Допускаемые значения показателей ходовых качеств подвижного состава
№ п/п | Наименование показателя | Допускаемое значение | |||||||
Нормы для вагонов [23] | Нормы для электропоездов [22] | Нормы для скоростных пассажирских вагонов [4] | РД. Методы испытаний на прочность и ходовые качества [19] | Нормы МСЖД [27] | |||||
порожний | груженый | немоторный | моторный | порожний | груженый | ||||
1 | Коэффициенты вертикальной динамики: для кузова; для рамы тележки | 0,25 0,40 | 0,20 0,37 | 0,20 0,30 | 0,20 0,35 | 0,15 | 0,25 0,40 | 0,20 0,35 | — |
2 | Коэффициент запаса устойчивости от схода вагона с рельсов | 1,6 | 1,6 | 1,4 | 1,4 | 2,0 | 1.81 | 1.81 | — |
3 | Ускорения | ||||||||
3.1 | Вертикальные ускорения (в долях д'): кузова рамы тележки | 0,25 0,40 | 0,20 0,37 | — | — | 0,15 | — | — | 0,25 |
3.2 | Поперечные ускорения (в долях д): кузова; рамы тележки | 0,15 0,20 | 0,12 0,15 | — | 0,12 | — | — | 0,25 | |
4 | Рамные силы (в долях от нагрузки на ось) | 0,30 | 0,25 | 0,30 | 0,30 | — | 0,25 | 0,24 | 0,80 |
5 | Показатель плавности хода: в вертикальной плоскости; в горизонтальной плоскости | 3,25 3,25 | 3,25 3,25 | 3,25 3,25 | 3,25 3,25 | 3,25 3,25 | 3,25 3,25 | 3,25 3,25 | — |
6 | Коэффициент запаса поперечной устойчивости от опрокидывания в кривых | 1,5(1,32) | 1,5(1,32) | 1,433 | 1,433 | 1,2 | 1,4’ | 1,4х | — |
1 При доверительной вероятности схода 0,001.
2 При опрокидывании внутрь кривой.
3 Сделан пересчет к традиционному определению коэффициента устойчивости от опрокидывания.
|
|
ние осуществляется вблизи неподвижной земли. Такое движение называют движением относительного экрана.
Аэродинамические задачи, решаемые при создании высокоскоростных поездов, включают:
— определение аэродинамического сопротивления движению поезда;
— определение аэродинамических возмущений от воздействия поезда на окружающую среду (безопасность нахождения людей рядом с движущимся поездом);
— боковая устойчивость вагонов от действия ветра;
— изучение особенностей аэродинамических возмущений, связанных со стеснением воздушного потока (при встрече и обгоне поездов, при прохождении тоннелей и других инженерных сооружений вблизи пути);
— перемещение воздушных масс внутри вагона и размещение воздухозаборных и воздуховыводящих устройств.
Для определения сопротивления движению поезда рассматривают его компоненты:
— лобовое сопротивление, вызываемое приведением в движение воздуха перед поездом;
хвостовое сопротивление, вызываемое разрежением в задней части поезда;
— сопротивление трению между стенками поезда и окружающим воздухом;
— сопротивление, вызываемое выступающими частями.
Механизм возникновения лобового сопротивления следующий. При движении поезда в воздушной среде происходит сжатие набегающего потока воздуха в носовой части. В результате здесь создается область повышенного давления. Под его влиянием струи воздуха устремляются к задней части поезда. Скользя по его поверхности, они обтекают его контур. При этом струи воздуха могут отрываться от обтекаемой ими поверхности и образовывать завихрения.
|
|
Хвостовое сопротивление поезда связано с отрывом воздушного потока от поезда и образованием области пониженного давления, куда осуществляется подсос воздуха из окружающего пространства.
Величина лобового и хвостового сопротивления определяется по сходным формулам
где 5 — площадь поперечного сечения головного или хвостового вагона; v — скорость движения; р — плотность воздуха: сх — коэффициент, учитывающий влияние формы носовой или хвостовой поверхности.
Коэффициент сх характеризует аэродинамическое совершенство и определяется, в большинстве случаев, экспериментально. Коэффициент воздушного сопротивления сх высокоскоростных поездов невелик, находится в переделах 0,2—0,4. Для сравнения можно указать, что параллелепипед имеет сх - 0,9, а капля — 0,05. Однако изучению лобового аэродинамического сопротивления высокоскоростных поездов, скорее в силу традиций, перешедших из авиации и автотранспорта, уделяют большое внимание[11]. Снизить аэродинамическое лобовое и хвостовое сопротивления можно двумя способами: уменьшить площадь сечения, т.е. размеры вагона, или улучшить форму. Но эти способы зачастую противоречат требованиям рациональной планировки и снижают полезную площадь поезда. Особенно это заметно на примере японских высокоскоростных поездов — форма носовой части головных вагонов становится все более вытянутой {рис. 13.10, 13.11, 13.12). На ВСМ Японии и некоторых европейских стран с множеством тоннелей такое конструктивное решение оправдано и позволяет снизить ударные аэродинамические нагрузки на подвижной состав при входе головных вагонов в тоннели.
|
|
Для высокоскоростных поездов длиной более 200 м, эксплуатирующихся на открытых пространствах, главное — обтекаемость всего поезда и исключение выступающих частей. Исследования компании «ВотЬаг-
Рис. 13.10. Носовые оконечности головных вагонов некоторых поездов: а — серии 0 (ноль), 1964 г.
Япония; б — серии 500, 1995 г., Япония; в — опытного поезда Fastech 360S, 2005 г. Япония
|
|
Рис. 13.11. Сопоставление длины носовой оконечности головных вагонов последних моделей японских высокоскоростных поездов: а — серии N700 (2007 г.); б — серии 700 (1999 г.) |
Рис. 13.12. Профили носовых частей головных вагонов некоторых японских высокоскоростных поездов (после наименования поезда указан год его выпуска) |
dier»[12]показали, что в величину общего аэродинамического сопротивления высокоскоростного поезда головная и хвостовая части поезда вносят только 25—30 %.
Боковое сопротивление обшивки и подкузовной части составляет 40—45%, токоприемников ~11%, тележек ~12%, зазоров между вагонами ~4% от общего аэродинамического сопротивления движению. В последние годы уделяется большое внимание формам подкузовной части, улучшению обтекаемости тележек и межвагонных переходов.
Сопротивление воздуха от трения о стенки вагонов (боковое сопротивление) пропорционально наружной площади поезда и первой степени скорости, определяют по формулам
F = «1Lv, F = a2Bv,
где Gj и a2 —некоторые численные коэффициенты; L — длина поезда; В — наружная площадь поверхности поезда.
Однако эти формулы справедливы только при ламинарном обтекании. Прилегающий к поверхности какого-либо тела слой воздуха сталкивается с микронеровностями покрытия и разгоняется — образуется так называемый пограничный слой. Пока это течение находится в ламинарном состоянии, т.е. все частицы движутся в одном направлении, толщина пограничного слоя невелика и сопротивление трению пропорционально скорости в первой степени. При высоких скоростях во время встречи с крупными препятствиями траектории движения частиц воздуха становятся хаотичными и поток воздуха переходит в турбулентное состояние, пограничный слой расширяется, вместе с тем увеличивается трение, — становится пропорциональным скорости во второй степени. Таким образом, для уменьшения трения необходимо обеспечение гладкости кузова, чтобы поток оставался ламинарным. Для этого необходимо уменьшать зазоры в элементах кузова; убирать поручни и ручки, выступающие детали уплотнения на дверях; вводить так называемое «ленточное остекление», при котором несколько или весь ряд окон на одной стороне вагона перекрыт снаружи единым стеклянным покрытием без разрывов и зазоров между окнами, и т.п.
Воздействие бокового ветра в аэродинамике подвижного состава — аспект не менее важный, чем сопротивление движению, так как боковой ветер может опрокинуть поезд, создавая опрокидывающий момент: разгружая колеса поезда с одной стороны и нагружая с другой. Наиболее опасен ветер, дующий под острым углом навстречу поезду. В этом случае векторы скорости ветра и поезда складываются и опрокидывающий момент возрастает. Для защиты от бокового ветра на некоторых участках, где возможен сильный ветер, устанавливают экраны (см. рис. 17.17) и размещают автоматические измерительные приборы, которые передают в центр управления данные о силе и направлении ветра. Современные поезда типа TGV Duplex допускают боковой ветер до 115 км/ч при скорости поезда 300 км/ч.
Вопросы аэродинамики изучаются теоретически и экспериментально. Теоретические исследования основаны на интегрировании уравнений гидродинамики. Но в условиях турбулентного движения воздуха их решения зачастую оказываются далекими от практики. В последние годы создан ряд современных средств автоматизированного проектирования (например система «Catia V6»), позволяющих на стадии проектирования определять характеристики аэродинамического сопротивления и устойчивости к боковому ветру. Теоретические выводы проверяют экспериментально: осуществляют продувку моделей поездов в аэродинамических трубах (см. рис. 13.30) и проводят натурные испытания поездов. При натурных экспериментах для определения коэффициентов сопротивления выключают тяговые двигатели и по замедлению определяют коэффициент аэродинамического сопротивления. К сожалению, точность такого эксперимента невысока, так как свой вклад в сопротивление движению вносят колебания подвижного состава, трение в тяговых передачах на холостом ходу и сопротивление качению колес по рельсам. Точность методов непрерывно повышается, и новые высокоскоростные поезда приобретают все более совершенные аэродинамические формы.
В Европейском Союзе основные требования к аэродинамическим характеристикам, обеспечивающим безопасную эксплуатацию высокоскоростных поездов, изложены в Технических требованиях ЕС по технико-эксплуатационной совместимости (TSI) и охватывают ряд факторов, в частности:
— устойчивость к воздействию бокового ветра и снижению риска схода поезда с рельсов при определенных климатических условиях на специфических участках пути (например, на мостах, и насыпях);
— защита персонала, занятого в работах на линии, и пассажиров на платформах при прохождении высокоскоростных поездов;
— уменьшение воздействий перепадов давления на открытых участках и в тоннелях;
— ограничение вероятности выброса балласта при высокой скорости движения поездов;
— снижение волн микродавления в случае возникновения звукового удара у выходного портала тоннеля при входе поезда с высокой скоростью в тоннель с противоположной стороны.
13.2. Кузова вагонов и локомотивов высокоскоростного подвижного состава
Требования к прочности кузовов и обеспечению безопасности пассажиров при авариях. Безопасность зависит от конструкции всего комплекса технических средств железной дороги. Движущийся с высокой скоростью поезд является потенциальным источником опасности из-за огромной кинетической энергии. Типичными и наиболее опасными случаями нарушения нормального движения, приводящимие к авариям и катастрофам, являются столкновения и сходы с рельсов.
Обычно при проектировании подвижного состава устанавливается несколько условных режимов действия внешних нагрузок. В силу традиций для разного вида подвижного состава они носят различные названия. Однако суть их в следующем.
Режим умеренных продольных сил (<1 МН) и допускаемой скорости движения (И - V t)• Этому режиму соответствуют силы, возникающие при эксплуатации подвижного состава с допускаемой скоростью, вплоть до конструкционной. Рассматривается движение подвижного состава в прямых, в кривых и по стрелочным переводам, при служебных торможениях. Число таких нагружений в продольном направлении измеряется тысячами в год, а в вертикальном — даже миллионами. Поэтому основное требование этого режима — недопущение усталостного разрушения узла или детали вагона при действии многократно повторяющихся нагрузок в движущемся поезде. Допускаемые напряжения в узлах подвижного состава определяются, исходя из предела выносливости материала.
Режим больших продольных сил (>1,5 МН) и малой скорости движения (<20 км/ч). Этому режиму обычно соответствуют силы, возникающие при маневрах и в аварийных ситуациях, при экстренных торможениях, столкновении, а также при аварийном рывке (толчке) вагона. Основным требованием этого режима является недопущение остаточных деформаций в узлах или деталях подвижного состава. Число таких нагружений за срок службы ограничено, и не превышает нескольких десятков или сотен тысяч. Поэтому при расчетах по этому режиму допускаемые напряжения устанавливаются близкими к пределу текучести материала и пределу прочности.
Режим катастрофически больших сил (>3,0 МН; v>20 км/ч). Этому режиму соответствует аварийная ситуация, связанная со столкновением или сходом с рельсов на высоких скоростях (более 20 км/ч). Вопрос о последствиях удара для подвижного состава здесь не ставится, главное — сохранение жизни локомотивной бригады и пассажиров.
Защита пассажирского салона и служебных помещений при аварийном столкновении обеспечивается рассеиванием энергии удара за счет:
— работы поглощающих аппаратов и рессорного подвешивания тележек;
— работы дополнительных аварийных амортизаторов разового действия;
— деформации и разрушения межвагонных соединений и тамбурных (концевых) частей кузова, которые преднамеренно проектируют меньшей прочности, создавая так называемые «жертвенные части», при деформации принимающие на себя значительную часть энергии, сохраняя от разрушений пассажирские салоны (рис. 13.13);
— деформаций, в том числе пластических, средней части кузова.
