Методы диагностирования амортизаторов и подвески
В практике диагностирования амортизаторов и подвески применяют метод измерения сцепления колес с дорогой и метод измерения амплитуды.
Схема метода диагностирования по сцеплению колес с дорогой представлена на рис. 1.70.
Рис. 1.70. Схема метода диагностирования амортизаторов по сцеплению колес с дорогой:
1 – колесо автомобиля; 2 – пружина; 3 – кузов; 4 – амортизатор; 5 – ось автомобиля; 6 – измерительная площадка
При этом методе база колебаний в нижней части жесткая и подпружинена только в верхней части. Технология проверки амортизаторов и подвески при использовании метода сцепления колес с дорогой заключается в следующем. Сначала проверяемое колесо автомобиля устанавливается точно посередине измерительной площадки амортизаторного стенда. В состоянии покоя измеряется статический вес колеса. Затем включается привод перемещения одной из площадок в вертикальном направлении (сначала левой, а потом правой). С помощью электродвигателя осуществляется периодическое возбуждение колебаний с частотой 25 Гц; при этом измерительная площадка перемещается как жесткое звено. Полученный в результате динамический вес колеса (вес на плате при частоте колебаний 25 Гц) сравнивается со статическим весом путем деления первого на второй.
Пример. Пусть статический вес колеса при частоте 0 Гц равен 500 кг, а динамический вес при частоте 25 Гц равен 250 кг. Тогда коэффициент падения веса колеса (в процентах), измеренный по методу сцепления колес с дорогой составит (250/500)∙100=50 %. Полученные значения коэффициента падения веса левого и правого колеса и их разность (в процентах) выводятся на экран монитора.
|
|
Состояние амортизаторов характеризуется следующими соотношениями: хорошее – не менее 70% (для спортивной подвески – не менее 90%); слабое – от 40 до 70 (от 70 до 90); дефектное – менее 40% (от 40 до 70).
Результаты оценки состояния амортизаторов не должны отличаться более чем на 25 % друг от друга по бортам транспортного средства. Обработка результатов базируется на эмпирических значениях, которые были получены с помощью серийных исследований автомобилей различных производителей. При этом предполагается, что у среднестатистического автомобиля жесткость амортизаторов, как правило, увеличивается с увеличением нагрузки на ось.
Рассмотренный метод имею следующие недостатки: данные измерений зависят от давления воздуха в шине диагностируемого автомобиля; при диагностировании обязательно расположение колеса точно посередине площадки амортизаторного стенда; приложение постоянных внешних сил, боковых сил (напряжение) оказывает влияние на боковое перемещение автомобиля, что сказывается на результатах тестирования.
|
|
Диагностирование по методу измерения амплитуды (рис. 1.71), применяемое на оборудовании фирм «Боге» и МАХА, более прогрессивное. Площадка стенда подвешена на гибком торсионе, база колебаний подпружинена как в верхней, так и в нижней части, что позволяет измерять не только вес, но и амплитуду колебаний на рабочих частотах.
Рис. 1.71. Схема метода диагностирования амортизаторов по амплитудным колебаниям (обозначения те же, что на рис. 1.70)
Технология проверки амортизаторов и подвески по методу измерения амплитуды заключается в следующем. Колесо автомобиля, установленное на площадку стенда, колеблется с частотой 16 Гц и амплитудой 7,5...9,0 мм. После включения электродвигателя стенда колесо автомобиля колеблется относительно покоящихся масс автомобиля, частота колебаний увеличивается до достижения резонансной частоты (обычно 6…8 Гц).
После прохождения точки резонанса принудительное возбуждение колебаний прекращается выключением электродвигателей стенда. Частота колебаний увеличивается и пересекает точку резонанса, в которой достигается максимальный ход подвески. При этом осуществляется измерение частотной амплитуды амортизатора.
|
|
Рабочие характеристики амортизатора определяются в «дроссельном» и «клапанном» режимах. В дроссельном режиме, когда максимальная скорость поршня не более 0,3 м/с, клапаны отбоя и сжатия в амортизаторе не открываются. В клапанном режиме, когда в амортизаторе максимальная скорость поршня более 0,3 м/с, клапаны отбоя и сжатия открываются, причем тем больше, чем больше скорость поршня.
