ДОЛГОВЕЧНОСТЬ АСФАЛЬТОБЕТОННЫХ ПОКРЫТИЙ АВТОМОБИЛЬНЫХ ДОРОГ
9.1. Общие сведения
Асфальтобетоны изготавливаются из асфальтового вяжущего, представляющего собой смесь битума с тонкомолотым минеральным порошком, крупного заполнителя – гравия или щебня и мелкого заполнителя – песка.
По назначению асфальтобетоны подразделяются на дорожные, аэродромные, гидротехнические, асфальтобетоны для устройства полов в промышленных зданиях.
Основные свойства асфальтового бетона зависят от примененного асфальтового вяжущего, состава бетона и его пористости. Пористость асфальтового бетона составляет 1…18%. Плотные бетоны (с пористостью не более 5%) обычно водонепроницаемы. Чем выше пористость асфальтового бетона, тем хуже его долговечность в связи с возрастанием водопоглощения, снижением морозостойкости, а также понижением стойкости к химической коррозии.
В отличие от цементного бетона, на показатели прочности асфальтобетона сильно влияет температура. Например, если предел прочности при сжатии асфальтобетона при 20оС составляет ~ 2…2,5 МПа, то при 50оС ~1 МПа.
Асфальтобетоны укладывают в горячем или холодном состоянии. Наиболее распространены горячие асфальтобетонные смеси, имеющие при укладке температуру от 140 до 170 оС. Для их приготовления предварительно высушенные и подогретые до 180-200 оС минеральные составляющие бетона (тонкомолотый минеральный порошок, песок, щебень) загружают в смеситель, в котором их перемешивают с расплавленным битумом. Готовые асфальтобетонные смеси укладывают и уплотняют катками. Через 1…2 часа асфальтобетон отвердевает, приобретая прочность камня.
|
|
Асфальтобетоны, укладываемые в холодном состоянии, приготовляют на жидких битумах и битумных эмульсиях. Жидкий битум подогревают до 110-120 оС и смешивают с высушенными и подогретыми до той же температуры заполнителями. Асфальтобетонную смесь с температурой 60 оС развозят на места и укладывают при температуре окружающей среды не ниже +5 оС.
Качество асфальтобетона зависит от его состава, технологии приготовления смеси, укладки и уплотнения. Изучение физико-химических процессов на границе минеральный материал - битумное вяжущее дает возможность обоснованно выбрать состав асфальтобетонной смеси, который при определенном режиме приготовления обеспечивает требуемые физико-механические свойства асфальтобетона. Природа, прочность, пористость, гранулометрический состав минеральной части оказывает влияние на особенности взаимодействия с различными вяжущими материалами.
9.2. Требования к материалам для асфальтобетона
1. Заполнители. Мелкий заполнитель – песок. В асфальто–и дегтебетонах могут применяться различные пески. Крупные пески оцениваются модулем крупности Мк > 2,5 и содержанием в них зерен крупнее 0,63 более 50%. Пески средние оцениваются модулем крупности Мк = 2,5-2 и содержанием в них зерен крупнее 0,315 в пределах 35- 50%.
|
|
Применяемый для асфальтобетонов песок природный и из отсевов дробления горных пород должен соответствовать требованиям ГОСТ 8736, общее содержание зерен менее 0,16 мм (в том числе пылевидных и глинистых частиц) в песке из отсевов не нормируется, а содержание глинистых частиц от 0,5 до 1 %.
По происхождению лучшим для асфальтобетона является искусственный (дробленый) песок, как имеющий неокатанную форму зерен и обладающий за счет этого лучшим сцеплением с битумом. По минеральному составу предпочтительней использовать песок из карбонатных пород (известняка, ракушечника, магнезита, доломита и др.), т.к. он обладает более высоким сродством к битуму за счет явления хемосорбции. На поверхности этих материалов битум образует водонерастворимые химические соединения, то есть происходит хемосорбционное взаимодействие с горной породой. Кислые горные породы (гранит, андезит и другие), содержащие более 65% SiO2, при взаимодействии с битумом не образуют хемосорбционных соединений. Адгезия битума к этим зернам пониженная, а асфальтобетон отличается более низкими показателями прочности, водо- и теплостойкости.
|
|
Крупный заполнитель – щебень и гравий. Щебень из плотных горных пород по зерновому составу, прочности содержанию пылевидных и глинистых частиц, содержанию глины в комках, должен соответствовать требованиям ГОСТ 8267-93.
