Метод полива из раствора. Основное технологическое оборудование
Метод разработан для изготовления эфироцеллюлозных пленок, принцип получения которых заключается в нанесении расплава полимера на твердую зеркальную поверхность и испарение из него основной массы растворителей.
Первые устройства, предназначенные для этих целей, представляли собой длинные столы с зеркальной поверхностью, на которые с помощью специального движущегося приспособления наносился тонкий слой эфироцеллюлозного раствора. В настоящее время созданы специальные машины, в которых расплав полимера наносится из неподвижной фильеры на движущуюся зеркальную поверхность барабана шириной 1,5 м и диаметром более 3 м.
Также разработаны машины ленточного типа (рис. 7.8). Они получили наибольшее распространение. Машина состоит из двух барабанов диаметром 1,5 м, изготовленных их чугуна (стали).
Рис. 7.8. Схема машины ленточного типа для получения пленок методом полива: 1, 2 - ведущий и ведомый барабаны, 3 - лента с зеркальной поверхностью, 4 - фильера, 5 - кожух машины
Барабан 1 ведущий, барабан 2 - ведомый. Барабаны охватываются «бесконечной» туго натянутой медной лентой 3 длиной 30-86 м. Лента также может изготавливаться из никеля или нержавеющей стали. Вся машина помещена в алюминиевый кожух 5, который образует два сушильных канала (для верхней и нижней части бесконечной ленты). Нагрев может осуществляться с помощью электрических нагревателей или с помощью теплоносителей.
|
|
Важным элементом машины является фильера 4. Это устройство позволяет наносить тонкий слой пленкообразного раствора на поверхность бесконечной ленты. Фильеры по принципу действия делятся на мажущие и льющие (рис. 7.9). Применение их обусловлено вязкостью пленкообразующего раствора.
Мажущая фильера представляет собой сосуд (рис. 7.9, а), в нижней части которого имеется щель по всей ширине.
Рис. 7.9. Фильер для нанесения пленкообразующего раствора: а) мажущая фильера, б) льющая фильера
Рамка фильеры предназначена для задерживания пленкообразующего раствора, который вытекает из формующей щели и создает некоторый запас раствора на зеркальной поверхности ленты. Планка регулирует толщину наносимого на ленту слоя и, значит, регулирует толщину готовой пленки.
Льющая фильера (рис. 7.9, б)представляет корытообразный сосуд, состоящий из двух камер: рабочей и запасной. Камеры отделены перегородкой. Раствор поступает в запасную камеру I, затем, пройдя под перегородкой, поступает в рабочую камеру II. Это обеспечивает равномерное вытекание раствора на зеркальный стол. Передняя стенка фильеры может перемещаться по вертикали, благодаря чему изменяется ширина формующей щели.
|
|
Технологический процесс изготовления пленок включает следующие операции:
- приготовление раствора полимера;
- очистка раствора от механических включений;
- удаление пузырьков воздуха из раствора;
- отлив пленки с последующим испарением растворителей.
Растворение полимера проводят в горизонтальном или вертикальном смесителе с мешалкой или без нее. В раствор иногда вводят пластификаторы, которые повышают эластичность пленок. От механических примесей раствор очищают путем фильтрования с помощью рамных фильтр-прессов и других конструкций. В момент фильтрования в раствор попадают воздушные пузырьки. От них освобождают раствор при помощи вакуумирования или путем выдержки при высокой температурой. Важной операцией является отлив пленки. При этом раствор полимера через фильеру поступает на движущуюся ленту и покрывает её ровным слоем, над которым пропускается слегка подогретый воздух. Когда пленка совершит один полный оборот, её снимают перед фильерой. В некоторых случаях производится почти полное высушивание пленки в поливочной машине, но это снижает производительность машины. Чаще пленку снимают недосушенной и переносят в сушилку.
