лоток; 4 — закладочный трубопровод; 5 — выработанное пространство; 6 — фильтрующие перемычки; 7 — выработки с водосточными канавками; 8 — водосборник; 9 — насосы; 10 — водопровод; 11 — водоотстойник; 12 — трубопровод для подачи осветленной воды
редко устанавливают также дренажные фильтры — обтянутые мешковиной перфорированные трубы (деревянные или металлические). Гидравлическая закладка отличается высокой производительностью, хорошим заполнением всех пустот и сравнительно небольшой усадкой закладочного массива (8—12 %). К н е д о с-таткам этого вида закладки можно отнести загрязнение и обводнение горных выработок, а также высокие капитальные затраты на комплекс по приготовлению пульпы, трубопровода и водоотлива.
Льдозакладка (или ледяная) имеет основное достоинство — невысокую себестоимость, но в то же время есть существенный недостаток — снижение несущей способности при длительном нагружении. Армирование льда дробленой породой (льдо-породная закладка) ускоряет процесс намораживания и повышает прочность закладочного массива.
Льдопородная и льдозакладка возводятся методом слоевого намораживания льда с заполнителем или одного льда путем подачи закладочного материала и холодного атмосферного воздуха, нагнетаемого в закладочное пространство вентиляторами. Использование таких способов закладки возможно только в условиях многолетней мерзлоты.
При использовании химических растворов в процессе закладки выработанного пространства первоначально производится укладка химически активной породы, которая может вступить в реакцию с ними. Затем подают химические растворы реагентов, которые вступают в реакцию с минералами, содержащимися в породе, происходит их растворение. Через определенное время происходит повторная кристаллизация, что позволяет консолидировать породу в выработанном пространстве. Такая закладка обладает достаточно высокими прочностными характеристиками, которые сохраняются при длительном нагружении.
29. Системы разработки горизонтальными слоями с закладкой.
Система разработки горизонтальными слоями с закладкой. Блок вынимают горизонтальными слоями, начиная с нижнего. Отработанный слой закладывают, оставляя свободным только рабочее пространство. Руду отбивают на поверхность закладки и доставляют по ней механизированным способом.
Условия применения: мощность и угол падения залежи — любые; устойчивая руда; боковые породы крутых залежей — неустойчивые (при устойчивых породах обычно применение системы нецелесообразно). Наиболее часто система применяется при высокой ценности руды, при возгорающейся руде или необходимости сохранения поверхности.
Параметры. Оптимальная высота этажа в крутых и наклонных залежах определяется по минимуму затрат (1.4) с учетом затрат на проходку и поддержание выработок (включая рудоспуски) и затрат на доставку материалов и оборудования.
Высота этажа колеблется от 35 до 60 м в крутых залежах, длина блока при разработке по простиранию от 30 до 100 м. При разработке вкрест простирания ширина камер 5—12 м, целиков 5—10 м.
В вариантах с сыпучей закладкой (рис.10.2) маломощные крутые залежи отрабатывают блоками по простиранию, а мощные крутые и пологие рудные тела отрабатывают в две стадии: камеры — горизонтальными слоями с закладкой, целики — другими системами.
Рис. 10.2. Варианты системы разработки горизонтальными слоями с сухой закладкой: а – с доставкой руды самоходным оборудованием; б – с доставкой руды скрепером; 1 – откаточный штрек; 2 – блоковый восстающий; 3 – вентиляционный восстающий; 4 – закладочный восстающий; 5 – вентиляционно-закладочный штрек; 6 – скреперная установка; 7 – ПДМ; 8 – бетонный настил; 9 – самоходная буровая установка.
Очистная выемка начинается с уровня кровли штрека. Над штреком иногда оставляют целик толщиной 2—5 м. Отбойка руды обычно шпуровая, доставка механизированная в рудоспуски. Широко используют самоходное оборудование. На поверхности сухой закладки устраивают настил. Иногда руду и закладку доставляют конвейерами. Высота слоя 2—3 м, при устойчивых рудах и боковых породах 4,5—5 м, высота открытого пространства достигает 7—8 м. Шпуры бурят вверх под углом 70° самоходными бурильными установками. Кровлю выравнивают контурным взрыванием горизонтальных шпуров. По окончании доставки руды из слоя разбирают настил, иногда зачищают в рудоспуск верхнюю часть закладки, обогащенную рудной мелочью.
Широко применяют гидравлическую закладку обесшламленными хвостами обогатительных фабрик или природным песком (рис.10.3). При малоустойчивых боковых породах между кровлей забоя и закладкой оставляют пространство высотой 0,4—0,5 м, а при более устойчивых породах 1,5—3 м.