Гравий для асфальтобетонов должен соответствовать требованиям ГОСТ 8267-93. Для асфальтобетонов применяют гравий фракций 5-10, 10-20(15), 20(15)- 40, а также смеси указанных фракций.
Качество щебня и гравия характеризуется показателями:
- прочности (маркой по раздавливанию в цилиндре, по сопротивлению износу в полочном барабане, по морозостойкости);
- крупностью и формой зерен (фракции 5…40 мм, форма зерен- кубовидная, количество лещадных зерен для смеси А до 15%, для смеси Б - 25% и В -35% по массе);
- степенью загрязненности пылевато-глинистыми частицами (не более 1,5% по массе);
- петрографическим составом, который влияет на шероховатость покрытия. Чем выше шероховатость, тем лучше сцепление колес автотранспорта с дорогой. Шероховатость для гранита сохраняется до 5 лет эксплуатации дороги, а для известняка – один сезон, хотя адгезия битума к поверхности известняка больше, чем к граниту.
|
|
Минеральный порошок (ГОСТ 52129-2003). Он представляет собой полидисперсный материал и является важнейшим структурообразующим компонентом асфальтобетона. На его долю приходится до 95% суммарной поверхности минеральных зерен асфальтобетона.
Основное назначение минерального порошка – переводить объемный битум в пленочное состояние. При этом повышается вязкость и прочность битума. Вместе с битумом минеральный порошок образует структурированную дисперсную систему, которая выполняет роль вяжущего материала в асфальтобетоне. Кроме того, минеральный порошок заполняет поры между частицами песка, что способствует повышению плотности асфальтобетона и снижению расхода битума.
Лучшими для асфальтобетонов являются минеральные порошки, получаемые в результате тонкого измельчения известняков и доломитов. Также широкое применение нашли минеральные порошки из отходов промышленности: цементной пыли, золы-уноса ТЭЦ, молотых основных доменных шлаков, шламов доменного и конверторного производства и др. В Башкортостане проведены исследования и показана возможность применения отходов содового и сахарного производства для этой цели.
Активность минерального порошка объясняется его высокоразвитой поверхностью, которая составляет 2500…5000 см2/г. Чем выше этот показатель, тем выше активность минерального порошка. Однако очень высокая дисперсность порошков приводит к слипанию наиболее мелких частиц. В минеральном порошке должно содержаться частиц меньше 0,071 мм не менее 70% в неактивированном и не менее 80% в активированном порошке. При этом все остальные зерна минерального порошка должны проходить через сито с отверстиями 1,25 мм.
3.Битум. Вяжущим в асфальтобетоне могут быть жидкий и вязкий нефтяные битумы, марка которых выбирается в зависимости от дорожно-климатической зоны.
9.3.Разрушение асфальтобетона в процессе эксплуатации автомобильных дорог и способы повышения его долговечности
Деструкция (разрушение) асфальтобетона связана прежде всего с изменением свойств битумного (асфальтового) вяжущего под влиянием различных факторов: старения, влияния знакопеременных температур, воздействия воды, загрязнений, усталостного разрушения и других факторов.
Старение битумов. Под старением битумов подразумевают совокупность всех химических и физических процессов, приводящих со временем к изменению их свойств. Обычно на битумы действуют тепло, солнечный свет, кислород воздуха, озон, вода, бактерии, динамические нагрузки от автомобильного транспорта. Эти факторы вызывают в молекулах битумов разрыв химических связей и образование свободных радикалов. Устойчивость битумов к действию тепла и кислорода зависит от их строения и, прежде всего, от наличия легкоокисляющихся групп и связей в макромолекулах, количество которых устанавливается методом электронного парамагнитного резонанса (ЭПР). В результате старения возрастает содержание твердых хрупких составляющих (асфальтенов) за счет уменьшения содержания смолистых веществ и масел.
Оценка интенсивности старения битумов основана на изучении степени изменения свойств в результате нагрева. По ГОСТ 22245-90 изменение их свойств определяют после нагревания битума до 160оС в течение 5 часов. Изменение температуры размягчения после прогрева и служит показателем его устойчивости к старению. Битумы, обнаруживающие большие изменения этого показателя, оказываются более склонными к атмосферному старению.