Рис. 13.13. Деформация жертвенной части кузова при испытании на продольное сжатие: смятие и выпучивание элементов конструкции крыши и рамы в районе тамбура вагона электропоезда «Сокол». Россия. 1999 г. |
В качестве критериев безопасности предлагается принимать:
— продольное усилие, соответствующее потере устойчивости жизненного пространства салона для пассажиров;
— ускорение центра масс вагонов;
— энергоемкость деформируемой в аварийной ситуации части кузова.
В действующих в Российской Федерации Нормах [4] предложено использовать в качестве критерия ускорение 4д, продольную силу 2 МН и энергоемкость при действии этой силы не менее 400 кДж. В соответствующих Нормах для электропоездов [22] предложено в качестве разрушающих продольных ударов считать усилия порядка 3 МН, энергоемкость штатных и аварийных деформированных элементов вагонов не менее 2 МДж, а энергоемкость кузова не менее 1 МДж.
При создании поезда TGV-2N в качестве критериев безопасности было принято продольное усилие 5 МН, а ускорение 5д.
При выборе формы кузова головного вагона и локомотива высокоскоростных поездов учитываются требования по обеспечению безопасности локомотивных бригад и пассажиров при аварийных столкновениях. В носовой части кузова первого вагона (локомотива) размещают сцепное устройство повышенной энергоемкости и аварийные амортизаторы удара, предназначенные для защиты в случае наезда поезда на препятствие (рис. 13.14,13.29). В последние годы разработаны аварийные амортизаторы удара с большой энергоемкостью, что позволяет обеспечить необходимые конструктивные параметры без увеличения длины носовой части головного вагона(локомотива). Широкое применение нашли ячеистые металлические конструкции (рис. 13.15), которые при аварийном соударении сми-
а |

б |
Рис. 13.14. Конструкция носовой части головного вагона высокоскоростного поезда AGV с энергопоглощающими модулями: а — схема размещения; б — общий вид на сборочном стапеле завода |
Стремление снизить массу вагона, увеличить жесткость кузова, повысить его надежность и долговечность, обеспечить красивый внешний вид заставляют вагоностроителей искать новые материалы и применительно к ним — соответствующие конструктивные и технологические решения. Опыт создания высокоскоростных поездов позволяет выделить наиболее перспектив-
Рис. 13.15. Ячеистая металлическая конструкция для поглощения энергии удара
ные конструкционные материалы: алюминиевые сплавы и нержавеющую сталь. В последние годы весьма хорошо зарекомендовали себя в производстве и эксплуатации конструкции из слоистого пластика, армированного стекло- и углеволокном, а также многослойные или сотовые панели из металла и пластика.
Алюминиевые сплавы отличаются от углеродистых сталей более высокой прочностью при низкой плотности, повышенной коррозионной стойкостью, они хорошо поддаются обработке резанием и давлением. Кузова из алюминиевых сплавов имеют большую энергоемкость при аварийных соударениях.
Но наряду с отмеченными преимуществами алюминиевые сплавы имеют и недостатки: модуль упругости сплавов почти в три раза меньше, чем стали. Поэтому для устранения опасности потери устойчивости и снижения частоты собственных колебаний конструкции из алюминиевых сплавов изготавливают с большим поперечным сечением.
В первых скоростных поездах применялись главным образом алюминиевые гофрированные и холодноштампованные листы или прессованные профили. В кузовах вагонов современных высокоскоростных
поездов используются, в основном, крупноразмерные экструдированные элементы из алюминиевых сплавов, которые менее подвержены короблению и выпучиванию.
В технически развитых странах для соединения элементов кузова освоена элек- тродуговая сварка алюминиевых сплавов в среде защитных газов (рис. 13.16]. Однако, несмотря на широкое распространение, она имеет и ряд недостатков, которые трудно избежать: изменение механических свойств материала в зоне шва; пористость шва, наросты металла (валик сварочного шва), высокая энергоемкость и т.д.
В последние годы все большее применение при соединении длинных экструдированных профилей в широкую панель для железнодорожного подвижного состава находит техника «фрикционной сварки вращением». Этот способ применен в Японии при создании поездов серии 700, N700, Е5; фирмой Alstom при изготовлении поездов Pendolino и др. Техника сварки основана на приведении алюминия в зоне шва в состояние текучести (как при экструдировании) за счет тепла, выделяемого при трении, с последующим перемешиванием расплавленного металла соединяемых профилей. Затем следует остывание места соединения под формирующим давлением инструмента (рис. 13.17).
За рубежом наряду с алюминиевыми сплавами широко используются и нержавеющие стали.
Рис. 13.16. Изготовление кузова вагона поезда Pendolino с применением автоматической электродуговой сварки |
12 3 4 2 1
Рис. 13.17. Схема установки фрикционной сварки: 1 — соединяемые детали; 2 — зона нагрева; 3 — зона термомеханического воздействия на свариваемые детали; 4 — ядро свариваемого шва; 5 — обрабатываемая поверхность сварного шва; 6 — вращающийся инструмент; 7 — направление движения рабочего инструмента; 8 — давление инструмента на свариваемые детали
струкция непрерывно подкрепляется слоем из легких пористых или ячеистых материалов (пенополистирол, пенополиуретан), причем обшивка может быть как металлической, так и композитной. Наружная и внутренняя обшивки кузова, соединенные непрерывным подкрепляющим слоем, образуют трехслойные плиты, способные эффективно воспринимать сжимающие, растягивающие и изгибающие нагрузки и препятствовать распространению вибраций. Пористый подкрепляющий слой одновременно является хорошей тепло- и звукоизоляцией, поэтому их использование в пассажирских салонах вагонов высокоскоростных поездов особенно перспективно.
Для выполнения нормативных требований современного подвижного состава — по жесткости, деформируемости и прочности, кузова изготавливаются цельноне- сущими. Сборку кузова производят из следующих частей: рама с полом, две боковые и две торцевые стены, крыша и перегородки, разделяющие пассажирское помещение на салон, тамбуры и купе (см. рис. 13.20 и 13.28). Пространственную несущую систему кузова, функционально относительно рамы, можно разделить на верхнюю часть, 58
являющуюся собственно кузовом, обеспечивающим полезно используемый объем для пассажиров, и нижнюю систему, являющуюся пространством для размещения оборудования и вспомогательных агрегатов. В некоторых кузовах нижняя часть не является несущей, а представляет собой фальшборты, закрывающие находящееся под вагонами оборудование. В других случаях нижняя часть включена в силовую конструкцию, что существенно увеличивает жесткость кузова.
По характеру устройства несущих элементов кузова современного подвижного состава выделяют три основных системы.
Подкрепленные листовые системы, в которых несущими элементами являются листы из алюминия, нержавеющей или обычной стали и связанный с ними набор стержней (балок, стоек, дуг и т.п.). Тонкие листы в несущей конструкции такого кузова, ограждающие его объем от внешней среды, принято называть обшивкой. Для предотвращения выпучивания листов их часто выполняют гофрированными или подкрепляют продольными элементами — стрингерами. Соединение осуществляют сваркой или на заклепках. Из-за наличия сварочных деформаций, поверхность листов имеет видимые глазом деформации — выпуклости и вмятины.
Каркасные системы, в которых нагрузки воспринимаются и передаются массивными коробчатыми стержнями. Наружная обшивка способствует повышению общей жесткости системы. В качестве облицовки могут применяться легкие листы из сплавов и стеклопластика, так как обшивка не является основным несущим элементом и меньше подвержена вспучиванию, она получается более гладкой.
Панельные системы, нагрузки в конструкциях воспринимаются несущими панелями, состоящими из наружных и внутренних пластин, которые соединяются для совместной работы. Такие панели выполняются преимущественно в двух вариантах. Используют полые экструдированные профили, соединенные с помощью сварки в основные сборочные единицы (пол, сте-
ны, крыша) и сотовые панели (сэндвич- системы), в которых нагрузки воспринимаются несущими панелями, состоящими из наружной и внутренней оболочек, соединенных для совместной работы легкими пористыми пенополиуретановыми и сотовыми алюминиевыми или композитными наполнителями.
Экструдированные панели после чистовой обработки мест электродуговой сварки практически не подвержены короблению и выпучиванию и имеют высокую местную прочность и хороший внешний вид. Достоинством таких панелей является также выполнение ими не только несущих, но и вибро-, звуко-, теплоизоляционных функций.
Листовые подкрепленные системы кузова состоят из типовых узлов (рис. 13.18). Типичным примером такой конструкции являются кузова вагонов электропоезда ЭР200. Сварная рама (без хребтовой балки) собрана из двух консольных частей, двух прямоугольных элементов в виде прессованных профилей прямоугольного сечения и набора поперечных балок. Концевые и шкворневые балки, а также центральная балка головного вагона выполнены из листов толщиной 10—14 мм, а раскосы изготовлены из прессованного профиля коробчатого сечения. Поперечные балки рамы сделаны из прессованного швеллера высотой 120 мм и шириной полки 60 мм.
Сварная рама кузова покрыта несущим полом, собранным из гофрированных листов толщиной 2 мм. Соединение стыков листов осуществляется только на поперечных балках рамы. Использование гофрированных листов в конструкции пола предусматривалось для полного включения пола в работу кузова при изгибе, сжатии и растяжении.
Крыша изготовлена из гофрированного листа, подкрепленного изнутри потолочными дугами. Средняя часть собирается из двух листов толщиной 2 мм и имеет 14 гофров с шагом 170 мм. Скаты крыши для придания большой жесткости выполнены в поперечном сечении с небольшим радиусом закругления и обшиты гладким листом толщиной 3 мм. Дуги изготовлены из прессованного Z-образного профиля и приварены к листам точечной сваркой.
Для боковой стенки кузова использованы гофрированные листы толщиной 3 мм, армированные горизонтальными и вертикальными элементами жесткости. Все элементы жесткости изготовлены из прессованных профилей Z-образного сечения, за исключением верхнего продольного обвязочного профиля, имеющего Т-образную форму. При сборке боковых стен первоначально собирают стойки оконных и дверных проемов. Профили и стойки соединяют с гофрированными листами обшивки контактной точечной сваркой.
Торцовая стена имеет каркас, сваренный из прессованных швеллерообразных профилей, которые обшиты гофрированным листом алюминия толщиной 3 мм. Каркас лобовой стены головного вагона сделан из прессованных профилей различных сечений. В передней части стены расположены две сварные вертикальные балки.
Для передачи усилия от вертикальных стоек на стойки боковых стен, раму и крышу под окнами лобовой стены смонтирована основная горизонтальная балка. В каркас входит также ряд вертикальных и горизонтальных профилей, придающих лобовой стене головного вагона необходимую форму. Снаружи каркас обшит листом толщиной 2 мм.
Так подробно описанная на примере электропоезда ЭР200 конструкция получила значительное распространение в 1960— 70-е годы XX в., в частности, при изготовлении кузовов вагонов японских высокоскоростных поездов серии 0 (рис. 13.19) и серии 200, позднее — в современных поездах.
Однако, как показали испытания и опыт эксплуатации, относительно простые в изготовлении кузова листовой системы имеют существенный недостаток. Нижняя частота их изгибных колебаний в ряде случаев оказывается менее 8 Гц и может совпадать с частотой галопирования или подпрыгивания рамы тележки. В этом случае плавность хода вагонов существенно ухудшается, становятся заметны вибрации.
в
------------------------------------- ft--Й- dft------------------ ■--------------------------------------- ft---------- D | |||
RVR V * | □ | 1 | |
I I I Io- 1 f / |
3080 |
26 537 |
Рис. 13.18. Электропоезд ЭР200: а — общий вид; б — элементы конструкции кузова вагона; в — основные размеры кузовов головного и промежуточного вагонов |
Каркасная несущая система создана в результате поиска более рациональных конструктивных схем стальных и алюминиевых кузовов. Такие кузова имеют каркас из стержней закрытого или открытого профиля, передающий основные нагрузки совместно с наружной обшивкой. В этих конструкциях допускается применение различных материалов для изготовления каркаса и обшивки.
Нижняя часть вагона (рама) состоит из хребтовой, боковых и шкворневых балок коробчатого сечения. Гофрированная обшивка нижней части кузова и пол увеличивают жесткость всей системы.
Боковые стенки кузова представляют собой решетку из стоек и балок различной толщины, что позволяет выполнять поперечные соединения за счет запрессовки тонких элементов в толстые (как правило, стойки), образуя со сварными соединениями устойчивую жесткую систему.
Обшивка прикрепляется точечной сваркой к каркасу (стойкам и стрингерам), поэтому ее деформации после изготовления значительно меньше, чем в листовых системах. Для повышения жесткости крыши вместо дуг используются арки, устойчивость обшивки крыши обеспечивают гофрированные ребра.
Жесткость кузова каркасного типа выше, чем у листовых конструкций с подкреплениями. Однако разнообразие конструктивных элементов увеличивает трудоемкость изготовления и стоимость вагона. Наличие следов от контактной сварки вызывает необходимость применения шпатлевки для сглаживания поверхности, что увеличивает массу вагона.
Типичным примером такой конструкции являются вагоны поездов семейства TGV. Общий вид вагона и конструкционная схема кузова вагона поезда TGV показаны на рис. 13.20. Рама кузова несимметрична (приведен пример концевого вагона, сцепленного с электровозом), что связано с различными способами опирания кузова. В левой части кузов опирается на тележку через шкворневую балку (на рис. 13.20, б — сторона А), а в правой (сторона Б) — на об-
Рис. 13.19. Кузов головного вагона поезда серии О (ноль) на технологических тележках. Япония. 1964 г.