Рис. 10.3. Система разработки горизонтальными слоями с гидрозакладкой и бетонным настилом: 1 – блоковые восстающие; 2 – рудоспуски и ходовые восстающие в два отделения; 3 – пульпопровод; 4 – гидрозакладка; 5 – бетонный настил; 6 – дренажная труба
В закладке по мере повышения ее поверхности наращивают рудоспуски из стальных труб. Иногда рудоспуски выкрепляют каменной кладкой на цементном растворе или железобетонными кольцами. Расстояние между рудоспусками 20—60 м при скреперной доставке руды и до 100 м и более при доставке самоходными машинами. Настил сверху закладки укладывают в каждом слое из металлических листов, деревянных щитов или старых конвейерных лент; иногда покрывают его брезентом. На ряде рудников делают бетонные настилы толщиной 15—20 см, торкретируя закладку жидким раствором быстросхватывающегося бетона. Бетонный настил вдвое дешевле деревянного и через двое суток позволяет работать на самоходном оборудовании. При отсутствии или недостаточной плотности настила потери металла в закладке достигают 20 %.
30. Системы разработки наклонными слоями с закладкой.
Система разработки наклонными слоями с закладкой. Выемку руды ведут наклонными (под углом до 40°) слоями (рис. 10.4); руда и закладочный материал перемещаются в очистном пространстве преимущественно под действием силы тяжести. Закладка возможна лишь сухая.
Условия применения: устойчивая руда; малоустойчивые боковые породы; мощность залежи любая; угол падения не менее 60—70°; правильные контуры залежи; ценная руда. В связи с внедрением самоходного оборудования применяют сплошную выемку. В этом случае (см. рис. 10.4, а, б) забой продвигают по длине этажа. Восстающий в этаже требуется только разрезной. Отбойка шпуровая. Руду, скатывающуюся по откосу, грузят и отвозят самоходным оборудованием. Закладку доставляют до откоса самоходным оборудованием.
Рис.10.4. Система разработки наклонными слоями с закладкой: а—вариант со сплошной выемкой и самоходным оборудованием, стадия закладки; б — то же, стадия доставки руды (1 - самоходный вагон; 2 - настил; 3 - ПДМ); в — вариант с выемкой блоками, разрез по простиранию, проекция на вертикальную плоскость (1,2-откаточный и вентиляционный штреки; 3 – блоковый восстающий для спуска закладки; 5- граница подштрекового целика; 6 - граница выемки слоями постоянной длины)
При выемке блоками (см. рис. 10.4, в) закладку на откос подают из восстающего. В блоке сначала вынимают треугольники в основании, а затем наклонные слои постоянной длины (основная стадия), после чего погашают треугольную потолочину.
При твердеющей закладке на очистных работах обычно используют самоходное оборудование. При большой протяженности залежей проводят уклон для заезда самоходного оборудования на все слои. Высота этажа на отдельных зарубежных рудниках достигает 250 м, длина блока 300 м и более. Выемка чаще сплошная.
На рудниках Норильского комбината, эксплуатирующих месторождения на большой глубине, систему применяют при сплошной выемке с использованием самоходного дизельного оборудования. Залежь отрабатывают от центра к флангам, забой пересекает всю залежь по длине (рис. 10.5). Перпендикулярно линии забоя пройдены полевые откаточные штреки, которыми нарезаны панели шириной 120—150 м по условию использования ПДМ. Панель разделяют на вертикальные секции шириной 6—8 м, которые вынимают горизонтальными слоями высотой 3 м.
Вентиляционный горизонт имеет ту же схему подготовки, что и откаточный. Рудоспуски, выкрепляемые в закладке, располагают в каждой второй секции. С каждой стороны залежи имеется уклон от откаточного горизонта до ее почвы. Рудный штрек пройден по всей длине залежи. Из рудного штрека в каждой панели проходят уклон до кровли залежи, из которого нарезают заезды на слои. На очистных работах используют дизельные бурильные установки на 2—3 перфоратора и самоходные погрузочно-доставочные машины производительностью 500—600 т/смену. Слой закладывают участками длиной 40—60 м, твердеющую смесь подают с вентиляционного горизонта по скважине диаметром 300 мм.
Производительность труда забойного рабочего 60—80 т/смену обеспечивает высокую концентрацию горных работ, расход подготовительно-нарезных выработок 2 м на 1000 т.