Повышение сопротивления старению битумов обеспечивают добавками ингибиторов, способствующих подавлению окислительных процессов, например, продуктов алкилирования n-крезола изобутиленом. Замедлению старения битума способствует введение в состав асфальтобетона сажи или технического углерода. Добавки алифатических аминов стабилизируют асфальтены битума, предотвращая их агрегирование, что также замедляет старение.
В процессе эксплуатации происходит окисление битума кислородом воздуха. Изменяется его групповой состав в сторону увеличения тяжелых фракций (асфальтенов и смол). Старение битума и, как следствие, деструкция асфальтобетона проявляется в разрушении поверхностного слоя покрытия в виде постепенного выкрашивания и шелушения с вырыванием отдельных минеральных частиц. Это является результатом снижения адгезии между заполнителями (щебень, песок) и органическим вяжущим.
Окислительный процесс ускоряется под воздействием солнечной радиации, особенно ультрафиолета. Воздействие ветра также приводит к к росту хрупкости и количества микропор и трещин в покрытии. С увеличением в битуме кислородосодержащих (в результате окисления), азотистых и сернистых соединений (например, при воздействии выхлопных газов автотранспорта) стабильность битума уменьшается.
Кроме окисления (воздействия кислорода воздуха) и полимеризации (за счет изменения температуры) на старение битума влияют процессы синерезиса и эмульгирования.
Синерезис представляет собой процесс самоуплотнения битума под влиянием сил тяжести или внешней нагрузки. Из битума постепенно выделяется жидкостная фаза (масла и легкие смолы), которая в дальнейшем или сорбируется минеральными компонентами, или выдавливается наружу под внешним давлением, выступая в виде “жирных” пятен. В первом случае возрастает количество асфальтенов в битуме, повышается прочность и жесткость, и, как следствие, хрупкость материала. Во втором случае ослабляются структурные связи в верхних слоях при повышенной температуре и появляются пластические деформации в покрытии.
Эмульгирование битума может быть вызвано присутствием в компонентах асфальтобетонной смеси эмульгаторов – глинистых примесей, извести, поверхностно-активных веществ и др. Частичный перевод битума в эмульгированное состояние приводит к снижению адгезионных свойств, некоторой потере связности и прочности. Синерезис и эмульгирование могут привести к необратимому ухудшению качества асфальтобетона.
Наличие в составе смеси полуторных оксидов (Fe2O3, Al2O3) также приводит к ускорению старения битума. Поэтому в минеральном порошке ограничивается содержание полуторных оксидов (1,7% для неактивированного и 7% для активированного минерального порошка).
Влияние температуры. Асфальтобетон чувствителен к изменению температуры воздуха. Это является источником постоянных структурных изменений. Как уже отмечалось выше, битум представляет собой коллоидную структуру, в которой соотношение дисперсионной среды и дисперсной фазы зависит от температуры. При снижении температуры повышается концентрация твердой (дисперсной) фазы, за счет выделения из системы новых центров структурообразования. При повышении температуры наблюдается обратная закономерность. Концентрация твердой фазы уменьшается вследствие снижения вязкости из-за усиления теплового молекулярного движения. При этом практически непрерывно изменяется пластичность асфальтобетона. При одновременном воздействии циклических механических нагрузок (воздействие колес автомобилей) изменение пластичности приводит к нарушению структуры, к потере деформационной устойчивости покрытия и разрушению материала.
Одним из характерных дефектов асфальтобетонного покрытия является появление и развитие остаточных деформаций в виде наплывов, волн, гребенок, колей. Это необратимые деформации, появлению которых способствует повышение температуры воздуха. Они зависят от теплоустойчивости битума. Теплоустойчивость - это способность асфальтобетонных смесей и асфальтобетона сохранять прочность при повышенных температурах. Характеризуется коэффициентом теплоустойчивости Кт, представляющим собой отношение предела прочности образцов смеси при сжатии при температуре +20оС к пределу прочности при +50оС.
;
где Кт – коэффициент теплоустойчивости,
Rсж 1 – предел прочности при температуре +20о;
Rсж 2 – предел прочности при температуре +50о;
Как правило, асфальтобетон имеет коэффициент теплоустойчивости 2-2,75. Чем меньше КТ , тем устойчивей асфальтобетон к повышению температуры.
