Конструирование подшипниковых узлов
Конструктивное оформление подшипниковых узлов (опор) редуктора зависит от типа подшипников, схемы их установки, вида зацепления редукторной пары и способа смазывания подшипников и колес.
Основным изделием подшипникового узла является подшипник. Помимо этого комплект деталей может включать: детали крепления колец подшипников на валу и в корпусе; крышки; компенсаторные и дистанционные кольца; стаканы; уплотнения (наружные и внутренние); регулирующие устройства.
В данном разделе рассмотрены схемы установок и выбор посадок подшипников, а так же рекомендации по конструированию и выбору отдельных комплектующих деталей подшипниковых узлов, правила вычерчивания внутренней конструкции подшипников.
8.4.1 Схемы установки подшипников
Типы подшипников подобраны в разделе 6 и их пригодность для каждого вала проверена в разделе 7. При этом вал с опорами должен представлять статически определимую систему в виде балки с одной шарнирно-подвижной (плавающей)опорой для предотвращения защемления в подшипниках от температурных деформаций вала и одной шарнирно-неподвижной (фиксирующей)опорой, препятствующей осевому смещению вала.
Плавающие опорыдопускают осевое перемещение вала от температурных деформаций в любом направлении и воспринимают только радиальные нагрузки (см. рисунки 34, 35). Если в зацеплении действуют радиальная F r и осевая F a силы, то в качестве плавающей выбирают более нагруженную опору - с большей суммарной реакцией; если в зацеплении действует только радиальная сила, то плавающая - менее нагруженная опора.
|
|
Фиксирующие опорыограничивают перемещение вала в одном (см. рисунки 36 - 40) или обоих направлениях (см. рисунки 34, 35) и воспринимают радиальную и осевую нагрузки.
Таким образом, осевое фиксирование валов осуществляется различными способами установки подшипников в плавающих и фиксирующих опорах.
Схема 1 - Осевое фиксирование вала в одной опоре одним подшипником(рисунок 34)
Плавающая опора. Внутреннее кольцо подшипника с обоих торцев закреплено на валу. Наружное кольцо в корпусе не закреплено и допускает осевое перемещение вала в обоих направлениях.
Фиксирующая опора.Внутреннее кольцо подшипника с обоих торцев закреплено на валу. Наружное кольцо также с двусторонним закреплением в корпусе ограничивает осевое перемещение вала в обоих направлениях.
Типы подшипников. Радиальные однорядные шариковые и роликовые и двухрядные сферические. Любой из типов подшипников плавающей опоры может быть применен с любым типом подшипника фиксирующей опоры. В проектируемых редукторах приняты радиальные однорядные шарикоподшипники.
|
|
Достоинства:
а) температурные удлинения вала не вызывают защемления тел качения в подшипниках;
б) не требуется точного расположения посадочных мест подшипников по длине вала.
Недостатки:
а) малая жесткость опор;
б) относительная сложность конструкции фиксирующей опоры.
Применение.При любых расстояниях между опорами, значительных температурных деформациях вала и невысоких требованиях к жесткости опор и вала. В проектируемых приводах схему 1 применяют ограниченно (в цилиндрических редукторах при а w > 180 мм.
Рисунок 34 – Установка радиальных шариковых подшипников по схеме 1: правая опора – фиксирующая; левая – плавающая
Схема 2. Осевое фиксирование вала в одной опоре двумя подшипниками
( рисунок 35)
Закрепление внутренних и наружных колец подшипников на валу и в корпусе плавающей и фиксирующей опор такое же, как и в схеме 1.
Типы подшипников.В плавающей опоре — радиальные однорядные шариковые и роликовые, а также двухрядные сферические. В фиксирующей опоре - сдвоенные одинарные радиальные и радиально-упорные. Любой из подшипников плавающей опоры может быть применен с любым из типов подшипников фиксирующей опоры. Подшипники фиксирующей опоры устанавливают в стаканы. В проектируемых редукторах приняты: в плавающей опоре радиальные однорядные шариковые подшипники; в фиксирующей – сдвоенные одинарные радиально-упорные шариковые и роликовые конические.
|
|
Достоинства и недостаткисхемы 2 такие же, как и схемы 1, но при этом схема 2 характеризуется большей жесткостью фиксирующей опоры.
Применение.При любых расстояниях между опорами, значительных температурных деформациях вала и высоких требованиях к жесткости опор и вала. В проектируемых приводах схему 2 применяют ограниченно (на быстроходных валах червячных редукторов при а w >160 мм).
Схема 3. Осевое фиксирование вала в двух опорах - враспор ( рисунки 36 - 39)
Обе опоры конструируют одинаково, при этом каждый подшипник ограничивает осевое перемещение вала в одном направлении. Внутренние кольца подшипников закрепляют на валу упором в буртики 3-й или 5-й ступени вала либо в торцы других деталей, установленных на 2-й или 4-й ступени. Наружные кольца подшипников закреплены от осевого смещения упором в торцы крышек или других деталей, установленных в подшипниковом гнезде. Кольца радиально-упорных подшипников обеих опор располагают широкими торцами наружу.
|
|
Рисунок 35 - Установка подшипников по схеме 2: нижняя опора - фиксирующая на двух конических роликовых подшипниках; верхняя - плавающая (радиальный шарикоподшипник); l* — расстояние между точками приложения реакций, когда у сдвоенного подшипника работает один ряд тел качения; l** - работают оба ряда
Рисунок 36 - Установка радиальных шариковых подшипников по схеме 3
враспор; обе опоры фиксирующие, крышки врезные
Рисунок 37 - Установка радиально-упорных шариковых подшипников по схеме 3 - враспор; обе опоры фиксирующие, регулирование подшипников - прокладками
Рисунок 38 - Установка конических роликоподшипников по схеме 3 — враспор; обе опоры фиксирующие, крышки торцовые, регулирование подшипников - прокладками
Рисунок 39 - Установка конических роликовых подшипников по схеме 3 - враспор; обе опоры фиксирующие, крышки врезные, регулирование подшипников – винтом
Типы подшипников. В проектируемых редукторах приняты радиальные однорядные шариковые и радиально-упорные шариковые и роликовые конические подшипники. Если в опорах применены радиальные подшипники, то для компенсации тепловых деформаций сравнительно коротких (до 300 мм) валов между торцем наружного кольца и крышкой устанавливают зазор а = 0,2...0,5 мм (на сборочных чертежах редукторов зазор а не показывают). При установке радиально-упорных подшипников для предотвращения защемления в телах качения от температурных деформаций вала предусматривают осевую регулировку зазоров в подшипнике.
