Методы вторичной защиты строительных конструкций
Защитить строительные конструкции от воздействия агрессивной среды можно различными способами. Если исчерпаны все возможности, чтобы придать материалу конструкций необходимую стойкость, то приходится защищать сооружение от контакта с агрессивной средой. Можно отвести агрессивную среду от сооружений или устроить непроницаемый для газов и жидкостей изолирующий слой на всей поверхности контакта сооружения и агрессивной среды.
Удаление агрессивной среды или снижение ее агрессивности весьма разнообразны и осуществляются обычно на основании специальной проектной проработки. Эта проработка осуществляется на этапе разработки технологической схемы и выбора объемно-планировочных параметров зданий и сооружений, а также типоразмеров строительных конструкций.
К основным принципам снижения агрессивности среды относятся:
- разработка генеральных планов предприятий, объемно-планировочных и конструктивных решений с учетом розы ветров и направленности потока грунтовых вод;
- проектирование технологического оборудования с максимально возможной герметизацией и обеспечение эффективной работы вентиляции.
Здания и сооружения, выделяющие в атмосферу газы, пыль, аэрозоль, влагу являются источниками повышенной опасности для ближайших к ним строительных конструкций. Попадая в атмосферу, агрессивные компоненты распространяются вместе с потоками воздуха, которые зависят от направления и скорости ветра.
|
|
Направление ветра наносят на генеральный план в виде т.н. «розы ветров» - схемы, показывающей преобладающее направление ветра в данном районе.
Здания и сооружения, попадающие в действие “розы ветров” с подветренной стороны, оказываются в зоне повышенной опасности, что следует учитывать при защите наружных стен, кровельных покрытий и всех открытых конструкций. Поэтому на генеральном плане источники агрессивных сред следует размещать таким образом, чтобы в зоне “розы ветров” за ними не было строений. Когда это невозможно – необходимо обеспечить защиту сооружений от атмосферных воздействий с учетом выделяющихся вредных веществ.
Внутри зданий и сооружений снижение степени агрессивности в первую очередь связано с уменьшением воздействия жидких сред. Исключение из производств мокрых процессов, гидросмыва, уменьшение объема канализационных стоков может на порядок снизить скорость коррозии.
Для тех производств, где по технологическим требованиям нельзя уменьшить высокую влажность воздуха, рекомендуются другие решения: подвесные потолки, специальные конструкции стен (вентиляция каналов в стенах), включение наружных конструкций во внутренние объемы здания и др.
|
|
Агрессивную грунтовую воду можно отвести от сооружения при помощи устройства наружного водоотвода, дренажа, различных водопонижающих устройств и др. Такие способы дают возможность длительно обеспечивать надежную эксплуатацию сооружений, но не защищают конструкции зданий от воздействия технологических проливов, которые могут иметь место в процессе производства. В этом случае необходимо изолировать строительные конструкции от воздействия агрессивной среды.
Для защиты подземных сооружений используется гидроизоляция различных видов. Простейшим видом гидроизоляции является устройство защитного экрана из плотно утрамбованной глины (т.н. глиняный замок). Толщина глиняного экрана поддается расчету, исходя из скорости диффузии агрессивного вещества из грунта в конструкции через глиняный слой. Как правило, по расчету требуется толщина замка 3-5 см, но технически это трудно сделать.Иногда для гидроизоляции используют бентонитовые маты (из высокопластичной бентонитовой глины), как зарубежного, так и отечественного производства.
Наиболее распространенным материалом для гидроизоляции бетонных и железобетонных конструкций являются битумы и битумные составы. В основном в России, и в частности в Башкортостане, используются нефтяные битумы. Они получаются после отгонки из нефти более легких фракций – бензина, керосина, солярового масла и некоторых других продуктов. Битумы термопластичны, т.е. размягчаются при нагревании, а при охлаждении затвердевают с образованием эластичной пленки. Битумы водостойки, а также проявляют высокую химическую стойкость при воздействии растворов разбавленных кислот, но растворяются в большинстве органических растворителей.
|
|
Перед нанесением битумных покрытий поверхность бетона грунтуют, обычно раствором битума в бензине (праймер). В последнее время для грунтовки начали применять битумные водные эмульсии, а еще лучше - битумно-полимерные эмульсии. Добавки в битум некоторых видов каучуков значительно повышают адгезию битумной пленки к бетону, ее эластичность и долговечность.
