МЕТОДЫ И МАТЕРИАЛЫ ДЛЯ ЗАЩИТЫ ОТ КОРРОЗИИ БЕТОНА И ЖЕЛЕЗОБЕТОНА
7.1.Методы первичной защиты бетонных и железобетонных конструкций
Главное направление борьбы с коррозией материалов и конструкций – повышение стойкости самого материала. Это можно достичь различными путями. Для капиллярно-пористых материалов типа бетонов – это прежде всего увеличение их плотности и водонепроницаемости. Изменение химического состава также может существенно повысить его стойкость.
Коррозионная стойкость бетона в большой степени зависит от химического (минерального) состава цемента. Можно придать бетону стойкость в определенной среде, если применить специальный цемент, например, сульфатостойкий портландцемент для эксплуатации в сульфатных средах. В этом цементе содержание C3A не должно превышать 5%.
Введение в портландцемент шлаков также, как правило, повышает сульфатостойкость бетона.
Иногда применяют портландцементы не только повышенной стойкости, но и цементы специального предназначения для работы в агрессивных средах. К ним в первую очередь относится кислотостойкий цемент на жидком стекле. Он состоит из порошкообразных кислотостойких материалов (молотого кварцевого песка, диабаза, андезита) и затворяется на жидком стекле – растворе силиката натрия или калия Na(K)2O·mSiO2. Для ускорения твердения в состав цемента вводится кремнефтористый натрий в количестве 10 – 12%.
Жидкостекольные бетона применяют для футеровки аппаратов баков, отстойников для кислот, устройства кислотостойких полов. Другая специальная область применения таких бетонов – жаростойкие бетоны, способные выдерживать температуры до 900оС.
|
|
При действии кислоты в бетонах образуется гель кремнекислоты и другие продукты, обладающие высокой кислотостойкостью и уплотняющие структуру бетона. Но при воздействии воды или слабых кислот жидкостекольные бетоны разрушаются вследствие выноса из них щелочи.
Существенное значение на показатели проницаемости бетона, а, следовательно, и на его коррозионную стойкость имеет водоцементное отношение (В/Ц) бетонной смеси. Чем меньше вводится воды, тем лучше свойства бетона. Однако, чем меньше воды, тем больше усилий нужно приложить, чтобы уплотнить смесь, т.е. уложить бетон. К наиболее распространенным способам уплотнения бетонной смеси относятся:
а) вибрирование. При вибрировании бетонной смеси передаются колебания, создаваемые вибромеханизмом, в результате чего она становится подвижной, текучей и заполняет все профили формы. Используют поверхностные вибраторы с плоской плитой, глубинные (внутренние) вибраторы и стационарные виброплощадки. Область применения вибраторов обусловлена размерами и формой бетонируемой конструкции, степени ее армирования и подвижности бетонной смеси. Внутренние вибраторы типа “булавы” с жестким валом применяют для уплотнения бетонной смеси массивных конструкций, а внутренние с гибким валом – для густоармированных конструкций. Наружными вибраторами уплотняют бетонную смесь в густоармированных тонкостенных конструкциях.
|
|
б) Вибропрессование и виброштампование. В этих методах вибрирование сочетается с прессующими воздействиями плоской (вибропрессование) или профилированной (виброштампование) плиты. Методом виброштампования формуют ребристые плиты, лестничные марши и др.
в) Центрифугирование. При формовании изделий на центрифугах форма с бетонной смесью вращается с определенной скоростью вокруг своей продольной оси, в результате чего центробежные силы распределяют бетонную смесь по стенкам формы. Изделия получаются полые, с внутренней полостью круглого сечения и любым внешним очертанием, в зависимости от профиля формы. Этим методом формуют трубы и другие полые изделия.
г) Уплотнение штыкованием ведут вручную с помощью шуровок. Из-за низкой производительности метод применяют редко и только для тонкостенных и густоармированных конструкций.
|
|
Не менее важны и условия твердения бетона. При недостаточной влажности структура цементного камня получается крупнопористой. Такой же она получается, если бетон твердеет в условиях прогрева без достаточного увлажнения. Высыхание бетона в период твердения приводит к появлению крупных сквозных пор. Поэтому для созревания бетона необходимо создавать благоприятные условия твердения. Изменения температуры не должны быть резкими и не вызывать температурных напряжений.
Длительное увлажнение, в том числе и полное погружение в воду, существенно увеличивают плотность и стойкость бетона.
Уменьшить В/Ц можно путем введения в смесь поверхностно-активных веществ – пластифицирующих добавок.
Для повышения плотности бетона и его долговечности и гидрофобности используются битумные эмульсии, и другие материалы, такие как “ Пенетрон ”, “Аквастоп” и т.п.
Также применяются уплотняющие (кольматирующие) добавки, которые при взаимодействии с солями кальция образуют новое соединение, заполняющее поры, и повышают водонепроницаемость бетона. К таким добавкам относится хлористое железо FeCl3, образующее в порах бетона осадок гидроксида железа
|
|
FeCl3 + Ca(OH)2 = CaCl3 + Fe(OH)3
Введение уплотняющих добавок в бетонную смесь имеет большую историю. Еще в конце ХIX-го века при строительстве Парижского метро в бетон добавляли альгинат натрия – продукт, получаемый после переработки водорослей. В процессе взаимодействия с солями кальция образуется рыхлый студенистый осадок, который при набухании уплотняет поры цементного камня. Есть сведения, что римляне использовали водоросли при строительстве акведуков.
