Долговечность сооружений из цементного бетона
Пособие по дисциплине “ДОЛГОВЕЧНОСТЬ ТРАНСПОРТНЫХ СООРУЖЕНИЙ” для бакалавров специальности БДС
Введение. Общие положения курса и терминология
В различных отраслях промышленности в технологических процессах используются и выделяются химически активные вещества, которые разрушительно действуют на строительные конструкции.
Если при проектировании зданий и сооружений не предусмотреть, а при возведении не осуществить необходимые меры защиты конструкций, то возможно их преждевременное повреждение – коррозия. Как следствие, потребуются значительные затраты на ремонт. В некоторых отраслях промышленности, например в нефтехимии, затраты на ремонт и восстановление зданий и сооружений значительно превышают затраты на новое строительство.
Строительные конструкции зданий и сооружений должны выполнять свои функции в течение сроков, заданных в проектах и обоснованных технико-экономическими расчетами. При этом не всегда выгодно, чтобы сооружение существовало как можно дольше. В современных условиях требования к зданиям и сооружениям быстро меняются, поэтому и необходимо, чтобы срок безаварийной службы конструкций до их замены или усиления соответствовал срокам возникновения или изменения новых требований к сооружениям. Это относится к большинству сооружений, непосредственно связанных с технологическими процессами.
Сооружения, менее тесно связанные с развитием технических средств (тоннели, каналы, мосты), должны иметь повышенные сроки службы. Некоторые сооружения, «изменяющие» или «улучшающие» природную среду, нужно проектировать на возможно более длительные сроки службы. Это – опорные стенки, плотины, берегоукрепительные сооружения и т.п.
|
|
Исходя из требований к срокам службы зданий и сооружений, определяются необходимые меры повышения стойкости строительных конструкций или защиты их от коррозии.
Наиболее рациональное решение вопроса в том, как защищать строительные конструкции от действия различных агрессивных сред, зависит от вида материала конструкций. В некоторых случаях вопрос решается просто - применением конструкций из наиболее стойкого в данных условиях материала. Например, в цехах с влажной атмосферой устойчивы конструкции из бетона и железобетона, а деревянные конструкции быстро выходят из строя. В условиях действия достаточно концентрированных кислот стойки только бетоны на жидком стекле и на некоторых полимерных смолах. Наиболее эффективен именно этот способ – применение конструкционного материала самого по себе, без защиты, стойкого в агрессивной среде. Если же не удается использовать заведомо стойкий материал, то приходится прибегать к различным способам изоляции поверхности конструкций от агрессивной среды.
|
|
Рассмотрим меры борьбы с коррозией строительных конструкций в следующей последовательности. Вначале обсудим вопросы, касающиеся оценки степени агрессивности среды по отношению к материалам и конструкциям. Затем остановимся на данных о стойкости основных строительных материалов. И, наконец, рассмотрим различные способы защиты строительных конструкций от действия агрессивных сред.
1.1. Основная терминология
Рассмотрим основные термины и определения курса “Долговечность транспортных сооружений”.
Химическая или коррозионная стойкость. Химической или коррозионной стойкостью называется способность материала противостоять агрессивному воздействию кислот, щелочей, солей или газов.
Ориентировочно ее можно оценить модулем основности материала Мо, представляющем собой отношение основных оксидов к кислотным (1)
(1)
Если в материале содержатся в большем количестве основные оксиды, то материал стоек к щелочам, но не стоек к кислотам. Если в химическом составе материала преобладают кислотные оксиды, то материал стоек к кислотам, но не стоек к щелочам.
|
|
Биостойкость – способность материалов сохранять свою прочность при контакте с живыми организмами, т.е. не являться для них питательной средой.
Долговечность. Под долговечностью материалов понимают их способность длительно выдерживать воздействие всей суммы атмосферных факторов (температуры, влажности, воздействия агрессивных веществ и др.) Она оценивается сроком службы материала без потери эксплуатационных качеств в конкретных климатических условиях и в определенном режиме эксплуатации. Например, для железобетона нормами предусмотрены 3 степени долговечности: I – со сроком службы не менее 100 лет, II – не менее 50 лет, III – не менее 20 лет. Долговечность зависит от совокупности физических, механических и химических свойств материала. Улучшая эти свойства, можно существенно повысить долговечность строительных материалов.