Технико-экономические показатели системы: при крепкой руде в месторождениях средней и большой мощности производительность блока (камеры, секции) составляет 1500—3000 т/мес и достигает 6000 т/мес при использовании самоходного оборудования; производительность труда забойного рабочего 15—80 т/смену и более при твердеющей закладке и самоходном оборудовании; расход крепежного леса до 0,01—0,02 м3/т; потери руды при плотном настиле или твердеющей закладке 1—5 %; разубоживание руды от 1—3 до 10 % при неправильных контурах; расход подготовительно-нарезных выработок 2—5 м на 1000 т. Экономическое сравнение с другими системами разработки можно вести по условию максимизации дохода (1.3).
Рис. 10.5. Система разработки горизонтальными слоями с закладной – вариант с твердеющей закладкой и сплошной выемкой (Норильский комбинат): а – схема вскрытия и подготовки и порядок отработки месторождения (1 – рабочее пространство; 2 – воздухоподающий ствол; 3 – рудопоъемный ствол; 4 – воздухоотводящие стволы; 5 – главный откаточный штрек; 6 – блоковые восстающие; 7 – закладочный горизонт; 8 – границы выемочных лент; 9 – закладка; 10 – границы слоев; 11 - слой): б – отработка панели (1 – откаточный штрек; 2 – штрек для сообщения с панелями; 3 – вентиляционно-закладочные восстающие; 4 – рудоспуски; 5 – уклон; 6 – заезды на слой; 7 – скважины для подачи закладки; 8 – вентиляционно-закладочные штреки
31. Системы разработки тонких жил с раздельной выемкой и закладкой.
Система разработки тонких жил с раздельной выемкой. Отработка жил ведется с подрывкой вмещающих пород (рис. 10.6). Боковые породы отбивают отдельно и оставляют в выработанном пространстве в качестве закладки.
Руда может быть устойчивой и пониженной устойчивости. Контакты жил должны быть четкими и правильными. Благоприятна различная крепость руд и боковых пород. Руда должна быть весьма ценной.
При крутом падении подрабатывают бок жилы со стороны более четкого и правильного контакта. С опережением на слой отбивают или руду, если она слабее, или пустую породу. Шпуры применяют уменьшенного диаметра, а при малой крепости руды заряды в шпуре рассредоточивают.
При большей выемочной мощности или при мощности жилы менее 0,3 м получается избыток отбитой породы, который выдают из блока.
Рудоспуски в закладке выкрепляют металлическими трубами диаметром 300—500 мм или деревянными трубами диаметром около 700 мм.
При устройстве деревянного настила на закладку укладывают доски, на них парусину или пластик, а сверху опять доски для защиты парусины. Производительность труда рабочего на укладке деревянного настила 10 м2/смену. После уборки руды счищают с парусины рудную мелочь в рудоспуски и снимают обогащенный верхний слой закладки (20—30 см). Иногда устраивают бетонный настил.
В пологих залежах блок разрабатывают по восстанию. Руду к рудоспускам доставляют скреперами, конвейерами (скребковыми, иногда передвижными пластинчатыми).
При мощности крутой жилы около 0,3 м производительность блока составляет 100—200 т/мес; производительность труда забойного рабочего 0,8—2 т/смену, редко 3—4 т/смену; расход крепежного леса 0,008—0,04 м3/т; потери руды 7—15%; разубоживание 15—20%; расход подготовительно-нарезных выработок 20—40 м на 1000 т.
32. Нисходящие системы послойной разработки с закладкой выработанного пространства.
Нисходящая слоевая выемка с твердеющей закладкой. Система применяется для выемки неустойчивых ценных руд, особенно при высокой их возгораемости или при необходимости поддержания земной поверхности. Крутые залежи могут быть любой мощности, пологие должны иметь мощность не ниже средней. Вмещающие породы могут быть любой устойчивости.
Блок отрабатывают слабо наклонными слоями, начиная с верхнего (рис. 10.7). Слои вынимают заходками, которые затем заполняют твердеющей закладкой. Работы ведутся под защитой закладочного массива.
Высота слоя 3—4 м, ширина заходок 3,5—7 м в зависимости от устойчивости кровли, представленной закладочным массивом. Наклон заходок (4—10°) немного превышает угол растекания закладочной смеси.
На бурении и доставке руды используют преимущественно самоходное оборудование легкого типа. При запасе залежи менее 30—50 тыс. т предпочтительнее скреперная доставка руды.
Закладочную смесь подают по трубам по возможности без перерывов для получения монолитного закладочного массива. На границе с заложенной заходкой работы начинают через 5—7 сут, а снизу через две недели.
