Конструирование вала-шестерни
Конструирование деталей и узлов редуктора
Учебное пособие
Для выполнения курсового проекта по дисциплине
«Детали машин и основы конструирования»
для студентов всех форм обучения
Екатеринбург
2019
Конструирование деталей и узлов редуктора. Учебное пособие для выполнения курсового проекта по дисциплине «Детали машин и основы конструирования». Екатеринбург, ФГБОУ ВО «Уральский государственный аграрный университет», 2019. 40с.
Автор: | канд. техн. наук, доцент | Н.Н. Эльяш |
Пособие предназначено для выполнения графической части курсового проекта. Приведены основные принципы конструирования зубчатых колес, валов, корпусных деталей редуктора. Изложены вопросы выбора подшипников и проверочного расчета их на долговечность; методика уточненного расчета валов по опасным сечениям, расчет шпоночных соединений. В приложениях имеются рекомендации по оформлению графической части проекта.
Рекомендовано к печати научно-методической комиссией факультета ТТМС
Протокол от ___._______._____г. № ___.
Председатель научно-методической комиссии | |||||||
| А.Н. Зеленин | ||||||
| © | ФГБОУ ВО «Уральский государственный аграрный университет», 2019 | |||||
| © | Эльяш Н.Н., 2019 | |||||
СОДЕРЖАНИЕ
№ п/п | Название раздела | Стр. |
1. | ОБЩИЕ ПРИНЦИПЫ КОНСТРУИРОВАНИЯ ДЕТАЛЕЙ МАШИН……………… | 4 |
2. | ЗУБЧАТЫЕ КОЛЕСА И ВАЛЫ………………………………………………….. 2.1. Конструирование вала-шестерни……………………………………………. 2.2. Конструирование выходного вала……………………………………………. 2.3. Конструирование зубчатого колеса…………………………………………. 2.3.1. Прямозубые и косозубые цилиндрические колеса………………………… 2.3.2.Шевронные колеса…………………………………………………………… | 5 5 11 16 15 17 |
3. | РАЗРАБОТКА КОМПОНОВОЧНОГО ЧЕРТЕЖА РЕДУКТОРА…………….. 3.1. Выбор подшипников. Определение расстояния между опорами. Эскизная компоновка редуктора……………………………………………………………. 3.2. Конструирование сборочных узлов редуктора……………………………… | 19 19 22 |
4. | ПРОВЕРКА ПОДШИПНИКОВ НА ДОЛГОВЕЧНОСТЬ……………………… 4.1. Определение реакций в опорах. ……………………………………………… 4.2. Расчетная долговечность подшипников…………………………………….. | 26 26 28 |
5. | ПРОВЕРОЧНЫЙ РАСЧЕТ ВАЛОВ И СОЕДИНЕНИЙ………………………. 5.1. Построение эпюр крутящих и изгибающих моментов. Определение эквивалентного момента....……………………………………………………… 5.2. Проверочный расчет вала по опасным сечениям……………………………. 5.3. Проверка шпоночных соединений на смятие ……………………………… | 30 30 33 35 |
ЛИТЕРАТУРА……………………………………………………………………… | 37 | |
ПРИЛОЖЕНИЯ | 38 |
Общие принципы конструирования деталей машин
|
|
При изучении дисциплины «Детали машин и основы конструирования» рассматриваются вопросы выбора материала, способа термообработки, геометрии деталей и точности их изготовления. Конструирование – это процесс создания чертежей механизма или машины на основе проектных и проверочных расчетов. В процессе выполнения расчета деталей рассматривают различные варианты с целью получения оптимальной конструкции с учетом требований экономичности, надежности, технологичности их изготовления. На первом этапе производят проектный расчет, который позволяет определить основные размеры деталей. Проверочный расчет выполняется после окончательного конструирования деталей, с учетом их формы и размеров. Проверочный расчет позволяет определить ресурс работы деталей, выполнить проверку на прочность по допускаемым напряжениям в реальных условиях эксплуатации.
|
|
Деталью называют часть машины, изготовленную без применения сборочных операций.
Узлом называют сборочную единицу, состоящую из деталей, имеющих общее функциональное назначение (вал в сборе с подшипниками, вал с зубчатым колесом, муфты, подшипники, и т.д.).
При расчетах и конструировании строго должны соблюдаться стандарты. Это обеспечивает взаимозаменяемость деталей и узлов в машине, облегчает ремонт; кроме того, стандартные детали изготавливаются на специализированных заводах, что повышает их качество и снижает стоимость[4c. 4-7; с.12].