Долговечность – способность изделия сохранять работоспособность до предельного состояния с необходимыми перерывами на ремонт. Предельное состояние определяется степенью разрушения изделия, требованиями безопасности или экономическими соображениями.
|
|
О долговечности судят, подвергая материал испытаниям, моделирующим воздействия в натуре. Например, о долговечности многих строительных материалов можно судить, подвергая их испытанию в “камере погоды” (везерометре), где материал подвергают воздействию дождевания, ультрафиолетового облучения, действию различных температур. Лабораторные испытания сочетают с натурными испытаниями, которые проводят в условиях, близких к эксплуатационным, например, на крыше для кровельных, гидроизоляционных и отделочных материалов, в зоне прилива и отлива для гидротехнических бетонов и т.д.
Для повышения долговечности строительных материалов, эксплуатирующихся на открытом воздухе, поверхность их покрывают гидрофобными добавками, предотвращающими проникновение воды в поры материала и ее замерзание в них.
Для повышения долговечности металлов их поверхность обрабатывают нанесением защитных покрытий.
Для повышения долговечности бетона защищают его от коррозии (в основном коррозии цементного камня). Например, придают ему повышенную плотность, используют цемент с малым содержанием алита и трехкальциевого алюмината, покрывают кислотоупорными керамическими кирпичами и плитками, кислотоупорным раствором или бетоном (на жидком стекле).
Надежность. Она представляет собой общее свойство, характеризующее проявление всех остальных свойств в процессе эксплуатации. Надежность складывается из долговечности, безотказности, ремонтнопригодности и сохраняемости. Безотказность – свойство сохранять работоспособность в определенных режимах и условиях эксплуатации в течение определенного времени без перерывов на ремонт.
Ремонтнопригодность – свойство материала, характеризующее его приспособленность к восстановлению исправности и сохранению заданных технических характеристик.
Сохраняемость – свойство материала сохранять обусловленные эксплуатационные показатели в течение и после срока хранения и транспортировки, установленного технической документацией. Повышение надежности связано с улучшением всех перечисленных показателей.
Степень агрессивности среды. Степень агрессивности внешней среды по отношению к бетону и железобетону нормируется Сводом Правил СП 28.13330-2012. Она определяется не только химическим составом среды, но и комплексом физических и физико-химических факторов, характеризующих условия контакта среды и сооружения, особенно процессов коррозии. Оценка степени агрессивности среды по отношению к данному материалу зависит от состава среды и условий ее взаимодействия с материалом конструкции.
Долговечность сооружений из цементного бетона
Бетоном называется искусственный каменный материал, получаемый в результате твердения рационально подобранной смеси, состоящей из вяжущего вещества, воды, мелкого заполнителя – песка, крупного заполнителя – щебня или гравия, а в необходимых случаях – специальных добавок. К компонентам бетона предъявляются следующие требования.
2.1. Материалы для цементного бетона и их влияние на долговечность
Вяжущие. Для тяжелых бетонов в качестве вяжущих веществ применяют портландцемент и его разновидности.
Минеральный состав портландцемента. Он отражает содержание в портландцементе основных минералов.
В процессе обжига при производстве портландцемента оксиды металлов и неметаллов соединяются друг с другом, образуя минералы. В состав портландцемента входят четыре основных минерала (табл. 1):
Таблица 1 – Минеральный состав портландцемента
№ | Название минерала | Формула | Условное обозначение | Содержание % |
1 | 2 | 3 | 4 | 5 |
1 | Трехкальциевый силикат или алит | 3СаО ·SiO2 | С3 S | 45-60 |
2 | Двухкальциевый силикат или белит | 2СаО·SiO2 | С2 S | 20-30 |
3 | Трехкальциевый алюминат | 3СаО·Al2O3 | С3А | 4-12 |
4 | Четырехкальциевый алюмоферрит | 4СаО·Al2O3·Fe2O3 | С4 AF | 10-20 |
Цемент выбирают с учетом требований, предъявляемых к бетону (по прочности, морозостойкости, водонепроницаемости и др.). При выборе марки (или активности) цемента необходимо, чтобы она в 1,5…2 раза была выше требуемой прочности бетона. В табл. 2 приведены рекомендуемые марки цементов в зависимости от класса бетона В.
