Средства технического диагностирования и их классификация
Средства технического диагности рования(СТД) представляют собой технические устройства, предназначенные для измерения текущих значений диагностических параметров.
В общем случае любое СТД состоит из следующих элементов (блоков):
источник воздействия (при тестовом методе), датчик, каналы связи;
усилитель и преобразователь сигнала;
блоки измерения, расшифровки и регистрации (записи) диагностического параметра;
блок накопления и обработки информации.
В современной аппаратуре блоки измерения, расшифровки, регистрации, накопления и обработки информации создаются на базе видео- и микропроцессорной техники, совместимой с персональным компьютером (ПК).
В зависимости от выполняемых задач, области применения и ряда других признаков методы и средства технической диагностики можно классифицировать по разным параметрам.
По назначению СТД подразделяются на штатныеи специальные.
Штатные СТД (термометры, манометры, расходомеры, амперметры, вольтметры и др.) предназначены в основном для функционального диагностирования, т.е. для обычного текущего контроля.
К специальным относятся СТД, которые периодически используются для уточнения работ по ремонту, проверки качества ремонта или определения причин выхода из строя.
По области применения СТД подразделяются на универсальныеисперциализированные.
Универсальные СТД предназначены для измерения определенных физических величин и параметров на любых объектах без учета их особенностей. К таким приборам относятся все известные средства для измерения электрических параметров и магнитного поля, температуры, давления и т.д. В эту группу входят и приборы для измерения и спектрального анализа вибрации и шума, средства дефектации и т.п.
|
|
Специализированные СТД создаются для диагностирования конкретных элементов автомобиля. Например, имеются специальные приборы для контроля состояния только системы питания или герметичности цилиндров двигателя внутреннего сгорания (ДВС).
По мобильности СТД подразделяются на стационарные, встроенные и переносные (передвижные).
Специальные СТД, как правило, являются переносными или стационарными, а штатные могут быть как переносными, так и встроенными.
Диагностические параметры и нормативы
Чтобы определить, в каком состоянии находится автомобиль или его элемент, необходимо знать параметры его технического состояния, заданные нормативно-технической документацией завода-изготовителя.
Параметрами технического состояния(структурными парамет рами)называются физические величины (миллиметр, градус и т.п.), определяющие связь и взаимодействие элементов автомобиля и его функционирование в целом. Например, параметрами технического состояния сопряжения поршень – цилиндр двигателя могут быть размеры сопряженных деталей поршней и цилиндров, которые определяют зазор между ними, овальность и т.п. В процессе эксплуатации параметры технического состояния изменяются от номинального до предельного значения под влиянием различных конструктивно-технологических и эксплуатационных факторов. Предельные значения структурных параметров обусловлены вероятностью отказов и неисправностей автомобиля и являются в основном значениями технико-экономического характера.
|
|
Возможность непосредственного измерения в процессе эксплуатации структурных параметров (износов, зазоров) сопряжений механизмов автомобиля без их разборки весьма ограничена. Поэтому при диагностировании пользуются косвенными признаками, отражающими техническое состояние автомобиля. Эти признаки называются диагностическими параметрами и представляют собой пригодные для измерения физические величины, связанные с параметрами технического состояния автомобиля и несущие информацию о его состоянии. Диагностические параметры– это качественная мера проявления технического состояния автомобиля и его элементов по косвенным признакам, определяемая количественными значениями.
|
|
Диагностическими параметрами могут быть параметры рабочих процессов (мощность, тормозной путь, расход топлива и др.), сопутствующих процессов (вибрация, шум и т.п.) и геометрические величины (зазор, люфт, свободный ход, биение и др.).
Для обеспечения надлежащей достоверности и экономичности диагностирования диагностические параметры должны обладать чувствительностью, однозначностью,стабильностью, информативностью.
Под чувствительностью К r диагностического параметра П понимают отношение приращения d П параметра к соответствующему изменению du структурного параметра:
К r = d П / d u .
Чем больше значение этой величины, тем чувствительнее диагностический параметр к изменению структурного параметра (рис. 1.2).
Рис. 1.2. Схема характеристик диагностических параметров:
1, 2, 3 – соответственно стабильность, чувствительность и однозначность диагностического параметра; – математическое ожидание, характеризующее стабильность параметра П1; ∆П/∆ u – чувствительность параметра П2; А – экстремум, характеризующий неоднозначность параметра П3в диапазоне uн- uп; uн, uп– соответственно начальное и предельное значения структурного параметра
|
|
Однозначность диагностического параметра определяется монотонно возвращающей или убывающей зависимостью его от структурного параметра в диапазоне от начального uндо предельного uпизменения структурного параметра.
Стабильностьдиагностического параметраопределяется дисперсией его значения при многократных измерениях в неизменных условиях на объектах, имеющих одно и то же значение структурного параметра. Нестабильность диагностического параметра снижает достоверность оценки технического состояния механизма, что в некоторых случаях заставляет отказаться от удобных методов диагностирования. Так, например, именно это является одной из основных причин, по которой площадочные тормозные стенды несмотря на некоторые их преимущества не применяются при государственном техническом осмотре. Это связано с тем, что такие стенды, как и стенды с беговыми барабанами, имеют нестабильность показаний. Для определения истинного состояния тормозной системы необходима повторная проверка, что не является проблемой при использовании стенда с беговыми барабанами.
