Обеспечение служебных характеристик и повышение технико-экономической эффективности применения металлических материалов
Для повышения технико-экономической эффективности применения материалов в машиностроении необходимо обеспечить определенный уровень таких свойств как прочность статическая и циклическая, износостойксость, контактная выносливость, жаропрочность, термостойкость, поверхностная стойкость (коррозионная стойкость и жаростойкость).
Статическая прочность сплавов
Прочность – важнейшее свойство конструкционных материалов. Повышение прочности приводит к снижению металлоемкости конструкций и повышению их надежности и долговечности.
Для обеспечения прочности используют различные механизмы упрочнения материалов, основанные либо на торможении движения дислокаций, либо – на введении в материал высокотвёрдых, высокомодульных составляющих. Для обеспечения этих механизмов упрочнения используют различные способы воздействия на материал.
1. Легирование. Если материал (сплав) состоит только из твёрдого раствора, то получаемое упрочнение (предел текучести) пропорционально разнице радиусов основного металла и легирующего элемента:
∆s т тв.р ~ [(ам – а л.э) /ам]
2. Легирование. Если легирование обеспечивает возможность проведения упрочняющей обработки (закалки и старения, закалки и отпуска), то получаемый прирост упрочнения зависит от количества упрочняющей фазыf, размеров её частицd и расстояния между частицамиλ:
∆σтуп ≈ f /, λ ·
|
|
3. Пластическая деформация. Получаемое упрочнение пропорционально плотности дислокаций в металле:
∆σтд ~ ρ
Упрочнение сохраняется только при температурах ниже температуры рекристаллизации.
4. Создание мелкозернистой структуры. Для этого используют следующие способы: а) повышение скорости кристаллизации; б) модифицирование расплава; в) проведение деформации с последующей рекристаллизацией; г) для сталей – проведение перекристаллизационного отжига. Получаемый прирост упрочнения обратно пропорционален размеру зерна:
∆σтз ~ d –1/2
Таким образом, предел текучести поликристаллического сплава может быть повышен несколькими способами, и в общем случае может быть получено суммарное упрочнение:
σт = σо + σттв + ∆σтуп + σтд + ∆σтз
где σо – предел текучести основного металла
Выше приведённые механизмы упрочнения являются универсальными и действуют в большинстве сплавов.
Обеспечение статической прочности сплавов композиционных и
Гетерофазных материалов.
Одними из наиболее высокопрочных материалов являются композиционные материалы, в которых использовано волокнистое армирование, т.е. упрочнение волокнами, расположенными параллельно действию основной нагрузки на материал (деталь). Армирующей составляющей в этих материалах являются вещества с высоким модулем упругости и высокой твердостью – тонкие волокна карбидов, углерода, бора, стеклянные нити, стальная проволока. Волокна различаются по размерам, расположению в матрице по отношению к приложенной нагрузке, непрерывностью или дискретностью.
|
|
Уровень прочности композитов зависит от следующих факторов: свойств волокон; объемного их содержания; диаметра волокон; схемы распределения в матрице; прочности связи с матрицей.
Гетерофазное упрочнение является одним из примеров высокомодульного упрочнения. Оно имеет место в сплавах, в которых промежуточная фаза имеет значительно более высокий модуль упругости, чем матрица. Содержание этой фазы не менее 1 %, её частицы являются массивными (т.е. частицы имеют микронные размеры), они расположены комплексами или колониями, например эвтектики и эвтектоиды.
Способ обеспечения гетерофазного упрочнения: специальное легирование сплавов, направленное на то, чтобы при кристаллизации образовывались тугоплавкие фазы микронных размеров: при выделении из жидкости по эвтектической реакции; а в твердом состоянии – по эвтектоидной реакции.
|
|
Для материалов, используемых в движущихся конструкциях (авиационная, автомобильная техника), где важна «весовая отдача» материала, кроме основных характеристик прочности, важное значение имеют удельные характеристики прочности: σв/ρ, s-1/ρ , где ρ – плотность материала.
Циклическая прочность.
При эксплуатации в условиях длительного воздействия циклических нагрузок в материале изделий развивается структурный процесс, который носит название усталость.
Усталость – процесс постепенного накопления повреждений материала (изделия) под действием многократных, знакопеременных нагрузок, производимых с высокой частотой, приводящий к изменению структуры, свойств и разрушению.
Способность материала сопротивляться усталости носит различные названия: циклическая прочность, усталостная прочность, выносливость.
Циклическая прочность определяет работоспособность большинства групп ответственных деталей машин – валов, шатунов, штоков, валов-шестерён и др.
Основной характеристикой усталостной прочности является предел выносливостиσ-1 .
