Высокоскоростной железнодорожный транспорт
скоростью движения vH= v2. При этом номинальная мощность двигателя равна
Р v
р = =0,278F -У-, [14.2]
н П3 КНП3
где т]3 — КПД зубчатой передачи (примерно равный 0,975); 0,278 — коэффициент связи между силой тяги (кН), скоростью (км/ч) и мощностью (кВт).
Для локомотивов пассажирских поездов расчетную мощность выбирают, исходя из обеспечения среднетехнической скорости на участке определенной длины. Для пригородных электропоездов (распределенная тяга) эта мощность составляет 200— 250 кВт, для междугородных скоростных электропоездов — 650 кВт, а для скоростных и высокоскоростных пассажирских локомотивов (сосредоточенная тяга) достигает 1200 кВт на одну движущую колесную пару.
Максимальная частота вращения вала тягового двигателя, как правило, не превышает 3000 об/мин из-за ограничения по работоспособности роликовых подшипников средней и тяжелой серий с консистентной смазкой. Для высокоскоростного подвижного состава максимальная частота вращения вала современных асинхронных двигателей достигает 4100 об/мин, что обусловливает необходимость применения подшипников новой серии.
Передача тягового момента на колесную пару сопровождается возникновением статической (полезной) составляющей силы. В процессе движения локомотива кроме статической составляющей появляется динамическая (вредная) составляющая, обусловленная недостатками способа регулирования мощности двигателя, кинематическим несовершенством схемы или конструкции тяговой передачи и рядом других причин. Динамическая составляющая нагрузки существенно возрастает с увеличением скорости. К вредным нужно отнести также динамические нагрузки, вызываемые переменными ускорениями корпуса тягового двигателя и редуктора. Основной причиной появления высоких динамических усилий, действующих на тяговый двигатель и редуктор, является взаимодействие ходовых частей локомотива и верхнего строения пути.
|
|
По критериям защищенности тягового двигателя от действия динамических сил выделяют системы привода с опорой тягового двигателя на ось колесной пары (опорно-осевой) и с опорой на подрессоренную часть тележки или кузова (опорно-рамный). По степени защищенности редуктора от воздействия динамических сил также различают редуктор, опирающийся на ось колесной пары (опорно-осевой) или установленный на раму тележки (опорно-рамный). По степени защищенности кинематической цепи от динамических моментов передачи выделяют три существенных признака: наличие опорно-осевых редукторов; горизонтальная или негоризонтальная модификация реализации тяги; степень приближения к единице передаточного числа от зубчатого колеса к шестерне.
|
|
По условию относительных угловых перемещений шарнирных элементов муфт (относится только к опорно-рамным приводам) различают две группы: первая — механизмы, в которых элементы шарнирного соединения ведущего вала с промежуточным звеном и звена с ведомым валом расположены в одной плоскости; вторая — механизмы, в которых шарнирное соединение ведущего вала и промежуточного звена расположено в одной плоскости, а промежуточного звена и ведомого вала — в другой.
По степени динамического совершенства все тяговые приводы принято подразделять на три класса: первый — с опорноосевыми двигателями и редукторами; второй — с опорно-рамными двигателями и опорно-осевыми редукторами; третий — с опорно-рамными двигателями и редукторами. На скоростном и высокоскоростном подвижном составе используются тяговые приводы третьего и второго классов.
На рис. 14.2 показаны кинематические схемы, применяемые при различных компоновках тяговых приводов с опорно-рамным двигателем и опорно-осевым (класс II) или опорно-рамным (класс 111) редуктором.
|
|
-£ |
IP |
Рис. 14.2. Кинематические схемы передачи при различных компоновках тяговых приводов: а — с опорно-рамным двигателем и опорно-осевым редуктором; б — с опорно-рамным двигателем и редуктором; 1 — схема первой группы с шарнирной муфтой поперечной компенсации; 2, 3 — схемы второй группы с шарнирной муфтой и коротким промежуточным валом; 4, 5 — схемы второй группы с шарнирной муфтой, длинным промежуточным валом; 6 — схема второй группы с шарнирной муфтой в полой оси вала тягового двигателя и с полым валом на оси колесной пары; 7, 8 — схемы второй группы с шарнирной муфтой с удлиненным полым валом на оси колесной пары; 9, 10 — схемы второй группы с шарнирной муфтой и длинным полым валом на оси колесной пары
В качестве примеров рассмотрим две кинематические схемы. Одна из них используется на многих высокоскоростных поездах японских Синкансэн, на германских поездах ICE3 (платформа «Velaro»), а вторая — на электровозах французских высокоскоростных поездов TGV, в том числе и тех, которыми были установлены мировые рекорды скорости: на опытных поездах TGV А №325 и V150.