Рис. 10.7. Нисходящая слоевая выемка с твердеющей закладкой
На глубинах 500—1000 м и более вести выемку без крепления заходок можно лишь при увеличенной прочности закладочных смесей и при образовании в нижней части слоя железобетонной конструкции за счет укладки в заходку металлических элементов перед заполнением ее закладочной смесью. Эти элементы могут быть подвешены к металлическим лежням вышележащего слоя.
При разработке небольших обособленных залежей руд средней крепости с применением легких ПДМ и площади блока 1000—1500 м2 производительность блока составляет 7—10 тыс. т/мес; производительность труда забойного рабочего 30—60 т/смену; расход подготовительно-нарезных выработок 8—12 м на 1000 т; потери руды 3—5 %, разубоживание 8—10 %.
33. Камерные системы с закладкой выработанного пространства
34. Системы разработки со сплошной однослойной выемкой руды и закладкой.
Однослойная выемка с закладкой. Систему применяют преимущественно при невозможности обрушения поверхности в пологих и наклонных залежах мощностью до 4—5 м, устойчивость руды может быть любой, породы висячего бока должны быть устойчивыми. Ценность руды высокая или средняя.
При использовании твердеющей закладки вынимают руду заходками, рудная стенка заходки играет роль опалубки. При сыпучей закладке выемку можно вести забоем-лавой по всей ширине панели.
Отбивают руду шпурами или скважинами уменьшенного диаметра. Доставляют руду самоходным оборудованием или скреперами, а в забое-лаве используют скребковый конвейер или многоковшовое скреперование. Вслед за выемкой закладывают выработанное пространство.
К этой системе условно можно отнести вариант с креплением призабойного пространства. Применяется при мягких рудах и неустойчивой кровле. Выемку ведут забоем-лавой, в горный комплекс входят комбайн для механической отбойки и передвижная механизированная крепь. Позади крепи выработанное пространство закладывают.
Системы этой группы находят ограниченное применение при выемке горизонтальных и пологопадающих месторождений небольшой мощности – 3-4 м.
Крепость и устойчивость руд могут быть любыми, вмещающие породы висячего бока сравнительно устойчивые, обрушение поверхности недопустимо.
Размеры блоков зависят от физико-механических свойств руды и вмещающих пород, способа транспортирования руды. Длина блоков 50-100 м. Размеры блоков по восстанию зависят от угла падения залежи и принятой высоты этажа.
Отбойка руды осуществляется буровзрывным способом. При транспортировании руды используют скреперные установки, конвейеры или ПДМ. При использовании сухой или гидравлической закладки выемку ведут широким забоем-лавой, а при твердеющей закладке —заходками.
![]() | ![]() |
В качестве временной крепи используются металлические стойки. На Урупском руднике проведены испытания варианта системы со сплошной выемкой, передвижной механизированной крепью и гидравлической закладкой выработанного пространства (рис. 10.1).
Рис. 10.1. - Вариант системы разработки лавой по восстанию механизированным комплексом с гидрозакладкой:
![]() |
1— откаточный штрек; 2— блоковые вентиляционно-ходовые восстающие; 3— скреперные установки; 4 — закладочный трубопровод; 5 — лебедка для передвижения механизированного комплекса; 6 — механизированная передвижная крепь; 7 — передвижная скреперная установка
При отработке блоков лавами закладочную смесь подают в выработанное пространство вслед за очистной выемкой с отставанием от забоя на 4—6 м с предварительным возведением изолирующей передвижной опалубки.
Достоинствами этой системы являются широкий фронт очистных работ, возможность раздельной выемки и сортировки руды и одностадийность отработки блока.
35. Система разработки с креплением и закладкой очистного пространства.
36. Классификация систем разработки с обрушением вмещающих пород. Характеристика и условия применения
При системах с массовым обрушением (сокращенное название) очистное пространство поддерживается только в период образования камер или щелей для обрушения основной части блока. Отбойка преимущественно скважинная, иногда самообрушением.
В связи с обрушением пород отработка залежей ведется в нисходящем порядке.
Системы применяют в мощных и средней мощности залежах, если не требуется поддержание земной поверхности. Ценность руды ограничена в связи с повышенными ее потерями.
Наличие глин и песков в обводненной толще насосов исключает применение систем из-за опасности, образования плывуна и прорыва его в горные выработки.
При большой глубине разработки (700—1200 м и более), особенно при пологом падении залежи, обрушение висячего бока отстает от выемки, в результате возрастает опорное давление, возникает опасность возникновения породных взрывов и горных ударов.
Обрушение вмещающих пород. Породы могут обрушаться со стороны висячего бока, сверху и со стороны лежачего бока.
