Упрочняющая термическая обработка: закалка и старение.
Упрочняющей термической обработкой или термическим упрочнением называются технологические операции, в результате которых в сплавах достигается уровень прочности, повышенный со сравнению с отожженным (или нормализованным) состоянием.
Термин «термическое упрочнение» применяют к обработке, которая включает два этапа: закалку и старение или закалку и отпуск.
Закалка – операция термической обработки, которая заключается в нагреве сплавов в высокотемпературную область твердых растворов и охлаждении с высокой скоростью, предотвращающей равновесные фазовые превращения. В зависимости от диаграммы состояния, т.е. от фазовых превращений, характерных для данной системы легирования, результатом закалки является неравновесная фаза:
– пересыщенный твердый раствор («закалка на пересыщенный твердый раствор»);
– мартенсит – твёрдый раствор, получаемый в полиморфных сплавах, который может быть как пересыщенным, так и непересыщенным («закалка на мартенсит»).
Вторым этапом термического упрочнения, создающим метастабильное состояние, являются такие операции какстарениеилиотпуск.
Старение или отпуск – операции термической обработки, которые заключаются в нагреве ниже температур закалки с последующим произвольным охлаждением. При старении или отпуске формируется то структурно-фазовое состояние, которое и определяет конечный комплекс механических свойств материала (детали).
|
|
Термическое упрочнение широко применяется для ответственных деталей, изготавливаемых из углеродистых и легированных сталей, а также для сплавов на основе цветных металлов: никелевым, алюминиевым, магниевым, титановым, медным и др.
Упрочняющую термическую обработку, состоящую из закалки со старением, применяют к сплавам, в которых возможно при быстрой закалке получить пересыщенный легирующим элементом твёрдый раствор. Это сплавы на основе цветных металлов: алюминиевые, магниевые, титановые, медные, никелевые, а также высоколегированные мартенситостареющие стали и титановые сплавы.
Рис. 2.26. Схема изменения твердости стареющих сплавов в зависимости
от температуры (а) и времени (б) старения: t 1 ‹ t 2 ‹ t 3 ; о – максимум твёрдости;
А – область недостаривания; В – область перестаривания
При старении в сплавах образуются высокодисперсные частицы промежуточных фаз. Эти частицы существенно тормозят перемещение дислокаций в сплавах, что и обеспечивает повышенную прочность. При этом, варьируя температуру и время старения, можно получить различное сочетание прочности, пластичности и ударной вязкости (рис. 2.26).
Закалка и отпуск сталей.
|
|
Цель закалки и отпуска – двухэтапной термообработкисостоит вобеспечении повышенной прочности (по сравнению с отжигом и нормализацией) и необходимого комплекса механических свойств.
Закалка с отпуском используется для широкой номенклатуры углеродистых и легированных машиностроительных и инструментальных сталей. Эти стали относятся к диаграммам состояния «железо - углерод» или «железо - углерод - легирующий элемент».
Закалка сталей на мартенсит.
Закалка сталей - сплавов на основеполиморфного металла – этооперация термической обработки, заключающаяся в нагреве в однофазную аустенитную область (иногда в двухфазные области), и быстром охлаждении со скоростью, предотвращающей распад аустенита по диффузионному механизму.
Цель закалки – получение мартенсита, как самостоятельной фазы, так и сочетании с аустенитом, трооститом или цементитом. Полученное структурно - фазовое состояние является подготовительным этапом для проведения последующего отпуска.
В углеродистых сталях неравновесная фаза мартенсит как результат сдвигового превращения одновременно является: твердым раствор внедрения; твердым раствором внедрения, пересыщенным по отношению к равновесному содержанию углерода в феррите при комнатной температуре – 0,006 %;
|
|
Кристаллическая решетка мартенсита – тетрагональная объемноцентрированная существенно отличается от исходной решетки аустенита (ГЦК). Тетрагональность решетки (отношение осей с/а) увеличивается с повышением содержания углерода.
Вследствие большой разницы в удельных объемах аустенита и образующегося из него мартенсита (около 3 %), результатом превращения является значительный фазовый наклеп. Фазовый наклеп – пластическая деформация, реализующаяся внутри зерна, которая осуществляется не внешним воздействием, а только за счет фазового превращения.
Значительная разница в удельных объемах аустенита и мартенсита углеродистых сталей (около 3 %) создает не только пластическую деформацию внутри зерен твердого раствора, но и упругую деформацию в объеме детали. К этому добавляются и термические напряжения. В результате резкого охлаждения при закалке детали с мартенситной структурой склонны к «короблению» («поводке») – неравномерному изменению формы и размеров, которые тем больше, чем сложнее форма детали. Это является главным недостатком закалки углеродистых сталей.
|
|
В ряде углеродистых и легированных сталей при закалке из аустенитной области возможно протекание бейнитного превращения (рис. 2.26, область А → Б).
Полученная в результате бейнитного превращения двухфазная структура (α + Ц) не называется перлитом, потому что получена не при эвтектоидном превращении. Кроме того, частицы карбида не имеет пластинчатого строения; при этом они очень дисперсны.
По дисперсности, расположению карбидов и структуре α - фазы различают верхний и нижний бейнит. Наилучшими свойствами обладает нижний бейнит, образующийся при температурах ниже 350ºС. Дисперсные частицы карбида расположены внутри зерен феррита. Такая структура обеспечивает сочетание высокой прочности, пластичности и ударной вязкости.