Достоинства:
а) возможность регулировки подшипников;
б) простота конструкции опор (отсутствие стаканов и других дополнительных деталей).
Недостатки:
а) вероятность защемления тел качения в опорах вследствие температурных деформаций;
б) более жесткие допуски на осевые размеры вала и ширину корпуса.
Применение.При небольших расстояния между опорами l ≤ (6...8) d. Меньшие значения относятся к роликовым, большие - к шариковым радиально-упорным, подшипникам. В разрабатываемых проектах схема 3 предпочтительна и широко применяется для быстроходных и тихоходных валов цилиндрических и червячных редукторов (для вала-червяка при а w < 160 мм), а также для тихоходных валов конических редукторов.
Схема 4. Осевое фиксирование вала в двух опорах - врастяжку (рисунки 40, 41)
Обе опоры конструируют одинаково, при этом каждый подшипник ограничивает осевое перемещение вала в одном направлении. Внутреннее кольцо одного подшипника (на рисунках - левого) упирают в регулировочную гайку, при этом его посадку для возможности перемещения по валу не ослабляют; внутреннее кольцо другого упирают в буртик третьей ступени или торцы других деталей, установленных на валу. Наружные кольца подшипников упирают широкими торцами в буртики отверстия корпуса (или стакана - см. рисунок 41) или применяют подшипники с бортами на наружном кольце (рисунок 40).
Типы подшипников.В проектируемых редукторах приняты радиально-упорные шариковые и роликовые конические подшипники.
Достоинства:
а) возможность регулирования опор;
б) малая вероятность защемления тел качения в опорах при температурных деформациях, так как зазоры в подшипниках будут увеличиваться.
Недостатки:
а) высокие требования точности к резьбе вала и гаек, и к торцам гаек;
б) усложнение конструкции опор.
Применение.При небольших расстояниях между опорами l = (8...10) d . Меньшие значения относятся к роликовым, большие - к шариковым радиально-упорным подшипникам,
В разрабатываемых проектах схема 4 применяется для быстроходных валов конических редукторов.
Рисунок 40 - Установка конических роликоподшипников по схеме 4 - врастяжку; обе опоры фиксирующие, крышка торцовая, регулирование подшипников - круглой шлицевой гайкой
Рисунок 41 - Установка радиально-упорных шариковых подшипников по схеме 4 - врастяжку; обе опоры фиксирующие, крышка торцовая, регулирование подшипников - круглой шлицевой гайкой
8.4.2 Посадка подшипников
В проектируемых редукторах внутреннее кольцо подшипника вращается относительно радиальной нагрузки, подвергаясь так называемому циркуляционному нагружению; наружное кольцо — неподвижно относительно радиальной нагрузки и подвергается местному нагружению.
Соединение вращающихся относительно радиальной нагрузки внутренних колец подшипника с валом осуществляется с натягом, исключающим проворачивание и обкатывание кольцом сопряженной ступени вала.
Посадки неподвижных относительно радиальной нагрузки наружных колец подшипника выбирают более свободными, допускающими наличие небольшого зазора: периодическое проворачивание наружного кольца полезно, так как при этом изменяется положение его зоны нагружения. Кроме того, такое сопряжение облегчает осевые перемещения колец при монтаже, при регулировании зазора в подшипниках и при температурных деформациях валов.
Подшипник является основным комплектующим изделием, не подлежащим в процессе сборки дополнительной доводке. Требуемые посадки в соединении подшипника качения получают назначением соответствующих полей допусков на диаметры вала или отверстия в корпусе.
Для наиболее распространенного в общем машиностроении случая применения подшипников класса точности 0 выбор полей допусков вала и отверстия корпуса можно производить в зависимости от вида нагружения колец, режима работы подшипников и соотношения большей эквивалентной динамической нагрузки RЕ с базовой динамической грузоподъемностью С r. Проектируемые согласно техническим заданиям приводы работают в режиме мало меняющейся наuhузки, при которой^
0,07С r < RE ≤ 0,15 Cr
В этом случае поле допуска вала для внутреннего кольца подшипника при циркуляционном нагружении:
- для шариковых – js 6,k6;
- для роликовых — k 6, т6.
Поле допуска отверстия для наружного кольца шариковых и роликовых подшипников при местном нагружении - Н7.
8.4.3 Крепление колец подшипников на валу и в корпусе
При выборе способа крепления колец подшипника следует учитывать схему установки подшипников, тип опоры (фиксирующая или плавающая), величину осевой нагрузки, способ регулирования подшипников и колес, тип и характер посадки подшипников, частоту вращения вала, размеры и конструкцию узла в целом. В каждом частном случае принятому способу крепления внутреннего кольца могут соответствовать различные способы крепления наружного кольца, и наоборот.
Рисунок 42 - Способы крепления внутреннего кольца подшипника: а - посадкой с натягом; б - пружинным упорным кольцом, в - круглой гайкой со шлицами; г - концевой шайбой
Рисунок 43 - Способы крепления наружного кольца подшипника: а - крышкой и уступом в корпусе; б — крышкой и уступом в стакане; в — концевой шайбой и уступом в корпусе; г — круглой гайкой со шлицами и уступом в корпусе
На рисунках 42 и 43 приведены наиболее распространенные в машиностроении способы крепления колец подшипников на валу и в корпусе.
а) Подшипники установлены по схемам 1 и 2. Внутренние кольцаобеих опор закрепляют на валу с двух сторон: с одной стороны буртиком вала, с другой - одним из способов крепления различными крепежными деталями:
- рисунок 42, б - пружинным упорным кольцом, которое закладывается в разведенном состоянии в кольцевую канавку на валу; крепление применяется при ограниченных частотах и значительных осевых нагрузках;
- рисунок 42, в - круглой шлицевой гайкой при значительных осевых нагрузках; гайка предохраняется от развинчивания стопорной многолапчатой шайбой, внутренний зуб которой входит в паз вала, а один из наружных отгибается в прорези гайки;
- рисунок 42, г - концевой шайбой, которая крепится к торцу вала винтом по оси вала и стопорным штифтом (или двумя винтами вне оси вала - рисунок 43, а -в);
- рисунок 34 - распорной втулкой, установленной между торцами внутреннего кольца подшипника и ступицы элемента открытой передачи или муфты. Крепление может передавать значительные осевые нагрузки.