Отставание обрушения пород висячего бока от выемки руды возрастает с устойчивостью пород, с уменьшением пролета обнажения по простиранию залежи и с глубиной разработки. Обычно общее обрушение висячего бока отстает на 1—2 этажа, а в залежах малой длины по простиранию на глубоких горизонтах оно может вообще не произойти. Тогда образуются обширные пустоты или в выработанное пространство опускаются обрушенные породы из верхних этажей. В случае внезапного обрушения пустот возникают воздушные удары, приводящие к большим разрушениям. Возможно разрушение оснований блоков ударом падающей массы пород. Рост опорного давления в соседних блоках может привести к разрушению массива руды и выработок.
Предотвращение воздушных ударов. Для гашения воздушной волны над выпускными выработками создают породную подушку (слой раздробленных пород) путем принудительного обрушения части пород кровли или временного оставления отбитой руды (рис.7.1).
При обрушении пород кровли минимально необходимая толщина предохранительной подушки
,
где — высота очистного пространства блока от его основания до кровли, м
(рис. 7.1); к—коэффициент пропорциональности
,
где, — коэффициент, учитывающий аэродинамическое сопротивление предохранительной подушки; k 2 — то же, обрушающихся пород и рудовыпускных выработок;
— коэффициент, учитывающий прочие факторы и резерв.
,
где f — коэффициент крепости пород; dcp— средневзвешенный диаметр куска пород, слагающих подушку, м.
Рис. 7.1. Схема к расчету толщины подушки h п : Нпад — высота падения обрушающихся пород; Нбл — высота очистного пространства в блоке; Нобр —высота слоя породы, обрушаемой для образования подушки; h р.п — толщина рудной подушки; h п.п — толщина породной подушки
,
где S — площадь блока, м2; п — число выпускных отверстий в блоке; s — площадь выпускного отверстия, м2; а, b , с — эмпирические коэффициенты, учитывающие характер обрушения (а = 0,36; b = 0,0004 и c = 1, если обрушение пород не выйдет за пределы свода естественного равновесия, а также при обрушении потолочины, на которой лежат раздробленные породы, а = 0,90; b = 0,001 и с= 1,7, если не исключена возможность мгновенного полного самообрушения налегающих пород с выходом воронки провала на земную поверхность); учитывает неравномерность толщины и диаметра среднего куска пород подушки по площади блока. Его можно принимать равным 1,3 при условии, что толщина подушки и диаметр среднего куска изменяются не более чем на 20 %.
При обычном значении kр = 1,35
,
Толщина слоя пород, подлежащего обрушению для образования подушки,
,
Для подушки из отбитой руды
,
Если по соседству имеется блок, подлежащий последующему массовому обрушению, то толщина подушки должна быть не меньше высоты этого блока, иначе часть руды будет выброшена на породную подушку и потеряна.
Рис. 7.2. – Породная подушка 1, граничащая с подлежащим обрушению соседним блоком 2: а – вид до обрушения блока; б – вид после обрушения; 3 – скважинные заряды для образования подушки в соседнем блоке.
Обрушают породы скважинами или сосредоточенными зарядами. Если устойчивые породы в кровле залегают в виде слоя, то взрыванием зарядов его достаточно отрезать от массива по границам посадки. Аналогичная схема посадки возможна при наличии в кровле пологих трещин. При развитой вертикальной трещиноватости возможно обрушение пучком из двух-трех вееров горизонтальных и слабонаклонных скважин или одним минным ярусом (рис. 7.3.).
Рис. 7.3. – Схемы обрушения пород над пологой залежью: а – самообрушение при средней устойчивости пород; б, в – сосредоточенными зарядами и скважинами при устойчивых породах; г – сосредоточенными зарядами при наличии над залежью прослоя 1 устойчивых пород; д – сосредоточенными зарядами при крепких породах с вертикальными крутыми трещинами; е – опережающая выемка верхнего слоя руды при самообрушении пород.
Метод обрушения кровли должен выбираться в комплексе с толщиной подушки и параметрами отбойки, от которых зависит кусковатость обрушенных пород. В общем случае, чем ниже затраты на обрушение пород, и, следовательно, меньше эти породы будут раздроблены, тем толще нужна подушка и больший объем пород требуется обрушить одним минным ярусом.
Снижение опорного давления. Главная мера предосторожности против опорного давления — своевременное обрушение подработанной толщи за счет увеличения площади обнажения или принудительным способом.
Полное обрушение пород до земной поверхности вслед за выемкой при глубинах разработки более 100—200 м практически неосуществимо. Обычно обрушается лишь нижняя часть налегающей толщи, а высота этой толщи уменьшается незначительно. Вместе с тем, опорное давление, передаваемое на массив через слой обрушенных пород, распределяется на увеличенную площадь, что снижает концентрацию напряжений на определенное время (до нескольких месяцев), в зависимости от реологических свойств пород.