Обе приведенные для примера схемы относятся к тяговой передаче второго класса с опорно-рамным расположением двигателя и опорно-осевым редуктором (в некоторых случаях редуктор дополнительно опирается через эластичные резиновые амортизаторы на раму тележки). Такая техническая идея тяговой передачи (схематически представлена на рис. 14.3), хорошо себя зарекомендовала в различных вариантах конст-
|
|
Рис. 14.3. Схематическое изображение тяговой передачи моторной тележки высокоскоростного электропоезда с тяговым двигателем, установленном на раме тележки, и подвижной передачей к редуктору с помощью зубчатой муфты: а — общая схема: б — вид на тележку сбоку (вдоль пути); в — вид зубчатой муфты японского высокоскоростного поезда серии 700; г — колеса зубчатой муфты поезда серии 700: 1 — колесная пара; 2 — зубчатая муфта; 3 — тяговый двигатель; 4 — шестерня редуктора; 5 — большое зубчатое колесо редуктора; б — редуктор; 7 — зубчатое колесо с внутренним венцом; 8 — шестерня с наружным венцом; 9 — рама тележки
руктивного исполнения. На японском высокоскоростном электроподвижном составе со времен первых японских высокоскоростных поездов серии 0 (1964 г.), включая японские поезда последнего поколения, например, серии N700, а также на германских высокоскоростных поездах платформы «Velaro» (к ним относятся и поезда «Сапсан», эксплуатируемые в России) подвижная кинематическая связь вала тягового электродвигателя и входного вала редуктора обеспечивается с помощью зубчатой муфты (она позволяет элементам вала как отклоняться от продольной оси, так и перемещаться вдоль оси). На рис. 14.4 показана тяговая передача моторного вагона высокоскоростного поезда «Сапсан».
В качестве второго примера рассмотрим кинематическую передачу тягового привода высокоскоростных поездов TGV компании Alstom, Франция. Первый поезд этого типа создавался в конце 1960-х — начале 1970-х годов. Для оценки работоспособности отдельных узлов и агрегатов были построены опытный газотурбинный высокоскоростной поезд с электрической передачей TGV 001 (1969 г.) и опытный высокоскоростной электровагон «Zebulon» (Z 7001) (1974 г.). На поезде TGV 001 использовался тяговый привод третьего класса с муфтой типа Жакмен. По результатам испытаний поезда сделали вывод о том, что для повышения критической (по вилянию) скорости движения (более 300 км/ч) необходимо снизить массу тележки. В связи с этим тяговый двигатель (массой около 1400 кг) и редуктор первой ступени перенесли на раму кузова локомотива (рис. 13.42 и 14.5], на оси колесной пары разместили редуктор второй ступени с опорно-осевым подвешиванием. В целом конструкция привода стала сложнее и, с инженерной точки зрения была шагом назад, так как являлась тяговой передачей второго класса, тем не менее поставленная задача была решена. Эта конструкция тяговой передачи с сохранением основных технических решений несколько раз модернизировалась и используется до настоящего времени на локомотивах поездов TGV (рис. 13.42; 14.5].