Наружные кольцафиксирующих опор закрепляют в корпусе с двух сторон: рисунок 43, а, г — врезной или торцовой крышкой и уступом в корпусе (см. таблицы 69 - 73);
- рисунок 43, б - торцовой крышкой и упорным буртиком стакана (см. таблицу 69);
- рисунок 43, в - пружинным стопорным кольцом и уступом в корпусе.
Наружные кольца плавающих опор в корпусе не закрепляют.
б) Подшипники установлены по схеме 3. Внутренние кольцаподшипников в обеих опорах устанавливают с упором в буртик вала с натягом без дополнительного крепления с противоположной стороны (см. рисунок 42, а). При недостаточной высоте буртика его функции выполняют распорные втулки.
Наружные кольцаподшипников в обеих опорах устанавливают в корпус с односторонней фиксацией упором в торец крышки или компенсаторного кольца (см. рисунки 36 - 39).
в) Подшипники установлены по схеме 4. Способы крепления колец подшипников рассмотрены при описании схемы.
8.4.4 Крышки подшипниковых узлов
Для герметизации подшипниковых узлов редуктора, осевой фиксации подшипников и восприятия осевых нагрузок применяют крышки. Они изготовляются, как правило, из чугуна СЧ 15 двух видов — торцовые и врезные. Те и другие выполняют в двух конструкциях — глухие и с отверстием для выходного конца вала. Размеры крышек определяют в зависимости от диаметра наружного кольца подшипника D или стакана и выбирают из таблиц 69 - 73.
а) Торцовые крышки (см. таблицы 69 - 71, 73). Применяются в неразъемных корпусах для подшипниковых узлов быстроходных валов редукторов; могут также применяться и в редукторах с разъемными корпусами. Выбор конструкции крышки зависит:
- от уплотнения валов. Крышки с отверстием для манжетного уплотнения - таблица 70, рисунок 35; крышки с жировыми канавками - таблица 71, рисунок 37; глухие крышки - таблица 69, рисунок 38; крышки под регулировочные винты - таблица 73;
- от крепления подшипников на валу. Низкие крышки применяют при закреплении внутреннего кольца подшипника без помощи крепежных деталей; высокие - при закреплении кольца, например, гайкой - см. рисунок 41;
- от регулировки зазоров в подшипниках. Производится установкой под фланец крышки набора прокладок или воздействием винтами с резьбовыми крышками (см. таблицу 73);
- от размещения комплекта деталей подшипникового узла. При размещении комплекта в корпусе крышка выбирается по диаметру наружного кольца подшипника D; если комплект деталей собирается в стакане, то размеры крышки определяют по его наружному диаметру.
б) Врезные крышки (см. таблицы 72, 73).
Широко применяют в современном редукторостроении в разъемных корпусах с межосевым расстоянием а w ≤ 250 мм. Выбор конструкции крышки зависит от способа уплотнения валов: с отверстием для манжетного уплотнения (см. рисунок 36); с жировыми канавками1; глухие крышки - см. рисунок 34. Регулировка радиально-упорных подшипников производится только резьбовыми деталями (см. рисунок 39), а радиальных - установкой компенсаторного кольца между наружным кольцом подшипника и глухой крышкой (см.рисунок 36). Осевой размер кольца определяется конструктивно с учетом зазора на температурную деформацию вала. Толщина кольца принимается равной толщине наружного кольца подшипника.
Таблица 69 – Крышки торцовые глухие (ГОСТ 18511 – 73)
мм | ||||||||||||
D | D1 | D2 | D3 | Отверстия под винты (болты) | H | H2 | h1 | b | s | |||
d | d1 | d2 | n | |||||||||
40; 42 | 54 | 70 | 34 |
7 |
12 |
14 |
4 |
10 |
20 |
5 |
4 |
5 |
44; 47 | 60 | 78 | 38 | |||||||||
50; 52 | 66 | 82 | 44 | |||||||||
55; 58 | 75 | 95 | 48 | 22 | 7 | |||||||
60; 62 | 75 | 95 | 52 | 22 | 7 | |||||||
65; 68 | 84 | 105 | 58 |
9 |
15 |
20 |
4 |
12 |
26 |
8 |
4 |
6 |
70; 72 | 90 | 110 | 62 | |||||||||
75 | 90 | 110 | 64 | |||||||||
80; 85 | 100 | 120 | 72 | 6 | ||||||||
90; 95 | 110 | 130 | 80 | 6 | ||||||||
100 | 120 | 145 | 90 | 11 | 18 | 24 | 6 | 15 | 32 | 9 | 5 | 7 |
105; 110 | 130 | 155 | 95 | 11 | 18 | 24 | 6 | 15 | 32 | 9 | 5 | 7 |
Таблица 70 – Крышки торцовые с отверстием для манжетного уплотнения (ГОСТ 18512 – 73)
мм | ||||||||||||||||||
D | D1 | D2 | D3 | D4 |
| H | h | h1 | B | b | s | B1 | b1 | l | h2 | |||
d | d1 | d2 | n | |||||||||||||||
40; 42 | 54 | 70 | 34 | 40 |
7 |
12 |
14 |
4 |
15 |
5 |
10 | 13 |
4 |
5 | 12 | 8 |
2 |
2 |
47 | 60 | 78 | 38 | 47 | 13 | 12 | 8 | |||||||||||
52 | 66 | 82 | 44 | 50 | 13; 15 | 12; 15 | 8; 11 | |||||||||||
55 | 75 | 95 | 48 | 50 | 15 | 15 | 11 | |||||||||||
60; 62 | 78 | 95 | 52 | 60 | 15 | 15 | 11 | |||||||||||
65; 68 | 84 | 105 | 58 | 68 |
9 |
15 |
20 |
4 |
17 |
6 |
12 |
15 |
4 |
5 | 15 |
11 | 2; 3 | |
70; 72 | 90 | 110 | 62 | 72 | 12; 15 |
3 |
- | |||||||||||
75 | 90 | 110 | 64 | 72 |
15 | |||||||||||||
80; 85 | 100 | 120 | 72 | 80 |
6 | 20 | 6 | |||||||||||
90; 95 | 110 | 130 | 80 | 92 | 20 | 6 | 3 | |||||||||||
100 | 120 | 145 | 90 | 100 |