Основным условием повышения теплоустойчивости асфальтобетона является выбор соответствующей марки битума, обеспечение оптимального состава асфальтобетона, высокая степень уплотнения смеси.
При отрицательных температурах и одновременном приложении нагрузки из-за температурных напряжений возникают хрупкие микро- и макроразрывы и в конечном итоге трещины в асфальтобетонном покрытии. Оценка морозостойкости асфальтобетона производится по следующей методике. Коэффициент морозостойкости устанавливается как отношение предела прочности на сжатие при 20оС образцов асфальтобетона после определенного числа циклов замораживания-оттаивания к пределу прочности водонасыщенных образцов при 20оС.
;
где Rсж 1 – предел прочности при сжатии образцов, подвергавшихся замораживанию-оттаиванию;
Rсж 2 - предел прочности при сжатии водонасыщенных образцов при 20оС.
Образцы асфальтобетона выдерживаются в течение 1 сут в нормальных температурно-влажностных условиях, затем 1,5 часа под вакуумом для насыщения водой, а потом оставляются на 1час в воде. Замораживание образцов производится при температуре (-20) –(-25)оС в течение 4 часов и оттаивание при +20оС не менее 4 часов.
Воздействие воды. Значительное влияние на долговечность покрытий оказывает и воздействие воды. Под влиянием воды также происходит разрушение структуры в результате нарушения сцепления битумных пленок с минеральными частицами. Чем больше воды проникает в материал, тем быстрее разрушается покрытие. Чтобы затормозить этот процесс, необходимо тщательное уплотнение асфальтобетона после укладки. Особенно важным это является для слоев износа. Наиболее интенсивно насыщение покрытия водой происходит при длительном контакте дорожной одежды с водой в осенний и весенний периоды.
Вода представляет собой сильно поляризованную жидкость. Она способна вытеснять с поверхности минералов менее полярные молекулы, ранее адсорбировавшиеся из битума. Затем происходит обводнение всей системы, приводящее к набуханию асфальтобетона. При переходах температуры покрытия через 0оС происходит разуплотнение асфальтобетона вследствие замерзания воды в порах покрытия. Увеличивается пористость материала, облегчается доступ кислорода воздуха внутрь покрытия, ускоряется процесс окисления битумного вяжущего. В результате изменяется групповой химический состав и свойства битума.
Загрязнения покрытия. В процессе эксплуатации необходимо следить за чистотой покрытия. Наличие на поверхности пыли и грязи способствует задержке воды на покрытии и диффузии ее в дорожную одежду.
На стадии эксплуатации необходимо поддерживать покрытие в чистом состоянии, проводя мероприятия по его очистке и обеспыливанию. Источниками пыли являются грунт, приносимый колесами автомобилей с грунтовых дорог и обочин, продукты износа покрытий и шин автотранспортных средств.
При этом нужно принимать во внимание, что наибольшее количество пыли образуется на гравийных и грунтовых дорогах и возрастает с ростом интенсивности движения. Шинная пыль вызывает аллергию и опухолевые заболевания. За 1 год эксплуатации шина может терять до 1 кг в виде пыли.
Обеспечение нормальных условий движения по дорогам требует периодической очистки усовершенствованного покрытия от пыли, грязи и посторонних предметов, а на покрытиях переходного и простейшего типа - проведение мероприятий по их обеспыливанию.
Основными способами обеспыливания автомобильных дорог являются:
- увлажнение водой в объеме 1 - 2 л/м2. Поливка водой способствует уменьшению пыли, но эффект поливки недолог (в жаркую погоду не более 1 часа);
-механизированная очистка дорожных покрытий. Для этого применяют автомобильные очистители (со щетками различного типа), снабженные цистернами и поливочными устройствами. Достаточно часто дороги загрязняются глинистыми грунтами, которые в сырую погоду создают опасность для движения. Глинистый грунт смывают водой или соскабливают с усовершенствованных покрытий щетками и ножевыми машинами;
-поливка морской водой или водой из соленых озер. Можно добавлять в воду гигроскопичные соли, такие как хлористый кальций, которые, поглощая влагу из воздуха, удерживают частицы пыли на покрытии. Расход раствора хлористого кальция при 20-30% концентрации составляет на 1 м2 около 0,15 - 0,25 л. Действие хлористого кальция продолжается в течение 1-2 месяцев, поэтому в сухих районах хлористый кальций достаточно применить 2-3 раза за лето;
-применение жидких или разжиженных органических материалов – жидких битумов, тяжелой нефти, топочного мазута, битумных эмульсий или паст. Разлив производят по сухому покрытию, очищенному от пыли, в солнечные дни, в часы наибольшего нагрева солнцем;
-устройство лесозащитных полос вдоль дорог. Зеленые насаждения обладают хорошей пылепоглощающей способностью, причем она зависит от породы деревьев и кустарников. Лучше пыль задерживают растения с шероховатыми листьями, покрытыми ворсинками (вяз, ива и др.). На листовой поверхности таких деревьев осаждается до 70% пыли из атмосферного воздуха.
