Нитроцементация (азотонауглероживание)
Нитроцементация – химико-термическая обработка сталей, состоящая в одновременном насыщении деталей углеродом и азотом. При нагреве в аустенитной области азот способствует ускорению диффузии углерода. Это даёт возможность снижения температуры насыщения, что имеет следующие преимущества: уменьшается степень окисления в процессе ХТО; уменьшается коробление при охлаждении; предотвращается рост зерна.
Целью нитроцементации являетсяповышение твердости, износостойкости и коррозионной стойкости. Нитроцементация применяется для низкоуглеродистых и низклолегированных сталей (сумма элементов – менее 5 %) и имеет широкое применение в автомобильной и автотракторной промышленности для нешлифуемых деталей сложной формы. Насыщающая среда – углеродсодержащий газ с 3 - 5 % аммиака. Температура процесса – не выше 880ºС (обычно 840 - 860ºС). Продолжительность процесса 4 – 10 часов. Термическая обработка проводится непосредственно с температуры нитроцементации. Заключительной операцией является отпуск при 160 - 180ºС.
Результат: глубина диффузионного слоя составляет 0,3 - 0,8 мм, твёрдость 58 - 64 HRC или 570 - 700 НV; высокий предел выносливости; меньшая степень коробления, чем после цементации.
Разновидностью процесса нитроцементации является цианирование, которое проводится в расплавах солей, содержащих цианистый натрий. Процесс является более производительным, чем цементация. Цианированные детали по сравнению с цементованными, имеет более высокую износостойкость и предел выносливости. Однако существенным недостатком процесса является сильная ядовитость цианистых солей.
|
|
Карбонитрация – процесс одновременного насыщения азотом и углеродом в расплавах нетоксичных солей. Карбонитрация отличается тем, что применяются неядовитые соли.
Сравнение трёх процессов насыщения сталей приведено в таблице 2.11.
Таблица 2.11
Параметры процессов ХТО, характеристики слоя и свойства сталей
| Вид ХТО | |||||
Цементация | Азотирование | Нитроцементация | ||||
Технология ХТО | Температура, °С | 910…950 | 500…600 | 820…860 | ||
Время, ч | 5 - 10 | 20 - 60 | 1 | |||
Свойства слоя | h,мм | 1,5 - 2 (до 6) | 0,2 - 0,4 | 0,3 - 1 | ||
Твёрдость, HRC | 58 - 62 | 62 - 64 | 58 - 64 | |||
Особенности термообработки | После ХТО - 2 закалки + отпуск | До ХТО – закалка + отпуск | Совмещение ХТО и ТО: закалка при температуре нитроцементации | |||
Преимущества
| Глубокие слои | Высокая твёрдость слоя | Высокая производительность | |||
Недостатки процесса | Окисление поверхности, необходимость шлифования | Большая длительность | - | |||
Область применения
(детали) | Тяжелонагру- женные | Детали сложной формы, тонких сечений | Детали нешлифуемые |
Химико-термическая обработка с диффузионным насыщением металлами (диффузионная металлизации).
Диффузионная металлизация – процесс насыщения поверхностного слоя металла (изделия) одним или несколькими металлическими элементами, происходящий при химико-термической обработке.
Цельдиффузионной металлизации – обеспечить различные физико-химические свойства поверхности:коррозионную стойкость, жаростойкость, износостойкость и др.
В зависимости от элемента (элементов), наносимых на поверхность, процессы диффузионной металлизации носят названия: борирование, хромирование, алитирование, ванадирование, титанирование, а при нанесении многокомпонентных покрытий – бороалитирование, хромоалитирование и др. При диффузионной металлизации используют свойства наносимых металлов.
Алюминий и хром являются стойкими к воздействию агрессивной среды при обычных температурах (т.е. коррозионно - стойкими) и при высоких температурах – в атмосфере горячих газов, (т.е. жаростойкими).
Титан, ванадий и ниобий имеют сильное сродство к углероду и образуют в поверхностном слое карбиды VC, NbC, TiC, более твёрдые и более термостабильные, чем цементит или нитриды. В связи с этим износостойкость деталей после металлизации в несколько раз выше, чем после цементации или азотирования. Кроме того, эти карбиды – более термостойкие, поэтому износостойкость сохраняется до температур порядка 1000°С.
|
|
Недостаткомтаких процессов как хромирование, ванадирование, ниобирование и титанирование является низкая скорость диффузии этих элементов (на 2 - 4 порядка ниже подвижности углерода и азота в стали). Вследствие этого для получения слоёв толщиной 0,1 – 0,3 мм необходим нагрев до температур 950 – 1100°С, что не всегда приемлемо из-за укрупнения зерна.
Поверхностная закалка сталей
Основное назначение поверхностной закалки: повышение твердости, износостойкости и предела выносливости деталей (зубьев шестерен, шеек валов, направляющих станин металлорежущих станков и др.). Сердцевина детали остается вязкой и хорошо воспринимает ударные и другие нагрузки.
Общим для всех способов поверхностной закалки является нагрев поверхностного слоя детали до температуры выше критической точки Ас3 с последующим быстрым охлаждением для получения структуры мартенсита.
|
|
При поверхностной закалке мартенсит образуется только в приповерхностном слое, а в сердцевине протекает диффузионный распад аустенита с образование структур различной степени дисперсности (перлит, сорбит, троостит). Вязкая сердцевина обеспечивает хорошее сопротивление детали ударным нагрузкам.
Для поверхностной закалки могут применяться различные источника нагрева поверхности: газопламенный, токи высокой частоты, контактный нагрев, высококонцентрированные источники энергии (лазер, электронный пучок, плазменные потоки и т.д.).
Для деталей несложной формы наиболее часто применяют индукционную закалку с нагревом токами высокой частоты (ТВЧ). При этом способе изделие помещается в переменное электромагнитное поле. Для создания электромагнитного поля используется индуктор – одновитковый или многовитковый контур медной трубы, через который пропускается переменный электрический ток. Нагрев происходит вследствие того, что вблизи поверхности изделия индуктируются вихревые токи (токи Фуко). Охлаждение при закалке производится через отверстия индуктора (после выключения тока). Оно может быть водным спрейерным или водо-воздушным.
Преимущества закалки ТВЧ по сравнению с объёмной закалкой:
–более мелкое зерно, так как высока скорость нагрева и отсутствует выдержка в аустенитной области;
–повышение предела выносливости: в два-три раза по сравнению с объемной закалкой;
–сокращение времени термообработки, повышение производительности;
–получение изделий без окалины;
–уменьшение коробления при закалке;
–возможность полной механизации и автоматизации процесса (включения его в поточную линию обработки, без разрыва технологического цикла).
Дата добавления: 2020-01-07; просмотров: 252; Мы поможем в написании вашей работы! |
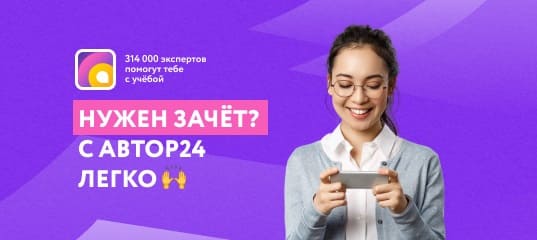
Мы поможем в написании ваших работ!