щую (промежуточную) поддерживающую тележку двух сочлененных вагонов. Обращает на себя внимание мощный каркас боковых стен. Нижняя часть кузова выполнена в виде рам, соединенных продольными элементами, пол и крыша — гофрированы. По данным испытаний, нижняя частота такого кузова больше 10 Гц.
Панельная система позволяет создать кузов вагона еще более прочной, жесткой и надежной конструкции с меньшей массой. Основная идея заключается в изготовлении несущей конструкции из крупногабаритных экструдированных алюминиевых профилей в виде двухслойной оболочки кузова. Экструдированные профили имеют высокую жесткость и хорошо сопротивляются короблению при сварке. Их соединяют продольными швами автоматической сваркой в большие панели с высокой готовностью к сборке. Для обеспечения необходимого внешнего вида применяется фрезерование сварных швов.
Панели из экструдированных профилей обладают не только большой изгибной жесткостью, но и высокой местной прочностью, что позволяет воспринимать сосредоточенные нагрузки. Это свойство используется для крепления оборудования. Главным преимуществом таких конструкций является снижение затрат на изготовление и уменьшение числа компонентов.
Однако, если кпанелям не прикладываются сосредоточенные нагрузки, то их прочность оказывается избыточной, а тепло-
Рис. 13.20. Электровоз и концевой вагон поезда TGV PSE: а — общий вид; 1 — локомотив; 2 — индивидуальная поддерживающая тележка вагона; 3 — концевой сочлененный вагон; 4 — общая (промежуточная) тележка сочлененных вагонов: 5 — сочлененный вагон; 6 — обтекатель на крыше концевого вагона; б — конструкционная схема кузова концевого вагона: 1 — обтекатель на крыше; 2 — крыша; 3 — боковая стена; 4 — торцевая стенка; 5 — место расположения общей промежуточной тележки; 6 — рама вагона; 7 место расположения индивидуальной тележки; А — сторона вагона, обращенная к локомотиву; Б — сторона вагона, обращенная к соседнему вагону
и звукоизоляционные свойства недостаточны. В этих условиях предпочтительными оказываются сэндвич-панели или сотовые элементы.
Типичные панельные конструкции кузовов высокоскоростных поездов имеют следующую принципиальную схему. Для изготовления пола и рамы используются экструдированные профили. На нижней стороне, как правило, имеются направляющие, к которым крепятся модульные блоки подкузовного оборудования. Боковые стенки с вертикальными стойками оконных и дверных проемов изготовляются в виде панелей из экструдированных профилей с усиливающими элементами.
Одними из первых в массовом производстве вагонов применили эту конструкцию в Японии при создании вагонов высокоскоростного поезда серии 300 (введен в эксплуатацию в 1992 г.), в котором наряду с облегченной конструкцией кузова было внедрено немало других технических и технологических новинок (рис. 13.21).
С использованием технологий, близких к этой, изготовлены вагоны поездов Talgo, 1СЕЗ (рис. 13.22), вагоны поездов TGV 2N (рис. 13.23), 1С-2000. Крыши вагонов некоторых поездов выполняют из полых конструкций со встроенными воздуховодами систем кондиционирования воздуха.
В разных странах в конце 90-х годов XX столетия проводились научные и опытноконструкторские разработки с целью выбора лучших конструкций кузовов вагонов и локомотивов. В частности, исследовались кузова оболочкового типа, состоящие из наружной и внутренней оболочек, соединенных так, чтобы они по возможности работали совместно. В опытном японском высокоскоростном электропоезде ЗООХ кузова вагонов были изготовлены из легких сплавов на основе алюминия с применением разных технологий: из объемных экструдированных панелей; из сотовых панелей, лицевые пластины которых имеют наполнитель из алюминиевого листа в виде пчелиных сот с шестигранными ячейками, соединенными пайкой в вакууме; по авиационной технологии — клепкой штампованных дюралюминиевых элементов (рис. 13.24).
В процессе испытания вагонов японского опытного поезда ЗООХ лучшие результаты (наименьшая удельная масса, наибольшая жесткость и прочность конструкции) показал кузов из сотовых паяных панелей, но он оказался и самым дорогим в производстве. Технология с применением сотовых паяных панелей использовалась при изготовлении вагонов высокоскоростного поезда серии 500 (рис. 13.25), но дальнейшего развития не получила. Не нашли применения для высокоскоростного подвижного состава и клепаные конструкции авиационного типа.
Наиболее перспективной оказалась конструкция, в которой применены объемные экструдированные панели из алюминиевых сплавов, называемые в зарубежной печати «двойная оболочка» (англ.: «double skin»). В первом десятилетии XXI века их использовали при изготовлении кузовов вагонов японских поездов серии 700, 700Т, N700, Е5 (рис. 13.26). Характерной особенностью этих панелей являются диагональные внутренние ребра жесткости между тонкими оболочками, пространство между которыми заполняется шумо- и виброизолирующей мастикой. Панели обладают большой жесткостью, их применение значительно сокращает объемы ручного труда при сборке кузова. Пространство между несущими панелями кузова и элементами обшивки интерьера заполняется пенистой звуко-теплоизолирующей массой. По мнению японских специалистов, конструкция кузовов поездов серий 700, N700 (рис. 13.27) обладает высокими техникоэксплуатационными показателями и является одной из самых технологичных и дешевых при поточном производстве.
Современное производство железнодорожного подвижного состава, включая локомотивы и вагоны для высокоскоростного движения, базируется на широкой кооперации, включая международную, и основывается на организации поточного производства, при котором на окончательную сборочную позицию поставляются предва-
Рис. 13.21. Поезд серии 300: а — общий вид головного вагона; б — элементы конструкции кузова. Япония. 1992 г.
Рис. 13.22. Конструкции элементов кузовов вагонов: а — Talgo; б — ICE3
Глава 13 |
Рис. 13.23. Двухэтажные вагоны поезда TGV2N, изготовленные с использованием длинномерных панелей из легких сплавов: а — стенки кузова вагона в сборочном цехе завода компании Alstom. Франция. 2006; б — схематическое изображение элементов |
рительно собранные крупные узлы и агрегаты. Кузов вагона состоит из нескольких крупных сборочных секций (блоков): рамы с элементами крепления подвагонного оборудования и пола, боковыми и торцевыми стенами, крыши (рис. 13.28).
При изготовлении кузовов электровозов в поездах с локомотивной тягой или концевых вагонов для электропоездов, добавляются еще носовые оконечности, имеющие специальные элементы рамы, часто включающие и силовые модули поглощения энергии удара (рис. 13.29, 13.32, 13.33). Носовые оконечности локомотивов или концевых вагонов высокоскоростных поездов имеют обшивку аэродинамической формы, которая, как правило, сложной пространственной формы, определяемой в ходе проектирования расчетами и проверяемой продувкой в аэродинамических трубах моделей, выполненных в различном масштабе, полномасштабных моделей на опытном подвижном составе (рис. 13.30).
Аэродинамическую обшивку часто не включают в силовую схему кузова, с помощью сварки или другими способами ее прикрепляют к несущей раме. Изготовление аэродинамической оболочки — сложная технологическая операция. В Японии, например, оболочки носовых частей концевых вагонов, как правило, выполняют из тонкого листового материала на основе алюминия высокой пластичности, которому придают необходимую пространственную форму на гибочных станках. Затем вручную, с использованием специального инструмента доводят до необходимой формы на деревянных болванках-выколотках. С помощью сварки получают из этих заготовок объемные конструкции, которые прикрепляют к силовой раме, тщательно рихтуют, шпатлюют швы, грунтуют и красят (рис. 13.31). В некоторых конструкциях локомотивов и вагонов применяют аэродинамические обшивки, выполненные из композитных материалов, в частности — стеклопластика (рис. 13.34).
Распространено мнение, что в перспективе для кузовов вагонов высокоскоростных поездов ведущее место должны занять композитные материалы. В настоящее время некоторые детали вагонов французского высокоскоростного поезда AGV изготавливают из углепластика, что позволяет снизить общую массу семивагонного поезда на 70 т (рис. 13.35).
б
1 2 3
Рис. 13.24. Опытный японский поезд серии 300Х (а); б — схематическое изображение различных типов конструкции кузова: 1 — из объемных панелей; 2 — из сотовых паяных элементов; 3 — клепаная конструкция самолетного типа
Рис. 13.25 (начало). Поезд серии 500 (а)
Рис. 13.25 (окончание): б — сечение кузова из сотовых панелей, ячеистая структура |
Вид А |
Рис. 13.26. Конструкция кузова вагона поезда серии 700 (Япония) из объемных панелей типа «двойная оболочка»; разрез панели, внутри видна изолирующая масса (справа вид А) |
Рис 13.27. Поезд серии N700. Япония. 2009 |
Носовая часть с обтекателем |
Крыша |
ГТ5-------------------------------------------------- В- ооооооооооооо | ||
Cl 1------ —— |
|
|
Рама вагона Боковые стены и узлы крепления подвагонного (левая и правая) оборудования |
Торцевая |
Рис. 13.28. Основные элементы кузова концевого вагона высокоскоростного поезда на примере поезда серии 700. Япония |
а |
б |
Поглощающие устройства в виде сотовой конструкции |
типа Шарфенберг |
устройства |
Главные поглощающие |
Рис. 13.29. Высокоскоростной поезд V250 «Альбатрос» для железных дорог Бельгии и Нидерландов. Компания AnsaldoBreda. (Италия) 2009 г.: а — общий вид; б — конструкция носовой части головного вагона с устройствами поглощения удара |
Рис. 13.30. Продувка модели головного вагона высокоскоростного поезда «Сокол» в аэродинамической трубе. Россия. 1995 г. |
Рис. 13.31. Изготовление головного вагона высокоскоростного поезда серии 700 на заводе компании «Кавасаки»: а — сборка объемной рамы носового обтекателя; б — вид обтекателя после обшивки панелями
Рис. 13.32. Схематическое изображение конструкции носовой части электровоза поезда TGV Duplex с элементами поглощения энергии удара (заштрихованы)
Рис. 13.33. Кузов электровоза высокоскоростного поезда КТХ. Завод компании Alstom. Франция. 1996 г. |
Рис. 13.34. Обтекатели носовых частей электровозов высокоскоростных поездов Thalys РВКА (слева) и TGV Duplex, изготовленные из стеклопластика. Завод компании Alstom. Франция. 1996 г.
|
Рис. 13.35. Кузов вагона поезда AGV на сборочном стапеле. Франция. 2010 г. (а); оконечные балки кузова из углепластика (б) |
13.3. Ходовая часть высокоскоростного подвижного состава
При создании ходовых частей высокоскоростного подвижного состава приходится по-новому ставить и решать задачи обеспечения безопасности, плавности хода, уменьшения колебаний при высоких скоростях движения и др., поэтому создание тележек локомотивов и вагонов современных экспрессов требует применения высоких технологий.
Для решения динамических задач, прежде всего, необходимо тщательное исследование динамических свойств разрабатываемой конструкции, в результате которого определяют с необходимой точностью основные динамические характеристики конструкции, в частности, собственные частоты, собственные формы и коэффициенты демпфирования колебаний.
Определение собственных частот, форм и коэффициентов демпфирования в ряде случаев является более трудным этапом исследования, чем прочностные расчеты, так как в этом случае решаются огромные системы дифференциальных, а не алгебраических уравнений. Например, вагон высокоскоростного поезда в диапазоне до 20 Гц в целом имеет около 30 собственных частот движения как систем твердых тел и около 20 собственных частот колебаний кузова как упругого тела. Даже использование сложных конечно-элементных схем, без дополнительного экспериментального обоснования не дает уверенности в правильности результатов.
В свою очередь, собственные частоты, формы и коэффициенты демпфирования рельсовых экипажей определяются массами, моментами инерции основных элементов и свойствами упругих и демпфирующих элементов. Упругие элементы тележек современных высокоскоростных поездов имеют разнообразную конструкцию: металлические рессоры; пружины и торсионы; пневматические подвески. С точки зрения динамических свойств подвижного состава конструктивное исполнение упругого элемента, способ его установки не имеет значения, важен вид силовой характеристики упругого подвешивания, т.е. зависимость прогиба /от вертикальной нагрузки на упругий элемент Р:
Р = Р(/).
Производная c = dP/dfназывается жесткостью рессорного подвешивания. Если жесткость постоянна (т.е. с = const), то считают, что такое подвешивание имеет линейную характеристику, если жесткость зависит от прогиба, то упругая характеристика нелинейная.
Для рессорного подвешивания с постоянной жесткостью, жесткость обычно определяется как отношение сил тяжести брутто Рст приходящейся на рессорный комплект, к статическому прогибу рессорного комплекта /ст от этой силы:
Для линейного подвешивания в этом случае имеется связь между собственной частотой колебаний подпрыгивания кузова и статическим прогибом, и существует общая зависимость: чем больше статический прогиб, тем меньше жесткость рессорного подвешивания и собственная частота:
=С/М = gj
где д — ускорение свободного падения.