37. Слоевое обрушение с выемкой руды заходками.
Слоевое обрушение. Очистные работы ведут под защитой искусственной кровли, опускающейся под давлением налегающих обрушенных пород по мере выемки руды. Это дает возможность отрабатывать неустойчивые руды.
В системе слоевого обрушения можно выделить две разновидности: с креплением рамами или стойками; с гибким перекрытием.
В системе слоевого обрушения можно выделить две разновидности: с креплением рамами или стойками; с гибким перекрытием.
Рис.11.5. Забой-лава при обособленной двухслоевой выемке калийных пропластков (план):1 — забой верхнего слоя; 2—забой нижнего слоя; 3—конвейерный штрек; 4—вентиляционный штрек; 5—крепь сопряжения 2М81Э; 6 — гидравлические стойки ГСК; 7 — костры из круглого леса; 8 — передвижные эстакады. Крестиками показан пропласток каменной соли
Рис. 11.6. Забой-лава при валовой выемке калийных пропластков - вариант с комплексом КМ-81 (план): 1 - конвейерный штрек; 2 - вентиляционный штрек; 3 -крепь 2М81Э; 4- комбайн КШ-ЗМ; 5 - конвейер КМ-81-02Б; 6-крепь сопряжения 2М81Э; 7 - гидростойки ГСК; 8 - промежуточный конвейер СП-63
38. Столбовые системы разработки с обрушением кровли и выемкой столбов заходками.
Столбовая система разработки с обрушением. Система (рис) применяется в маломощных горизонтальных и пологих залежах с неустойчивыми налегающими породами. Вслед за выемкой руды передвигают крепь для поддержания очистного пространства у забоя, а позади непосредственная кровля обрушается.
Рис. 11.4 . Столбовая система с обрушением: а – выемка лавами; б – выемка заходками; 1 – основной штрек; 2 – основной вентиляционный штрек; 3 – выемочные штреки; 4 – сбойки; 5 – индивидуальная крепь; 6 щиты; 7 - комбайны
Шахтное поле разделяют штреками на прямоугольные блоки, называемые столбами. В отдельных случаях при небольшой площади залежи применяют сплошную выемку (одним столбом).
Столб отрабатывают обратным ходом по длине. По мере выемки механизированную крепь передвигают вслед за забоем, а индивидуальную извлекают.
При мощности залежи до 1,5—2 м и средней устойчивости кровли иногда обрушают взрывными скважинами слой кровли толщиной 3—4 м для заполнения обрушенными породами всего образовавшегося пространства.
Размеры столбов ограничены необходимостью обеспечения достаточно интенсивной его отработки и доставкой руды. Ширина столбов составляет 20—40 м и достигает 60—80 м при двухсторонней выемке. Длина столбов на металлических рудниках находится в пределах 50—100 м, на марганцевых шахтах — 300—750 м, на калийных рудниках — 1200—1500 м.
В Никопольском бассейне около 85 % руды доставляют конвейерами КЛЗС и Л-65, более 90 % руды погружают комбайнами МБЛ и погрузочными машинами ППН-1с.
Вариант с выемкой заходками применяется главным образом при слабой кровле. Длина столба примерно такая же, как и при выемке лавами, ширина 40—80 м при двухсторонней выемке и 20—40 м при односторонней. Ширина заходки 2,8—3,5 м.
В каждой панели очистные работы ведут в одном, двух или трех соседних столбах с опережением не менее 10—70 м.
В Никопольском бассейне руду с коэффициентом крепости 1—3 отбивают комбайнами МБЛМ и МБЛД, а доставляют ленточными конвейерами. Внедряют более производительные комбайны КМШ.
В Чиатурском бассейне применяется буровзрывная отбойка. Шпуры бурят колонковыми электросверлами. Руду в вагоны погружают машинами ЭПМ-1.
Заходки крепят металлическими или деревянными рамами через 0,7—1 м с затяжкой кровли и боков.
При мощности пласта менее 1,5 м подрывают породы почвы и оставляют их в выработанном пространстве или выдают из шахты.
При комбайновой выемке производительность столба 6000—9000 т/мес, производительность труда забойного рабочего — 17—20 т/смену. Объем подготовительно-нарезных работ 6—7 м на 1000 т. Расход металла при металлическом креплении 0,3—0,5 кг/т. Потери руды 10—12 %, разубоживание 2—7 %.
