Конструирование быстроходного вала
Консольный участок этого вала оставляем таким, каким он спроектирован на I этапе эскизного проектирования. При конструировании остальной части используем найденные ранее расчетные значения расстояний между серединами подшипников и быстроходной шестерни (рисунок 6).
Для решения вопроса конструирования быстроходного вала и шестерни быстроходной пары необходимо найти отношение , где d В – диаметр прилегающей к шестерне ступени вала;
Если < 1,6 – принимают к конструированию совместную сложную деталь под названием «вал-шестерня».
В случае, если это отношение больше, чем 1,6, принимают к конструированию вал и шестерню по отдельности, как две отдельные детали.
l ВЫХ – участок выхода режущего инструмента (таблица 22)
Рисунок 17 – Пример конструирования быстроходного вала для
случая < 1,6
Таблица 22 – Внешний диаметр фрезы, мм
Модуль зацепления, мм | 2 - 2,25 | 2,5- 2,75 | 3- 3,75 | 4 – 4,5 | 5 – 5,5 | 6 - 7 | ||
D Ф | Степень точности | 7 8…10 | 90 70 | 100 80 | 112 90 | 125 100 | 140 112 | 160 125 |
Размеры фасок, галтелей, диаметров промежуточных ступеней можно принять по справочным таблицам.
Таблица 23 – Галтели
| ||||
d | 20…28 | 32…45 | 50…70 | 80…90 |
r | 1,6 | 2,0 | 2,5 | 3,0 |
f | 2,0 | 2,5 | 3,0 | 4,0 |
Таблица 24 – Канавки
| |||
d | Св. 10 до 50 | Св.50 до 100 | Св. 100 |
b | 3,0 | 5,0 | 8,0 |
h | 0,25 | 0,5 | 0,5 |
r | 1,0 | 1,6 | 2,0 |
|
|
Таблица 25 – Концы валов цилиндрические
| ||||||||||||||
d | 20 | 22 | 25 | 28 | 32 | 36 | 40 | 45 | 50 | 55 | 60 | 70 | 80 | 90 |
c | 1.6 | 2.0 | 2.5 | 3.0 | ||||||||||
r | 1.0 | 1.6 | 2.0 | 2.5 |
Таблица 26 – Концы валов конические
| ||||||||
Номинальный диаметр d1 | b | h | t1 | t2 | d2 | d 3 | l2 | l3 |
20 |
4 |
4 |
2.5 |
1.8 |
М12×1,25 |
М6 |
6,5 |
8,8 |
22 | ||||||||
25 | ||||||||
28 | 5 | 5 | 3,0 | 2,3 | М16×1,5 | М8 | 9,0 | 10,7 |
32 | М10 | 11,0 | 13,0 | |||||
36 | 6 | 6 | 3,5 | 2,8 | М20×1,5 | М12 | 14,0 | 16,3 |
40 | 8 | 8 | 5,0 | 3,3 | М24×2 | М12 | 14,0 | 16,3 |
45 | 8 | 8 | 5,0 | 3,3 | М30×2 | М16 | 21,0 | 23,5 |
50 | 8 | 8 | 5,0 | 3,3 | М36×2 | М20 | 21,0 | 23,5 |
56 | 9 | 9 | 5,5 | 3,8 | М36×2 | М20 | 23,5 | 26,5 |
63 | 10 | 10 | 6,0 | 4,3 | М42×3 | М20 | 23,5 | 26,5 |
71 | 11 | 11 | 7,0 | 4,4 | М48×3 | М24 | 26,0 | 29,5 |
80 | 12 | 12 | 7,5 | 4,9 | М56×4 | М30 | 32 | 35,9 |
90 | 14 | 14 | 9,0 | 5,4 | М64×4 | М30 | 32 | 35,9 |
Таблица 27 – Канавка для выхода резьбонарезного инструмента
| Размеры канавки | Шаг резьбы | ||||
1 | 1,25 | 1,5 | 1,75 | 2 | ||
b | 3 | 4 | 4 | 4 | 5 | |
r | 1 | 1 | 1 | 1 | 1,5 | |
r1 | 0,5 | 0,5 | 0,5 | 0,5 | 0,5 | |
d К | d Р -1.5 | d Р -1.8 | d Р -2.2 | d Р -2.5 | d Р -3 |
Расчет и конструирование промежуточного вала
Расчетная схема промежуточного вала приведена на рисунке 14.
|
|
6.6.1 Определение изгибающих моментов и построение эпюр МГОР, МВЕРТ, МРЕЗ (в горизонтальной плоскости, в вертикальной и результирующего момента).