Таблица 2 - Выбор марки цемента в зависимости от класса бетона
Марка цемента | Класс бетона по прочности при сжатии | |||||
В 10 | В 20 | В 30 | В 35 | В 40 | В 50 | |
Рекомендуемая | М 300 | М 300 | М 400 | М 500 | М 600 | М 600 |
Допускаемая | М 300 | М 400 | М 500 | М 550, М 600 | М 500, М 550 | М 550 |
Твердение портландцемента. Оно наступает при затворении цемента водой вследствие протекания реакций гидратации между ней и минералами портландцемента. В результате этих реакций образуются гидросиликаты, гидроалюминаты и гидроферриты кальция, образующие прочный цементный камень.
Цементное тесто, приготовленное путем смешивания цемента с водой, вначале (в течение 1-3 часов после затворения) пластично и легко формуется. Потом наступает схватывание, заканчивающееся обычно через 5 – 10 часов после затворения; в период схватывания цементное тесто загустевает, утрачивая подвижность, но его механическая прочность невелика. Переход цементного теста в твердое состояние означает конец схватывания и начало твердения, для которого характерно возрастание прочности.
Сразу после затворения цемента водой начинаются химические реакции, в результате которых образуются гидросиликаты, гидроалюминаты и гидроферриты кальция, образующие прочный цементный камень. Минералы цемента – трехкальциевый силикат (алит) 3СаО·SiO2, двухкальциевый силикат (белит) 2СаО·SiO2, трехкальциевый алюминат 3СаО·Al2O3 и четырехкальциевый алюмоферрит 4СаО·Al2O3·Fе2О3 твердеют с разной скоростью и различным тепловым эффектом.
1. Трехкальциевый силикат (алит) - твердеет достаточно быстро, с образованием в ранние сроки твердения прочного гидросиликата кальция. При твердении выделяется большое количество тепла.
2(3СаО· SiO 2 ) + 6Н2О = 3СаО·2 SiO 2 ·3Н2О + 3Са(ОН)2
Выделение достаточно большого количества Са(ОН)2 может провоцировать развитие коррозии цементного камня I и II вида.
2. Двухкальциевый силикат (белит) - твердеет значительно медленнее алита, но в поздние сроки твердения образует прочный гидросиликат кальция. При твердении выделяется небольшое количество тепла.
2(2СаО· SiO 2 ) + 4Н2О = 3СаО·2 SiO 2 ·3Н2О + Са(ОН)2
Поведение С2S относительно влияния на развитие коррозионного процесса в цементном камне достаточно нейтрально.
3. Трехкальциевый алюминат твердеет чрезвычайно быстро, но образует непрочный рыхлый гидроалюминат кальция. Тепловыделение при твердении значительное. Если этой реакции дать осуществиться, она вызовет “ложное схватывание” цемента.
3СаО· Al 2 O 3 + 6Н2О = 3СаО· Al 2 O 3 ·6Н2О
Для предотвращения образования этого продукта в состав портландцемента при помоле вводят гипс, который связывает трехкальциевый алюминат в гидросульфоалюминат кальция, дополнительно упрочняющий твердеющее цементное тесто.
3СаО· Al 2 O 3 + 3Са SO 4 ·2 H 2 O + 25Н2О = 3СаО· Al 2 O 3 ·3Са SO 4·31Н2О
Повышенное содержание С3А может вызвать коррозию цементного камня III вида и существенно понизить морозостойкость бетона.
4. Четырехкальциевый алюмоферрит по скорости твердения и тепловыделению находится между алитом и белитом и не оказывает влияния на развитие коррозии цементного камня в бетоне.
4СаО· Al 2 O 3 · F е2О3 + 10Н2О + 2Са(ОН)2 = 3СаО· Al 2 O 3 ·6Н2О + 3СаО· F е2О3·6Н2О
Заполнители. Заполнители для тяжелого бетона подразделяются на две группы: мелкие и крупные.
а) Мелкий заполнитель – песок для строительных работ – должен удовлетворять требованиям ГОСТ 10268, 8736. Песком называют рыхлую смесь зерен с крупностью от 0,16 до 5 мм, образовавшуюся в результате естественного разрушения горных пород (естественные пески) или при их дроблении (искусственные пески).
На качество бетона влияет:
- Наличие в песке примесей (глинистых, илистых, пылевидных, остатков растительных и животных организмов);
- зерновой состав песка. Для получения высококачественных бетонов песок должен содержать зерна всех фракций от 0,16 до 5мм, чтобы объем пустот в нем был минимальным. Чем меньше будет объем пустот, тем меньше потребуется цемента для получения плотного бетона.