11 |
18 |
24 |
23 |
8 |
15 | 18; 20 | 5 | 7 |
17 | 11; 13,6 | - | ||
105; 110 | 130 | 155 | 95 | 110 | 20 | 5 | 7 | 11; 13,6 | - |
Примечания. 1 Размеры под манжетное уплотнение см. таблицу 73. 2 Диаметр отверстия в крышке (Н12) определяется по соответствующему диаметру вала или втулки. 3 Значения Н1, h 3 , l 1 для крышек подшипников быстроходного вала конической передачи выбрать из ряда:
Размеры | Диаметр вала или втулки, мм | ||||||||
15 | 17 | 20 | 25 | 30 | 35 | 40 | 45 | 50 | |
H1 | 22 | 22 | 27 | 28 | 28 | 30 | 28 | 31 | 33 |
h3 | 7 | 7 | 12 | 13 | 10 | 10 | 12 | 13 | 15 |
l1 | 10 | 10 | 12 | 12 | 13 | 13 | 15 | 16 | 18 |
Таблица 71 – Крышки торцовые с жировыми канавками (ГОСТ 18513 – 73)
| |||||||||||||||||||||
D | D1 | D2 | D3 | Отверстия под винты (болты) | H | h | h1 | B | b | s | l | ||||||||||
d | d1 | d2 | n | ||||||||||||||||||
40; 42 | 54 | 70 | 34 |
7 |
12 |
14 |
4 |
18 |
5 |
10 |
16 |
4 |
5 |
2 | |||||||
44; 47 | 60 | 78 | 38 | ||||||||||||||||||
52 | 66 | 82 | 44 | ||||||||||||||||||
55 | 75 | 95 | 48 | ||||||||||||||||||
60; 62 | 78 | 95 | 52 | ||||||||||||||||||
65; 68 | 84 | 105 | 58 |
9 |
15 |
20 | 19 |
6 |
12 |
6 | |||||||||||
70; 75 | 90 | 110 | 62 | 19 |
3 | ||||||||||||||||
80; 85 | 100 | 120 | 72 | 6 | 21 | 18 | |||||||||||||||
90; 95 | 110 | 130 | 80 | 6 | 21 | 18 | |||||||||||||||
Примечания. 1 Размер а = 2 мм при D ≤ 95 мм; а = 3 мм при D ≥ 100 мм. 2 Диаметр отверстия в крышке (Н12) определяется по соответствующему диаметру вала или втулки. 3 Значения Н1, h 3, l 1 для крышек подшипников быстроходного вала конического редуктора выбирать из ряда: | |||||||||||||||||||||
Размеры | Диаметр вала или втулки | ||||||||||||||||||||
15 | 17 | 20 | 25 | 30 | 35 | 40 | 45 | 50 | |||||||||||||
Н1 | 26 | 26 | 28 | 29 | 29 | 31 | 32 | 32 | 34 | ||||||||||||
h3 | 11 | 11 | 13 | 14 | 14 | 16 | 16 | 16 | 18 | ||||||||||||
l1 | 10 | 10 | 12 | 13 | 13 | 15 | 15 | 16 | 18 | ||||||||||||
Таблица 72 – Крышки врезные с отверстиями и глухие
| ||||||||||||
D | 40 | 42 | 47 | 52 | 62 | 72 | 80 | 85 | 90 | 95 | 100 | 110 |
D0 | 43 | 46 | 52 | 56 | 67 | 77 | 85 | 92 | 95 | 102 | 105 | 117 |
D3 | 34 | 34 | 38 | 44 | 52 | 62 | 72 | 72 | 80 | 80 | 90 | 95 |
h | 14 | 16 | 20 | |||||||||
h1 | 3 | 4 | 5 | 7 | ||||||||
l | 8 | 10 | 12 | |||||||||
l1 | 2 | 3 | ||||||||||
B | 10 | 15 | ||||||||||
Примечания. 1 Размеры под манжетное уплотнение см. таблицу 73. 2 Диаметр отверстия в крышке (Н12) для крышки с манжетным уплотнением определяется по соответствующему диаметру вала или втулки. 3 Допускаемое отклонение диаметра крышки D по h 8. 4 Размер а = 2 мм, а1 = 1 мм, при D ≤ 95 мм; а = 3 мм, а1 = 1,5 мм при D ≥ 100 мм. |
8.4.5 Конструирование стаканов
Применение стаканов при конструировании подшипниковых узлов обусловлено облегчением их сборки (и разборки) вне корпуса редуктора и удобством регулировки подшипников и колес. В проектируемых редукторах стаканы ставят в фиксирующих опорах при установке подшипников по схемам 1 и 2 (рисунок 35 и рисунки а, б таблицы 74), а также по схеме 4 (рисунок 40 и рисунок в таблицы 74). Кроме того, установка стаканов необходима в подшипниковых узлах быстроходных валов червячных редукторов и цилиндрических вертикальных редукторов с неразъемным корпусом в случае, если диаметр выступов червяка или шестерни окажется больше диаметра наружного кольца подшипника dа1 > D (рисунок г таблицы 74). Стаканы изготавливают обычно из чугуна СЧ 15, реже из стали. Конструкцию и размеры стаканов определяют по таблице 74.
Таблица 73 – Крышки (торцовые и врезные) под регулировочные винты
мм | |||||||||||||||
D | D0 | D1 | D2 | D3 | D4 | d0 | d | d1 | n | d2 | H | h | h1 | h2 | l |
47 | 52 | 60 | 75 | 38 | М39×1,5 |
М16 |
7 |
12 |
4 | 28 |
14 | 4 |
6,5 |
5 |
8 |
52 | 56 | 66 | 82 | 44 | М42×1,5 | 30 | 4 | ||||||||
62 | 67 | 78 | 95 | 52 | М52×1,5 | 30 |
5 | ||||||||
72 | 77 | 90 | 110 | 62 | М56×1,5 |
9 |
15;18 |
32 |
16 |
8,5 |
6 |
10 | |||
80 | 85 | 100 | 120 | 72 | М68×1,5 |
6 | |||||||||
85 | 92 | 100 | 120 | 72 | М68×1,5 | ||||||||||
90 | 95 | 110 | 130 | 80 | М76×1,5 | ||||||||||
95 | 102 | 110 | 130 | 80 | М76×1,5 |
7 | |||||||||
100 | 105 | 120 | 145 | 90 | М85×1,5 | М20 | 11 | 18;20 | 38 | 20 | 11 | 8 | 12 | ||
110 | 117 | 130 | 155 | 95 | М95×1,5 | М20 | 11 | 18;20 | 38 | 20 | 11 | 8 | 12 | ||
Примечание. На эскизе совмещены торцовая и врезная крышки. |
8.4.6 Уплотнительные устройства
Применяют для предотвращения вытекания смазочного материала из подшипниковых узлов, а также защиты от попадания пыли, грязи и влаги. В зависимости от места установки в подшипниковом узле, уплотнения делят на две группы: наружные — устанавливают в крышках (торцовых и врезных - таблицы 69 - 73) и внутренние – устанавливают с внутренней стороны подшипниковых узлов.