39. Столбовые системы с выемкой забоем – лавой
Рисунок и столбовая система на 38 вопросе
Вариант выемки лавами. Длина столба 300—800 м, ширина 50—80 м и более при комбайновой отбойке и конвейерной доставке или 20—30 м при буровзрывной отбойке и скреперной доставке (в более крепких рудах).
При мягких рудах и неустойчивой кровле используют механизированные комплексы ОКП. Между выемочными штреками в конце столба проходят выработку, в которой монтируют комплекс. Отбивают руду полосами толщиной 0,63 м на всю мощность пласта.
40. Системы разработки с обрушением руды и вмещающих пород. Характеристика и условия применения.
При системах с массовым обрушением (сокращенное название) очистное пространство поддерживается только в период образования камер или щелей для обрушения основной части блока. Отбойка преимущественно скважинная, иногда самообрушением.
В связи с обрушением пород отработка залежей ведется в нисходящем порядке.
Системы применяют в мощных и средней мощности залежах, если не требуется поддержание земной поверхности. Ценность руды ограничена в связи с повышенными ее потерями.
Наличие глин и песков в обводненной толще насосов исключает применение систем из-за опасности, образования плывуна и прорыва его в горные выработки.
При большой глубине разработки (700—1200 м и более), особенно при пологом падении залежи, обрушение висячего бока отстает от выемки, в результате возрастает опорное давление, возникает опасность возникновения породных взрывов и горных ударов.
Общие особенности систем с обрушением
Руду обрушают скважинами или сосредоточенными зарядами на полную высоту этажа и выпускают через выработки в основании блока.
Залежь должна быть мощной. Руды устойчивые и средней устойчивости, не слеживающиеся.
При возгорающейся руде эти системы разработки используют редко, причем профилактически заиливают обрушенное пространство.
Параметры системы. Оптимальную высоту этажа (блока) находят из условия (1.4) с учетом затрат: на проходку этажных выработок (в величинах k, с) и выработок для выпуска и доставки руды; на поддержание перечисленных выработок — при неустойчивых породах и большом горном давлении; на доставку материалов и оборудования; ущерба от потерь и разубоживания руды при выпуске.
Обычная высота этажа 70—80 м; при ограниченной мощности 20—30 м, при недостаточно крутом падении и неправильной форме залежей 45—60 м. В пологих залежах высота блока ограничивается мощностью залежи.
Ширина блока чаще соответствует мощности залежи, но не превышает 60—80 м. При большом горном давлении и не особенно крепкой руде ширина блока не должна превышать 40-50 м.
41. Системы подэтажного обрушения. Варианты.
42. Вариант подэтажного обрушения «Закрытый веер».
43. Способы подготовки и нарезки блока при подэтажном обрушении.
44. Варианты подэтажного обрушения с отбойкой на компенсационные щели.
45. Варианты подэтажного обрушения с отбойкой руды в «зажиме» с торцовым выпуском.
46. Выпуск обрушенной руды.
47. Системы разработки с принудительным этажным обрушением.
48. Принудительное этажное обрушение на горизонтальные компенсационные камеры.
49. Принудительное этажное обрушение на вертикальные компенсационные камеры.
50. Принудительное этажное обрушение без компенсационных камер.
51. Система разработки этажного самообрушения.
Вариант этажного самообрушения со сплошной выемкой. Этаж разделяют на панели, длина которых в несколько раз превышает обычный поперечный размер блока.
Панель разрезают поперек щелью и затем постепенно подсекают по длине, вызывая этим самообрушение массива с отставанием на 30—60 м от подсечки. Отсечные выработки на подэтажах проходят по границам панели. Этот вариант эффективен при выдержанных элементах залегания и при отсутствии жесткой необходимости в усреднении качества рудной массы.
Иногда ускоряют обрушение руды взрыванием зарядов (сосредоточенных или скважинных) на подэтажах.
Частичный выпуск, особенно в начальной его стадии, целесообразно вести так, чтобы высота свободного пространства под обрушаемым массивом не превышала 5 м во избежание вывалов крупных глыб и образования воздушных ударов. В первый период после подсечки выпуск должен быть малоинтенсивным, так как подсеченный массив деформируется, расчленяется микротрещинами. С опережением выпускают руду со стороны лежачего бока во избежание преждевременной посадки висячего бока.
На руднике «Клаймакс» (США) при этажном самообрушении (рис. 8.7) высота этажа составляет 100 м. Руду доставляют скреперными установками мощностью 110 кВт, погрузка вагонов безлюковая. Сетка выпускных отверстий 10,5 X 10,5 м. Скреперный штрек и наклонные выпускные выработки, расположенные попарно, закреплены бетоном. Подсечка траншейная.