При выполнении курсового проекта студент выполняет расчет деталей и узлов редуктора; графическая часть состоит из конструирования валов, зубчатых колес или сборочных узлов и может быть выполнена по одному из
4-х вариантов, примеры которых даны в приложении. В зависимости от полученных в результате расчетов размеров деталей чертежи могут быть представлены на листах формата А4 или А3 в масштабе 1:1 или 1:2 и подшиты к расчетно-пояснительной записке. Компоновочный чертеж на миллиметровой бумаге выполняется во всех случаях и в обязательном виде подшивается к расчетно-пояснительной записке.
В соответствии с правилами оформления чертежей на каждом листе должна быть выполнена основная надпись по ГОСТ2.104-68.
|
|
Зубчатые колеса и валы
Конструирование вала-шестерни
Шестерней называют меньшее из двух колес, входящих в зацепление,
в редукторах шестерня является ведущим звеном. Шестерни конструируют
в двух исполнениях: отдельно от вала или за одно целое с валом(вал-шестерня).
При необходимости перемещения шестерни вдоль вала по условиям работы или сборки (например, в коробках передач) шестерню изготавливают отдельно от вала. Раздельное изготовление шестерни и вала снижает точность и увеличивает стоимость производства, поскольку увеличивается число посадочных поверхностей, требующих точной обработки. Кроме этого возникает необходимость применения шпоночного или шлицевого соединения. Шпоночные пазы ступицы и вала ослабляют сечения, требует жестких допусков на симметричность, параллельность граней шпоночного паза и т.д.
В большинстве случаев диаметр впадин зубьев шестерни превышает диаметр вала, поэтому обычно ее изготавливают заодно с валом, и эта деталь называется вал-шестерня. Это позволяет повысить жесткость и снизить стоимость изготовления.
Входной вал одноступенчатого цилиндрического редуктора конструируем в виде вала-шестерни. Для этого необходимо определить некоторые размеры
[1, c.65-66].
Ранее, при расчете энергосиловых параметров привода, был определен диаметр входного конца быстроходного вала. Если входной вал редуктора соединяется непосредственно с электродвигателем через муфту, то он должен быть согласован с диаметром вала электродвигателя и со стандартной муфтой ГОСТ 23360-78. Этот диаметр обозначим d, при этом входной конец может быть цилиндрическим или коническим. Цилиндрический конец проще в изготовлении; конический конец обеспечивает более точное соединение, легкую сборку узла и его демонтаж. Конусность концевого участка вала принимают 1:10[1, c.262].
В том случае, когда проектируем конический конец вала (рис.1), то под размером d следует понимать максимальный диаметр конического участка. Определяем длины участков; полученные значения следует округлить до ближайших больших стандартных [1, c .481]:
длина посадочного конца lM = 1,5d;
длина цилиндрического участка l = 0,15d ;
диаметр резьбы d р = 0,9 (d - 0,1lM);
длина резьбы l р = 1,2 d р .
Рис.1. Конический участок вала с фиксирующей гайкой.
Определяем диаметр следующего участка вала, который предназначен для посадки подшипника d П (рис.2). Для осевой фиксации деталей (полумуфты) диаметр следующего участка должен быть больше на величину заплечиков t.
d П = d + 2tцил(tкон);
Рекомендуемые высоты заплечиков для цилиндрических и конических концов валов, а также размеры фасок приведены в таблице 1 [1, c .47]:
Таблица 1
Размеры элементов валов
d | 17-22 | 24-30 | 32-38 | 40-44 | 45-50 | 52-58 | 60-65 | 67-75 | 80-85 |
tцил | 3 | 3,5 | 3,5 | 3,5 | 4 | 4,5 | 4,6 | 5,1 | 5,6 |
tкон | 1,5 | 1,8 | 2,0 | 2,3 | 2,3 | 2,5 | 2,7 | 2,7 | 2,7 |
r | 1,5 | 2 | 2,5 | 2,5 | 3 | 3 | 3,5 | 3,5 | 4 |
f | 1 | 1 | 1,2 | 1,2 | 1,6 | 2 | 2 | 2,5 | 2,5 |
Примечание: r- координата фаски подшипника; f – размер фаски колеса.