Рис. 14.4. Схематическое изображение тяговой передачи высокоскоростного поезда «Сапсан»: 1 — колесная пара; 2 — тяговый двигатель; 3 — ротор двигателя; 4 — статор двигателя; 5 — зубчатая муфта; 6 — элемент узла подвески редуктора; 7 — шестерня; 8 — большое зубчатое колесо; 9 — корпус редуктора; 10 — ось колесной пары [изображена упрощенно без шеек). Германия, 2009 г. |
16 15
17
I
18
Рис. 14.5 (рекомендуется рассматривать совместно с рис. 13.42). Тяговая передача электровозов поездов TGV: а — вид сверху на тележку электровоза; б — схематическое изображение устройства передачи и компонентов ШРУС; в — схематическое изображение элементов шарнира Гука и разрез шлицевого вала со сферическими головками: 1 — рама тележки; 2 — колесная пара; 3 — подшипники опоры редуктора второй ступени; 4 —редуктор второй ступени; 5 — ось колесной пары; 6 — редуктор первой ступени; 7 — тяговый электродвигатель; 8 — реактивная тяга; 9 — кожух редуктора второй ступени; 10 — шлицевой вал; 11 — шестерня тягового двигателя; 12 — промежуточная шестерня редуктора первой ступени; 13 — зубчатое колесо редуктора первой ступени; 14 — сферические головки скользящей муфты; 15 — датчик частоты вращения выходного вала редуктора первой ступени; 16 — датчик частоты вращения колесной пары; 17 —устройство сравнения частоты вращения;
18 — аварийный сигнал неисправности ШРУС; 19 — вилки шарниров 1ука; 20 — цилиндрические пазы; 21 — игольчатый подшипник; 22 — уплотнение; 23 — ведомый вал ШРУС со сферическими головками; 24 — направление продольного перемещения сферических головок
В передаче подвижная кинематическая связь между двумя ступенями осуществляется с помощью шарнира равных угловых скоростей (ШРУС). Его элементы — шарниры Гука и скользящая муфта с узлом в виде трех сферических (шарообразных) головок[23] (вращающихся на игольчатых подшипниках), входящих внутрь трех цилиндрических пазов шлицевого вала. В отличие от обычных шлицевых валов в этой конструкции при осевом перемещении реализуется трение качения. Сферические головки имеют возможность двигаться в осевом направлении по цилиндрическим пазам на расстояние ±120 мм, а шарниры Гука позволяют отклоняться элементам вала от продольной оси. В результате колесная пара электровоза с редуктором на оси может перемещаться относительно тягового двигателя. Датчики скорости постоянно передают в устройство сравнения частоты вращения на входе и выходе ШРУС. Их несоответствие говорит о неисправности, и аварийный сигнал поступает в компьютер управления поездом.
Конструкция элементов кинематической цепи передачи существенно влияет на габариты привода, пространство, отводимое для размещения тягового электродвигателя на тележке, что, в свою очередь, определяет требования к тяговым двигателям по их удельной мощности.
Абсолютные значения отдельных размеров для приводов разных типов могут различаться. В схемах с большей длиной промежуточного вала соответственно меньше углы поворота шарниров, а, следовательно, они (по четвертому критерию) являются более совершенными. Сочетание большого расхождения центров муфт (так называемая «расцентровка») с малой длиной промежуточных элементов приводит к неудовлетворительным результатам. Большие расцентровки муфт свойственны приводам с опорно-рамными двигателями и опорноосевыми редукторами с горизонтальными реактивными тягами.
По типу тягового электропривода подвижной состав можно разделить на четыре поколения (рис. 14.6). К первому поколению относятся локомотивы и моторвагонные подвижные единицы, разработанные до 1970 г. Второе поколение — подвижной состав, построенный после 1970 г., имеющий коллекторные двигатели и полупроводниковые преобразователи. Третье и четвертое поколения подвижного состава представлены новыми разработками, осуществленными в основном после 1985 г., с бесколлекторными тяговыми двигателями, преимущественно асинхронными двигателями трехфазного тока с короткозамкнутым ротором. В тяговых преобразователях подвижного состава третьего поколения используют однооперационные тиристоры, как правило, с принудительной конденсаторной коммутацией.
К четвертому поколению высокоскоростного подвижного состава относятся разработки, осуществленные в конце XX—начале XXI столетия, в том числе, высокоскоростные поезда: германский многосистемный электропоезд ICE3 и его модификация для железных дорог России поезд VelaroRus («Сапсан»), японские поезда серии 500, 700, Е5, Е6, французский поезд AGV, испанский поезд «Avril», китайский CHR380 и др. Преобразователи этих образцов подвижного состава разработаны на базе мощных полупроводниковых приборов новых типов: 1GCT— тиристоров и IGBT—транзисторов[24], коммутируемых по управляющему электроду с заданием оптимальных алгоритмов с многократным переключением за период изменения питающего напряжения от цифровых блоков управления, выполненных на логических программируемых контроллерах.