Наружные уплотнения. В проектируемых редукторах применены уплотнения по цилиндрическим (манжетные), торцевым (торцовые) поверхностям и щелевые. Выбор типа уплотнения зависит от способа смазывания подшипников, окружной скорости вала, рабочей температуры и характера внешней среды.
Таблица 74 – Стаканы. Конструкция и размеры
| |
Толщина стенки | δ = 4…5 при D ≤ 52 |
δ = 6…8 при D > 52…80 | |
Толщина упорного буртика | δ1 = δ |
Толщина фланца | δ 2 = 1,2δ |
Высота упорного буртика | t = (1,3…1,5)r, где r – радиус скругления наружного кольца подшипника |
Диаметры фланцев D 1, D 2 и количество отверстий n | Соответствуют размерам D 1, D 2 и количеству отверстий крышки подшипникового узла |
Профиль канавки на наружной поверхности стакана | Смотри таблицу 24 |
П р и м е ч а н и я : 1 Посадка стакана конической шестерни H7/ js 6 обеспечивает его перемещение при регулировке зацепления. Стаканы подшипниковых узлов других валов неподвижны - посадки с натягом типа Н7/к6 или Н7/т6. 2 При установке стакана в корпус с натягом фланец делают уменьшенным без отверстий под винты (рисунок б). 3 Наружный диаметр стакана Dа и его длина определяются конструктивно в зависимости от диаметра наружного кольца подшипника, длины вала (или его ступеней) и размещения комплекта деталей подшипникового узла. |
а) Манжетные уплотнения. Их используют при смазывании подшипников как густым, так и жидким материалом при низких и средних скоростях v ≤ 10 м/с, так как они оказывают сопротивление вращению вала.
Резиновые армированные манжеты(таблица 75). Манжета (рисунок 44, а) состоит из корпуса 2, изготовленного из бензомаслостойкой резины, стального Г-образного каркаса 3 и браслетной пружины 1, которая стягивает уплотняющую часть манжеты и образует рабочую кромку шириной b = 0,4...0,8 мм (рисунок 44, в). Манжеты, работающие в засоренной среде, снабжены "пыльником" (рисунок 44, б).
Рисунок 44 – Резиновые армированные манжеты: а – без пыльника, б – с пыльником, в – рабочая кромка манжеты
Рисунок 45 – Манжетное уплотнение подшипникового узла
Таблица 75 – Манжеты резиновые армированные для валов (ГОСТ 8752-79)
мм | |||||||||
Диаметр вала d | D1 | h1 | h2, не более | Диаметр вала d | D1 | h1 | h2, не более | ||
1-й ряд | 2-й ряд | 1-й и 2-й ряды | 1-й ряд | 2-й ряд | 1-й и 2-й ряды | ||||
20 |
40 | 35 |
8 |
12 | 42 | 62 | 62 |
10 |
14 |
37 | 65 | ||||||||
38 | 44 | - | 68 | ||||||
42 | 10 | 14 | - | 62 | |||||
21 | 37 | 8 | 12 |
45 |
65 | 65 | |||
35 | 10 | 14 | 62 | ||||||
22 | 42 | 8 | 12 | 70 | |||||
42 |
10 |
14 | 48 |
70 | 65 | ||||
24 | 42 | 72 | |||||||
45 | 50 | 72 | |||||||
25 | 42 | 40 | 8 | 12 | 50 | 70 | 75 | ||
42 | 45 | 10 | 14 | 80 | 12 | 16 | |||
26 | 45 | 40 | 8 | 12 | 52 | 75 | 72 | 10 | 14 |
45 | 47 |
10 |
14 | 80 | 12 | 16 | |||
28 |
- | 45 | 55 |
80 | 75 | 10 | 14 | ||
47 | 82 | 12 | 16 | ||||||
50 | 56 | - | 10 | 14 | |||||
30 |
52 | 45 | 58 | 75 | 10 | 14 | |||
47 | 82 | 12 | 16 | ||||||
50 | 60 | 85 | 80 |
10 |
14 | ||||
32 | 45 | 82 | |||||||
50 | 62 | - | 80 |
Продолжение таблицы 75
Диаметр вала d | D1 | h1 | h2, не более | Диаметр вала d | D1 | h1 | h2, не более | ||
1-й ряд | 2-й ряд | 1-й и 2-й ряды | 1-й ряд | 2-й ряд | 1-й и 2-й ряды | ||||
35 | 52 | 47 |
10 |
14 |
62 | - | 82 | 10 | 14 |
50 | - | 85 | 10 | 14 | |||||
58 | 55 | - | 90 | 12 | 16 | ||||
57 | 63 | 90 | - | 10 | 14 | ||||
36 | 52 | 65 | 95 | 10 | 14 | ||||
55 | 67 | - | 90 | 12 | 16 | ||||
55 | 68 | - | 90 | 12 | 16 | ||||
38 | 60 | - | 95 | 12 | 16 | ||||
62 | 70 | 95 | 100 | 12 | 16 | ||||
40 | 60 | 55 | 71 | 95 | - | 10 | 14 | ||
58 | 75 | 100 | - | 10 | 14 | ||||
102 | 12 | 16 | |||||||
Примечание. Пример условного обозначения манжеты типа 1 исполнения 1, для вала диаметром d = 30 мм, с наружным диаметром D = 52 мм, из резины группы 1: Манжета 1.1- 30×52 – ГОСТ 8752 – 79. |
Для предохранения смазочного материала от вытекания манжету обычно устанавливают рабочей кромкой внутрь корпуса (рисунок 45), что обеспечивает к кромке доступ масла, уменьшающего износ резины.
Для удобства выемки манжеты в крышке подшипника иногда предусматривают 2...3 отверстия диаметром 3...4 мм.
