Станкоемкость механической обработки
Основой расчетов количества оборудования является станкоемкость механической обработки, которая представляет собой сумму станочных затрат времени на выполнение операции и выражается обычно в станко-часах или станко-минутах [1].
При проектировании деревоперерабатывающих цехов станкоемкость обработки предметов труда можно определить по технологическому процессу, по заводским нормам или по материалам ранее выполненных проектов, по технико-экономическим показателям и по типовым нормам. Использование того или иного метода зависит от типа производства, номенклатуры, программы и других факторов.
Станкоемкость по технологическому процессу определяется путем нормирования затрат времени для выполнения отдельных операций с учетом прогрессивных режимов обработки. Это наиболее точный метод, применяемый в основном для массового и крупносерийного производства.
Норма времени ТШ на операцию в общем виде определяется по формуле
Т Ш = Т О + Т В + Т ОБС + Т ОТД + Т П-3, (4)
где Т О - основное (технологическое или машинное) время, мин; ТВ – вспомогательное время на операцию, мин; Т ОБС – время на обслуживание (техническое и организационное) рабочего места, мин; Т ОТД – время на перерывы для отдыха и естественные надобности, мин; Т П-3 – время подготовительно-заключительное, мин.
Из всех составляющих, входящих в данную формулу, только основное время определяется теоретическими расчетами в зависимости от принятых режимов обработки и кинематики станка, остальные берутся по нормативам.
|
|
Для укрупненных расчетов в серийном и единичном производстве, а так же при реконструкции цехов механической обработки находят станкоемкость по нормам завода или материалам ранее выполненных проектов. В этом случае за основу расчета принимают фактическую станкоемкость ТФ с учетом коэффициента ужесточения за счет принятой прогрессивной технологии:
(5)
где ТПР – станкоемкость, принимаемая для проекта, станко-ч; ТН – действующая на заводе норма станкоемкости, станко-ч; В – средний уровень выполнения норм, %; КУ – коэффициент, учитывающий ужесточение норм.
Определение коэффициента КУ зависит от опыта и квалификации проектанта, от его умения оценить ожидаемые усовершенствования технологии производства в проекте.
Метод определения станкоемкости деталей по технико-экономическим показателям является еще более укрупненным и заключается в том, что станкоемкость определяют по данным аналогичных производств или из отраслевых нормативов.
|
|
Независимо от способа определения станкоемкости составляют расчетную ведомость станкоемкости механической обработки для каждого предмета труда, входящего в программу.
Расчет ритма выпуска продукции
При проектировании технологического процесса механической обработки предметов труда поточного производства должен быть определен ритм их выпуска с поточной линии [1].
Величина ритма рассчитывается по формуле
(6)
где Д – количество предметов труда, подлежащих обработке в год на данной поточной линии, шт; Ф ЭФ – эффективный (расчетный) годовой фонд времени работы оборудования, ч:
(7)
где Т К – календарное число дней в году; m – количество нерабочих дней; С – количество смен; ТС – продолжительность смены, ч; КП – коэффициент, учитывающий простой оборудования при планово-предупредительных ремонтах, К П = 0,93…0,97.
Для многопредметных поточных линий, где обрабатываются предметы труда сходные по размерам и конфигурации, но различающиеся по трудоемкости, ритм выпуска определяется по формуле
(8)
|
|
где Д1 + Д2 + … + Дп – количество предметов труда разных наименований, подлежащих обработке в год на данной линии, шт; КП – коэффициент, учитывающий потери времени на переналадку линии (принимают в пределах 0,9).
При разработке технологического процесса для поточных линий необходимо синхронизировать операции.
Степень синхронности по операциям (%) определяют по формуле
(9)
где N П и N Р – принятое и расчетное количество рабочих мест или оборудования.
Синхронизация операций производится с целью приведения продолжительности каждой операции к величине, равной или кратной ритму. При этом используют концентрацию (объединение) и дифференцирование (расчленение) операций. При необходимости вводятся новые приспособления, инструменты, разрабатываются мероприятия по улучшению организации рабочих мест, заменяется ранее выбранное оборудование, меняется количество рабочих мест, пересматриваются нормы выработки, производится перестановка и перегруппировка элементарных операций. Величина отклонения длительности операций от ритма допускается в пределах 10 %.
|
|
3.7. Выбор и определение потребного количества
технологического оборудования
При выборе оборудования необходимо учитывать следующие факторы [1]:
а) технические требования к выпускаемой продукции (например, не может быть принято оборудование экономически выгодное, но не обеспечивающее требуемого качества);
б) технические возможности оборудования и наличие производственных площадей (например, при ограниченных производственных площадях может быть принят вариант с повышенными производственными затратами, но обеспечивающий выполнение программы на имеющихся площадях);
в) требования техники безопасности и промышленной санитарии (не может быть принято оборудование с низкими приведенными затратами, но не обеспечивающее выполнение техники безопасности и производственной санитарии).