Рис. 14.6. Классификация электроподвижного состава по типу тягового электропривода: 1 — реостатный контроллер; 2 — коллекторный тяговый двигатель; 3 — тяговый трансформатор с переключаемой обмоткой; 4 — контроллер переключения числа витков трансформатора и диодный выпрямитель; 5 — сглаживающий реактор; 6 — дизель или газовая турбина; 7 — генератор постоянного тока независимого возбуждения; 8 — сетевой LC-фильтр (возможно активный); 9 — импульсный преобразователь постоянного тока; 10 — тяговый трансформатор; 11 —управляемый выпрямитель; 12 — синхронный генератор; 13 — диодный неуправляемый выпрямитель; 14 — автономный инвертор тока (АИТ); 15 — тяговый асинхронный двигатель; 16 —управляемый выпрямитель или четырехквадрантный преобразователь (4qS); 17 — звено постоянного тока с LC-фильтром (для АИН); 18 — автономный инвертор напряжения (АИН); 19 — звено постоянного тока с конденсаторным фильтром; 20 —управляемый выпрямитель; 21 — АИТ; 22 — тяговый синхронный двигатель; 23 — АИН с ШИМ (широтно-импульсной модуляцией) на запираемых тиристорах или IGBT-транзис- торах, либо на IGCT-mupucmopax; 24 — выпрямитель (4qS) на GTO-mupucmopax, IGBT-транзисторах или IGCT-mupucmopax; 25 — неуправляемый выпрямитель; 26 — звено постоянного тока
Основные данные электротяговых приводов, используемых в скоростном и высокоскоростном подвижном составе, приведены в Приложении 4.
14.2. Требования
к электрическому приводу высокоскоростных поездов
Развитие электрической тяги сопровождалось повышением мощности локомотивов за счет увеличения числа движущих осей и единичной мощности тяговых двигателей. При конструкционной скорости 300—500 км/ч требуется примерно 14 кВт мощности тягового электропривода на одну тонну массы поезда. Такие показатели по удельной мощности электрического тягового привода трудно достижимы на основе коллекторных двигателей постоянного тока.
Практическое применение в электрической тяге двигателей переменного тока началось в Германии, Швеции и некоторых других странах. Первоначально были применены однофазные коллекторные двигатели пониженной частоты 16 2/3 и 25 Гц. Принцип их работы аналогичен работе машин постоянного тока, но процессы коммутации в них тем сложнее, чем выше частота питающего тока. При стандартной частоте 50 Гц двигатели однофазного тока имеют низкие тяговые свойства и энергетические показатели.
Попытки применения на электроподвиж- ном составе простейших по конструкции трехфазных асинхронных двигателей были предприняты в Германии, Италии и Швейцарии еще в конце XIX в. Для питания двигателей использовалась специальная контактная сеть трехфазного тока. Из-за сложности и недостаточной надежности такой конструкции и неудовлетворительных регулировочных свойств трехфазная система тягового электропривода не нашла широкого применения.
Для обеспечения допустимой нагрузки от одной оси высокоскоростного поезда на рельсы не более 180 кН и возможности снизить эту нагрузку до 100 кН и ниже удельная масса тягового двигателя не должна превышать 1,5—2,0 кг/кВт. Удельный объем тягового двигателя при размещении в стесненном пространстве экипажной части электроподвижного состава должен быть ограничен и не превышать 0,5—0,8 дм3/кВт. Максимальная допустимая частота вращения вала двигателя не должна быть ниже 3000 об/мин. Тяговый двигатель должен иметь механически прочную и защищенную от внешних воздействий конструкцию. Электрические потери в тяговом двигателе должны быть минимизированы. Отвод теплоты должен надежно обеспечиваться системой принудительного воздушного или, возможно, жидкостного охлаждения с приемлемыми для подвижной единицы параметрами.
В 20-е годы XX века исследования отечественных ученых и инженеров М.П. Костенко, А.Е. Алексеева и Б.Н. Тихменева показали, что проблема увеличения мощности электроподвижного состава и скорости его движения при одновременном повышении надежности может быть решена на основе перехода от коллекторных тяговых двигателей постоянного тока на бесколлектор- ные тяговые двигатели трехфазного тока — асинхронные и синхронные, питание которых должно осуществляться от специальных преобразователей числа фаз и частоты переменного тока.