Песок относится к химически инертным материалам и в коррозионное взаимодействие не вступает.
б) Крупный заполнитель (гравий и щебень) – должен удовлетворять требованиям ГОСТ 10268, 8267, 9268, 10260.
Гравием называют рыхлый материал с размером частиц от 5 до 70 мм, образовавшийся в результате естественного разрушения горных пород. Для гравия характерна гладкая поверхность и достаточно окатанная форма зерен, что не слишком благоприятно сказывается на прочности сцепления его с цементным камнем.
На качество бетона влияет:
- наличие в гравии примесей, особенно глины (не более 1 % для высококачественных бетонов и не более 3% для рядовых);
- зерновой состав заполнителей. В гравии должны содержаться зерна всех фракций, чтобы объем пустот был минимальным, и бетон получался более плотным и с меньшим расходом цемента;
- предельная крупность зерен гравия. Она не должна превышать ¼ части минимального сечения конструкции, а если конструкция армированная, то быть не более наименьшего расстояния между стержнями арматуры.
Щебень. Щебнем называют материал, образующийся при дроблении горных пород и имеющий размеры от 5 до 70 мм. Щебень имеет малоокатанную остроугольную форму и шероховатую поверхность, поэтому прочность сцепления его с цементным камнем выше, чем у гравия. В остальном требования к щебню предъявляются те же, что и к гравию.
Щебень и гравий – инертные заполнители, не влияющие на коррозионное поведение бетона.
Вода. Для затворения бетона пригодна питьевая вода, а также любая другая, не содержащая вредных примесей:
- хлоридов, вызывающих коррозию стальной арматуры в бетоне, если бетон армирован;
- сульфатов, вызывающих коррозию III вида цементного камня в бетоне;
- кислот, масел, нефтепродуктов, фенолов и др., вызывающих коррозию II вида цементного камня в бетоне..
Пригодность воды для бетона устанавливают химическим анализом и сравнительными испытаниями прочности бетонных образцов, изготовленных на испытуемой воде и на контрольной питьевой воде. Образцы испытывают через 28 суток нормального твердения. Вода считается пригодной, если приготовленные на ней образцы имеют прочность не меньше, чем контрольные на питьевой воде.
Добавки. Добавки для бетонов должны удовлетворять требованиям ГОСТ 24211-2003 «Добавки для бетонов и строительных растворов. Общие технические условия»). Они подразделяются на регуляторы твердения, пластифицирующие, гидрофобизирующие, воздухововлекающие и другие добавки.
Регуляторы твердения. К ним относятся ускорители и замедлители процессов схватывания и твердения бетона. Добавки-ускорители каталитически воздействуют на реакции гидратации между минералами цемента и водой, ускоряя скорость их протекания. К ним относятся хлористый кальций CaCl2, карбонат калия К2СО3, а также комплексные добавки ННК (нитрит-нитрат кальция), ННХК (нитрит-нитрат-хлорид кальция) и другие. Добавки-замедлители замедляют процессы схватывания и твердения бетонной смеси (табл. 3).
Таблица 3 - Рекомендуемые добавки для регулирования схватывания и твердения бетонной смеси
Класс добавки | Пред- ставители | Название | Дозировка,% от массы цемента | Эффект от применения |
Регуляторы сроков схватывания: Замедлители Ускорители | Сахаристые вещества НК ХК ННК ННХК СН ТНФ | Нитрат кальция Хлорид кальция Нитрит-нитрат кальция Нитрит-нитрат-хлорид кальция Сульфат натрия Тринатрийфосфат | 0,1-2 | Замедление схватывания до нескольких часов Ускорение схватывания и твердения в ранние сроки |
Особенностью использования добавок–ускорителей твердения является то, что эффективность их действия на твердение бетона и набор прочности проявляется в основном в течение первых 3…4 суток после затворения цемента водой. В дальнейшем эффект ускорения твердения и возрастания прочности ослабевает, и в 28-суточном возрасте прочности бетонов с добавками и без добавок становятся одинаковыми (рис.1). Следует отметить, что ускорители твердения на основе хлоридов могут вызвать коррозию стальной арматуры в армированных бетонах, поэтому их не рекомендуется вводить в количестве более 2% от массы цемента, а соли натрия и калия могут образовывать на поверхности бетонных конструкций белые налеты – высолы, ухудшающие внешний вид изделий и их свойства.