Информативностьдиагностического параметра является главным критерием, положенным в основу определения возможности применения параметра для целей диагностирования. Она характеризует достоверность диагноза, получаемого в результате измерения значений параметра (рис.1.3).
Рис. 1.3. Схема сравнительной информативности диагностических параметров:
а – информативного (П); б – малоинформативного (П′); в – неинформативного (П″); f1, f2 – функции распределения параметров соответственно исправных и неисправных объектов
Диагностические параметры механизма, как и структурные, являются переменными случайными величинами и имеют соответствующие номинальные и предельные значения. С увеличением пробега автомобиля диагностические параметры могут либо увеличиваться (вибрации и др.), либо уменьшаться (давление масла и т.д.). Существующая связь между диагностическими и структурными параметрами позволяет без разборки автомобиля и его элементов количественно оценить их техническое состояние.
Диагностические нормативы– это количественная оценка технического состояния диагностируемой системы. К ним относятся: начальное значение диагностического параметра; его предельное значение, при достижении которого возникает вероятность появления отказа; упреждающее или допустимое значение при заданной периодичности диагностирования. Определение технического состояния системы в данный момент и прогнозирование ее работоспособности в период предстоящей наработки выполняются путем сравнения измеренного значения диагностического параметра с его предельным значением.
Процесс диагностирования
В общем случае процесс технического диагностирования включает следующие элементы (рис. 1.4): обеспечение функционирования объекта в заданных режимах или тестовое воздействие на объект; улавливание и преобразование с помощью датчиков сигналов, выражающих значения диагностических параметров, их измерение; постановка диагноза на основании логической обработки полученной информации путем сопоставления с нормативами.
Рис. 1.4. Схема процесса диагностирования:
S – диагностический параметр; S ′ – диагностический параметр в трансформированном виде; Si – текущее значение диагностического параметра; Sном – номинальное значение; Sп.д – предельнодопустимое значение диагностического параметра; Sп – предельное значение
Диагностирование осуществляется либо в процессе работы самого транспортного средства, его агрегатов и систем в заданных нагрузочных, скоростных и тепловых режимах (функциональное диагностирование), либо при использовании внешних приводных устройств (роликовых стендов, подкатных и переносных приспособлений), с помощью которых на автомобиль оказываются тестовые воздействия (тестовое диагностирование). Эти воздействия должны обеспечивать получение максимальной информации о техническом состоянии объекта при оптимальных трудовых и материальных затратах.
Как показано на рис.1.4, от объекта диагностирования, выведенного в заданный режим, с помощью специального датчика (механического, гидравлического, пьезоэлектрического, индукционного и др.), воспринимается сигнал, отражающий диагностический параметр S, характеризующий, в свою очередь, значение структурного параметра.
Различают легкосъемные и встро енные датчики. Первые устанавливаются на объект на время диагностирования (магнитные, навесные, на зажимах и т.п.), а вторые являются элементами конструкции автомобиля. Встроенные датчики могут быть подключены к контрольным приборам для постоянного наблюдения или к централизованным штепсельным разъемам.
От датчика сигнал в трансформированном виде S ′ поступает в измерительное устройство, затем значение диагностического параметра Si выдается устройством отображения данных (стрелочный прибор, цифровая индикация, графопостроитель и т.п.).
В автоматизированных СТД с помощью специального логического устройства, функционирующего на базе микропроцессора, выполняется автоматическая постановка диагноза, а также выдаются рекомендации в нормативной форме о возможности дальнейшей эксплуатации или необходимости проведения ремонтно-регулировочных операций и замены неисправных элементов. В неавтоматизиро ванных СТД постановка диагноза осуществляется оператором.
В зависимости от задач диагностирования и сложности объекта диагнозы могут различаться по глубине. Для оценки работоспособности агрегата, системы, автомобиля в целом используются выходные параметры, на основании которых ставится альтернативный диагноз («годен» – «не годен»). Для определения потребности в ремонтно-регулировочной операции требуется более глубокий диагноз, основанный на локализации конкретной неисправности. Постановка диагноза в случае, когда приходится пользоваться одним диагностическим параметром, не вызывает особых методических трудностей. Она сводится к сравнению измеренного значения диагностического параметра с нормативным.
Если производится поиск неисправности сложного механизма, системы и используется несколько диагностических параметров, постановка диагноза существенно сложнее. В этом случае необходимо на основании данных о надежности объекта выявить связи между его наиболее вероятными неисправностями и используемыми диагностическими параметрами. Для этой цели в практике диагностирования транспортных средств наиболее часто применяют диагностические матрицы.
Дата добавления: 2020-01-07; просмотров: 550; Мы поможем в написании вашей работы! |
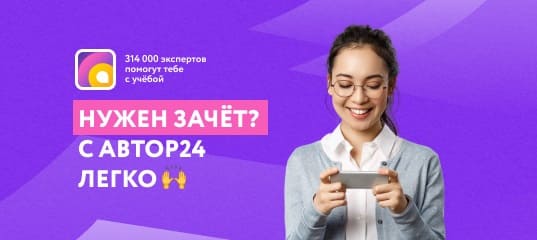
Мы поможем в написании ваших работ!