Во всех остальных случаях предпочтение отдается варианту с наименьшей станкоемкостью и минимальными приведенными затратами на использование оборудования, которые определяются размерами затрат на его приобретение и эксплуатацию.
В условиях крупносерийного и массового производства технологический процесс целесообразно строить на основе поточного производства с использованием автоматических, полуавтоматических и конвейерных линий, однако применение высокомеханизированного и автоматизированного оборудования может быть обусловлено сроком окупаемости не более 5 лет.
При выборе оборудования рекомендуется пользоваться следующими источниками информации:
- типовыми технологическими процессами и режимами изготовления продукции;
- стандартами или техническими условиями на технологическое оборудование;
- каталогами и паспортами на технологическое оборудование;
- проспектами станкостроительных заводов, справочной литературой по современному технологическому оборудованию.
Технико-экономические показатели имеющегося нетипового оборудования принимаются по технической документации на него, а вновь создаваемого по аналогам.
Количество деревоперерабатывающего оборудования, необходимого для выполнения заданной программы, определяется различными методами: по общей станкоемкости и эффективному фонду времени работы оборудования; производительности и годовому объему работы станка; по затратам времени на один предмет труда и ритму работы поточной линии.
По первому методу расчет количества станков ведут по формуле
(10)
где NР – расчетное число станков данного типа; ТС – станкоемкость механической обработки, станко-ч; П – годовая программа выпуска изделий, шт.; Ф ЭФ – эффективный фонд времени работы оборудования, ч.
При втором методе расчета станков и автоматических линий используют формулу
(11)
где Q Г.СТ – годовой объем работы станка (линии) в учетных единицах (шт., м3, м2, пог.м); П Г – годовая производительность станка (линии) в учетных единицах (шт., м3, м2, пог.м).
Расчет количества оборудования в составе поточной линии производят пооперационно по формуле
(12)
где Т – время обработки предметов труда на данной операции, мин; R – ритм выпуска предметов труда в линии, мин.
Полученное количество станков является расчетным и обычно бывает дробным. Дробные величины округляют в большую сторону, получая принятое число станков, N П, причем всегда N П > N Р.
Полученное количество станков далеко не всегда отражает фактическую потребность в оборудовании.
Полнота использования оборудования характеризуются коэффициентом загрузки оборудования, который показывает загруженность по выполнению программы и определяется отношением расчетного количества станков к принятому:
(13)
Средние значения коэффициента загрузки оборудования по цеху для единичного и мелкосерийного производства принимают 0,85…0,9 и выше, для серийного производства не ниже 0,75…0,85.
При анализе загрузки оборудования необходимо пользоваться следующими рекомендациями:
- перезагрузку станка можно ликвидировать путем передачи объема работы на другой, менее загруженный станок, технические возможности которого позволяют выполнить данную операцию, если это не нарушает маршрутов движения предметов труда;
- в некоторых случаях целесообразно заменить перегруженные станки на более производительные;
- при низкой загрузке целесообразно заменить станок на менее производительный с меньшими приведенными затратами;
- повысить коэффициент загрузки можно путем изменения годовой программы выпуска продукции.
В результате анализа загрузки оборудования производится уточнение и корректировка состава оборудования.
Для облегчения и систематизации расчетов при установлении числа станков составляют ведомость по установленной форме для каждого участка, отделения и других организационных форм, предусмотренных проектом.
Дата добавления: 2019-07-15; просмотров: 437; Мы поможем в написании вашей работы! |
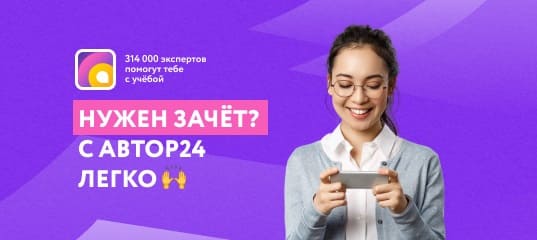
Мы поможем в написании ваших работ!