Диаграммы при испытании амортизатора на стенде записываются в дроссельном режиме при частоте 30 циклов в минуту, ходе поршня 30 мм, максимальной скорости 0,2 м/с. Причем в том случае, когда амортизатор испытывается в амортизаторной стойке, ход поршня составляет 100 мм. Диаграммы записываются в клапанном режиме при частоте 100 циклов в минуту, таком же ходе поршня, что и в дроссельном режиме, и при максимальной скорости поршня 0,5 м/с.
При испытании амортизаторов дефектом считается появление жидкости на штоке и у верхней кромки манжеты стойки или сальника амортизатора при условии, что жидкость появляется вновь после протирки места течи. Дефектом считается наличие стуков, скрипов и других шумов, за исключением звуков, которые связаны с перетеканием жидкости через клапанную систему, а также наличие избыточного количества жидкости – «подпор», эмульсирование жидкости, недостаточное количество жидкости («провал»).
|
|
Дефектом считается и отклонение формы кривых диаграмм от эталонной. На рис. 1.72 показана эталонная форма диаграммы и форма диаграммы амортизатора с дефектами.
Рис. 1.72. Диаграммы работы исправного и дефектного амортизаторов:
I, II, III – участки, свидетельствующие о наличии соответственно эмульсирования жидкости, «провала» и «подпора»; Ро, Рс – силы сопротивления при ходе отбоя и ходе сжатия
Амплитуда колебаний (рис. 1.73) определяется по движению следующей за колесом проверочной площадки и регистрируется. При этом измеряется максимальное отклонение (максимальная амплитуда колебаний). Оно пересчитывается и показывается на экране монитора раздельно для левого и правого амортизаторов. По графику колебаний на экране монитора можно оценить эффективность амортизаторов, даже не зная параметров, заложенных изготовителем: чем меньше амплитуда резонанса на графике, тем лучше работает амортизатор.
Рис. 1.73. Амплитуда колебаний амортизатора
Пример документирования результатов проверки амортизаторов передней и задней осей автотранспортного средства на стенде показан на рис. 1.74
Рис. 1.74. Данные контроля амортизаторов
Измеренные для каждого колеса на резонансной частоте значения амплитуды колебаний выводятся в миллиметрах. Кроме того, для обоих амортизаторов одной оси выводятся разности хода колес. Благодаря этому можно судить о взаимном влиянии обоих амортизаторов одной оси.
Состояние амортизаторов по амплитудному показателю определяется следующим образом: хорошее – 11…85 мм (для задней оси массой до 400 кг – 11…75 мм); плохое – менее 11; изношенное – более 85 мм (для задней оси массой до 400 кг – более 75 мм). Разница хода колес не должна превышать 15 мм.
На стендах для проверки амортизаторов, например фирмы МАХА, можно производить поиск шумов подвески. В этом режиме оператор может сам задавать частоту вращения ротора (от 0 до 50 Гц). Без режима поиска шумов источник шума необходимо искать за доли секунды, пока затухают колебания подвески.
ТО стендов для проверки амортизаторов и подвески включает проверку крепления стенда к основанию, а также всех резьбовых соединений через каждые 200 ч работы и не реже одного раза в год. Через каждые 200 ч работы смазывают рычаги стенда густой смазкой.
1.7.4. Стенды экспресс-диагностики положения колес
Стенд для экспресс-диагностики положения колес транспортного средства представляет собой площадку, имеющую возможность поперечного перемещения. Если колесо автомобиля по своим углам установки расположено не оптимально, при движении в пятне его контакта с дорогой возникает поперечная сила, которая сместит площадку. Этот сдвиг определяется в метрах на километр (рис. 1.75). Смещение площадки указывает на общее состояние ходовой части и рулевого управления.