Замена тяговых двигателей постоянного тока синхронными и асинхронными машинами с плавным регулированием частоты и напряжения трехфазного тока посредством электронных преобразователей явилось качественно новым направлением электрического локомотивостроения. Оно позволяет:
— поднять мощность на одну движущую ось до 1200 кВт и более при сохранении допустимой нагрузки на рельсы;
— увеличить коэффициент тяги (отношение силы тяги к силе давления от ко
лесной пары] на 15—20 % путем электрического спаривания движущих осей;
— обеспечить не менее чем в два раза сокращение количества отказов работы локомотивов из-за выхода из строя тяговых двигателей;
— сократить на 10—15 % эксплуатационные расходы на содержание электрооборудования электроподвижного состава;
— уменьшить динамическое воздействие на экипаж и железнодорожный путь вследствие снижения массы двигателя на 30—40 %;
— снизить долю сложных и трудоемких работ по ремонту тяговых двигателей, высвободить часть рабочей силы и поднять общий уровень культуры технического обслуживания подвижного состава;
— перейти к созданию скоростного и высокоскоростного электроподвижного состава нового поколения.
Однако практическое применение бескол- лекторных тяговых двигателей длительное время задерживалось тем, что не были созданы пригодные для коммерческого производства надежные экономичные преобразователи, способные преобразовывать полученную из контактной сети электрическую энергию в виде переменного тока (однофазного напряжением 15—25 кВ промышленной или пониженной частоты) или постоянного тока напряжением 1,5—3,0 кВ, в электроэнергию трехфазного тока регулируемой частоты, изменяемого по напряжению.
Для тягового электропривода применяются преобразователи электрической энергии различных видов: переменно-постоянного тока (выпрямители], постоянно-переменного тока (инверторы], переменно-переменного тока (преобразователи частоты и напряжения] и постоянно-постоянного тока (импульсные преобразователи). Преобразователи должны обеспечивать питание тяговых электродвигателей от контактной сети постоянного и однофазного переменного тока электроэнергией требуемых параметров по роду тока, уровню напряжения и частоте переменного тока. При питании тяговых асинхронных двигателей преобразователи должны не только преобразовывать род тока и уровень напряжения, но и обеспечивать плавное регулирование напряжения от единиц вольта до 1,5—3,0 кВ и частоты трехфазного тока от единиц до 100—150 Гц. Удельные показатели по массе (кг/кВт) и рабочему объему (дм3/кВт) не должны превышать аналогичные показатели тяговых двигателей.
14.3. Тяговые электрические двигатели
Первые опытные образцы тягового подвижного состава с бесколлекторными двигателями в СССР были созданы в 1965— 1974 гг. Результатами работ инженеров и ученых явилось создание опытной пригородной электросекции переменного тока ЭР9А; маневрового тепловоза ВМЭ24А; магистрального тепловоза ТЭ120; электровозов ВЛ80А (с асинхронными] и ВЛ80В (с синхронными] двигателями. В те же годы в Германии были построены опытные локомотивы с асинхронными двигателями: тепловоз DE4000 и электровоз переменного тока Е120. Тогда же во Франции разрабатывался электроподвижной состав с синхронными двигателями. Эти пионерные работы заложили фундамент для развития в 80-е и 90-е годы XX столетия тягового подвижного состава третьего и четвертого поколений и способствовали практическому осуществлению программы скоростного и высокоскоростного движения в Европе.