Многочисленные исследования показывают, что уменьшение жесткости рессорного подвешивания при прочих равных условиях благоприятно сказывается на плавности хода рельсовых экипажей. Поэтому существующие тенденции в развитии конструкций рессорного подвешивания, направленные на улучшение плавности хода, в первую очередь характеризуются снижением жесткости рессорного подвешивания и соответствующим увеличением статического прогиба/сг
Наилучшая плавность хода получилась бы при жесткости рессор, близкой к нулю. Однако, если учесть возможность сцепления порожнего и груженого вагона, обес
печение ограничений по валкости кузова на рессорах и особенности восприятия человеком вибраций различного частотного состава и укачивание («морская болезнь») считается оптимальной частота колебаний подпрыгивания кузова 0,9—1,2 Гц.
Реализовать прогибы более 200 мм трудно, поэтому в современных конструкциях используют нелинейные упругие элементы, которые обеспечивают рациональную величину жесткости только в диапазоне реальной фактической загрузки. В этом случае вводится понятие эквивалентная (приведенная) жесткость Сэ, и эквивалентный статический прогиб которые определяются следующим образом:
df |

при Р=РСГ |
Существует рекомендация, предлагающая устанавливать численную величину статического прогиба рессорного подвешива-
Рис. 13.36. Связь между статическим прогибом / нагрузкой Рп и эквивалентным прогибом fcrдля рессор с различными видами силовых характеристик: 1 — линейной; 2 — жесткой; 3 — мягкой
ния вагона высокоскоростного поезда, в мм, равной конструкционной скорости, в км/ч. Так для поезда с конструкционной скоростью 200 км/ч, необходим статический прогиб подвешивания 200 мм, а для поезда с конструкционной скоростью 300 км/ч — 300 мм.
Демпфирование колебаний современных рельсовых экипажей, в том числе высокоскоростных в основном осуществляется за счет сил трения. При этом следует различать несколько видов трения.
1. Вязкое трение, которое зависит от скорости относительных перемещений подрессоренных и неподрессоренных масс. В подвижном составе такое трение создается специальными устройствами — гидравлическими гасителями колебаний. В пневматическом рессорном подвешивании аналогичные по закону изменения силы трения возникают при перетекании воздуха в дополнительный резервуар через дроссельный проход.
2. Сухое трение, которое зависит в основном от направления движения (знака скорости). Такое трение возникает между листами рессор, в шарнирах, челюстных направляющих, пятниках или специальных устройствах — фрикционных гасителях колебаний.
3. Внутреннее трение, которое пропорционально относительному перемещению и сдвинуто по фазе относительно перемещения на величину л/2. Такое трение возникает в упругих резиновых элементах и любых других конструкционных материалах. В этом случае демпфирующие свойства конструкционных материалов не зависят от частоты колебаний — влияние внутреннего трения существенно при использовании в рессорном подвешивании больших объемов резины или при высокочастотных вибрациях кузова.
Четкую границу между действием различных видов трения в рельсовых экипажах провести трудно, так как они действуют одновременно. Задача выбора оптимального демпфирования является более сложной, чем выбор жесткости. Большое демпфирование уменьшает амплитуды колебаний при
резонансах, однако, существенно увеличивает ускорение кузова, как при прохождении единичных неровностей, так и в зарезонансной области. Коэффициент относительного демпфирования /-той формы колебаний железнодорожного экипажа вычисляется по формуле
1 {v/’Kltv) '2ш, (y.l'lMKv,)'где [С] и [ЛГ] — соответственно матрицы демпфирования и инерции динамической модели экипажа, в которой кузов и обрессоренные массы тележек представляют собой твердые тела, соединенные между собой упругими и диссипативными связями; {у.} — вектор-столбец, характеризующий /-ую форму колебаний; со, — собственная частота /-той формы колебаний.
Коэффициенты относительного демпфирования определенной формы колебаний определяют величину демпфирования по отношению к собственной частоте данной формы, что имеет физический смысл отношения к критическому демпфированию, при котором прекращаются колебания.
Для демпфирования колебаний вагонов рекомендуется коэффициенты относительного демпфирования иметь в пределах:
-для вертикальных колебаний — 0,2...0,3;
-для горизонтальных колебаний — 0,3...0,4;
-для боковой качки — 0,1...0,2.
Для получения таких коэффициентов демпфирования в ходовых частях современного высокоскоростного подвижного состава применяют гидравлические гасители колебаний и устройства с резиновыми или полиуретановыми амортизирующими элементами. В некоторых случаях ставят гасители колебаний с регулируемой силой сопротивления, что позволяет обеспечивать хорошие ходовые качества независимо от состояния пути.
Устройство тележки. Необходимые уп- руго-демпфирующие характеристики подвешивания реализуются в конструктивных схемах рессорного подвешивания тележек, которое в пассажирских вагонах, как правило, включает две ступени — буксовую и центральную. Буксовая ступень является 74 первичной, служит для подрессоривания вагона, в ней реализуется передача усилий от колесной пары на раму тележки. Эта ступень играет доминирующую роль в обеспечении устойчивости движения при высоких скоростях на прямых участках пути и обеспечении вписывания в кривые.
Для реализации высоких скоростей движения необходима увеличенная горизонтальная продольная жесткость и несколько уменьшенная (примерно в 2 раза] поперечная жесткость буксовой ступени рессорного подвешивания. В кривых участках пути с увеличением жесткости происходит усиление воздействия гребней колес на головку рельса, что ухудшает динамические качества вагона. Одним из подходов в решении данной проблемы является создание такой конструкции буксовой ступени, в которой можно реализовать разные продольную и поперечную жесткости и удовлетворить требования по обеспечению безопасного движения с высокими скоростями как в прямых, так и в кривых участках пути.
Для решения этой задачи используются два основных компромиссных варианта: применение поводков и резинометаллических элементов.
Исторически первой конструкцией, удовлетворявшей указанным требованиям и освоенной в массовом производстве вагонов, предназначенных для движения со скоростью более 200 км/ч, была тележка модели DT200 — вагонов первого в мире высокоскоростного электропоезда серии 0 (ноль) в Японии[XIV], эксплуатация которых началась в конце 1964 г. В качестве буксового узла использована конструкция с пластинчатыми поводками (рис. 13.37, 13.38), впервые примененная в 1950 г. в тележке Minden- Dentz (Германия), получившая обозначение 1S. Для снижения вертикальных деформаций пружин жесткость буксовой ступени делают высокой. Это допустимо в случаях применения в центральной ступени пнев-
Рис. 13.37. Конструкция буксового узла подвешивания типа IS тележки DT200 вагонов высокоскоростного поезда серии 0 (ноль). Япония. 1963 г.: 1 — поводки в виде пластин (плоских стальных пружин); 2 — рама тележки; 3 — пружины буксового подвешивания; 4 — букса |

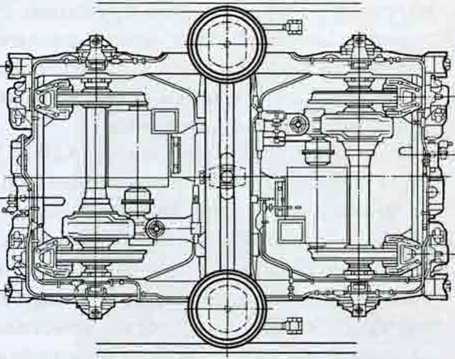
а |
О о гЧ |
LT. СО Tj- |


Рис. 13.38. Тележка типа DT200: а — вид сверху; б — вид сбоку; в — вдоль пути. Япония. 1963 г. |
3164 2840 2500 |
1300 |
моподвешивания, как это и было сделано в тележке DT200. При вертикальной деформации пружин поводки в результате собственного изгиба дают возможность поступательного перемещения буксы. Пластины- поводки жестко крепятся к раме тележки и буксе и упруго деформируются при вертикальных колебаниях. При этом в горизонтальной плоскости жесткость пластины значительно больше, что обеспечивает передачу через нее горизонтальных усилий. Такая конструкция обеспечивает различные жесткости в продольном и поперечном направлении.
Конструкция моторной тележки типа DT200 (в поезде серии 0 все вагоны были моторными) демонстрирует важный подход японских проектировщиков к созданию качественно нового продукта, в данном случае, тележки для пассажирских вагонов, рассчитанных на эксплуатацию со скоростью 210 км/ч. Тележки были сформированы из хорошо известных элементов, эксплуатационные достоинства которых были подтверждены практикой. Позже японские вагоностроители продолжили использование в конструкциях тележек буксового узла с пластинчатыми поводками (рис. 13.39).
Шарнирно-поводковый механизм с резинометаллическими шарнирами (сайлент- блоками) впервые применила фирма Als- thom (Франция) в тележке Y-32 для пассажирских вагонов (рис. 13.40). Это позволило избавиться от поверхностного трения и связанных с ним износов. Пример такого
Рис. 13.40. Фрагмент тележки Y32 пассажирского вагона. Франция. 80-е годы XX века
Рис. 13.39. Тележка высокоскоростного поезда серии Е6 (Япония. 2012 г.): 1 — гидравлический гаситель колебаний первичной ступени подвешивания; 2 — букса; 3 — предохранительный ограничительный угольник системы противодействия выходу за пределы рельсовой колеи при сходе с рельсов; 4 — поводки в виде пластин (плоских стальных пружин); 5 — гасители колебаний виляния (один из них отключается при движении по линии Мини-Синкансэн для уменьшения динамического воздействия подвижного состава на путь); 6 — рама тележки (см. п. 17.5, рис. 17.28) |
В этом случае полностью разделены функции направления (тяги с шаровыми шарнирами в буксовой ступени) и вертикального опирания (стальная пружина). Такое решение сохраняет хорошее качество хода тележки и позволяет значительно улучшить характеристики механизма гашения колебаний в вертикальном направлении в буксовой ступени. Однако имеется недостаток, связанный с коаксиальным скручиванием сайлент-блоков, что особенно нежелательно на моторных тележках.
В буксовой ступени моторных тележек поездов TGV (и AVE серия 100), например, использованы пружинные комплекты цилиндрические направляющие и резинометаллические амортизаторы (рис. 13.41, 13.42,13.43). Основная часть вертикальной нагрузки воспринимается пружиной. Резинометаллический блок имеет различную жесткость в продольном и поперечном направлениях, а также частично выполняет функции гасителя колебаний.
В тележках шведского поезда Х2000 (рис. 13.44) буксовое подвешивание выполнено на шевронных резинометаллических рессорах, обеспечивающих возможность радиальной установки колесных пар в кривых. Пакеты резины, соединенные вулканизацией с металлическими пластинами, установлены наклонно к горизонтальной плоскости. При таком расположении резиновая прокладка под действием вертикальной нагрузки на буксу одновременно испытывает напряжения сжатия и сдвига. Благодаря принятой форме упругих элементов, жесткость в продольном направлении в 3—6 раз больше, чем в поперечном. Недостатком этой конструкции явля-
Рис. 13.41. Поддерживающая промежуточная тележка модели Y-237 поезда TGV А и AVE (Франция — Испания): 1 — гидравлический гаситель колебаний буксового подвешивания; 2 — букса; 3 — пружина буксового подвешивания; 4 — рычаг с резинометаллическим шарниром; 5 — пневморессора центрального подвешивания; 6 — дополнительный резервуар; 7 — тормозные диски
Рис. 13.42. Моторная тележка электровоза поезда AVE (TGVА): 1 — редуктор первой ступени; 2 — пружины центрального подвешивания; 3 — тяговые двигатели; 4 — рама тележки; 5 — буксовый гидравлический гаситель колебаний; 6 — букса; 7 — пружина буксового подвешивания; 8 — резинометаллический амортизатор; 9 — редуктор второй ступени на оси колесной пары; 10 — шлицевой вал шарнира равных угловых скоростей тяговой передачи
12 3 1 |
Рис. 13.43. Первичное подвешивание моторной тележки электровоза TGV POS (Франция): 1 — резинометаллический амортизатор; 2 — буксовый гидравлический гаситель колебаний; 3 — букса |
/ / \ \ |
12 3 4 |
Рис. 13.44. Фрагмент тележки вагона высокоскоростного поезда X 2000 (Швеция. 1989 г.): 1 — рама тележки; 2 — шевронные резинометаллические рессоры первичной ступени подвешивания; 3 — букса; 4 — гидравлический гаситель колебаний первичной ступени подвешивания |
ется зависимость упругих и механических характеристик от температуры окружающей среды.
В опытном поезде V150 (Франция), который в 2007 г. установил мировой рекорд скорости 574,8 км/ч, в первичном подвешивании тележек двухэтажных вагонов использовались резинометаллические амортизаторы с цилиндрическими направляющими, применяемые на поезде TGV 2N NGV Duplex.
Центральное подвешивание пассажирского вагона должно обеспечивать необходимую плавность хода и комфортные условия проезда пассажиров. Традиционным типом центрального подвешивания, применяющегося более 100 лет в пассажирских вагонах, является конструкция в виде люльки. В этом случае обеспечивается возвращающее усилие люльки при боковых смещениях кузова вагона. В таких схемах нагрузка от кузова вагона передается через пятник на надрессорную балку. Такая конструкция, являющаяся относительно дешевой в изготовлении, с различными усовершенствованиями применяется и на высокоскоростном подвижном составе.
