Производительность оборудования фанерных производств
При выборе оборудования необходимо учитывать следующее. Производительность и коэффициент загрузки оборудования; качество выполняемой операции; уровень автоматизации и механизации работ на нем; перспективность его использования; условия эксплуатации.
Расчетное количество потребного оборудования по отдельным технологическим операциям на заданную программу рассчитывается
Nрасч= , шт, (53)
где Q – количество продукции (полуфабриката) определенного вида на заданную программу; Псм – сменная производительность определенного вида технологического оборудования; m – число рабочих смен в сутки; N – число дней работы оборудования в году.
При этом необходимо следить, в каких размерностях определяется производительность оборудования. Количество продукции определенного вида должно выбираться из расчета расхода сухого шпона и сырья на заданную программу.
Например, производительность лущильного станка в смену определяется в м3 сырого шпона определенной толщины. Количество лущильных станков рассчитывается по расходу сырого шпона этой толщины в м3на годовую программу. Количество рабочих смен в сутки выбирается с учетом организации работ на отдельных участках технологического процесса (непрерывности процессов, сезонного характера работы, условий работы и т.п.)
Число дней работы оборудования в году (фонд времени работы оборудования) определяется с учетом продолжительности рабочей смены, продолжительности планируемого текущего ремонта оборудования, количества календарных рабочих дней в году.
|
|
Коэффициент загрузки фактически принятого оборудования
К3= , (54)
где nрасч. – расчетное количество единиц оборудования; nфакт – фактически принятое количество оборудования.
Фактически принятое количество оборудования получается путем округления nрасч. до ближайшего целого числа.
В отдельных случаях допустима перегрузка оборудования на 5…10 % (К3=1,05…1,10), если при расчете производительности оборудования использованы средние параметры режима обработки, например, скорости подачи, числа оборотов шпинделей, температуры при оклеивании и т. п. Целесообразно при этом сравнить расчетную производительность со средней производительностью оборудования, достигнутой наиболее передовыми промышленными производствами.
Производительность лущильного станка.
В чураках, разлущиваемых за смену
А= , шт/см, (55)
В куб. метрах сырого шпона за смену
Псм=А×Vш.ср., м3/см, (56)
|
|
где Т – продолжительность смены, мин; Тц – продолжительность полного цикла обработки одного чурака, с; К – коэффициент использования рабочего времени (К=0,94…0,95); Vш. ср. – объем сырого шпона (полноформатного и деловых кусков), полученного из одного чурака, м3 (определяется при расчете расхода сырья).
Продолжительность полного цикла обработки одного чурака (Тц) включает следующие затраты:
(57)
где Т1 – продолжительность установки чурака, зависит от диаметра и формы чурака, конструкции станка и центровочно–загрузочного приспособления, с.
Т1=3…6 с.
Т2 – продолжительность зажима чурака шпинделями
Т2= , с, (58)
где hk – глубина внедрения центра кулачка в торец чурака, равна в среднем 30-60 мм; Uн – скорость осевого перемещения наружных шпинделей, мм/с;
Тз – продолжительность подвода суппорта на ускоренной подаче
Тз= , с, (59)
где Lс – путь, проходимый суппортом на ускоренной подаче, мм (30 мм); Uс – скорость ускоренной подачи суппорта, мм/с,(50…100 мм/с);
Тч – продолжительность оцилиндровки чурака
|
|
Т4= , с, (60)
где b – коэффициент формы чурака, определяется по формулам
для березовых чураков
b=0,935+0,165·Lч;
для сосновых и лиственничных чураков
b= 0,885+0,167·Lч;
а – коэффициент оцилиндровки, определяемый по формулам
для березовых чураков
а=0,818+0,067·Lч;
для сосновых и лиственничных чураков
а=0,828+0,067·Lч
Lч – длина чурака, м; Дч – диаметр чурака, мм; nш – число оборотов шпинделей, мин – 1; Sш – толщина шпона, мм; Т5 – продолжительность лущения оцилиндрованного чурака
Т5= с, (61)
где Дк – диаметр карандаша, мм; Т6 – продолжительность отвода суппорта, с
Т6= , с, (62)
Т7 – продолжительность отвода шпинделя
Т7= с, (63)
Uв – скорость осевого перемещения внутреннего шпинделя, мм/с; Т8 – продолжительность удаления карандаша, 2…3 с; Т9 – продолжительность прочистки просвета между ножом и прижимной линейкой, (1…2 с).