Конструкция коллекторного двигателя постоянного тока. На рис. 14.7 приведены разрезы тягового двигателя электровозов серии ЧС2Т (производства компании «Шкода», ЧССР) постоянного тока 3 кВ, которые на протяжении длительного времени были основным типом локомотивов, обслуживавших скоростные поезда на линии Ленинград—Москва Октябрьской железной дороги. Двигатели рассчитаны на номинальное напряжение 1,5 кВ, ток и мощность продолжительного режима, соот-
5 6 7 8 9 1011 |
18 |
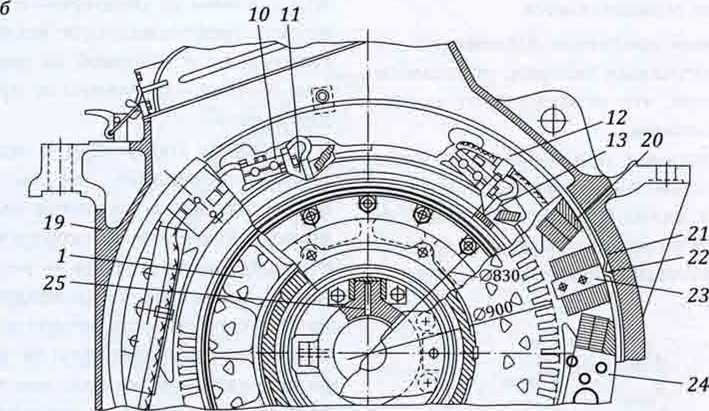
Рис. 14.7. Продольный (а) и поперечный (б) разрезы коллекторного электродвигателя (1 AL4846dT, Uc = 3 кВ; /те - 545 А, Рю = 770 кВт]: 1 — сердечник якоря; 2,7 — нажимные шайбы; 3, 14 — подшипниковые щиты; 4 — обмотка полюсов; 5, 15 — передняя и задняя втулки коробки якоря; 6 — коробка якоря; 8 — уравнитель; 9 — коробка коллектора; 10 — кронштейн щеткодержателя; 11 — щеткодержатель; 12 — траверсы щеткодержателей; 13 — коллектор; 15 — шарнирная муфта привода; 17, 18 — якорные подшипники; 19 — остов; 20 — опора катушки; 21 — шихтованная вставка; 22 — пластмассовый клин; 23 — добавочный полюс; 24 — главный полюс; 25 — деталь крепления |
С = 0,5(£>я+dQ) +А + 5+е, (14.3)
где £>я — диаметр якоря; dQ — диаметр оси колесной пары; А — расстояние от внутренней поверхности полюса до наружной поверхности корпуса двигателя по линии централи; 5 — воздушный зазор якоря; е х 5-6 мм — наибольшее горизонтальное перемещение оси колесной пары относительно рамы тележки.
Формула показывает, что централь сильно зависит от конструкции двигателя. Это
качество оценивается коэффициентом централи к =0д/С. Значение коэффициента для передачи с карданным валом составляет для электровозов 1,15—1,25, а для электропоездов 1,1—1,18.
От конструкции тягового привода зависит длина тягового двигателя. Для рассматриваемого примера
/ - I ~(А +А„+Ь + A +b + AM_), (14.4) д к '• 1 2 р Ml М M2J v J
где /к — расстояние между внутренними гранями колесных бандажей; — ширина кожуха или корпуса редуктора; Д1(А2 — соответственно зазоры между бандажом и редуктором, редуктором и двигателем; Ьм — ширина муфты привода; ДМ1,ДМ2 — зазоры между муфтой и редуктором, муфтой и двигателем, т.е. для приводов II и III классов длина двигателя дополнительно ограничивается.
Коллекторный двигатель заполняется до 25 % конструктивным зазором, отводимым для коллектора, что ограничивает активный объем машины.
С другой стороны, основные проектные размеры якорей электрических машин; диаметр Da,и длина /я зависят от вращающего момента в соответствии с требуемой тяговой характеристикой электроподвиж- ного состава:
С.Р
-А-Цом =с м
А ном'
(14.5) |
п ном |
D2! =СкР Я Я Я V ном |
(14.6) |
где Сд — постоянная Арнольда, зависящая от технического уровня выполнения машины. С учетом всех особенностей предложена (П.А. Золоторевым) зависимость: где Ся=(0,14-0,2)10’3 — постоянная технического уровня выполнения; kv — коэффициент соотношения скоростей, kv -nmax/nHOM= = Vmax/VH0M’ обь,чно k v = 1.8-2,0.
Из приведенных соотношений следует, что основные тяговые параметры: вращающий момент Л7Н0М и мощность Рном зависят от размеров Ья и /я, которые можно вписать в пространство, отводимое в экипажной части локомотива. В асинхронной машине нет коллектора, поэтому при прочих равных условиях возможно значительно увеличить единичную мощность тягового двигателя.
Дата добавления: 2019-11-16; просмотров: 1423; Мы поможем в написании вашей работы! |
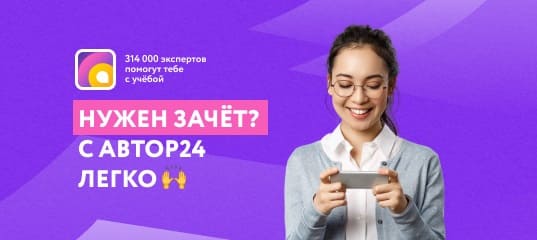
Мы поможем в написании ваших работ!