Конструирование паянных соединений.
При пайке деталей приборов места соединений нагревают до температуры плавления припоя, которая должна быть ниже температуры плавления соединяемых материалов. Расплавленный припой при этом растекается по нагретым поверхностям стыка деталей, образуя при охлаждении паяный шов, диффузионно и химически связанный с материалом деталей. Пайка позволяет соединять детали не только из однородных, но и из разнородных материалов. Пайкой соединяются, например, стали со сплавами цветных металлов; металлы с графитом, ферритом, фарфором; керамика с полупроводниками; пластмасса, резина и т. и. Кроме того, можно
паять детали с тонкостенными элементами, где применение сварки недопустимо из—за опасности прожога. Пайкой можно изготавливать за один производственный цикл сложные по конфигурации узлы и целые конструкции. Это позволяет рассматривать пайку как групповой метод соединения деталей.
В плоских паяных конструкциях встречаются соединения внахлестку (рис. 21.5, а), встык (Рис- 21.5, б) и др. Нахлёсточные соединения наиболее распространены, так как позволяют изменением величины нахлестки достигать равнопрочности паяного соединения.
Зазор между деталями при пайке зависит от вида припоя и паяемых материалов и в значительной мере определяет прочность соединения. Уменьшение зазора до некоторого предела увеличивает прочность. При малых зазорах диффузионный процесс и процесс растворения материалов деталей и припоя может распространяться на всю толщину паяного шва, а диффузионный слой и слой раствора - прочнее самого припоя.
|
|
Необходимость малых и равномерно распределенных зазоров является одним из недостатков пайки, ограничивающих ее применение. По этой же причине перед пайкой требуется более точная по сравнению со сваркой механическая обработка и сборка деталей. В качестве припоев используются многие металлы и сплавы. Одной из важнейших характеристик припоя, определяющей назначение и способ его применения, является температура плавления Тпл. По этому признаку припои разделяются на высокотемпературные с Тпл> 450°С и низкотемпературным – на основе олова и свинца.
Для уменьшения вредного влияния окисления поверхностей деталей применяются специальные флюсы, которые не только защищают, но и растворяют окисные пленки, повышая текучесть припоя. Флюсы в зависимости от температурного интервала активности разделяются на низкотемпературные с Тпл меньше или равно 450°С(канифольные, кислотные, фтороборатные и т.д.) и высокотемпературные в Тпл больше 450°С (боридные, боридно-углекислые и др.).
Конструирование клеевых соединений.
|
|
Благодаря созданию высококачественных клеев на основе полимеров соединению склеиванием подвергаются практически все промышленные материалы (стали, сплавы, серебро, медь, пластики, дерево и др.).
В конструкциях приборов с помощью склеивания изготавливают агрегаты оперения (рули направления и высоты, триммеры, стабилизаторы), агрегаты механизации крыла (панели хвостовой части, предкрылки, закрылки, дефлекторы, тормозные щитки, элероны‚ спойлеры), агрегаты фюзеляжа (люки и лючки, панели пола), агрегаты установки двигателя (капоты, панели пилонов, воздухозаборные каналы), агрегаты несущих
и хвостовых лопастей вертолетов и др.
Клеевые соединения по сравнению с заклепочными, сварными и паяными имеют ряд преимуществ: возможность соединения деталей из разнородных материалов, в том числе из тонколистовых, не поддающихся сварке и пайке; равномерное распределение напряжений по всей склеиваемой поверхности и, как следствие, снижение концентрации напряжений и повышение выносливости клеевого соединения; высокую коррозионную стойкость; герметичность; низкую себестоимость.
Основные недостатки клеевых соединений: старение со временем; ограниченный диапазон рабочей температуры (от -60 до 300 °С); малая прочность при неравномерном отрыве (отдире); необходимость сложной оснастки для изготовления сложнопрофильных конструкций и точной пригонки склеиваемых поверхностей; трудность контроля качества склейки.
|
|
На рис. 21.6 представлены наиболее распространенные типы клеевых соединений в приборах: нахлесточные (а), врезные и стыковые по косому срезу, позволяющие получать гладкие внешнюю и внутреннюю поверхности (б), с накладками (в).
Для повышения прочности соединения внахлестку выполняют так, чтобы плоскость клеевого слоя находилась в плоскости воспринимаемых им нагрузок, а само соединение работало на сдвиг. Для уменьшения напряжений отрыва, возникающих по краям плоскости склеивания, соединяют детали со скошенными на ус концами нахлестки (рис.21.6, а). Прочность такого соединения в 1,5…2 раза больше, чем прочность соединения с прямыми концами при прочих равных условиях.
Прочность клеевых соединений зависит от толщины слоя клея. Рекомендуемая толщина составляет 0,05…0,15 мм и зависит от вязкости клея и давления при склеивании. Существует большое разнообразие клеев. Находят широкое применение клеи на основе органических полимерных смол: фенольно-каучуковые клеи ВК-25, ВК-32-200, ВК-3, эпоксидные ВК-40, ВК-27, ВК-9, полиуретановые ПУ-2 и т.д. Эти клеи применяют для склеивания деталей, работающих при температурах не выше 200°С. Выбор марки клея определяется техническими требованиями, предъявляемыми к клеевым конструкциям.
|
|
Клеевые соединения хорошо работают при сдвиге и равномерном отрыве, плохо – при неравномерном отрыве. В таких случаях для обеспечения надежности предусматривают дополнительное механическое крепление соединяемых деталей клепкой, сваркой, болтами или винтами. Такие соединения называют комбинированными, к ним относятся: клеесварные, клееболтовые. Их применяют для создания особо прочных соединений, хорошо работающих при различных видах нагрузок. Испытания на срез показали, что прочность комбинированных соединений более чем в 2 раза превышает прочность клеевых соединений.
Успешно применяют клеи для стопорения резьбовых соединений, повышения прочности соединения зубчатых колес с валами (например, локайтов-смол, твердеющих при отсутствии воздуха); при установке наружных колец подшипников в корпус.
Дата добавления: 2019-07-17; просмотров: 246; Мы поможем в написании вашей работы! |
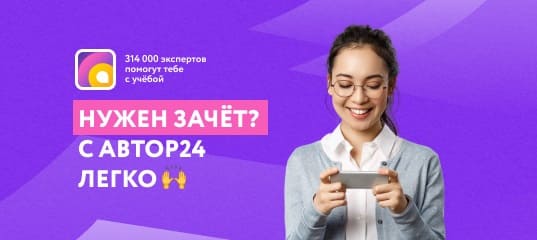
Мы поможем в написании ваших работ!