Вертикальная плоскость.
Сечения 1 и 2:
Сечение 3:
Сечение 4:
Строим эпюру МВЕРТ (рисунок 18)
Рисунок 18 – Эпюры изгибающих и крутящего моментов
Горизонтальная плоскость
Сечения 1 и 2:
Сечение 3 (слева):
Сечение 3 (справа):
Сечение 4:
Строим эпюру МГОР (рисунок 18).
Вычисляем величину результирующего момента МРЕЗ в различных сечениях по формуле:
В сечениях 1 и 2: МРЕЗ = 0
В сечении 3 (слева):
В сечении 3 (справа):
В сечении 4:
Для рассматриваемой схемы редуктора деформации кручения подвержен средний участок промежуточного вала между зубчатым колесом быстроходной ступени и шестерней тихоходной ступени моментом Т2.
Опасное сечение определяем по максимальному значению эквивалентного крутящего момента в сечениях 3 и 4 (рисунок 18).
Сечение 3:
где большее из значений
и
.
Сечение 4:
6.6.2 Конструирование промежуточного вала
Выбираем материал для вала (обычно таким же, как и у шестерни тихоходной зубчатой пары); из справочников выписываем параметры физико-механических свойств ( σВ, МПа; σ–1, МПа; τ–1, МПа; ψσ; ψτ). Допускаемое напряжение: [σ] = (0,05–0,08) σВ.
|
|
Основными материалами для валов служат углеродистые и легированные стали (таблица 28). Для большинства валов применяют термически обработанные среднеуглеродистые и легированные стали 45, 40Х; для высоконапряженных валов ответственных машин – легированные стали 40ХН, 20Х, 12ХН3А.
Таблица 28 – Основные материалы для валов
Марка стали | Диаметр заготовки, мм | Твердость НВ (не менее) | Механические характеристики, МПа | Коэффи-циент ψσ | Коэффи-циент ψτ | |||
σВ | σТ | σ–1 | τ–1 | |||||
Ст5 | Любой | 190 | 520 | 280 | 220 | 130 | 0 | 0,06 |
45 | ![]() | 240 | 780 | 540 | 360 | 200 | 0,1 | 0,09 |
45 | ![]() | 270 | 900 | 650 | 410 | 230 | 0,15 | 0,1 |
40Х | ![]() | 240 | 790 | 640 | 370 | 210 | 0,15 | 0,09 |
40Х | ![]() | 270 | 900 | 750 | 410 | 240 | 0,15 | 0,1 |
40ХН | ![]() | 270 | 920 | 750 | 420 | 230 | 0,15 | 0,1 |
20Х | ![]() | 197 | 650 | 400 | 310 | 170 | 0,1 | 0,07 |
12ХН3А | ![]() | 260 | 950 | 700 | 430 | 240 | 0,15 | 0,1 |
18ХГТ | ![]() | 330 | 1150 | 950 | 500 | 280 | 0,15 | 0,12 |
Находим расчетное значение диаметра опасного сечения промежуточного вала:
При отношении принимаем к конструированию сложную совместную деталь «вал-шестерня» (рисунок 19 а).
|
|
В случае >1,6 необходимо конструировать промежуточный вал и шестерню тихоходной зубчатой пары как две отдельные детали (рисунок 19 б).
Далее, учитывая оба варианта, находим диаметр сечения промежуточного вала под зубчатым колесом быстроходной ступени.
а)
б)
Рисунок 19 – Конструкция промежуточного вала: а – совместно с тихоходной шестерней; б – в виде отдельной детали
6.6.3 Проверочный расчет промежуточного вала
Проверочный расчет выполняется по сечению с наибольшим количеством концентраторов напряжений. Для принятой схемы редуктора таковым является сечение 3. В этом сечении два концентратора напряжений: посадка колеса быстроходной ступени с натягом и шпоночный паз. Наиболее чувствительным является второй концентратор. В случае конструкции промежуточного вала по схеме (б) – рисунок 19, проверочный расчет выполняется по сечению, нагруженному наибольшим вращающим моментом.
Проверку статической прочности выполняют в целях предупреждения пластических деформаций в период действия кратковременных перегрузок (при пуске, разгоне, реверсировании, торможении, срабатывании предохранительного устройства.