Рис. 13.45. Поддерживающая тележка вагона поезда 1СЕ1 (Германия): 1 — гидравлический гаситель колебаний вторичной ступени подвешивания; 2 — надрессорная балка; 3 — реактивные штанги; 4 — цилиндрическая пружина первичной ступени подвешивания; 5 — букса; 6 — гидравлический гаситель колебаний первичной ступени подвешивания; 7 — цилиндрические пружины вторичной ступени подвешивания |
Безлюлечная конструкция имеет меньше деталей в центральном подвешивании, что устраняет сложности, связанные с ремонтом. Эта система базируется на использовании упругих свойств элементов подвешивания в вертикальном и горизонтальном направлениях. Детали могут быть выполнены в виде удлиненных пружин типа «Flexicoil»[XV], которые применяются, например, в тележках локомотивов и вагонов итальянских высокоскоростных поездов (рис. 13.46).
Практически во всех последних конструкциях высокоскоростного подвижного состава в центральной ступени подвешивания используются пневматические рессоры. Они представляют собой резиновые баллоны, армированные кордом (конструкция похожая на автомобильную шину), иногда частично заключенные в металлический кожух (рис. 13.47). Баллоны нижней частью установлены на раме тележки, а на их верхнюю часть опирается кузов. На каждой тележке, как правило, имеется два баллона — слева и справа от ее продольной оси симметрии.
Интенсивные исследования и инженерные разработки по созданию воздушных и газовых рессор для пассажирских вагонов начались после Второй мировой войны в связи с потребностью в увеличении скорости движения поездов. Преимущество пневматической подвески по сравнению с традиционными типами пружинных рессор заключается в том, что они препятствуют передаче высокочастотных колебаний и шума от тележек к кузову. Важным свойством пневморессор является возможность изменяя давление воздуха (газа) регулировать жесткость подвешивания (изменять в широких пределах величину статического прогиба). Это позволяет при разной массе вагона (например, при различной его загрузке) поддерживать неизменной высоту кузова над уровнем головки рельса. В свою
2 |
б |

1 |
Рис. 13.46. Тележки высокоскоростного поезда ETR 500: а — электровоза; б — прицепного вагона; 1 — пружины центрального подвешивания; 2 — пружины первичного подвешивания. Италия. 1992 г. |
очередь это способствует улучшению ходовых качеств подвижного состава и созданию унифицированных тележек для различных типов вагонов.
Одна из первых пригодных для практической эксплуатации конструкций пневматических рессор была разработана в США в конце 1940-х годов для тележки скоростного пассажирского вагона «Pioneer». В СССР на- 80
чало теоретическим исследованиям в области создания пневморессор положили работы, начавшиеся под руководством А.В. Кузнецова в 50-х годах в Научно-исследовательском институте вагоностроения. В 1964 г. на участке Калинин — Бологое были проведены скоростные испытания вагонов с разработанными в СССР тележками на пневматических рессорах баллонного и диафраг-
Рис. 13.47. Центральное пневматическое подвешивание вагона поезда TGV Т. Франция
менного типов. В 1972 г. на Калининском вагоностроительном заводе была создана тележка ТСК-1 с диафрагменными пневморессорами для скоростного вагона РТ200, а в 1974 г. выпущен скоростной электропоезд ЭР200, вагоны которого имели пневмоподвешивание.
Тележки с центральным пневматическим подвешиванием применяются на эксплуатируемых в настоящее время поездах Х2000, Швеция (см. рис. 13.44);TGV, Франция (см. рис. 13.41; рис. 13.47), поездах линий Синкансэн Япония (рис. 13.48), на вагонах высокоскоростного поезда компании «Bombardier», Канада, 2010 г. (рис. 13.49), «Сименс» и др.
Важно отметить, что подобные устройства подвешивания достаточно сложны в изготовлении, поэтому необходимо иметь технологически подготовленную производственную базу. Однако именно такая конструкция позволяет достичь наилучших результатов на подвижном составе, предназначенном для высоких скоростей движения.
Во всех вагонах высокоскоростных поездов для обеспечения демпфирующих свойств ходовых частей применяется схема раздельного гашения колебаний в разных ступенях подвешивания, что позволяет создать эффективную схему успокоения и обеспечить надлежащий комфорт для пассажиров. Как правило, в буксовой ступени подвешивания устанавливают вертикальные гасители колебаний; в центральной — вертикальные демпферы — гасители относа (горизонтальные поперечные) и горизонтальные гасители виляния (вдоль оси пути).
В 30—40-е годы XX в. в устройствах подвески вагонов вместо фрикционных гасителей колебаний началось использование гидравлических гасителей, успешно зарекомендовавших себя к тому времени в автомобилестроении. Применение гидравлических демпферов позволяет избавить конструкцию от негативного воздействия пар сухого трения и улучшает ее ходовые качества при высоких скоростях движения.
Одними из первых гидравлическими гасителями колебаний были оснащены тележки скоростной автомотрисы «Комета», построенной в 1935 г. в США для железной дороги Нью-Хавен. В конце 40-х годов прошлого века такие элементы систем подвески уже широко использовались на скоростном подвижном составе, в частности, на новых тележках скоростных пассажирских вагонов «Pioneer» (США), Minden-Dentz, 1950 г. (ФРГ), на тележках скоростных ди- зель-поездов. Принцип действия гидравлических гасителей колебаний заключается в последовательном перемещении вязкой жидкости поршнем через узкие (дроссельные) каналы и всасывании ее обратно через клапан одностороннего действия. При прохождении жидкости через дроссельные каналы возникает вязкое трение, в результате чего механическая энергия колебательного движения вагона превращается в тепловую, которая затем рассеивается.
На рис. 13.50 показана схема устройства гидравлического гасителя колебаний и при- 81
Пневматические рессоры |
Рис. 13.48. Моторная тележка вагона поезда серии Е1. Япония |

Пневматические рессоры |
Рис. 13.49. Пневматическое подвешивание тележки вагона высокоскоростного поезда компании «Bombardier». 2008 |
мер его конструктивного исполнения. При движении поршня 6 вниз (сжатие) верхний клапан 7 приподнимается, и жидкость из полости под поршнем перетекает в полость, расположенную над ним. Вследствие движения штока 1 давление в полости рабочего цилиндра 4 повышается, и часть жидкости с большим гидравлическим сопротивлением перетекает через дроссельные отверстия нижнего клапана 8 в резервуар 5. При движении поршня 6 вверх (растяжение) верхний клапан 7 закрывается, давление жидкости в пространстве над поршнем 6 повышается, и жидкость с большим гидравлическим сопротивлением перетекает через дроссельные каналы верхнего клапана 7 в полость под поршнем. Одновременно в этой полос-
Рис. 13.50. Устройство гидравлического гасителя колебаний: 1 — шток; 2 — направляющая втулка; 3 — цилиндр; 4 — рабочий цилиндр;
5 — резервуар; 6 — поршень; 7 — верхний клапан; 8 — нижний клапан
ти наступает разряжение, так как объем перетекающей в нее из полости над поршнем жидкости меньше объема самой полости. Вследствие этого нижний клапан 8 поднимается и часть жидкости засасывается в зону под поршнем из резервуара 5, заполняя освобожденное штоком 1 пространство. Резервуар 5 гасителя колебаний служит не только емкостью для жидкости, вытесняемой штоком 1 из цилиндра 3, но и сборником жидкости, просачивающейся через кольцевой зазор между направляющей втулкой 2 и штоком 1. Рабочей жидкостью для гидравлических гасителей колебаний вагонных тележек служат масла: веретенное, приборное и трансформаторное, а также другие специальные жидкости. Размещение гидравлических гасителей колебаний на современных железнодорожных тележках видно на фото выставочного стенда и на тележке вагона высокоскоростного поезда [рис. 13.51).
Необходимо отметить, что проход экипажем кривых участков пути ведет к увеличению механических напряжений в ходовых частях. Эффективным средством снижения износов колес и рельсов является установка колесных пар в кривых по радиусу («радиальная» установка) [рис. 13.52). Примером такой конструкции является устройство тележек вагонов высокоскоростных поездов серии Х2000 (Швеция), в которых в буксовых узлах установлены упругие элементы, обеспечивающие незначительное пассивное отклонение осей колесных пар.
Разработаны и другие конструкции тележек с колесными парами, устанавливаемыми по радиусу кривых. Эти системы эффективны на магистралях, где имеется много кривых. Пока такие системы не получили широкого распространения в силу более высокой цены и увеличения затрат на эксплуатацию, по сравнению с обычными.
Особым типом подвешивания является маятниковая подвеска. Она нашла применение на подвижном составе, который эксплуатируется на железных дорогах с множеством кривых участков пути. Благодаря размещению опорных поверхностей выше центра массы кузова, при движении в кривой происходит больший крен кузова, чем при других типах подвешивания, с отклонением верхней части кузова внутрь кривой (см. п. 13.5).
В последнее десятилетие в ряде стран в работе по улучшению ходовых свойств подвижного состава и повышения комфорта проезда пассажиров были достигнуты ощутимые результаты в создании так называемых «активных систем» подавления колебаний кузова вагона. По степени сложности их разделяют на так называемые «полностью активные системы управления» и «полуактивные системы управления»[XVI]. Исследования и разработки в этой области велись в ряде стран, впервые в коммерческой эксплуатации активные и полуактивные устройства подавления вибрации были введены в 2000 г. на высокоскоростном
1 2
Рис. 13.51. Гидравлические гасители колебаний в первичном и вторичном подвешивании, гасители виляния (на фото показаны с демонстрационными разрезами): а — выставочный макет; 1 — букса; 2 — пружина первичной ступени подвешивания; 3 — гидравлический гаситель колебаний первичной ступени подвешивания; 4 — рама тележки; 5 — гидравлический гаситель колебаний виляния;
6 — гидравлический гаситель колебаний центральной ступени подвешивания; б — тележка вагона высокоскоростного поезда: 1 — гаситель колебаний виляния; 2 — вертикальный гаситель колебаний первичной ступени подвешивания
Рис. 13.52. Схемы тележек: а — «обычная» установка; б — «радиальная» с колесными парами, устанавливающимися по радиусу кривой (тележка вагона поезда Х2000) поезде серии Е2-1000 Восточной японской железнодорожной компании.
На рис. 13.53, а приведена упрощенная блок-схема активной системы управления подавлением вибрации кузова вагона. Суть ее работы сводится к следующему. Установленный на уровне пола пассажирского салона датчик поперечных вибраций кузова передает в контроллер системы данные о величине и частоте возникающих вибраций. Контроллер анализирует поступающую информацию и вырабатывает управляющие команды для привода (его иногда называют активатором) подавления колебаний, уставленного в узле связи между кузовом и тележкой. Сжатый воздух, направляемый в левую или правую полость цилиндра привода, вызывает движения поршня, совпадающего по частоте с частотой возмущающих вибраций, по направлению — противоположных усилиям вибраций, а по величине — соответствующих величине импульсов колебаний. Таким образом, происходит активное подавление поперечной вибрации кузова вагона.
На большинстве выпускаемых в настоящее время в Японии высокоскоростных поездов в головных вагонах, испытывающих наибольшие колебания кузова, установлена активная система подавления вибрации. Принципиально их конструкции не отличаются от описанной выше, однако вместо пневматического привода используется гидравлический, что способствует повышению эффективности системы. На промежуточных вагонах установлены относительно меньшие по стоимости полуактивные системы подавления вибрации (рис. 13.53, б).
В этой системе также имеется датчик поперечных колебаний кузова вагона. Данные о величине и частоте вибраций поступают в контроллер, где происходит их обработка. В результате контроллер выдает управляющую команду на гидравлический гаситель колебаний, установленный в узле связи тележки и кузова вагона. Используемый гаситель колебаний имеет устройство изменения жесткости, величина которой задается контроллером исходя из реальной ситуации колебаний кузова вагона. Принцип действия гасителя колебаний переменной жесткости показан на схеме (рис. 13.54).
На рисунке показано, что левая и правая полости цилиндра гидравлического гасителя колебаний соединены между собой трубками с калиброванными отверстиями (жиклерами), величина которых определяет объем масла, переходящего из одной полости в другую в единицу времени (скорость движения поршня), следовательно, изменяется жесткость гасителя колебаний. В гасителе колебаний поезда серии 700 (введен в эксплуатацию в 1999 г.) управление жесткостью осуществляется открытием и закрытием с помощью контроллера электромагнитных клапанов. В поезде следующей серии — N700 (эксплуатируется с 2007 г.) в схему введен дополнительно пропорциональный электромагнитный перепускной клапан, а также еще один клапан — в соединительной трубке между ближним и дальним концами правой полости цилиндра. Управление пропорциональным и дополнительным клапаном с помощью контроллера позволило осуществлять более точную настройку жесткости гидравлического гасителя колебаний по условиям движения и более эффективно снижать колебания кузова вагона (рис. 13.55).