В Индии при строительстве наиболее ответственных сооружений в известковые растворы добавляли казеин (в виде кислого молока) или яичный белок. Яйца добавляли в кладочный раствор при строительстве Покровского собора (собор Василия Блаженного) на Красной площади.
Конечно, при современных масштабах строительства такие способы неприемлемы. Современные уплотняющие добавки представляют собой неорганические соли или полимерные соединения.
7.2. Защита арматуры железобетонных конструкций
В обычных условиях защита арматуры в железобетонных конструкциях не требуется. При действии агрессивных сред возможны следующие способы защиты стальной арматуры.
Во-первых, в зависимости от степени агрессивности среды нормируется плотность и толщина защитного слоя бетона, ограничивается ширина раскрытия трещин. В сильноагрессивных средах раскрытие трещин, как правило, полностью исключается, особенно если среда содержит хлориды. В среднеагрессивных средах ширина раскрытия трещин должна быть ≤ 0,25 мм.
Можно затормозить коррозионные процессы в стали, находящейся в бетоне. Для этого в состав бетона вводятся специальные добавки – ингибиторы коррозии стали. К ним относятся, например, нитриты и фосфаты металлов. Обычное содержание ингибиторов в бетонной смеси составляет 1…2% от массы цемента. Они вводятся в растворенном виде с водой затворения бетона. Ингибиторы вступают в реакцию с металлом и создают на поверхности арматуры защитную пленку. От вида и количества ингибитора зависит продолжительность и степень его защитного действия.
Например, введение в бетон 2% фосфата натрия Na3PO4 позволяет повысить критическое содержание хлорид-ионов с 0.4 до 2% (от массы цемента).
Иногда для защиты арматуры применяются металлические или полимерные покрытия. В качестве металлических покрытий чаще всего применяется цинкование, реже – покрытие алюминием. Обычно цинкованию подвергаются закладные детали. Арматура не оцинковывается. Это связано с размерами гальванических ванн (завод Автоприбор в г.Октябрьском имеет размер ванн не более 2 м).
Покрытие арматуры окрасочными составами применяется в бетонах, не способных пассивировать сталь, например, в газобетонах. В газобетонах pH поровой жидкости < 11.8, т.к. нет свободной Ca(OH)2.
При изготовлении панелей из газобетона устраиваются специальные линии для антикоррозионной защиты арматурных каркасов. В качестве защитных составов часто используются так называемые наполненные составы с металлическим порошком (цинол, цинакс), например, цинксиликатные покрытия. Но возможно применение и других составов (например, на основе эпоксидных смол).
Важное направление повышения стойкости железобетонных и металлических конструкций в агрессивной среде – правильное конструирование элементов и узлов строительных конструкций.
К общим принципам конструирования относятся:
- придание конструктивным элементам возможно более простой формы, с минимальным отношением поверхности к объему;
- полное исключение из конструкций элементов с глухими зазорами, недоступными для осмотра и ремонта;
- исключение горизонтальных поверхностей (устройство уклонов), чтобы предотвратить возможный застой жидкой среды на поверхности конструкций.
Коррозионную стойкость арматуры и металлических конструкций можно повысить, применяя легированные стали. На практике это используется в ограниченном масштабе из-за их дороговизны (ранее – из-за дефицита таких сталей). Пока для строительных конструкций перспективны только низколегированные стали. В частности, стали, содержащие небольшое количество меди и обладающие повышенной стойкостью в атмосферных условиях. Можно полагать, что со временем использование нержавеющих сталей и других коррозионностойких сплавов увеличится, т.к. это – наиболее надежный способ повышения стойкости арматуры и металлоконструкций.
Существует множество способов защиты металла от коррозии. Катодное покрытие – это покрытие металлом, более электроположительным, чем основной. Например, железо способом лужения покрывают оловом. Разрушение основного металла может произойти только в том случае, если на покрытии образуется трещина и пленка не будет уже механически защищать основной металл.
Анодное покрытие – это покрытие более электроотрицательным металлом, чем основной. В соответствующих условиях будет разрушаться покрывающий металл. В случае повреждения электрохимическое растворение металла покрытия препятствует растворению основного металла. Примерами такой защиты является цинкование и хромирование.
Лакокрасочные покрытия основаны на механической защите металла пленками из различных лаков и красок.
Дата добавления: 2019-07-15; просмотров: 216; Мы поможем в написании вашей работы! |
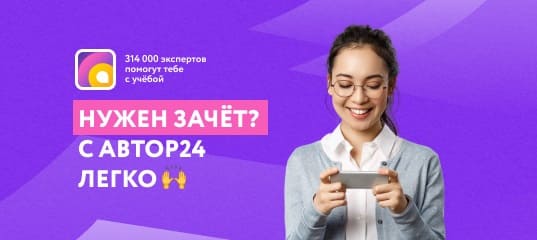
Мы поможем в написании ваших работ!