В случае лущения шпона разных толщин производительность станка рассчитывается для каждой толщины.
Производительность ножниц для рубки ленты шпона определяется по формуле
Псм=3600Т×Ки×Кр×Vл/t, м3/см, (64)
|
|
где Т – продолжительность смены, ч; Ки – коэффициент использования рабочего времени ножниц (0,93…0,95); Vл – объем одного листа сырого шпона, м3;
Кр – коэффициент продолжительности рубки листов, % от продолжительности полного цикла получения шпона от одного чурака; t – затраты времени на прохождение одного листа шпона через ножницы и отрезку его от ленты (1,5…5 с) или из технической характеристики ножниц.
При отводе шпона от ножниц (без перекладки) Кр=0,6…0,8, при перекладывании шпона вручную со стола ножниц на подстопное место Кр= 0,4…0,6.
Производительность сушилок за смену по сухому шпону
Псм=Т×n×S×b× ×К1×К2×К3, м3/см, (65)
где Т – время работы сушилки за смену, мин; n – число листов шпона по ширине этажа, умноженное на число этажей; S - толщина листа шпона, м; b – ширина листа после сушки, м; L – полная рабочая длина сушилки, м; t1 – время прохождения шпона через сушилку, мин; К1 – коэффициент учета времени при переходе от сушки шпона одного вида к другому и равен 0,9…1; К2 – коэффициент использования времени работы сушилки, К2=0,9…0,95; К3 – коэффициент заполнения шпоном рабочей длины сушилки равен 0,98.
Продолжительность прохождения шпона по всей роликовой сушилки (по зонам сушки и охлаждения) определяется по формуле
t1=t , мин, (66)
где t – продолжительность сушки шпона в сушильной зоне, мин; L – полная рабочая длина сушилки, м; l – длина сушильной зоны, м.
Продолжительность сушки шпона в роликовых сушилках определяется по формуле
t= ×Kn×Kц, мин, (67)
где Wн, Wк – начальная и конечная влажность шпона, %; 30 – влажность шпона, соответствующая переходу от периода постоянной скорости сушки к периоду убывающей скорости; Nр – скорость сушки в период постоянного ее значения %/мин; Кр – коэффициент продолжительности сушки в период убывающей скорости сушки; Kn – коэффициент, учитывающий породу древесины (для березы равен 1; для ольхи – 0,83; для сосны и лиственницы при 0С воздуха свыше 130-0,9; при 0С 110-125 равен 1, ниже 110 0С – 1,2; для липы – 1,25); Кц – коэффициент, учитывающий направление циркуляции воздуха (при продольной циркуляции воздуха Кц=1; при поперечной выбирается в зависимости от средней температуры агента сушки.
Производительность шпонопочиночных станков.
А= , лист/см, (68)
Псм=А×l×b×S, м3/смену, (69)
где Т – время смены, мин; К – коэффициент загрузки станка, К=0,94;
t1 – вспомогательное время на один лист, t1 = 7c; t2- время, затрачиваемое на одну заплатку t2=2,6c; n – среднее количество заплаток на один лист 10…15шт;
l – длина листа шпона, м; b – ширина листа шпона, м; S – толщина листа шпона, м.
Починке подлежит 20…30 % от объема сухого шпона в зависимости от сортности сырья
Qпоч.=Qсух. × , м3, (70)
где m – объем шпона, подлежащего починке, % (20-30).
Производительность гильотинных ножниц
П= , м3/см, (71)
где Lш – длина листа шпона, м; вк – средняя ширина кускового шпона, м (0,3…0,4); hп – высота пачки шпона, м; tц – продолжительность цикла обработки, мин (4…6); Кр – коэффициент рабочего времени (Кр=0,95).
Производительность ребросклеивающих станков.