Сочетание большой мощности залежи с небольшой глубиной разработка позволяет подсекать массив на большую ширину (100—400 м), достаточную для самообрушения даже сравнительно устойчивых руд. За ходом самообрушения наблюдают из штреков, пройденных на верхнем уровне подсечки.
Особенности варианта этажного самообрушения с выемкой блоками. Поперечные размеры блока составляют 30—40 м при слабых рудах и высоком горном давлении и 50—60 м при иных условиях.
По углам блока проходят отрезные восстающие, а из них подэтажные отрезные выработки по периметру блока (рис 8.8).
На расстоянии 8—12 м от углов блока проходят смотровые восстающие, из которых нарезают смотровые ходки для наблюдения за ходом обрушения.
Рис. 8.7. Этажное самообрушение — вариант со сплошной выемкой (рудник «Клаймакс», США): 1 — откаточный штрек; 2 — откаточный орт; 3 — вентиляционный орт; 4 — скреперный штрек; 5 — выработки для выпуска руды; 6 — вентиляционный восстающий; 7 — подсечной штрек; 8 — сборка для образования воронок; 9 — буровой штрек; 10 — скважины для подсечки
Подсечку блока ведут от лежачего бока к висячему и от центра к краям по простиранию.
Если соседний блок заполнен отбитой рудой, то в направлении по простиранию подсечку ведут в отступающем порядке. В блоке, граничащем с обрушенными вмещающими породами, подсечку подвигают от массива к обрушению.
Производительность блока (панели) средняя за период очистных работ составляет 10—40 тыс. т/мес., производительность труда забойного рабочего 50—90 т/смену, потери и разубоживание руды 12—25%, удельный расход подготовительно-нарезных выработок (7—10) м/1000 т.
Рис.8.8. Система этажного самообрушения блоками.
Этажное самообрушение сохранилось преимущественно в варианте со сплошной выемкой.
Требования ПТЭ к системам с самообрушением:
· При естественном обрушении руда должна легко обрушаться небольшими кусками при ее подсечке;
· При естественном этажном обрушении кусковатость руды регулировать скоростью ее обрушения и выпуска. Не допускать чрезмерного отставания обрушения от поверхности выпускаемой руды.
52. Комбинированные системы разработки. Общая характеристика. Классификация.
VI | Комбинированные системы | 21. | С креплением и магазинированием руды |
22. | С креплением и закладкой | ||
23. | С магазинированием руды и обрушением | ||
Комбинированные системы:
Комбинированные системы с выемкой камер с открытым очистным пространством.
Комбинированные системы с выемкой камер с магазинированием руды
Комбинированные системы с выемкой камер закладкой.
К классу относятся такие системы разработки, при которых в определенных условиях панель разделяется на регулярно чередуемые камеры и междукамерные целики, разрабатываемые последовательно в две стадии различными системами разработки. Следует отметить, что комбинированные системы — это не совместное и одновременное применение нескольких систем разработки. При комбинированных системах, как подчеркивает акад. М. И. Агошков, подготовка, нарезка и очистная выемка в камере и междукамерном целике, которые составляют вместе выемочный блок, настолько связаны и конструктивно неотделимы друг от друга, что систему разработки блока следует рассматривать как новую.
53. Комбинированные системы разработки с открытыми камерами.
54. Комбинированные системы разработки с магазинированием руды.
55. Комбинированные системы разработки с закладкой камер.
56. Комбинированные системы разработки последующей закладкой камер.
57. Классификация методов выемки целиков.
Классификация методов выемки целиков | ||
Класс | Состояние камер | |
С обрушение руды и вмещающих пород (с | При открытых камерах | |
При камерах с замагазинированой рудой | ||
массовым обрушением) | ||
При обрушенных камерах | ||
При камерах, заполненных твердеющей | ||
С искусственным поддержанием очистного | закладкой | |
пространства камерами с закладкой | При камерах, заполненных сыпучей | |
закладкой |
58. Выемка целиков с обрушением руды и вмещающих пород.
Дата добавления: 2020-04-08; просмотров: 1419; Мы поможем в написании вашей работы! |
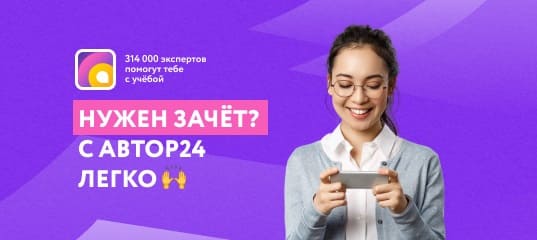
Мы поможем в написании ваших работ!