б) Торцовые уплотнения. Их применяют преимущественно при жидком смазочном материале. Эффективно предохраняют подшипник от вьггекания масла и попадания воды и грязи. Наиболее простые торцовые уплотнения - стальными шайбами (таблица 76).
Толщина шайб в зависимости от их размера составляет s = 0,3...0,6 мм. Торцевая грань шайбы выступает за ее плоскость на величину С = 0,5...0,6 мм, что создает после закрепления шайбы некоторую силу прижатия ее граней к торцам кольца подшипника (рисунок 46).
в) Щелевые уплотнения. Они эффективно работают при любом способе смазывания подшипников, практически при любой скорости, ибо не оказывают сопротивления вращению вала. Щелевые уплотнения надежно удерживают смазочный материал от вытекания под действием центробежной силы. Формы проточек щелевых уплотнений показаны на рисунке 47. Размер щелевых проточек а определяется при выборе соответствующей крышки подшипника. Зазоры щелевых уплотнений целесообразно заполнять пластичным смазочным материалом, создающим дополнительный жировой заслон для попадания извне пыли и влаги.
Внутренние уплотнения . Установка и конструкция внутренних уплотнений зависят от способа смазывания подшипников и конструкции подшипникового узла (рисунок 25).
а) Смазывание разбрызгиванием. При нижнем или боковом расположении червяка в червячных редукторах и шестерни в цилиндрических и конических передачах масло, выжимаемое из зацепления, обильным потоком выбрасывается в рядом расположенные подшипники. Во избежание попадания в подшипники продуктов износа червячных и зубчатых колес, а также излишнего полива маслом подшипниковые узлы закрывают с внутренней стороны корпуса маслозащитными шайбами (рисунок 48). Толщина шайб 1,2...2,0 мм; зазор между корпусом и наружным диаметром шайбы - 0,2...0,6 мм (на чертежах этот зазор не показывается); выход за торец корпуса или стакана С= 1...2 мм.
Рисунок 46 – Торцовые уплотнения стальными шайбами: а, б – исполнение 1; в, г – исполнение 2
Рисунок 47 – Формы щелевых канавок
Рисунок 48 -Маслозащитные шайбы: а, б – со ступицей; в, г – с центрирующим кольцом
б) Смазывание пластичным материалом. При этом способе смазывания подшипниковые узлы должны быть изолированы от внутренней полости редуктора во избежание вымывания пластичного смазочного материала жидким, применяемым для смазывания зацепления.
Уплотнение мазеудерживающим кольцом(рисунок 49, а). Такое уплотнение является комбинированным — центробежным и щелевым одновременно. Кольцо вращается вместе с валом и имеет две-четыре круговые канавки треугольного сечения; зазор между кольцом и корпусом (стаканом) 0,1...0,3 мм (на чертежах зазор не показывают); выход за торец корпуса (или стакана) С = 1...2 мм. Выступающий за пределы корпуса участок кольца отбрасывает жидкое масло, остальная цилиндрическая поверхность с проточками удерживает пластичный смазочный материал от вымывания.
Эффективное уплотнение при постоянном направлении вращения создает винтовая канавка, нарезанная на внешней поверхности кольца (рисунок 49, б), по которой смазочный материал направляется внутрь корпуса (направление нарезки винтовой линии канавки противоположно направлению вращения).
Торцовое уплотнение стальной шайбой(рисунок 49, в). Оно относится к типу контактных и весьма эффективно предохраняет подшипник от вытекания смазочного материала и попадания воды и грязи. Кольцо (на эскизе заштриховано) между шайбой и буртиком вала обеспечивает ее точное центрирование . Размеры шайб - в таблице 76.
Рисунок 49 – Мазеудерживающие кольца и шайбы: а – с круговыми канавками; б – с винтовыми канавками; в – стальная шайба с центрирующим кольцом
Таблица 76 – Шайбы уплотнительные стальные
| |||||||||
| Исполнение I | мм | Исполнение II |
| |||||
Диаметры подшипника | Общие размеры | Исполнение I | Исполнение II | ||||||
d | D | s | h | D1 | d | d1 | d2 | D | D2 |
20 | 47 |
0,3
| 2 | 41,2 | 20 | 29 | 25,7 | 47 | 37 |
52 | 44,8 | 33 | 27,2 | 52 | 40 | ||||
25 | 52 |
2,5
| 47 | 25 | 36 | 31,5 | 52 | 42 | |
62 | 54,8 | 40 | 32,2 | 62 | 47 | ||||
30 | 62 | 56,2 | 30 | 44 | 36,3 | 62 | 47 | ||
72 | 64,8 | 48 | 37,2 | 72 | 56 | ||||
35 | 72 | 64,8 | 35 | 48 | 43 | 72 | 56 | ||
80 | 70,7 | 54 | 45 | 80 | 65 |
Продолжение таблицы 76
Диаметры подшипника | Общие размеры | Исполнение I | Исполнение II | ||||||
d | D | s | h | D1 | d | d1 | d2 | D | D2 |
40 | 80 |
0,3 |
3 | 72,7 | 40 | 57 | 48 | 80 | 62 |
90 | 80,5 | 60 | 51 | 90 | 70 | ||||
45 | 85 | 77,8 | 45 | 61 | 53 | 85 | 68 | ||
100 | 90,8 | 75 | 56 | 100 | 80 | ||||
50 | 90 | 82,8 | 50 | 67 | 57,5 | 90 | 73 | ||
110 | 98,9 | 80 | 62 | 110 | 86 | ||||
55 | 100 | 90,8 | 55 | 75 | 64,5 | 100 | 80 | ||
120 | 108 | 89 | 67 | 120 | 93 | ||||
60 | 110 | 100,8 | 60 | 85 | 70 | 110 | 85 | ||
130 | 117,5 | 95 | 73 | 130 | 102 | ||||
65 | 120 | 110,5 | 65 | 90 | 74,5 | 120 | 95 | ||
140 | 0,5 | 3,5 | 127,5 | 100 | 77,5 | 140 | 110 |
8.4.7 Регулировочные устройства
Подшипники качения могут быть собраны в узле с различными радиальными и осевыми зазорами. Под радиальным е или осевым а зазором понимают полную величину радиального или осевого перемещения в обоих направлениях одного кольца подшипника относительно другого под действием определенной силы или без нее (рисунок 50).