В ответственных случаях, например при гидроизоляции подземных помещений, тоннелей и т.п. применяют оклеечную изоляцию. В ней слои битумной мастики чередуются со слоями армированного материала – гидроизола, стеклобитума, фольгоизола. Основа гидроизола – асбестовый картон, стеклобитума – сетка из стеклянного волокна, стеклохолста или стеклоткани, фольгоизола – алюминиевая фольга.
|
|
В наземных конструкциях – как металлических, так и железобетонных, находящихся в средне- и сильноагрессивной газовой среде, основным способом защиты от коррозии является устройство лакокрасочного покрытия из химически стойких к действию данной агрессивной среды красочных материалов. Лакокрасочными материалами называют вязкожидкие составы, наносимые на поверхность конструкции тонким слоем, который через несколько часов отвердевает и образует пленку, прочно сцепляющуюся с основанием. Красочные составы содержат:
- связующие вещества. Они являются главными компонентами красочного состава, определяющими консистенцию краски, а также прочность, твердость и долговечность образующейся пленки. В зависимости от вида красочного состава связующими веществами являются: полимеры – в полимерных красках, олифы – в масляных красках, цементы – в цементных красках, известь – в водно-известковых красках, жидкое стекло – в силикатных красках и т.д.
- Пигменты. Они представляют собой тонкие цветные порошки, не растворимые в связующем веществе и растворителе. От них зависит не только цвет, но и долговечность лакокрасочного покрытия. Подобно заполнителю в бетонах и растворах, пигменты уменьшают усадочные деформации пленки при ее твердении (высыхании) и при колебании влажности окружающей среды. Пигменты подразделяются на неорганические и органические. Неорганические пигменты бывают природные (мел, охра, сурик, мумия) и искусственные. Искусственные пигменты представляют собой в основном оксиды и соли металлов. К ним относятся белила, кроны, ультрамарин, лазурь малярная и др. Органические пигменты подразделяются на природные (сажа, графит) и синтетические, представляющие собой сложные органические соединения.
- Растворители и разбавители. Растворители способны растворять связующее вещество. В основном это органические жидкости – ацетон, скипидар, бензол, уайт-спирит и др. Разбавители не растворяют пленкообразующие вещества и служат лишь для уменьшения вязкости красочного состава, т.е. их добавляют для придания краскам удобонаносимости. Роль разбавителя играет олифа в густотертых масляных красках, или вода, вводимая в водоэмульсионные краски.
- Наполнители. Наполнители вводят в состав красок для экономии связующих веществ, а также для улучшения механических свойств красочных пленок. В основном используют тонкие природные порошки – мел, тальк, молотый известняк и др. Это может быть молотая горная порода, например, диабаз или андезит – для кислотостойких составов; известняк или доломит – для щелочестойких составов; графит – для составов, стойких в кислотах, щелочах и растворителях. Во многие составы защитных покрытий вводят асбест для повышения прочности слоя на растяжение и придания ему повышенной трещиностойкости.
Лаки и краски известны всем, но не все из них годятся для защиты строительных конструкций от коррозии. Нужно применять лаки и краски, устойчивые к действию именно тех агрессивных веществ, которые могут попасть на конструкции. Кроме того, к защитным покрытиям железобетонных конструкций предъявляют еще одно важное требование – они должны быть эластичными и выдерживать без разрушения деформации бетона, если в нем возникнут трещины. Такие покрытия называют трещиностойкими.
Из химически стойких веществ, способных образовывать защитные пленки, применяются самые различные полимеры. Хлорвиниловые и полихлорвиниловые смолы наиболее широко распространены в качестве защитных лакокрасочных покрытий.
Высокой стойкостью обладают лаки и краски на основе эпоксидных смол, хлоркаучуков, полиуретановых смол. Повышенной термостойкостью отличаются покрытия на основе кремнийорганических соединений.
В момент нанесения защитное покрытие должно быть в жидком, подвижном состоянии, а затем затвердеть на поверхности. Чаще всего затвердевание происходит в результате испарения из лакокрасочного состава растворителя. Растворители, как правило, представляют собой легколетучие жидкости. Получающаяся пленка может стать непроницаемой только после многократного нанесения состава.
Наиболее распространены в настоящее время защитные химически стойкие покрытия на основе перхлорвиниловых смол (марки ХВ). Чтобы получить непроницаемое покрытие, необходимо нанести 5…7 слоев, постепенно наращивая толщину покрытия (у надежных защитных покрытий она должна быть не меньше 0.1 мм).
Из других составов большой интерес представляют эпоксидные смолы. Эпоксидные смолы применяют в виде клеев, лаков, красок, шпатлевок. Они хороши для защиты и металла и бетона. Эпоксидные покрытия обладают высокой химической стойкостью и прочностью. Это позволяет применять их также для устройства т.н. наливных полов. Толщина покрытия пола составляет ~ 2 мм, но такая конструкция весьма эффективна.
Полное защитное покрытие обычно состоит из грунтовочного слоя (грунта), и нескольких защитных слоев. Сумму всех слоев называют системой покрытия. В качестве грунта обычно применяют лаки. Если защищаемая поверхность шероховатая, ее выравнивают слоем густого состава – шпатлевкой. Основные слои системы покрытия представляют собой эмали.