Уменьшению вибраций вагонов, снижению поперечных колебаний способствует
со |
Контроллер |
Сжатый воздух |
Кузов вагона |
Датчик |
» |
- | |Л1 | |
Тележка |
|
вибрации |
\ Привод |
Усилие |
Вибрация |
Контроллер |
Привод |
Тележка |
Тележка |
Сжатый воздух |
Кузов вагона |
» I |
Данные |
Кузов вагона |
Противодействие J |
Вибрация |
Контроллер |
Сжатый |
1 Датчик -поперечных |
I»4Сжатый воздух создает усилие, противодействующее вибрации |
Контроллер |
Тележка |
Полуактивная система \ управления |
_ Датчик поперечных вибрации |
Кузов вагона |
Кузов вагона |
Кузов вагона |
Контроллер |
Контроллер |
Тележка |
I— Датчик поперечных вибрации |
Полуактивная система управления |
Полуактивная ^управления |
Тележка |
Подавление вибрации |
i “Ц / * ■ | —— Датчик —~ 'поперечных вибрации |
II |
Усилия |
Рис. 13.5.3. Упрощенная блок-схема системы управления подавлением вибрации кузова вагона высокоскоростного поезда серии Е2-1000: а — активной системы; б — полуактивной системы |
Поезд |
Вибрация |
Поезд |
Кузов вагона |
Поршень |
Цилиндр |
Масло |
Вибрация |
Тележка |
Клапаны Калиброванные отверстия (жиклеры) |
Вибрация Кузов вагона |
Цилиндр Поршень Г° Жиклер®! |
С |
Масло |
Клапаны |
Вибрация |
Тележка |
Пропорциональный электромагнитный перепускной клапан |
Рис. 13.54. Схематическое изображение гидравлического гасителя колебаний переменного сопротивления, используемого в полуактивной системе подавления колебаний кузова вагонов японских высоко скоростных поездов: а — серии 700; б — серии N700
Рис. 13.55. Система подавления колебаний вагона высокоскоростного японского поезда серии N700: а — контроллер управления; б — гидравлический гаситель колебаний переменного сопротивления с блоком коммутации; в — размещение на тележке |
Рис. 13.56. Установка межкузовных гидравлических гасителей колебаний: а — внешний вид гасителя продольных колебаний, установленного между кузовами вагонов высокоскоростного поезда серии N700. Япония; б — расположение гасителей на кузове вагона; 1 — гасители вертикальных колебаний; 2 — гасители продольных колебаний; 3 — жесткое межвагонное сцепное устройство |
Рис. 13.57. Тележка высокоскоростного поезда серии N700. (Япония, 2007 г.); основные детали и узлы: 1 — рама; 2 — опора пневматической рессоры центрального подвешивания; 3 — пневматическая рессора центрального подвешивания и механизма наклона кузова; 4 — тяга; 5 — активатор системы подавления вибрации кузова; 6 — опора кузова; 7 — кронштейн крепления к кузову гидравлического гасителя колебаний виляния (кронштейн крепится к кузову вагона); 8 — редуктор тягового привода; 9 —тяговый двигатель; 10 — гидравлический гаситель колебаний виляния; 11 — кронштейн опоры центрального подвешивания; 12 — высоторегулирующий клапан пневматической рессоры центрального подвешивания с поводком; 13 — гидравлический гаситель колебаний первичной ступени подвешивания; 14 — букса; 15 — пружина первичной ступени подвешивания; 16 — колесная пара; 17 — ось колесной пары; 18 — муфта |
установка гасителей колебаний, связывающих между собой кузова двух соседних вагонов (рис. 13.56).
Завершая рассмотрение конструкций тележек высокоскоростных поездов приведем в качестве примера упрощенный сборочный чертеж одной из лучших современных конструкций — моторную тележку высокоскоростного поезда серии N700, Япония, 2007 г. (рис. 13.57).
Подводя итог можно выделить следующие основные направления в техническом развитии и совершенствовании ходовых частей высокоскоростного подвижного состава:
— в буксовой ступени подвешивания применяются упругие элементы, реализующие раздельно продольную и поперечную жесткость с характеристиками, удовлетворяющими как требуемой устойчивости движения в прямых участках пути, так и вписыванию в кривые с высокими скоростями;
— использование безлюлечной конструкции центральной ступени подвешивания, обеспечивающей высокие показатели комфортного проезда пассажиров со скоростями 250—350 км/ч;
— на скоростном подвижном составе для эксплуатации на участках с множеством кривых вводятся устройства радиальной установки колесных пар и технических средств, обеспечивающих дополнительный наклон кузова вагона внутрь кривой;
— во всех конструкциях тележек локомотивов и вагонов высокоскоростных поездов применяются только гидравлические гасители колебаний.
13.4. Сцепные устройства высокоскоростного подвижного состава
Важную роль в обеспечении надежной и безопасной эксплуатации железнодорожного подвижного состава играют сцепные приборы, с помощью которых вагоны и локомотивы соединяются в поезд и действуют как единая пространственная система, включающая несколько подсистем: механическую, пневматическую, энергетическую, информационную, а в случае электрической тяги — электромеханическую и подсистему электроснабжения. На обычных (не высокоскоростных) железных дорогах многих стран мира, в том числе и европейских, как в грузовом, так и в пассажирском движении, продолжают применять сцепные приборы с винтовой стяжкой (рис. 13.58). При ее использовании на под-
а
б
Рис. 13.58. Сцепные приборы с винтовой стяжкой: а — общий вид; б — сцепщик вагонов за работой
вижном составе обязательна установка буферов — пружинных амортизаторов, смягчающих удары вагонов и локомотивов:при сближении происходит сжатие пружины буферных устройств. После этого на крюки вручную накидывают стальные петли и вращением винта сближают тарелки буферов соседних вагонов так, чтобы они постоянно соприкасались. Использование винтовой стяжки требует при осуществлении сцепки и расцепки вагонов и локомотивов тяжелого и опасного физического труда составителей поездов (сцепщиков[XVII]). Однако для внедрения единых в масштабах больших железнодорожных систем автоматических сцепных устройств (автосцепки) для всего подвижного состава необходимы значительные единовременные затраты, согласованные действия многих заинтересованных и причастных организаций, структур, ведомств. Только несколько стран в мире, в частности, США, СССР, КНР оказались способны внедрить на своих железнодорожных сетях единую и совместимую систему автосцепки вагонов и локомотивов.
Ручная сцепка с винтовыми стяжками сейчас используется и на грузовом, и на пассажирском подвижном составе многих железных дорог мира. Такие сцепные устройства установлены и на первых французских высокоскоростных поездах серии TGV PSE (TGV Sud-Est) и TGV La Poste (TGV—почтовый). Как известно, эти поезда состоят из сочлененных вагонов, что исключает необходимость использования сцепных устройств между ними. Однако сцепка необходима между электровозами и концевыми вагонами.
Широкое внедрение в начале XX в. моторвагонного подвижного состава, как электрического, так и с двигателями внутреннего сгорания, вызвало к жизни новую идеологию эксплуатации поездов. С целью экономии ресурсов, создания для пассажиров более комфортных условий проезда и повышения конкурентоспособности железнодорожных компаний возникла идея увеличения или уменьшения вагонов в составе поезда в зависимости от пассажиропотока. Такие изменения иногда приходится осуществлять несколько раз в сутки. Это привело к необходимости создания автоматической сцепки, которая не только обеспечивает надежную механическую связь подвижных единиц, но и соединение электрических цепей управления и пневматических тормозных магистралей, что позволяет с меньшими затратами ручного труда осуществлять формирование поездов. В первые десятилетия XX в. было предложено несколько конструкций так называемых «жестких» автоматических сцепных устройств, обеспечивающих соединение электрических и пневматических систем поезда. Одна из удачных конструкций жесткой автоматической сцепки (патент 1904 г.) была предложена немецким инженером К.В. Шарфенбергом (Scharfen- berg) для вагонов Берлинской городской скоростной железной дороги (S-bahn), а после Второй мировой войны на пригородных электропоездах внедрялась в ГДР, ФРГ, Голландии и других странах (рис. 13.59). Подобная конструкция сцепных устройств
Рис. 13.59. Автоматическое сцепное устройство на вагоне пригородной электросекции зарубежного производства (типа устройства Шарфен- берга)
была принята для вагонов на метрополитенах в СССР.
Создание высокоскоростного подвижного состава потребовало новых решений вопроса о сцепных приборах для соединения локомотивов с вагонами и вагонов между собой с учетом условий надежности и безопасности эксплуатации при высокой скорости. При организации высокоскоростного движения во всех странах была принята концепция использования составов постоянного формирования, которые в процессе эксплуатации не требуют переформирования и используются на протяжении всего срока службы в том виде, в котором были выпущены заводами. Это, на первый взгляд, несколько упростило требования к сцепным межвагонным устройствам, поскольку в повседневной эксплуатации не требовалось часто соединять и разъединять вагоны высокоскоростных поездов, а производить эти работы только при ремонте в депо. Однако повышенные требования к сцепным устройствам высокоскоростных поездов диктовались требованиями надежности, безопасности, увеличенными динамическими нагрузками при высокой скорости движения.
В Японии и других странах для соединения между собой вагонов высокоскоростных поездов стали использовать конструкции, в частности типа Сибата (Shibata), созданные на основе технической идеи жесткой автоматической сцепки Шарфенбер- га (рис. 13.60'). Автосцепка облегченного типа такой же разновидности устанавливалась на промежуточных вагонах первого советского скоростного поезда ЭР200. На лобовых стенках концевых вагонов этого поезда устанавливалась серийная отечественная автосцепка СА-3 (позже СА-ЗМ).
На зарубежных высокоскоростных поездах — на головных вагонах или локомотивах, используемых для производства маневровой работы или передвижения высокоскоростного поезда в чрезвычайных ситуациях вспомогательным локомотивом (другим поездом), устанавливались сцепные приборы,
Рис. 13.60. Жесткая автосцепка вагонов японских высокоскоростных поездов (разновидность сцепки Шарфенберга)
совместимые с теми, что используются на обычном подвижном составе. Как правило, на головных вагонах или локомотивах эти сцепные устройства постоянно закрыты кожухами-обтекателями и для доступа к автосцепке требуется их демонтаж.
В 90-е годы прошлого века вначале в Японии, а затем и в ряде европейских стран (Франции, Германии и др.), началась реализация идеи использования в разные часы суток в зависимости от пассажиропотока одинарных или двойных составов высокоскоростных поездов. Для этого в случае необходимости осуществляется быстрое объединение или разъединение двух поездов. В некоторых странах появились так называемые «У-образные маршруты». На них два поезда, сцепленные вместе, выходят с какой-то большой станции, вместе доходят до станции, где маршрут разветвляется. Здесь прямо на пути у пассажирской платформы происходит разъединение двух поездов, далее каждый из них продолжает одиночным порядком следование по своему маршруту.
Для обеспечения такого маневра на головных вагонах (локомотивах) высокоскоростных поездов также устанавливаются автосцепки типа устройства Шарфенберга, которые позволяют машинистам двух поездов без привлечения дополнительных работников производить сцепку или расцепку состава. При сближении двух поездов для объединения в один состав раскрывают элементы
Рис. 13.62. Вид сцепного устройства поезда серии ЕЗ с открытым обтекателем. Япония 2001 г.
Рис. 13.61. Головной вагон высокоскоростного поезда серии ЕЗ в положении с закрытым обтекателем сцепного устройства. Япония. 2001 г. |
13.5. Подвижной состав с устройствами для наклона кузова
На существующих железнодорожных линиях возможности повышения скорости движения в кривых ограничены действием на вагон и пассажиров повышенного поперечного (центробежного) ускорения, которое возрастает пропорционально квадрату скорости и убывает пропорционально радиусу кривой. Центробежное ускорение вызывает силу, прижимающую вагон к наружному рельсу, превышение некоторой величины которой вызывает опасность схода подвижного состава с рельсов. Пассажиры также испытывают действие центробежной силы, направленной от центра кривой и стремящейся отбросить их к боковой стенке вагона, что создает дискомфорт при езде. Максимально допустимое поперечное ускорение для экипажа определяется усилиями, действующими на путь, и значительно превосходит то, которое без ощущения дискомфорта переносит человек.
Частично действие центробежного ускорения в кривых снижается за счет устройства пути с возвышением наружного рельса (рис. 13.63}. При этом некоторая доля
Рис. 13.63. Компенсация поперечного ускорения за счет возвышения наружного рельса в кривых: анп — непогашенное поперечное ускорение; ап — поперечное ускорение, скомпенсированное за счет возвышения наружного рельса; ац — центробежное ускорение; а7 — доля поперечного ускорения, воспринимаемая пассажиром как вертикальное; Мд — сила тяжести; и — возвышение наружного рельса |
При невозможности реконструкции пути с целью уменьшения участков кривых или увеличения их радиуса выходом из сложившейся ситуации является применение вагонов с устройствами для наклона кузова (ВНК). При их использовании некоторая доля центробежного ускорения ощущается пассажирами как вертикальное ускорение, что улучшает комфортность езды. Однако система наклона кузова не должна компенсировать центробежную силу полностью, иначе у пассажиров может возникнуть ощущение болезни движения (укачивания, морской болезни), которое появляется в случае недостатка бокового ускорения при следовании в кривой.
Рассмотрим проблему воздействия центробежного ускорения на пассажира с формальной точки зрения. Скорость поезда в кривой v зависит от возвышения и наружного рельса и недостатка возвышения, допустимая величина которого определяется уровнем комфорта пассажиров. В нормах Международного союза железных дорог (МСЖД) на строительство и эксплуатацию железных дорог допустимая скорость в кривых определяется по формуле:
|
км/ч. |
где г — радиус кривой, м.