По способу подачи шпона ребросклеивающие станки делятся на станки с продольной подачей и поперечной. Способ соединения полос шпона может быть различный: ленточный (с применением гуммированной ленты), безленточный (термореактивный клей), клеевая нить, клеи-расплавы.
Производительность станков с продольной подачей
П= , м3/см, (72)
где U – скорость подачи, м/мин; bш - средняя ширина форматного шпона, м;
Sш – толщина шпона, м; Кр – коэффициент рабочего времени (0,95…0,96); Км – коэффициент машинного времени (0,92); вк – средняя ширина кускового шпона, м;
с поперечной подачей
П=480×U×bш×Sш×Кр×Км, м3/см. (73)
При использовании термореактивных клеев для ребросклеивания скорость подачи зависит от состава клея, толщины шпона и температуры нагревателей. При температуре нагревателей 180…2000С рекомендуются следующие режимы ребросклеивания.
Основной технологической операцией производства фанеры является склеивание. Наиболее распространен горячий способ склеивания фанеры в многоэтажных клеильных прессах.
В зависимости от организации производства сборку пакетов, холодную подпрессовку их и склеивание могут производить на поточных (механизированных или полуавтоматических) линиях сборки-подпрессовки-склеивания. Производительность такой линии определяется производительностью клеильного пресса, но при этом необходимо учитывать производительность участков сборки пакетов, холодной подпрессовки, которые не должны сдерживать работу клеильного пресса.
Значительно реже эти три операции выполняются на отдельных участках.
Производительность клеильных прессов.
Псм= , м3/см, (74)
где Т – продолжительность смены, мин; n – число этажей пресса; m – число единичных пакетов, загружаемых в один промежуток пресса; Sф – толщина фанеры (или другой клееной продукции), мм; Fо – площадь листа обрезной фанеры, м2; t – продолжительность цикла прессования, мин; К – коэффициент использования рабочего времени (0,94).
Продолжительность цикла прессования фанеры складывается из суммы трех слагаемых
t=tn+tс.д.+tb , мин, (75)
где tn,, tс.д. и tb – продолжительности соответствию пьезотермообработки (прессования), снятия давления и вспомогательных операций, мин.
После охлаждения фанера подвергается обрезке. В настоящее время для обрезки фанеры наиболее распространены 4-хпильные (или 2-х пильные спаренные станки). Причем, в зависимости от конструкции станка обрезку проводят по 1 листу или по-несколько листов в пачке.
Переобрез фанеры производит, как правило, на однопильных станках. Для шлифования фанеры в настоящее время и в перспективе используют широколенточные шлифовальные станки.
Производительность обрезных станков 4-пильных (составленных из 2-пильных спаренных)
Псм.= , л/см, (76)
Псм.= , м3/см, (77)
где Т – продолжительность смены, мин; U – скорость подачи, м/мин; n – число листов фанеры в пачке; Sn – высота пачки, мм; Sф – толщина фанеры, мм; К1 – коэффициент использования машинного времени станка, К1=0,9; К2 – коэффициент использования рабочего времени, К2=0,9; lH – длина листа необрезной фанеры, м; L, b – соответственно длина и ширина листа обрезной фанеры, м.
Производительность шлифовальных станков.
Псм.= , м3/см (78)
где Т – продолжительность смены, мин; U – скорость подачи, м/мин; К3 – коэффициент заполнения станка, (К3=0,9…0,95); Кр – коэффициент использования рабочего времени станка (Кр=0,9…0,94); b, Sф – ширина (м) и толщина фанеры (мм).
Дата добавления: 2019-07-15; просмотров: 373; Мы поможем в написании вашей работы! |
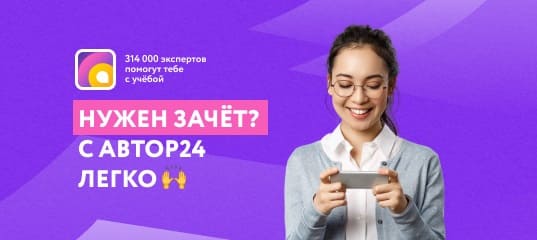
Мы поможем в написании ваших работ!