Между характеристиками циклической и статической прочности существует связь, определяемая коэффициентом выносливости: kв = σ-1/ σт. В связи с этим повышением уровня статической прочности вызывает и повышение циклической прочности. Так, для сталей коэффициент kв для углеродистых легированных сталей составляет примерно 0,5 (при sв до 1200 МПа).
|
|
Факторы, влияющие на предел выносливости.
Для обеспечения выносливости необходимо управлять различными факторами при конструировании изделия, при получении материала и изготовлении изделия, а также при его эксплуатации:
– на этапе конструирования изделия – уменьшение его размеров, количества и остроты концентраторов напряжений;
– на этапе выплавки сплава – повышение качества металла: уменьшении количества пор и неметаллических включений; а также уменьшение размера зерна;
– на этапе механической обработки изделия – уменьшение шероховатости поверхности;
– на этапе термообработки изделия – повышение прочности материала и уменьшение размера зерна;
– при химико-термической обработке (цементации, азотировании, нитроцементации), при поверхностной пластической деформации – создание напряжения сжатия на поверхности;
– на этапе эксплуатации – снижение активности внешней среды, в которой работают изделия.
Обобщённое влияние различных конструктивно-технологических факторов на предел выносливости материала можно выразить зависимостью:
где: σв – временное сопротивление разрыву; HRCпов – твердость поверхности; σсжост – напряжения сжатия на поверхности; dзерна, – размер зерна в сплаве; n деф , – количество металлургических дефектов
Обобщённое влияние различных факторов на усталостную прочность изделия можно выразить зависимостью:
Усталостная прочность изделия = f (1/ dдетали, n конц, Rz),
где dдетали – размер детали; n конц – количество концентраторов напряжений;
Rz – шероховатость поверхности.
Особенно важно применять поверхностное упрочнение для повышения предела выносливости на таких деталях как валы, оси, зубчатые колёса, работающие на изгиб и кручение, так как при таких способах нагружения вследствие неравномерного распределения напряжений по сечению максимальная их величина приходится на поверхностные слои, где и начинается зарождение трещины усталости.
Контактная выносливость
При эксплуатации в условиях длительного воздействия циклических контактных нагрузок в материале изделий развивается структурный процесс, который носит название контактная усталость.
Контактная усталость -процесс постепенного повреждения поверхностных слоёв деталей (выкрашивание), работающих в условиях циклических контактных нагрузок высокой частоты.
Контактная выносливость - сопротивление материала контактной усталости.
Контактная усталость развивается при циклических контактных напряжениях в таких деталях как зубчатые передачи, подшипники и др. Подшипники и зубчатые колёса являются широко распространёнными и ответственными деталями, от надёжности и долговечности их службы зависит работоспособность узлов и механизмов.
Характеристикой контактной долговечности является предел контактной выносливости σHlimb МПа или число циклов Nц при испытании образцов с заданным контактным напряжением σконт.
Нагрузки в зоне контакта создают напряжения сжатия в поверхностном слое деталей. Под действием циклических контактных нагрузок развиваются следующие стадии процесса: микропластическая деформация, исчерпание запаса прочности, образование микротрещин а потом и трещин в приповерхностном слое, распространения трещин вглубь и скалывание частиц металла (выкрашивание). В результате такого процесса поверхности детали образуется дефект под названием «питтинг» (результат усталостного выкрашивания).
Для обеспечения контактной выносливости деталей необходимо увеличить сопротивление поверхностного слоя развитию пластической деформации, истиранию, т.е. повысить твердостьконтактирующих поверхностей.Кроме того, применяют смазочные материалы, плёночные полимерные покрытия, затрудняющие контакт металлических поверхностей.
Способы обеспечения контактной выносливости:
1. Применение высокоуглеродистых заэвтектоидных сталей, например, для подшипников качения (размером до 60 мм).
2. Применение цементации легированных сталей, например, для крупногабаритных роликовых подшипников диаметром до 2 м.
3. Применение поверхностной закалки с последующим отпуском (при σHlimb до 1000 МПа).
4. Применение химико-термической обработки для зубчатых колёс: цементации и нитроцементации (при σHlimb до 1300 МПа), азотирования (при σHlimb до 1100 МПа).
5. Применение объёмной закалки с высокий отпуском (улучшение) (при σHlimb до 770 МПа).
Дата добавления: 2020-01-07; просмотров: 149; Мы поможем в написании вашей работы! |
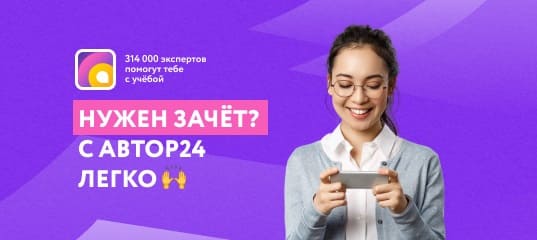
Мы поможем в написании ваших работ!