Рисунок 1 – Влияние добавок-ускорителей твердения на набор прочности цементных бетонов во времени
Пластифицирующие добавки. Они повышают подвижность бетонных смесей, или, при сохранении подвижности неизменной, позволяют снизить водопотребность бетонной смеси. Снижение водопотребности приводит к уменьшению водо-цементного отношения, что позволяет снизить расход цемента, или при том же расходе цемента повысить прочность бетона.
В табл. 4 приведены составы пластифицирующих добавок для бетонных смесей.
Таблица 4 - Пластифицирующие добавки для бетонных смесей
Класс добавки | Представители | Название | Дозиров- ка, % от массы цемента | Эффект от применения |
Суперпластификаторы | С-3 ДФ СМФ | Разжижитель С-3 Дофен Разжижитель СМФ | 0,4 - 0,8 | Снижение водопот-ребности бетонной смеси более 20% |
Сильнопластифицирую-щие | ЛСТМ-2 МТС-1 | Лигносульфонат технический модифицированный Модифицированный лигносульфонат | 0,15 – 0,3 | Снижение водо-потребности бетонной смеси до 20% |
Среднепластифицрующие | ЛСТ УПБ ПДК | Лигносульфонат технический Мелассная упаренная последрожжевая барда Плав дикарбоновых кислот | 0,1 – 0,2 | Снижение водопотребности бетонной смеси до 10% |
Слабопластифицирующие | ЩСПК НЧК ГКЖ-10 ГКЖ-11 | Щелочной сток производства капролактама Нейтрализованный черный контакт Этилсиликонат натрия Метилсиликонат натрия | 0,05 – 0,1 | Снижение водопотребности бетонной смеси до 5% |
Пластифицирующие добавки не влияют непосредственно на протекание коррозионных процессов, но могут существенно повысить морозостойкость бетона, что положительно сказывается на его долговечности.
Гидрофобные добавки. Они обеспечивают бетонным смесям нерасслаиваемость, а затвердевшему бетону придают некоторые водоотталкивающие свойства. Они могут вводиться в объем бетонной смеси с водой затворения в количестве от 0,1 до 0,8%., или наноситься на поверхность бетона. К ним относятся кремнийорганические жидкости (ГКЖ), битумные дисперсии, а также пропиточные гидрофобизирующие составы как отечественного производства (Аквастоп), так и зарубежные (Пенетрон). Они повышают долговечность бетона, т.к. из-за своей гидрофобности препятствуют прониканию воды в поры бетона, что повышает морозостойкость.
Воздухововлекающие добавки. Эти добавки при замешивании бетонной смеси вовлекают в нее дополнительное количество воздуха, которое создает в бетоне так называемую резервную пористость. При замерзании вода через систему капилляров попадает в эти резервные поры под давлением растущего льда, и опасного давления на стенки пор бетона не возникает. Это приводит к увеличению морозостойкости бетона. Вид и дозировка воздухововлекающих добавок представлены в табл. 5.
Таблица 5 - Рекомендуемые воздухововлекающие добавки для бетонных смесей
Класс добавки | Представители | Название | Дози ровка, % от массы цемента | Эффект от применения |
Воздухо- вовлекающие | СНВ КТП ОТП ГКЖ-10 ГКЖ-11 | Смола нейтрализованная воздухововлекающая Клей таловый пековый Омыленный таловый пек Этилсиликонат натрия Метилсиликонат натрия | 0.005 -0,03 | Обеспечение воздухововлечения на 3-5%, повышение морозостойкости бетона на 100-200 циклов |
Дата добавления: 2019-07-15; просмотров: 260; Мы поможем в написании вашей работы! |
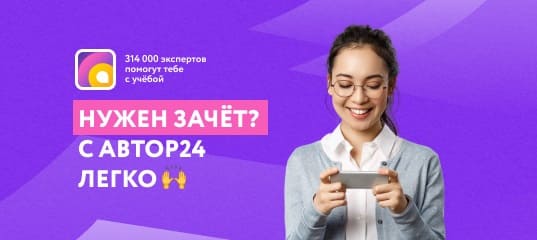
Мы поможем в написании ваших работ!