Во время включения системы наклона верхняя часть кузова наклоняется к центру кривой, что по воздействию на пассажира равносильно дополнительному возвышению наружного рельса (рис. 13.64). Это кажущееся возвышение t/H= 2stgy (где 2s — расстояние между кругами катания колес, у — угол наклона кузова относительно плоскости рельсов) позволяет увеличить скорость движения поезда в кривой:
и+иГ+и
fн „ ,
При движении с такой скоростью в вагоне, не оборудованном устройством наклона кузова, возникает критическое значение поперечного ускорения (1,6 м/с2); в ВНК ускорение снижается до 0,5 м/с2. Как уже отмечалось выше, чтобы избежать приступа морской болезни пассажиры должны испытывать некоторое поперечное ускорение. При расчетах принимается достаточным, чтобы кажущееся возвышение, возникающее при наклоне кузова, составляло две трети от недостатка возвышения наружного рельса иИ = 2/3 iy.
Исследования показали, что за счет применения системы наклона кузова скорость движения в кривых может быть увеличена приблизительно на 25 %. При этом время в пути, в зависимости от плана и профиля линии, снижается на 10—20 %.
13.6.
2s |

Рис. 13.64. Компенсация центробежного ускорения, действующего на пассажира, за счет наклона кузова вагона: а — движение по прямой; б — движение в кривых; и — возвышение наружного рельса; а — угол возвышения; иИ — добавочное возвышение за счет наклона кузова; у —угол наклона плоскости пола вагона |
Различают две основные системы наклона кузовов вагонов в кривых: пассивную и активную.
В пассивных системах наклона конструкция подвешивания экипажа аналогична маятнику: воображаемая точка подвеса кузова расположена выше его центра масс, например, в вагонах типа Talgo она поднята примерно на 2 м над уровнем пола, т.е. находится на 2,3—3,4 м выше уровня головки рельса. При движении в кривой центр масс под действием центробежной силы смещается наружу, обеспечивая необходимый наклон кузова. В такой системе угол наклона кузова определяется собственной частотой колебаний воображаемого маятника и параметрами участка пути и может достигать 3—5°. При этом компенсируется около 40 % центробежной силы, а скорость в кривых с возвышением наружного рельса 150 мм повышается примерно на 14 %.
Активные системы наклона применяют в кузовах, поворот которых производится принудительно вокруг точки, почти совпадающей с центром масс вагона (в большинстве конструкций вагонов с такой системой она находится примерно на 0,4 м выше уровня пола и на 1,3—1,9 м выше уровня головки рельса). При входе в кривую специальные датчики включают систему управления приводом наклона кузова вагона; устройство может быть электрическим, пневматическим или гидравлическим. Обеспечивается угол наклона кузова до 10°, что позволяет компенсировать поперечное ускорение различного уровня и повысить на 25 % скорость движения в кривых с возвышением наружного рельса 150 мм. Автоматическая система управления приводами для большей надежности и безопасности дублируется.
В настоящее время более чем в 15 странах мира эксплуатируется или находится в процессе внедрения подвижной состав с ВПК. Число типов механизмов, обеспечивающих наклон кузовов вагонов в кривых, растет почти пропорционально рынку таких перевозок.
Идея создания вагонов с наклоном кузовов в кривых была высказана еще в начале XX столетия, в частности немецким ин
женером Ф. Крукенбергом. Одна из первых конструкций вагонов с пассивной системой наклона кузовов были разработана в США в 1938 г. для железных дорог Ачисон, Топика и Санта-Фе. Кузова этих вагонов опи- сплавов, опирающиеся на две концевые независимые двухосные тележки (колесная база 2,73 м) и центральную промежуточную двухосную тележку (база — 3,68 м). Испытания этого вагона показали хорошие
рались на высокие пружинные опоры, установленные на рамах тележек, так, что центр масс вагонов находился ниже точек опоры. В результате при проходе кривых верхняя часть кузова наклонялась внутрь. Вагоны представляли собой два кузова обтекаемой формы, выполненные из легких |
результаты, но относительная сложность конструкции тележек, устройства подвешивания и кузовов не способствовала широкому распространению.
Современные системы наклона кузова вагона различных поездов имеют конструкционные особенности.
Пассивная система наклона кузова вагонов японских электропоездов серии 381 была первой, успешно введенной на серийно выпускаемых поездах, находящихся в коммерческой эксплуатации (с 1973 г.) {рис. 13.65). В этих поездах система наклона кузова вагона включает надрессорную балку тележки с установленными на ней опорными роликами, по которым может перекатываться нижняя закругленная балка кузова. При проходе поездом кривой кузов под воздействием центробежных сил по-
Рис. 13.65. Электропоезд серии 381; схема устройства наклона кузова: Цд — центр вращения; — центр масс. Япония. 2010 г. |
ворачивается вокруг центра вращения (Цв), поскольку центр масс вагона (Цм) находится ниже.
Пассивная система наклона кузова вагона фирмы Patentes Talgo(Испания) также, как и конструкция вагонов японского электропоезда серии 381, не требует для функционирования дополнительного источника энергии.
В начале 40-х годов XX в. была предложена и воплощена в жизнь интересная техническая идея, положившая начало особому направлению в конструировании скоростного, а в последующем и высокоскоростного подвижного состава, — созданию поездов из легких сочлененных вагонов. Речь идет о поездах Talgo[XVIII]. Техническая идея вагонов типа Talgo обозначена в самом названии: «сочлененные легкие вагоны» (патент 1942 г.) — относительно короткие по длине, с одной осью, расположенной на заднем (по ходу движения) конце вагона (уменьшена масса). Передней частью каждый вагон опирается на предыдущий, первый вагон опирается на локомотив (рис. 13.66,13.67).
Вагоны опираются на разрезные оси с независимой подвеской и вращением колес в колесной паре. Благодаря этому удалось существенно опустить центр тяжести и уменьшить высоту вагона. Высота пола в пассажирских салонах составляет всего 365 мм от уровня головки рельса, в то время как в обычных пассажирских вагонах — около 1000 мм. Места сочленения вагонов закрываются гибкой обшивкой.
Такой «змееобразный» поезд из коротких вагонов с низким центром тяжести и небольшими по высоте кузовами, хорошо вписывался в кривые малого радиуса, проходя их со скоростью до 160 км/ч (рис. 13.68).
Рис. 13.66. Поезд Talgo I (вагоны без наклона кузова) 1944 г.
Кроме того, вагоны с одной осью, расположенной в хвостовой части по ходу движения поезда, обеспечивают высокую безопасность при проходе кривых, поскольку гребень наружного колеса имеет отрицательный угол по отношению к рельсу и это снижает возможность схода с рельсов при «набегании» колеса на наружный рельс. Естественно, что внутреннее колесо в этом случае имеет более благоприятную позицию для «набегания» на рельс, но вероятность этого уменьшается с увеличением скорости. Несимметричная конструкция вагонов имеет недостаток, так как поезд может двигаться только в одном направлении. В конечном пункте маршрута поезд должен осуществлять оборот на участке пути в виде петли. Этот недостаток был устранен в последующих модификациях вагонов.
Позже идея вагонов была дополнена системой пассивного маятникового наклона в поездах Talgo Pendular (от исп.: Pendular — маятник) (рис. 13.68, 13.69). Ее достоинства — экономичность и высокая надежность. Пассивный наклон кузова при прохождении кривых достигается тем, что пневматические рессоры, на которые он опирается, подняты в верхнюю часть вагона и плоскость подвеса находится значительно выше центра масс (см. рис. 13.68). Благодаря такому расположению пневморессор кузов вагона фактически представляет собой маятник. При следовании ва-
а б |

Рис. 13.67. Поезда Talgo (вагоны с наклоном кузова): а — первый поезд Talgo //. 1950 г. Испания; б — установка гибкой обшивки межвагонного перехода: видны элементы первичного подвешивания вагона (50-е годы XX в.); в — концевой и промежуточные вагоны поезда Talgo III. 60-е годы XX в. Испания |
Маятниковая система наклона кузова вагона Talgo Pendular реализуется благодаря особой конструкции одноосных тележек (см. рис. 13.67, 13.68). Система Talgo Pendular обеспечивает оптимальный угол наклона кузова (до 3,5°) с учетом скорости движения и характера пути. Поезда Talgo при ускорении в плоскости рельсов, равном 1,6 м/с2, могут развивать скорость на 19 % большую, чем поезда с обычными вагонами. При одинаковой скорости движения использование устройств ВНК уменьшает непогашенное ускорение, действующее на пассажиров, примерно на 75 %. Недостатком пассивных систем является запаздывание наклона кузова при входе вагона в кривые.
Активные системы наклона кузова на 20—25 % эффективней пассивных, поэтому они получили более широкое распространение.
Активную систему наклона кузова вагона в кривых начали разрабатывать в 70-х годах XX столетия, независимо друг от друга, конструкторы Великобритании, Италии, Швеции, Франции, Японии.
Одной из первых реализованных активных систем была конструкция опытного британского поезда APT[XIX](см. рис. 13.70), который создавался в 1962—1985 гг. Вагоны поезда имели механизм принудительного наклона кузова в кривых. Предполагалось, что на существующих линиях поезд сможет обеспечить движение со скоростью до 250 км/ч.
чО 00 |
Плоскость пути |
_______ Центробежное _ускорение Ускорение |
Центр |
Плоскость пола вагона |
Плоскость пути |
I в Горизонтальная |
плоскость |
Горизонтальная |
Рис. 13.68. Схема пассивной системы наклона кузова вагона Talgo: а — схематическое изображение обыкновенного вагона; б — вагон Talgo Pendular: 1 — рама одноосной тележки; 2 — колонны, на которые опирается кузов; 3 — резиновые баллоны пневматического подвешивания (положение кузовов вагонов показано в момент движения по кривой)
Рис. 13.69. Вид на торцевую стенку вагона поезда Talgo Pendular в расцепленном состоянии: 1 — рама одноосной тележка вагона (с независимыми «полуосями» для каждого колеса); 2 — колесо; 3 —узел буксы и механизма перемены колеи; 4 — нижний межвагонный гидравлический гаситель колебания; 5 — верхний межвагонный гидравлический гаситель колебания; 6 — баллон пневмоподвески («подушка») в спущенном состоянии; 7 — опорная колонна; 8 — межвагонный переход; 9 — площадка и дверь межвагонного перехода; 10 — элемент межвагонного сцепного устройства |
В конструкции вагона поезда APT изогнутая люлечная балка подвешена к поперечной балке тележки через угловые качающиеся подвески, а гидравлические цилиндры наклона смещают ее в поперечном направлении вместе с кузовом. Пневматические рессоры второй ступени подвешивания расположены между люлечной балкой и кузовом, что позволяет им работать независимо от наклона кузова.
Команду на наклон кузова подает компьютер, получающий величины исходных боковых ускорений от датчиков, находящихся на уровне пола и потолка вагонов. Максимальная величина отклонения кузова от вертикали в ту или другую сторону с помощью гидроцилиндров составляла 9°, еще 3° отклонения могли добавить газовые пружины за счет изменения в них давления азота.
Несмотря на успехи в реализации отдельных компонентов системы и постройки нескольких опытных поездов на газотурбинной и электрической тяге, программа создания поезда APT в целом не была реализована. Отдельные разработки, сделанные
Рис. 13.70. Опытный высокоскоростной поезд АРТ-Е. Великобритания. 1974 г.: а — головной вагон; б — схема механизма наклона кузова: 1 — габарит подвижного состава; 2 — угол наклона; 3 — центр вращения; 4 — баллон пневматической рессоры; 5 — рама тележки; 6 — гидроцилиндры наклона; 7 — поперечная балка тележки; 8 —угол наклона плоскости пути |
В 1972 г. фирма Fiat Ferroviaria[XX](Италия) провела успешные опыты с электровагоном, оборудованным электрогидравличес- кой системой наклона кузова, которая в 1975 г. была использована в прототипе поездов с ВНК, получившем наименование Pendolino 401 (рис. 13.71).
Устройство наклона кузова, опробованное в вагонах поезда Pendolino 401, было использовано в серийном поезде Pendolino 450 (1989 г.) (рис. 13.72). В конструкции изогнутая U-образная надрессорная балка тележки 4 (на рис. 13.73 выделена желтым цветом) опирается на винтовые пружины второй ступени подвешивания 9, а кузов вагона подвешивается к ней на качающихся подвесках (серьгах) 3. Длинноходовые гидравлические цилиндры наклона кузова 5 установлены вертикально, их нижние концы закреплены на надрессорной балке, а верхние прикреплены к кузову вагона на уровне крыши. При выдвижении штоков цилиндров с одной стороны и втягивании с другой кузов поворачивается относительно продольной оси.
Такое устройство использовалось и на подвижном составе других типов с системой наклона кузовов по типу Pendolino, например в дизель-поезде VT610 железных дорог Германии (рис. 13.74). Недостатком системы являлась необходимость устройства в тамбурах вагонов почти на всю высоту кузова специальных отсеков для размещения гидроцилиндров наклона, что сокращало полезную площадь тамбуров. В электропоездах ETR 460/470, ETR 480 второго поколения гидравлические цилиндры уже размещены под полом кузова вагона на тележках.