Кроме того, чрезвычайно важным на стадии эксплуатации автомобильных дорог является поддержание высокого уровня гидрофобности покрытия, что достигается обработкой верхних слоев дорожной одежды битумом или специальными гидрофобными составами.
Нарушения технологии укладки покрытия. Недостаточное уплотнение покрытия может свести на нет любые мероприятия, направленные на повышение качества и долговечности асфальтобетонного покрытия. Недоуплотненные покрытия разрушаются до приобретения необходимой плотности. В первую очередь выходят из строя полосы, где нет движения и не происходит доуплотнения асфальтобетона.
Усталостные разрушения. Сопротивление усталости характеризуется пределом выносливости – напряжением, соответствующим разрушению при заданном числе циклов нагружений. Усталость – это снижение механической прочности в результате многократного воздействия нагрузок. Это явление связано с образованием и накоплением микродефектов с последующим развитием их в макродефекты и снижением прочности. При проходе колеса автомобиля максимальные растягивающие возникают в подошве покрытия, в результате чего через определенное число циклов приложения нагрузки в подошве покрытия под полосой наката возникают микротрещины, объединяющиеся затем в макротрещины. Макротрещины растут одновременно в двух направлениях: вверх и параллельно плоскости покрытия. Еще через определенное число циклов нагружения трещина проростает сквозь покрытие и становится видимой на его поверхности. В соответствии с описанным механизмом процесс разрушения покрытия можно разделить на 2 стадии: накопление повреждений и рост магистральной трещины. Основной причиной усталостного разрушения является относительно тонкие или слабые (по прочности на растяжение при изгибе) асфальтобетонные слои для заданной транспортной нагрузки. Многочисленные исследования показывают, что в наибольшей степени усталостному разрушению подвержены асфальтобетонные покрытия толщиной 7,6-12,7 см. Учитывая, что в РФ на дорогах 3 и 4 категории толщина двухслойного покрытия составляет 10-14 см, основной механизм разрушения таких покрытий носит усталостный характер.
Износ. Износ характеризуется потерей массы материала, отнесенной к площади оцениваемого участка. Долговечность дорожных покрытий определяется износостойкостью асфальтобетона и выражается величиной истираемости (поверхностный износ), внутреннем износе и шелушении. Наиболее значимой составляющей является истираемость. Истираемость И – свойство материала уменьшаться в объеме и массе вследствие разрушения поверхностного слоя под действием истирающих усилий. Она оценивается потерей массы образца, отнесенной к площади истирания
где И – истираемость, г/ см2;
м1 – масса материала до испытания, г;
м2 – масса материала после испытания, г;
А – площадь образца, см2.
Износ асфальтобетона является очень сложным явлением и не поддается вычислению по формулам. Неодинаковый износ по площади покрытия обусловлен следующими факторами: непостоянством прочности поверхностного слоя по площади, низкой ровностью, что приводит к ударным нагрузкам и застою воды на поверхности покрытия.
Дата добавления: 2019-07-15; просмотров: 1193; Мы поможем в написании вашей работы! |
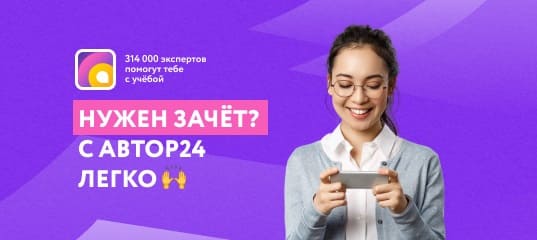
Мы поможем в написании ваших работ!