Поверхностная обработка сталей и сплавов.
Поверхностную обработку сталей и сплавов проводят с целью обеспечения таких свойств, как повышенная твёрдость, износостойкость, контактная выносливость, усталостная прочность, коррозионная стойкость и жаростойкость. Поверхностная обработка может быть проведена двумя путями:
С изменением химического состава поверхностного слоя: химико-термическая обработка, нанесение покрытий, лазерное легирование.
Без изменения химического состава поверхностного слоя: поверхностная закалка, поверхностное пластическое деформирование (ППД), лазерная обработка (без легирования), электроискровая обработка и др.
Химико-термическая обработка сплавов.
Химико - термическая обработка (ХТО) – технологический процесс, сочетающий термическое воздействие с изменением химического состава поверхностного слоя детали. Технология ХТО состоит в нагреве деталей в специальных активных атмосферах (твердых, жидких, газообразных), т.е. в атмосферах с повышенной концентрацией элемента, изменяющего химический состав поверхностного (приповерхностного) слоя.
Существуют две разновидности ХТО:
1. Диффузионное насыщение сталей и сплавов элементами-металлоидами с меньшим размером атома, чем металл-основа (железо, титан и др.): углеродом, азотом, бором. При этом слой, обогащенный данными элементами, располагается вглубь от поверхности («внутри сплава») (рис. 2.32).
Рис. 2.32. Химико-термической обработка сплавов металлоидами
|
|
Рис. 2.33. Химико - термической обработка сплавов металлами
2. Диффузионное насыщение сталей и сплавов металлами: алитирование (Al), хромирование (Cr), цинкование (Zn) и другими элементами при этом слой, обогащенный данными элементами, располагается на поверхности, образуя покрытие, и частично проникает внутрь металла (рис.2.33).
ХТО с диффузионным насыщением углеродом и азотом.
Цементация – вид ХТО, при котором производится диффузионное насыщение поверхностного слоя металла (сплава) – углеродом.
Рис. 2.34. Свойства цементованной стальной детали, обеспечивающие сопротивление различным видам нагрузок
Цель обработки является повышение твердость, износостойкости (при хорошем сопротивлении ударным нагрузкам), сопротивления циклическим нагрузкам, циклическим контактным нагрузкам. При этом сохраняется пластичная и вязкая сердцевина детали, что обеспечивает работоспособность в сложных условиях нагружения (рис. 2.34).
Процесс цементации проводят на сталях, содержащих 0,08 - 0,25 % С; это могут быть как углеродистые стали, так легированные. В результате цементации концентрация углерода в поверхностном слое возрастает до 0,8 - 1,4 % С.
|
|
Наиболее распространенные детали, к которым применяется ХТО: зубчатые колеса, пары трения, кулачки, опоры валов под посадку подшипников.
При химико-термической обработке, к параметрам, необходимым любому процесса термообработки, – температуре, времени выдержке, скорости охлаждения, добавляется еще один – среда насыщения (или активность среды насыщения).
Нагрев цементуемых деталей проводится в аустенитной области при температурах 900 - 1000ºС.
Время выдержки зависит от марки стали и от той толщины слоя, который необходимо получить для данной детали. Так например, на низкоуглеродистых сталях для получения науглероженного слоя глубиной 2 мм при температуре 900ºС требуется 16 часов, при температуре 950ºС - 10 часов.
Насыщающая средапри цементации называется карбюризатором. Карбюризатор может быть твердым, жидким, газообразным.
При этом цементация всегда протекает через газовую фазу. В насыщающей среде протекают следующие реакции:
В твердой фазе:
ВаСО3 + С → ВаО + 2СО
На поверхности детали протекает ведущая реакция:
2СО → СО2 + С
При газовой цементации используется в качестве карбюризатора – природный газ (основная часть его – метан) и реакция имеет следующий вид:
|
|
СН4 → 2Н2 + С
В ряде случаев исходную газовую среду активизируют ионизацией в тлеющем разряде. Углерод в виде ионов переносится на насыщаемую поверхность, адсорбируется на ней. Проникновение ионов углерода вглубь детали, т.е. диффузионное насыщение, происходит в аустенитной области. Скорость охлаждения после выдержки при температуре цементации – замедленная, с печью. Таким образом, после цементации сталь имеет структуру отжига. После цементации проводят закалку и низкий отпуск. Поверхность детали, которая должна сопротивляться износу и контактным нагрузкам, состоит из высокоуглеродистого мартенсита отпуска и частиц цементита. Толщина упрочнённого слоя после цементации составляет 1,5 – 2 мм (но может достигать и 6 мм).
«Двухслойная» структура всей цементованной детали – высокоуглеродистый мартенсит на поверхности и малоуглеродистый мартенсит в сердцевине, различные удельные объемы этих составляющих, обуславливает возникновение сжимающих напряжений в поверхностном слое, которые благоприятны для работы деталей в условиях циклических нагрузок.
Азотирование – процесс насыщения сплавов азотом из газовых сред.
Технология процесса азотирования (температуры, продолжительность), а также сопутствующая термическая и механическая обработки, химический состав применяемых сталей и окончательные свойства отличаются от процесса цементации. Азотирование применяется для сталей, содержащих более сильные нитридообразующие элементы, чем железо: хром, молибден, алюминий. Такими сталями являются низко- и среднеуглеродистые легированные стали марок 38ХМЮА, 20Х2Н4ВА, 30Х3ВА и др.
|
|
Азотированиепроводят в среде аммиака, который при нагреве диссоциирует в соответствии с реакцией:
2NH3 → N2 + 3H2
Нагрев проводится в α - области, при температурах 500 - 600ºС. Поскольку эти температуры находятся в интервале температур отпуска или старения (для ряда сталей), то процесс насыщения может быть совмещён с термообработкой. Длительность составляет до 24 - 60 часов (из-за пониженной по сравнению с цементацией температуры насыщения).
Азотирование является более дорогим процессом, чем цементация, из-за повышенной длительности процесса. Его применяют для ответственных деталей –коленчатых валов, гильз цилиндров, червяков, для деталей сложной формы и тонких сечений, которые не подвергаются последующему шлифованию.
Недостатки:большая длительность процесса; более низкие контактные нагрузки, чем для цементованных деталей, из-за меньшей толщины упрочнённого слоя.
Современным прогрессивным способом азотирования является ионное азотирование. Его проводят в специальных установках, в которых детали являются катодом, стенки вакуумной камеры - анодом. В разреженной атмосфере чистого азота при давлении 500 – 1300 Па и напряжении 300 - 800 В возбуждается тлеющий разряд и при этом происходит ионизация азота. Преимущества ионного азотирования состоят в экономичности, хорошей управляемости процесса, применимости не только к легированным, но и к высоколегированным (коррозионностойким сталям), высокой производительности.
Дата добавления: 2020-01-07; просмотров: 178; Мы поможем в написании вашей работы! |
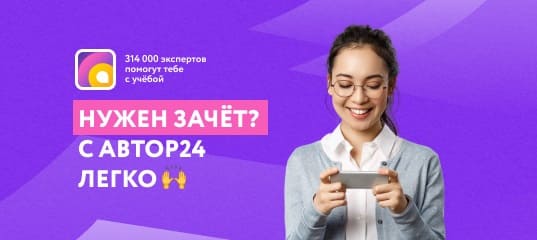
Мы поможем в написании ваших работ!