Нерегулируемые типы подшипников(например, радиальные шариковые) изготовливают со сравнительно небольшими зазорами: после установки на вал и в корпус они могут работать без дополнительной регулировки (рисунок 50, а, б).
В регулируемых типахподшипников(радиально-упорные шариковые, роликовые конические) необходимые осевые и радиальные зазоры могут быть установлены в определенных пределах только регулировкой при монтаже комплекта подшипников в узле (рисунок 50, в).
Наличие зазоров в подшипниках обеспечивает легкое вращение вала, предотвращает защемление тел качения в результате температурных деформаций.
Устранение (выборка) зазоров повышает жесткость опор, точность вращения вала, а также улучшает распределение нагрузки между телами качения, повышая несущую способность подшипника.
Таким образом, под регулированием подшипников понимают установление минимальных зазоров, при которых в условиях эксплуатации не возникает натяг (в результате температурных деформаций), или создание при необходимости предварительного натяга.
Регулирование подшипников осуществляется перемещением одного из его колец относительно другого в осевом направлении и зависит от типа подшипника, схемы установки и способа крепления внутреннего и наружного колец. Регулирование подшипников производят до регулирования зацепления.
а) Подшипники установлены по схеме 1 (рисунок 34). Фиксирование вала осуществляется в одной опоре одним радиальным подшипником, регулировку которого не производят: необходимый зазор создан при изготовлении подшипника.
Рисунок 50 – Зазоры в подшипниках: а, б – осевой и радиальный в радиальном шарикоподшипнике; в – в коническом роликоподшипнике осевое перемещение наружного кольца в одном из направлений не ограничено
б) Подшипники установлены по схеме 2 (см. рис. 10.18). В проектируемых редукторах эта схема применена в подшипниковых узлах червячных валов при
aw ≥ 160 мм. Регулирование подшипников производят только в фиксирующей опоре вала, состоящей из двух радиальных или радиально-упорных подшипников, и установленной, как правило, со стороны глухой крышки. Регулирование может производиться перемещением наружных или внутренних колец подшипника.
Перемещение наружных колец (при этом они установлены узкими торцами друг к другу) осуществляется набором прокладок, устанавливаемых под фланец крышки. Достаточно точную регулировку можно получить, составляя набор прокладок из ряда толщин: 0,1; 0,2; 0,4; 0,8 мм или используя два полукольца, которые устанавливают под фланец без снятия крышки.
Перемещение внутренних колец (при этом наружные кольца установлены широкими торцами друг к другу) производят поджимом шлицевой гайки, которую после создания в подшипниках требуемого зазора стопорят многолапчатой шайбой. Ослаблять посадку под перемещаемым при регулировке внутренним кольцом подшипника не требуется.
Осевой размер дистанционных колец, устанавливаемых между наружными или внутренними кольцами подшипников фиксирующей опоры, определяется конструктивно в зависимости от расположения подшипников, комплекта деталей подшипникового узла и требуемого зазора в подшипниках.
в) Подшипники установлены по схеме 3 - враспор (рисунки 36 - 39). Эта схема применяется в подшипниковых узлах большинства валов проектируемых редукторов. Способы регулирования здесь зависят от типа подшипников и крышек подшипниковых узлов:
- при установке торцовых крышек (рисунки 37, 38), регулирование выполняется набором металлических прокладок, обеспечивает достаточно высокую точность и применяется как при установке радиальных, так и радиально-упорных подшипников. Для регулирования подшипников набор прокладок можно установить под фланец одной из крышек. Если дополнительно требуется регулировать осевое положение вала, общий набор прокладок разделяют на два, а затем каждый из них устанавливают под фланец соответствующей крышки;
- при установке врезных крышек (рисунки 36, 39), регулирование радиальных подшипников производят установкой компенсаторных колец между торцами наружных колец подшипников и крышек. При этом между торцом наружного кольца подшипника и торцом крышки с отверстием оставляют зазор для компенсации тепловых деформаций а = 0,2...0,5 мм (рисунок 36). На сборочных чертежах этот зазор ввиду его незначительности не показывают.
Регулирование радиально-упорных подшипников производят только воздействием винта на самоустанавливающуюся шайбу (рисунок 39), которая предохраняет наружные кольца подшипников от перекоса. Для повышения точности регулирования применяют резьбы с мелким шагом. При этом следует учитывать:
- регулирование зазоров подшипников производят с одной стороны вала (со стороны глухой крышки);
- в цилиндрических редукторах размеры регулировочного винта желательно назначать одинаковыми для крышек обоих валов, ориентируясь на размеры меньшей;
- если требуется регулирование зацепления колес, то воздействие винтами производят с обоих концов вала.
Комплект деталей регулировочного устройства включает (рисунок 51): регулировочный винт большого 1 или малого 2 диаметра (таблица 77), регулировочную самоустанавливающуюся шайбу 3 (таблица 78), торцовую или врезную крышку с резьбовым отверстием 4 ( таблица 73) и стопорные детали -контргайку 5 и др. (рисунок 52).
г) Подшипники установлены по схеме 4 - врастяжку (рисунки 40, 41). В разрабатываемых проектах по этой схеме установлены подшипники быстроходного вала конических редукторов. Регулирование подшипников производят осевым перемещением внутреннего кольца подшипника, смежного с выходным концом вала, с помощью круглой шлицевой гайки. После создания в подшипниках требуемого зазора гайку стопорят многолапчатой шайбой.
8.4.8 Вычерчивание внутренней конструкции подшипников (рисунок 53)
На сборочных чертежах редукторов и общих видах приводов вычерчивают внутреннюю конструкцию подшипников быстроходного и тихоходного валов. Работа выполняется в следующем порядке.