Полученный размер d П необходимо согласовать с диаметром внутреннего кольца подшипника! В одноступенчатых цилиндрических редукторах принимают однорядные шариковые подшипники легкой или средней серии (ГОСТ 8338-75 и ГОСТ 7242-81). Последние две цифры в маркировке подшипников – это посадочный диаметр, деленный на 5. Предыдущая цифра в маркировке подшипника обозначает серию: 1- особо легкая, 2- легкая, 3- средняя.*)
Например, подшипник № 211 означает: 2 - легкая серия, внутренний посадочный диаметр d П = 11 ∙ 5 = 55мм. Исходя из этого участок вала под подшипники должен иметь диаметр d П, вычисленный по приведенному выше соотношению, но значение d П необходимо принять кратным 5-ти, то есть последняя цифра в обозначении номера подшипника должна быть 5 или 0
[2, c. 392-394].
Остальные размеры, показанные на рис.2:
длина промежуточного участка l П = 1,4d П ;
b 1 , d 1 – ширина зубчатого венца и диаметр шестерни, соответственно;
В – ширина кольца подшипника.
____________________________________________________________________
*) Примечание:Данная маркировка принята для случаев, когда диаметр внутреннего кольца подшипника превышает 17 мм.
Рис.2. Конструирование сборочного узла вала-шестерни с подшипниками
Если проектируем цилиндрический конец входного вала, то фиксирующая гайка отсутствует и размеры l р = 0; l = 0. Длина входного конца вала предварительно вычисляется также, как длина конического, т.е. l М = 1,5d.
Рис.3. Цилиндрический участок входного вала.
Затем длина участка lM уточняется в зависимости от расчетной длины шпонки, соединяющей вал с муфтой (рис.3).
Расчетная длина шпонки l ш вычисляется по формуле [1, c.121]
,
где Т – вращающий момент, Н∙мм;
D – диаметр вала, мм (для конического конца принимают d = d ср);
h – высота шпонки, мм; t 1 – глубина врезания шпонки в паз вала, мм.
Размеры h и t 1 принимаются для стандартной шпонки в зависимости от диаметра вала по таблице 2 [1, c.488];
[σсм] = 110…190 Н/мм2 - допускаемое напряжение смятия для стальных шпонок (например, сталь 45,… Ст.6).
Таблица 2
Шпонки призматические (ГОСТ 23360-78). Размеры, мм
Диаметр вала d | Сечение шпонки bxh | Глубина паза | Длина l | |
Вала t1 | Втулки t2 | |||
12…17 | 5 x 5 | 3,0 | 2,3 | 10 - 56 |
17…22 | 6 x 6 | 3,5 | 2,8 | 14 - 70 |
22…30 | 8 x 7 | 4,0 | 3,3 | 18 - 90 |
30…38 | 10 x 8 | 5,0 | 3,3 | 22 - 110 |
38…44 | 12 х 8 | 5,0 | 3,3 | 28 - 140 |
44…50 | 14 x 9 | 5,5 | 3,8 | 36 - 160 |
50…58 | 16 x 10 | 6,0 | 4,3 | 45 - 180 |
58…65 | 18 x 11 | 7,0 | 4,4 | 50 - 200 |
65…75 | 20 x 12 | 7,5 | 4,9 | 56 - 220 |
75…85 | 22 x 14 | 9,0 | 5,4 | 63 - 250 |
85…95 | 25 x 14 | 9,0 | 5,4 | 70 - 280 |
Примечание: Длину шпонки выбирают из ряда: 6, 8, 10, 12, 14, 16, 18, 20, 25, 28, 32, 36, 40, 45, 50, 56, 63, 70, 80, 90, 100, 125, 140, 160, 180, 200 …(до 500). Пример условного обозначения шпонок: Шпонка 20 x12 x 90 ГОСТ 23360-78
Окончательно длину участка вала lM с учетом размеров шпоночного паза назначают на 8…10 мм больше, чем lp [1, c.476].
Дата добавления: 2020-01-07; просмотров: 885; Мы поможем в написании вашей работы! |
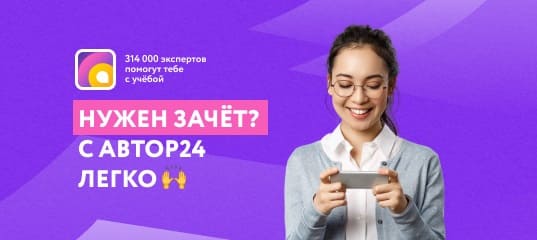
Мы поможем в написании ваших работ!