Возможно получение непроницаемого покрытия, если использовать составы без растворителя. Например, если в качестве связующего используется натуральная олифа: льняное масло, окисляясь, образует полимерную пленку. Полиуретановые лаки твердеют под действием влаги, что позволяет наносить их на влажную поверхность.
Важную группу защитных покрытий составляют тиксотропные покрытия. Явление тиксотропии представляет собой способность жидкости к резкому изменению вязкости при изменении скорости ее деформации. В спокойном состоянии вязкость максимальная. При встряхивании, перемешивании краска становится подвижной и текучей. При нанесении тиксотропного вещества можно за один слой получить покрытие ~ 100 мк. Это покрытие на основе хлоркаучука и хлорсульфированного полиэтилена. Они чрезвычайно трещиностойки. Самый рациональный способ нанесения тиксотропных покрытий – метод безвоздушного напыления. При этом методе материал (даже очень вязкий) под высоким давлением (~200 ат.) подается в сопло, распыляется и наносится на поверхность. На поверхности материал опять загустевает и не стекает с конструкции. Обычно хватает двух слоев при минимальном количестве растворителя.
Одной из ответственных и сложных задач является защита полов. Недостаточная стойкость полов приведет к повреждению основных несущих конструкций (например, перекрытия) или прониканию агрессивного компонента в грунт к фундаментам и подземным конструкциям. В то же время полы должны выдерживать механические нагрузки. Во многих производствах полы подвергаются действию агрессивных жидкостей при мокрой уборке. Кроме того, иногда требуются антистатические свойства: беспыльность, гигиеничность и др. Таким образом, конструкция пола должна удовлетворять разнообразным требованиям. Износостойкость и химическую стойкость обеспечивают керамические кислотостойкие материалы. Непроницаемость для жидких сред обеспечивается устройством специального гидроизоляционного слоя из химически стойкого материала.
В последние годы широкое распространение получили наливные полы; в т.ч. у нас в Башкирии. Это производство минеральной воды на Стерлитамакском ОАО «Шихан», молочные и мясоконсервные комбинаты, ОАО «Куастик», ОАО «Полиэф». Кроме полов на основе эпоксидных смол, наиболее часто применяются полиуретановые полы.
Из специальных способов защиты остановимся на пропитке пористых материалов органическими термопластичными или термореактивными полимерными материалами. Коррозионную стойкость древесины, кирпича, бетонов и других пористых материалов можно существенно повысить, заполнив их поры полимерами. Для этого материалы погружают в жидкий пропитывающий состав при атмосферном или повышенном давлении. Отвердевание составов в порах происходит следующими способами:
- при прогревании изделий;
- под действием радиации.
После отвердевания полимера материал называют бетонополимером. Бетонополимеры представляют собой композиционные материалы, в которых силикатная (цементная) матрица совмещена с органическим полимером. Изготовление бетонополимеров включает следующие операции. Бетонные изделия высушивают и под вакуумом пропитывают раствором мономера, который потом полимеризуется в порах бетона. Для ускорения этого процесса используют радиационный или термокаталитический способы. При радиационном способе изделия облучают γ-лучами. При термокаталитическом способе в мономер вводят катализатор полимеризации, а изделия подвергают термической обработке.
Изделия могут пропитываться полностью, или только с поверхности на небольшую глубину.
Свойства бетонополимера значительно отличаются от свойств исходного бетона. На основе бетонов В 30 – 50 получают пропитанные бетоны с прочностью при сжатии 120-300 МПа. В 3-4 раза возрастает сопротивление истиранию, в несколько раз снижается водопроницаемость, а морозостойкость возрастает до нескольких тысяч циклов.
Из бетонополимеров изготавливают трубы, а также железобетонные конструкции, подвергающиеся при эксплуатации интенсивной коррозии.
Бетоны пропитывают стиролом, метилметакрилатом и др. смолами. У бетона, пропитанного стиролом, после прогрева, в результате которого стирол полимеризуется, резко повышаются физико-химические свойства. Предел прочности на сжатие 100…200 МПа, химическая стойкость также высока, т.к. полистирол химически стоек в кислотах и щелочах.
Дата добавления: 2019-07-15; просмотров: 283; Мы поможем в написании вашей работы! |
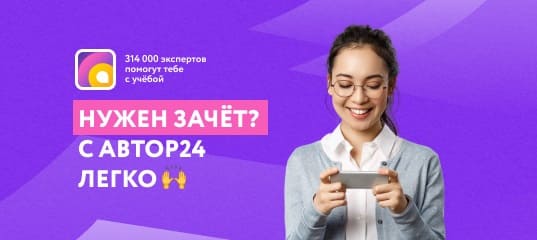
Мы поможем в написании ваших работ!