Изотермическая закалка, использующая бейнитное превращение, широко применяется для деталей из легированных сталей, обеспечивая им высокую конструкционную прочность.
Технология закалки.
Температуру закалки выбирают по отношению к критическим точкам (линиям) на диаграмме состояния – Ас1, Ас3, Асm. Закалка от температур выше Ас3 и Асm, называется полной закалкой, а закалка от температур в интервале Ас1 – Ас3 или Ас1 – Асm называется неполной закалкой.
К сталям доэвтектоидным применяют полную закалку, т.е. из аустенитной области. от температур выше Ас3 на 30 - 50ºС; к сталям заэвтектоидным применяют неполную закалку, т.е. из области «аустенит + цементит», от температур на 30 - 50ºС выше Ас1 .
Скорость охлаждения при закалке для получения мартенсита выбирают в соответствии с термокинетической диаграммой (ТКД) распада переохлажденного аустенита. Скорость охлаждения при закалке должна исключить какое-либо равновесное превращение. Наименьшая скорость, при которой получается мартенсит называется критической скоростью охлаждения при закалке Vкрит (на рис. 1.33 это скорость V4), поэтому их линии на ТКД должна находится левее начала С - образной кривой распада (рис. 2.27).
Рис. 2.27. Схема скоростей охлаждения из аустенитной области, дающих в центре
образца( V ц ), перлитную структуру на поверхности( V п ) – мартенситную
Критическая скорость охлаждения сталей (Vкрит) – минимальная скорость охлаждения, при которой аустенит превращается в мартенсит.
Для мартенситного превращения характерен определённый температурный интервал превращения: существуют температуры начала и конца превращения: Мн и Мк находящиеся ниже выступа С-образной кривой диффузионного распада (рис. 2.27).
Прокаливаемость – одна из важнейших технологических характеристик при термической обработке стали.
Прокаливаемость определяется темпом, с какой температура во время быстрого охлаждения распространяется по сечению детали конкретного размера с конкретной теплопроводностью. При высокой скорости охлаждения обеспечить мартенситное превращение в интервале температур Мн и Мк, т.е. «прокалить» деталь возможно только при небольших ее размерах. На деталях больших размеров охлаждение с критической скоростью успевает произойти только в приповерхностных слоях. А в глубинных слоях охлаждение происходит с меньшей, чем критическая, скоростью, что приводит к распаду аустенита уже не сдвиговому, в диффузионному механизму. Результатом различия скоростей охлаждения по сечению детали является различие в фазовом составе: в приповерхностном слое - мартенсит, а в центре - феррит + цементит.
Прокаливаемость – это свойство стали приобретать в результете закалки мартенситную или мартенсито - трооститную структуру с высокой твердостью в слое определенного размера. Количественно прокаливаемость характеризуется критическим диаметром.
Критический диаметр – максимальный диаметр детали, при котором в результате закалки получается мартенситная или полумартенситная (50 % мартенсита + 50 % троостита) структура. Критический диаметр обратно пропорционален критической скорости охлаждения:
dкр = f (1/Vкр).
Для того, чтобы прокалить насквозь детали крупного сечения, их изготавливают их легированных сталей, потому что все легирующие элементы (кроме кобальта) снижают критическую скорость закалки.
Способы закалки разделяются по следующим признакам:
– по среде охлаждения (закалка в воде, в масле, на воздухе, в полимерных средах);
– по объему детали, к которому применяется закалка – объемная и поверхностная;
– по ступенчатости охлаждения (закалка в двух средах, ступенчатая закалка, изотермическая и др.).
Применение различных сред охлажденияпри объёмной закалке определяется критической скоростью охлаждения. Снижение критической скорости охлаждения сталей позволяет переходить к более «мягким» средам: от воды к маслу и далее к воздуху.
Применение объемной или поверхностной закалки диктуется требованиями, предъявляемыми к изделиям. Для большинства деталей применяют объемную закалку, когда мартенситная (мартенситно - трооститная) структура получается по всему сечении.
Поверхностную закалку применяют для деталей, в которых по условиям работы требуется высокая поверхностная твердость, износостойкость, а также высокий предел выносливости.
Применение ступенчатого охлаждения при объёмной закалке вызвано стремлением к снижению того высокого уровня остаточных упругих напряжений, которые характерны для закаленных стальных деталей.
Для ослабления возникающих напряжений, используют различные способы охлаждения (рис. 2.28).
«Тепловые» напряжения снижаются при понижении скорости охлаждения в интервале температур Мн - Мк (закалка в двух средах). Закалку в двух средах осуществляют при погружении детали сначала в воду – для быстрого прохождения температурного интервала минимальной устойчивости аустенита, а затем в масло – для охлаждения с меньшей скоростью в интервале мартенситного превращения.
Рис. 2.28. Схемы различных способов объемной закалки сталей:
Дата добавления: 2020-01-07; просмотров: 1065; Мы поможем в написании вашей работы! |
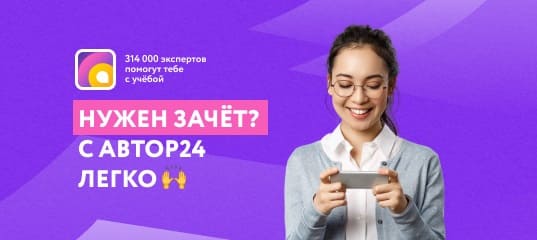
Мы поможем в написании ваших работ!