Рис. 1.75. Принцип определения положения колес
На диагностических станциях наибольшее распространение имеют стенды MINC фирмы МАХА. Стенд имеет рамную конструкцию, предназначенную для проезда колеса через его подвижную контрольную платформу в заданном направлении и измерения ее горизонтального перемещения в направлении, перпендикулярном к направлению проезда (рис. 1.76).
Рис. 1.76. Конструкция стенда для экспресс-диагностики положения колес:
а – вид сбоку; б – вид сверху; 1 – короб; 2, 3, 6, 7, 8 – салазки; 4 – измерительная плита; 5 – измерительный датчик; 9 – устройство сдвига; 10 – направляющие
Основные элементы конструкции стенда – плита, по которой проезжает колесо проверяемой оси автомобиля, салазки, служащие для перемещения плиты, устройство сдвига. Устройство сдвига связано с измерительной плитой и может передвигаться по направляющим. С устройством сдвига связан измерительный датчик, представляющий собой потенциометр, регистрирующий величину сдвига и направление перемещения плиты при проезде по ней автомобиля.
Нахождение автомобиля на площадке определяется датчиком присутствия, находящимся под подвижной площадкой (рис. 1.77).
Рис. 1.77. Датчик присутствия:
1 – датчик; 2 – место установки датчика
При проезде колеса через измерительную плиту, установленную на уровне пола, она отжимается вправо или влево (в зависимости от движения колеса). Это отклонение отображается на экране (рис. 1.78). Результаты измерений записываются автоматически последовательно (сначала для переднего моста, затем для заднего) и отмечаются различными цветами. Зеленым цветом отображаются положительные результаты проверки, увод колеса при этом находится в пределах 0…7 м/км. Оранжевым цветом отображается удовлетворительное состояние в пределах 7…14 м/км, красным – неудовлетворительное, если увод составляет больше 14 м/км или результаты увода отрицательные.
Рис. 1.78. Данные контроля схождения колес автомобиля
Неудовлетворительные результаты проверки свидетельствуют о неисправностях шин, колес, подвески, рулевого управления или указывают на необходимость регулировки углов установки управляемых колес. Для более точного определения углов установки управляемых колес необходимо применять специальные стенды на отдельном посту.
Управление стендом бокового увода MINC производится через пульт управления «Евросистема». Все результаты измерений непрерывно передаются на пульт управления и отображаются на экране. Данные измерений заносятся в компьютер линии технического контроля с последующей передачей на монитор и распечаткой на принтере.
На линиях инструментального контроля стенд экспресс-диагностики положения колес может быть смонтирован на фундаменте или установлен на диагностической линии напольного типа (рис. 1.79), причем его целесообразно располагать первым, потому что при контроле рассматриваемого параметра не требуется сухое состояние протектора.
Рис. 1.79. Пример монтажа стенда бокового увода Minc на напольной линии:
а – вид сбоку; б – вид сверху; 1 – подъемник; 2 – тормозной стенд; 3 – тестер люфтов; 4 – въездная рампа
ТО стенда заключается в проверке, чистке и смазывании нижних частей каждые 200 ч или раз в год.
Дата добавления: 2020-01-07; просмотров: 561; Мы поможем в написании вашей работы! |
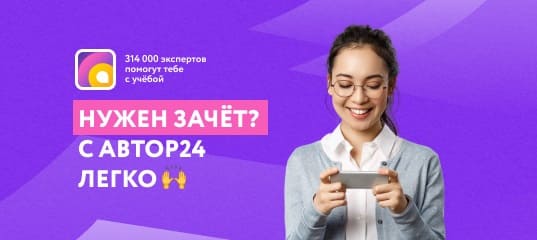
Мы поможем в написании ваших работ!