Величина перегрузки зависит от конструкции привода. При наличии предохранительной муфты величину перегрузки определяет момент, при котором эта муфта срабатывает. При отсутствии предохранительной муфты возможную перегрузку условно принимают равной перегрузке при пуске приводного электродвигателя.
Коэффициент перегрузки:
,
где Т max - максимальный кратковременный вращающий момент электродвигателя при пуске;
Т – номинальный вращающий момент (расчетный).
Для большинства асинхронный электродвигателей КП = 2,2
В расчете определяют нормальные σ и касательные τ напряжения в рассматриваемом сечении вала при действии максимальных нагрузок:
где - максимальный изгибающий момент, Н
м;
- максимальный вращающий момент, Н
м;
- максимальная окружная сила, Н;
W и W К – моменты сопротивления вала при расчете на изгиб и кручение, мм3;
А – площадь поперечного сечения, мм2.
Частные коэффициенты запаса прочности по нормальным и касательным напряжениям:
Общий коэффициент запаса прочности по пределу текучести при совместном действии нормальных и касательных напряжений:
Статическую прочность считают обеспеченной, если , где
= 1,3…2 – минимально допустимое значение общего коэффициента запаса по текучести (назначают в зависимости от ответственности конструкции и последствий разрушения вала).
Моменты сопротивления W при изгибе, WK при кручении и площадь А поперечного сечения вычисляют по формулам:
- для сплошного круглого сечения диаметром D:
- для полого круглого сечения с наружным диаметром D и внутренним d:
- для вала с одним шпоночным пазом (рисунок 20):
Рисунок 20 – К определению моментов сопротивления изгибу и кручению
Уточненный расчет на сопротивление усталости отражает влияние разновидности цикла напряжений, статических и усталостных характеристик материалов, размеров, формы и состояния поверхности. Расчет выполняют в форме проверки коэффициента запаса прочности S, минимально допустимое значение которого принимают в диапазоне [ S ] = 1,5…2,5 в зависимости от ответственности конструкции и последствий разрушения вала.
Для каждого из установленных предположительно опасных сечений вычисляют коэффициент S:
где Sσ и Sτ - коэффициенты запаса по нормальным и касательным напряжениям, определяемые по зависимостям:
Здесь σа и τа – амплитуды напряжений цикла в опасном сечении:
σт и τт – средние напряжения цикла. В расчетах валов принимают, что нормальные напряжения изменяются по симметричному циклу, поэтому σт = 0, а касательные напряжения – по отнулевому циклу: τа = τт;
ψσ d и ψτ d – коэффициенты влияния асимметрии цикла напряжений для рассматриваемого сечения.
Тогда:
Пределы выносливости вала в рассматриваемом сечении:
где σ-1 и τ-1 – пределы выносливости гладких образцов при симметричном цикле изгиба и кручения (таблица 28);
Кσ d и Кτ d – коэффициенты снижения предела выносливости. Вычисляются по зависимостям:
где Кσ и Кτ – эффективные коэффициенты концентрации напряжений (таблица 29, 30);
К dσ и К dτ – коэффициенты влияния абсолютных размеров поперечного сечения (таблица 31, 32);
К Fσ и К Fτ – коэффициенты влияния качества поверхности (таблица 33);
К V – коэффициент влияния поверхностного упрочнения (таблица 34).