Рисунок 51 - Конструкции регулировочных устройств (на рисунках в, г, д совмещены торцовая и врезная крышки): а, б - винты большого диаметра воздействуют непосредственно на наружные кольца подшипника: резьба нарезана в корпусе, в крышке; в - винт малого диаметра с резьбовой крышкой и регулировочной шайбой; г, д - винты большого диаметра (глухой и с отверстием) с резьбовой крышкой и регулировочной шайбой
Рисунок 52 - Стопорные устройства: а - стопор с носком для пазов на резьбовой поверхности глухого винта; б - прямой стопор для пазов на торцевой плоскости глухого винта; в - резьбовой винт, создающий дополнительное трение в резьбе винта с отверстием. Размеры: d 1 = M6; d2 = 6,5 мм; l 1 = (0,3...0,35)D; l 1 = 5 мм; h1 = 3,5 мм
Рисунок 53 - Соотношение размеров конструктивных элементов подшипников: а - шариковых радиальных; б - шариковых радиально-упорных; в - роликовых конических
Таблица 77 – Винты регулировочные с отверстиями и глухие тип I
| ||||||
D | 40 | 42 | 47 | 52 | 62 | 72 |
D3 | 31 | 34 | 38 | 42 | 50 | 60 |
d4 | М45×1,5 | М48×1,5 | М52×1,5 | М56×1,5 | М68×1,5 | М76×1,5 |
R | 42 | 47 | 58 | 70 | 98 | 132 |
d | 6 | |||||
H | 22 | |||||
H1 | 20 | |||||
B | 14 | |||||
l | 8 | |||||
l1 | 7 | |||||
D | 80 | 85 | 90 | 95 | 100 | 110 |
D3 | 68 | 75 | 78 | 83 | 86 | 96 |
d4 | М85×1,5 | М90×1,5 | М95×1,5 | М100×1,5 | М105×1,5 | М115×1,5 |
R | 162 | 183 | 205 | 228 | 252 | 305 |
d |
| 7 | ||||
H |
| 27 | ||||
H1 |
| 25 | ||||
B |
| 17 |
Продолжение таблицы 77
|
Примечания. 1 На эскизе совмещены винты с отверстием для манжетного уплотнения и с уплотнением (таблица 73). 2 Допускаемое отклонение винта D по h 8. 3 Размер а = 2 мм при t = 5 мм, при D ≤ 80 мм; m = 6 мм, t = 5 мм при D > 80 мм |
Таблица 78 – Шайбы регулировочные
мм | ||||||||||||
Диаметр крышки | d | d1 | d2 | d3 | d4 | l | s | s1 | H | h | R | r |
40 | 39,5 |
3 | 32 | 24 |
15 | 22 |
3 | 4 |
8 |
2 | 33 |
1,6 |
42 | 41,5 | 35 | 27 | 26 | 37 | |||||||
47 | 46,5 | 40 | 31 | 30 | 4,5 | 42 | ||||||
52 | 51,5 |
4 | 42 | 34 | 34 |
4 | 5 |
10 | 47 |
2 | ||
62 | 61,5 | 47 | 38 | 40 |
6 | 58 | ||||||
72 | 71,5 | 52 | 42 | 20 | 50 | 70 | ||||||
80 | 79,5 | 62 | 50 | 25 | 55 |
5 |
12 |
3 | 98 |
2,5 | ||
85 | 84,5 | 72 | 60 |
30 | 60 | 132 | ||||||
90 | 89,5 | 80 | 68 | 65 | 162 | |||||||
95 | 94,5 | 85 | 75 | 70 | 183 | |||||||
100 | 99,5 | 90 | 78 | 75 | 6 | 7 | 205 | |||||
110 | 109,5 | 6 | 95 | 83 | 40 | 80 | 14 | 4 | 252 | 3 |
а) Радиальные и радиально-упорные шарикоподшипники (рисунок 53, а, 6):
- на 2-й и 4-й ступенях вала нанести тонкими линиями внешний контур подшипника по его габаритным размерам d, D, В: определить и нанести диаметр D pw окружности, проходящей через центры тел качения Dpw = 0,5( D + d );
- по соотношениям, указанным на рисунке 53, вычертить тела качения и кольца.
Радиально-упорные шарикоподшипники имеют на наружном кольце только один борт. Второй борт срезан. Для вычерчивания наружного кольца со стороны срезанной части проводят вспомогательную вертикальную линию до пересечения с окружностью шарика в точке 1. Точки 1 и 2 соединяют.
б) Конические роликоподшипники (рисунок 53, в):
- на 2-й и 4-й ступенях вала нанести тонкими линиями внешний контур подшипника по его габаритным размерам d, D Т, b , с;
- нанести вспомогательную вертикальную линию, делящую монтажную высоту подшипника T пополам;
- разделить отрезок а b точками 1, 2 и 3на четыре равные части и из точки 3под углом α = 15° провести образующую конуса до ее пересечения с осью вращения подшипника в точке О;
- из точки О провести линии О1 и О2, а източки т, полученной пересечением линии О1с торцом наружного кольца km, провести линию mf перпендикулярно образующей O2;
- отложив отрезок de = fk, провести параллельно линию, оформляющую малый торец ролика;
- для получения диаметра d2 борта внутреннего кольца найти точку l, делящую радиус большего торца ролика пополам.
Сепараторы на чертежах подшипников не изображают, тем не менее при установке смежных с коническим роликоподшипником деталей, например шлицевых гаек, или установке двух подшипников рядом надо учитывать, что сепаратор выступает за пределы наружного кольца на т и п (рисунок 54, а, б). Поэтому смежная деталь должна отстоять от торца наружного кольца конического роликоподшипника на b = 4...6 мм, что обеспечивается установкой дистанционной втулки. Чтобы цилиндрические поверхности смежных деталей не касались сепаратора, высоты h1 и h2 не должны превышать величин h1 = 0,1( D – d ); h2 =0,05(D - d).
При проектировании подшипникового узла контакт смежных с подшипником деталей необходимо предусматривать только по торцам подшипниковых колец, на высоте заплечика. Другие поверхности смежных деталей должны отстоять от торцов колец для всех типов подшипников (кроме конических роликовых) не менее чем на a = 2...3 мм (рисунок 55).
Рисунок 54 - Установка двух рядом расположенных конических роликовых подшипников и шлицевой гайки (или других фиксирующих деталей): а -подшипники взаимонаправлены узкими торцами наружных колец; б - широкими
Рисунок 55 - Контакт радиальных или радиально-упорных подшипников со смежными деталями
Дата добавления: 2019-11-16; просмотров: 470; Мы поможем в написании вашей работы! |
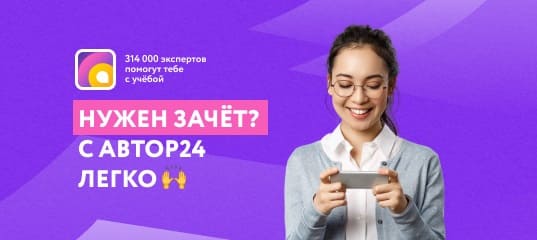
Мы поможем в написании ваших работ!