Рассмотрим конструкцию тележек поездов Pendolino последних серий, включая
Рис. 13.72. Поезд Pendolino 450 на прямом участке линии. Италия. 1989 г.
Рис. 13.73. Поезд Pendolino 450 с активной системой наклона кузова вагона: 1 — колесная пара; 2 — рама тележки; 3 —качающиеся подвески (серьги); 4 — U-образная надрессорная балка тележки; 5 — длинноходовые гидравлические цилиндры; 6 — контур сечения кузова вагона при наклоне влево (соответствует положению качающихся подвесок на рисунке); 7 — контур сечения кузова вагона при наклоне вправо; 8 — контур сечения кузова вагона при среднем положении; 9 — пружины центрального подвешивания. Италия. 1989 г. |
механизм наклона кузова, на примере поезда ETR 460/470 (рис. 13.75). Устройство тягового привода высокоскоростных поездов и конкретные примеры их исполнения будут рассмотрены в 14 главе, однако для понимания устройства тележек вагонов поездов Pendolino, несколько забегая вперед, необходимо сделать следующее пояснение. На поездах этого типа каждый моторный вагон имеет по два асинхронных тяговых электродвигателя, подвешенных к кузову вагона (рис. 13.76). Вращающий момент от двигателя передается к движущей оси карданным валом и коническим редуктором, расположенным на оси на внутренней колесной пары тележки моторного вагона. Таким образом, каждый моторный вагон имеет две движущие оси.
Тележки вагонов поезда ETR 460/470 (рис. 13.77) оснащены поводковыми буксами 14, первичное подвешивание выполнено на цилиндрических пружинах 16. В буксовых узлах расположены эластичные элементы, позволяющие колесным парам устанавливаться по радиусу кривых, что снижает сопротивление движению, износ
Рис. 13.74. Дизель-поезд железных дорог ФРГ серии VT610 с вагонами ВНК. 1990 г. |
Рис. 13.75. Поезд Pendolino ЕТР 460/470. Италия. 2000 г. |
Рис. 13.76. Схема тягового привода моторных вагонов поездов Pendolino: 1 — осевой редуктор; 2 — карданный вал; 3 — кузов вагона; 4 — тяговый электродвигатель (узел крепления двигателя на схеме не показан) |
колесных пар и рельсов, повышает плавность хода и уменьшает механический шум от качения колес по рельсам.
Тележки имеют рамы Н-образной формы без оконечных балок, выполненные в виде сварной конструкции 5 из листовой стали. Боковые элементы рамы соединены между собой трубчатыми балками 8, к которым через шарниры прикреплены тяги лемни- скатного механизма[XXI]9. Такой механизм является жестким (передаетусилия, возникающие при тяге или торможении) вдоль вагона (вдоль оси пути), но не препятствует
Рис. 13.77 (начало). Тележка поезда Pendolino ETR460 (Fiat Ferrovia): а — общий вид; б, в —упрощенные схемы, показывающие механизм наклона и горизонтального поворота кузова; г, д, е — компоненты сборочного чертежа; 1 — нижний поводок; 2 — поддерживающая колесная пара; 3 — тормозные диски; 4 —ось поддерживающей колесной пары; 5 — рама тележки; 6 — тормозной механизм пневматического фрикционного тормоза; 7 — опоры пружин вторичной системы подвешивания; 8 — поперечная трубчатая балка рамы тележки; 9 — лемнискатный механизм передачи усилий от тележки к кузову и наоборот, возникающих при тяге или торможении; 10 — тормозная балка; 11 — тормозной цилиндр; 12 — редуктор на оси ведущей колесной пары; 13 — карданный вал; 14 — верхние поводки; 15 — букса: 16 — пружины первичной ступени подвешивания; 17 — гидравлические амортизаторы первичной ступени подвешивания; 18 — поперечный гидравлический гаситель колебания кузова; 19 — шкворень; 20 — воздушные цилиндры механизма активной стабилизации кузова; 21 — комплект пружин вторичной ступени в собранном виде (21а, 216, 21в) — элементы комплекта пружин; 22 — надрессорная балка; 23 — вертикальный гидравлический гаситель колебаний центральной ступени подвешивания; 24 — серьги (подвески) подвешивания поперечной балки кузова; 25 — гидроцилиндры механизма наклона кузова; 26 — гидравлические гасители колебаний виляния; 27 — кузов; 28 — поперечная балка кузова
г
Рис. 13.77 (окончание)
перемещению кузова относительно тележки поперек пути.
Вторичное подвешивание выполнено на комплектах цилиндрических пружин «Fle- xicoil» 21 и 24, поддерживающих надрессорную балку 22. К этой балке на четырех серьгах 25 подвешена поперечная балка кузова 28, который способен наклоняться в обе стороны с помощью гидравлических цилиндров 26. На тележках установлены пневматические цилиндры 20, штоки которых соединены с надрессорной балкой и могут смещать ее и кузов относительно тележек в горизонтальной плоскости.
С помощью электронных управляющих устройств обеспечивается центрирование кузова вагона по отношению к тележке пневматическими цилиндрами 20 и наклон его верхней части внутрь кривой с помощью гидравлических цилиндров. Величину угла наклона и горизонтального смещения задает центральный процессор, который, исходя из показаний акселерометров, гироскопов и тахометров (находящихся на нескольких тележках поезда), вычисляет скорость движения и непогашенное ускорение. Процессоры, расположенные в вагонах, в свою очередь, управляют наклоном каждого кузова, что осуществляется при выполнении следующих условий:
— обнаружения места перехода прямого участка в кривую и вновь в прямую и определение радиуса кривой;
— скорости движения более 70 км/ч;
— недостатка возвышения наружного рельса, которое постепенно увеличивается;
— некомпенсированного ускорения выше минимально допустимого.
Рис. 13.78. Поезд Pendolino ETR600 (ETR610). Alstom. Выставка «Innotrans». Берлин. 2008 г. |
Рис. 13.79. Поезд Sm6 «Аллегро» на линии Санкт-Петербург — Хельсинки. 2011 г. |
Активная система наклона кузова фирмы ADtranz[XXII]используется на поезде X 2000, близка по конструкции к системе Pendolino, но имеет некоторые особенности (рис. 13.80, 13.81). Поезд Х2000 формируется из электровоза и пяти или шести прицепных вагонов, концевой из которых имеет кабину управления. Поезд может двигаться вперед с максимальной скоростью 200 км/ч, как локомотивом, так и вагонами, при этом управление ведется из кабины концевого вагона. Кузов электровоза в поездах X 2000 не наклоняется. Механизмы наклона кузовов вагонов управляются с помощью датчика бокового ускорения, смонтированного на первой тележке. Компьютер, по данным о скорости движения, вычисляет угол, на который необходимо наклонить кузов каждого вагона. Наибольший угол наклона составляет 6,5°, а максимальная скорость наклона — 4 град/с.
В новейших разработках японских поездов линии Синкансэн, в частности серии 700, N700, Е5, Е6 (рис. 13.82) применены устройства центрального пневматического подвешивания, выполняющие также и функцию наклона кузова вагона в кривых, впрочем, на небольшую величину — около 1,5— 3°. Однако на линиях «Токайдо—Синкансэн» и Санъё, построенных в 1960—70-е годы и имеющих максимальные радиусы кривых порядка 2500 м, использование поездов
Рис. 13.81. Тележка вагона поезда Х2000. Швеция. 1999 г.
Рис. 13.80. Высокоскоростной поезд Х2000 (Х2): а — общий вид поезда со стороны концевого вагона с кабиной управления, проходящего кривую с наклоном кузовов вагонов; б — схема устройства наклона кузова вагона: 1 — колесная пара; 2 — рама тележки; 3 — пневматические рессоры центрального подвешивания; 4 — кузов вагона; 5 — качающаяся балка (опора пневматических рессор); 6 — гидроцилиндры наклона кузова; 7 — качающиеся подвески. Швеция. 1989 г. |
Особой проблемой при проектировании электропоездов с наклоняемыми кузовами вагонов является размещение токоприемника, который, несмотря на наклон кузова в кривых, должен постоянно находиться над осью пути в вертикальном положении, чтобы не нарушался контакт между полозом и проводом. Кроме того, требуется сохранять вписывание токоприемника в габарит подвижного состава.
У поездов Pendolino токоприемники на крыше помещены на салазки, которые связаны тягами с рамой тележки, что обеспечивает устойчивое центрированное положение токоприемника при наклоне кузова. Тяги соединены с тележкой посредством демпферов, что смягчает вибрации, получаемые от пути через тележку [рис. 13.83).
Применение подвижного состава с ВПК дает положительный результат. Время в пути поездов с ВНК по сравнению с обычными уменьшается примерно на 10—20 %. При этом удорожание подвижного состава со-
1 - 2 т 2 — 1 |
Рис. 13.82. Высокоскоростной поезд серии N700: а — общий вид; б — схема устройства механизма наклона кузова вагона: 1 — компьютер головного вагона — компонент цифровой автоматической системы управления движением поезда; 2 — компьютеры всех вагонов, входящие в систему управления поездом; 3 — устройство управления пневматическими рессорами центрального подвешивания вагона; 4 — пневматические рессоры центрального подвешивания; 5 — рама тележки. Япония. 2007 г.
б |
Рис. 13.83. Схема устройства коррекции положения токоприемника поезда Pendolino: а — положение кузова вагона на прямом участке пути; б — положение в кривой ставляет 5—10 %. При эксплуатации ВНК заметно снижение энергозатрат на тягу поезда, так как скорость движения становится более равномерной и нет торможений и разгонов при входе и выходе из кривой.
Вместе с тем отмечается ряд недостатков:
— для эксплуатации таких поездов необходимо повышенное качество содержания пути, особенно в кривых;
— на горных линиях с малыми радиусами кривых выигрыш во времени оказывается незначительным;
— большие центробежные силы приводят к появлению значительных механических напряжений в конструкции и быстрому износу пути и ходовой части подвижного состава;
— более сложная конструкция подвижного состава, помимо увеличения его цены, о чем говорилось выше, влечет за собой и удорожание технического обслуживания, что особенно отмечается в странах с суровыми зимним условиями эксплуатации (обилием снега и продолжительным периодом отрицательных температур).
Кроме того, применение поездов с наклоном кузовов вагонов в кривых создает дополнительные проблемы, связанные с обеспечением безопасности движения, поскольку задание предельной скорости в кривых устройствами перегонной автоматики должно осуществляться раздельно для поездов с ВНК и без них. В этой связи ведется разработка специализированной системы безопасности на линиях, где эксплуатируются высокоскоростные ВНК. Таким образом, для принятия решения в пользу использования тех или иных поездов необходимо технико-экономическое обоснование для каждой линии с учетом ее профиля, наличия смешанного движения (скоростных и обычных поездов), рынка транспортных услуг, включая возможную конкуренцию с другими видами транспорта.
13.7. Конструктивные особенности подвижного состава с устройствами, обеспечивающими эксплуатацию на железных дорогах с разной шириной колеи
В главе 7 рассматривались проблемы взаимодействия ВСМ, имеющих разную ширину колеи. В мире уже на протяжении более ста лет разрабатывается подвижной состав, способный переходить с одной железнодорожной колеи на другую. Эти работы начались задолго до создания специализированных ВСМ. Речь идет о странах, где соседствовали или стыковались железнодорожные линии разной колеи, например, в США, Российской империи, Испании. С помощью универсального подвижного состава пытались организовать по путям разной колеи беспересадочное сообщение для пассажиров или перевозку товаров без перегрузки. Для перехода подвижного состава с одной колеи на другую использовалась перестановка тележек или специальные конструкции осей колесных пар.
К настоящему времени в разных странах предложено несколько десятков конструкций ходовой части железнодорожного подвижного состава, пригодного для перехода с одной колеи на другую с помощь специальных устройств, изменяющих расстояние между колесами на оси колесной пары, несколько из этих конструкций уже находятся в коммерческой эксплуатации или близки к ней (табл. 13.5). В XX столетии Испания, имеющая более широкую колею (1668 мм), чем большинство других европейских стран испытывала трудности при организации прямых железнодорожных сообщений со странами западной и центральной Европы. В Испании в коммерческой эксплуатации находятся две системы: компании Talgo (с 1969 г.) и CAF (Construcciones у Auxiliar de Ferrocarriles, с 2003 г.), в Польше с 2000 г. используются раздвижные колесные пары типа SUM 2000, выпускаемые предприятием ZNTK Poznan; оригинальные конструкции колесных пар с изменяемым расстоянием между колесами
Таблица 13.5
Дата добавления: 2019-11-16; просмотров: 1624; Мы поможем в написании вашей работы! |
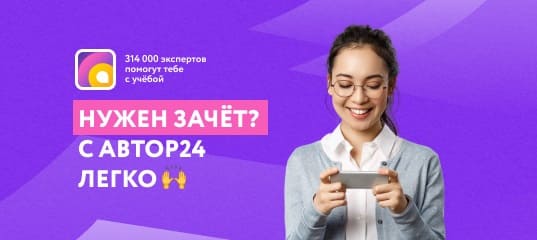
Мы поможем в написании ваших работ!