Таблица 29 – Значения коэффициентов Кσ и Кτ для шпоночного паза
σВ, МПа | Кσ при выполнении паза фрезой | Кτ | |
Концевой | Дисковой | ||
500 | 1,8 | 1,5 | 1,4 |
700 | 2,0 | 1,55 | 1,7 |
900 | 2,2 | 1,7 | 2,05 |
1200 | 2,65 | 1,9 | 2,4 |
Таблица 30 – Значения коэффициентов Кσ и Кτ для шлицевых и резьбовых участков валов
σВ, МПа | Кσ для | Кτ для шлицев | Кτ для резьбы | ||
Шлицев | Резьбы | Прямобочных | Эвольвентных | ||
500 | 1,45 | 1,8 | 2,25 | 1,43 | 1,35 |
700 | 1,6 | 2,2 | 2,50 | 1,49 | 1,7 |
900 | 1,7 | 2,45 | 2,65 | 1,55 | 2,1 |
1200 | 1,75 | 2,9 | 2,8 | 1,6 | 2,35 |
Таблица 31 – Значения коэффициентов К dσ и К dτ
Вид деформации и материала | К dσ (К dτ) при диаметре вала d, мм | |||||
20 | 30 | 40 | 50 | 70 | 100 | |
Изгиб для углеродистой стали | 0,92 | 0,88 | 0,85 | 0,81 | 0,76 | 0,71 |
Изгиб для легированной стали | 0,83 | 0,77 | 0,73 | 0,70 | 0,65 | 0,59 |
Кручение для всех сталей | 0,83 | 0,77 | 0,73 | 0,70 | 0,65 | 0,59 |
Таблица 32 – Значения отношений и
в местах установки на валу деталей с натягом
Диаметр вала d, мм |
|
| ||||||
500 | 700 | 900 | 1200 | 500 | 700 | 900 | 1200 | |
30 | 2,6 | 3,3 | 4,0 | 5,1 | 1,5 | 2,0 | 2,4 | 3,05 |
40 | 2,75 | 3,5 | 4,3 | 5,4 | 1,65 | 2,1 | 2,6 | 3,25 |
50 | 2,9 | 3,7 | 4,5 | 5,7 | 1,75 | 2,2 | 2,7 | 3,4 |
60 | 3,0 | 3,85 | 4,7 | 5,95 | 1,8 | 2,3 | 2,8 | 3,55 |
70 | 3,1 | 4,0 | 4,85 | 6,15 | 1,85 | 2,4 | 2,9 | 3,7 |
80 | 3,2 | 4,1 | 4,95 | 6,3 | 1,9 | 2,45 | 3,0 | 3,8 |
90 | 3,3 | 4,2 | 5,1 | 6,45 | 1,95 | 2,5 | 3,05 | 3,9 |
100 | 3,35 | 4,3 | 5,2 | 6,6 | 2,0 | 2,55 | 3,1 | 3,95 |
Примечание. При установке с натягом обойм подшипников табличное значение следует умножить на 0,9.
Таблица 33 – Значения коэффициентов К Fσ и К Fτ
Вид механической обработки | Параметр шероховатости Ra, мкм | К Fσ при σВ, Н/мм2 (МПа) | К Fτ при σВ, Н/мм2 (МПа) | ||
![]() | >700 | ![]() | >700 | ||
Шлифование тонкое | До 0,2 | 1 | 1 | 1 | 1 |
Точение тонкое | 0,2 – 0,98 | 0,93 – 0,99 | 0,91 – 0,99 | 0,96 – 0,99 | 0,95 – 0,99 |
Шлифование чистовое | 0,8 – 1,6 | 0,89 – 0,93 | 0,86 – 0,91 | 0,94 – 0,96 | 0,92 – 0,95 |
Точение чистовое | 1,6 – 3,2 | 0,86 – 0,89 | 0,82 – 0,86 | 0,92 – 0,94 | 0,89 – 0,92 |
Таблица 34 – Значения коэффициента К V
Вид упрочнения поверхности вала | Значения К V при: | ||
Кσ = 1,0 | Кσ = 1,1…1,5 | Кσ ![]() | |
Закалка ТВЧ | 1,0 - 1,3 | 1,6 – 1,7 | 2,4 – 2,8 |
Азотирование | 1,15 - 1,25 | 1,7 – 1,9 | 2,0 – 3,0 |
Накатка роликом | 1,2 – 1,4 | 1,5 – 1,7 | 1,8 – 2,2 |
Дробеструйный наклеп | 1,1 – 1,3 | 1,4 – 1,5 | 1,6 – 2,5 |
Без упрочнения | 1,0 | 1,0 | 1,0 |
Коэффициенты влияния асимметрии цикла для рассматриваемого сечения вала:
где ψσ и ψτ – коэффициенты чувствительности материала к асимметрии цикла напряжений (таблица 28).
Дата добавления: 2019-11-16; просмотров: 278; Мы поможем в написании вашей работы! |
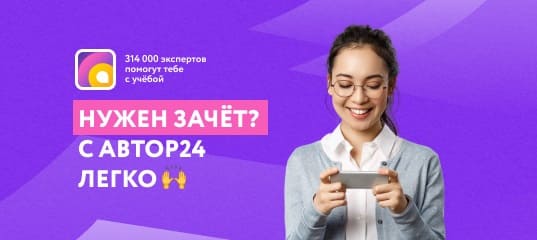
Мы поможем в написании ваших работ!