Данный метод может применяться для получения полистирольной пленки малой толщины. При этом используется раствор, получаемый при полимеризации стирола.
|
|
24) Производство резинотехнических изделий и технологическое оборудование
В настоящее время производство резиновых изделий имеет тенденцию к увеличению. Резинотехнические изделия нашли свое применение во многих отраслях промышленности, таких как: машиностроение, горнодобывающая промышленность, железнодорожное дело и т.д. Ассортимент вырабатываемой резинотехническими предприятиями продукции масштабен и с каждым годом совершенствуется. Это всевозможные ремни, чехлы, втулки, уплотнители, прокладки и многое другое.
Оборудование и технологии, применяемые на большинстве росийских предприятий давно уже устарели. Ввиду данной причины, производительность низкая, велика доля брака, осуществляются выбросы вредных веществ в атмосферу, себестоимость продукции высока и т.д. Основой любой резины служит каучук натуральный или синтетический, который и определяет основные свойства резинового материала. Синтетический каучук в промышленном масштабе впервые получен в 1931 году в СССР по способу Лебедева. На полузаводской установке было получено 260 кг синтетического каучука из дивинила, а в 1932 году впервые в 1932 году впервые в мире осуществлен его промышленный синтез. В Германии каучук был синтезирован в 1936-1937 годах, а в США – в 1942 году.
|
|
Смешение каучука с ингредиентами проводится в специальных аппаратах – резиносмесителях или вальцах резиносмесительных, в которых каучук перетирается вместе с ингредиентами. Вулканизирующий агент вводится в резиновую смесь в последний момент приготовления резиновой смеси во избежание преждевременной вулканизации [4].
Резиносмесители являются основным видом оборудования, применяемым для приготовления резиновых смесей и пластикации каучука. Резиносмеситель представляет собой закрытую камеру с вращающимися навстречу друг другу валками с фигурным профилем или машину червячного типа, в загрузочную воронку которой подаются в определенной последовательности все компоненты резиновой смеси.
Преимуществом резиносмесителей являются:
• герметизация рабочего процесса (в результате чего не просыпаются сыпучие компоненты, и отсутствует пылевыделение);
• более приятные условия перемешивания материала;
• высокая производительность;
• значительное сокращение продолжительности процесса смешения (создаваемое в смесительной камере давление позволяет производить смешение за 2,5-8 мин.);
• безопасность работы.
Кроме того, резиносмесители легко агрегируются с машинами для последующей обработки смеси; протекающий в них процесс поддается автоматизации.
Различают резиносмесители периодического и непрерывного действия. К резиносмесителям периодического действия относятся машины, у которых загрузка компонентов и выгрузка готовой смеси происходит периодически. Резиносмесителями непрерывного действия называют машины, у которых загрузка и выгрузка готовой смеси происходят непрерывно. Резиносмесители периодического действия отличаются друг от друга размерами и объемом одновременно загружаемого материала, формой рабочей части роторов, частотой их вращения, мощностью привода и давлением на обрабатываемый материал в камере смешения. В зависимости от способа охлаждения все резиносмесители делятся на две группы. К первой группе относятся машины с открытым охлаждением смесительной камеры, ко второй – с закрытым охлаждением.
Основными видами смесителей, применяемых в настоящее время, являются резиносмесители со свободным объемом камеры 250 л. Смесители, имеющие частоту вращения роторов около 20 об./мин., считаются тихоходными, а 40 об/мин. - скоростными.
Для получения резиновой смеси на вальцах каучук и другие ингредиенты загружают на валки, которые вращаются по направлению к зазору между ними. Слои каучука, соприкасающиеся с поверхностью валков, за счет сил адгезии и трения затягиваются в зазор между валками со скоростью, соответствующей окружной скорости валков. Каждый следующий слой каучука или резиновой смеси, соприкасающийся с предыдущим слоем, за счет когезионных сил также увлекается в зазор вальцов, но со скоростью, постепенно уменьшающейся по мере удаления этого слоя от поверхности валков. Таким образом, в пространстве над зазором на поверхности каждого из двух валков всегда имеется “запас” каучука или резиновой смеси, скорость движения слоев в котором постепенно убывает по мере удаления их от поверхности соответствующего валка.
На некотором расстоянии от минимального зазора слои материала встречаются, и часть смеси, не проходящая в зазор начинает обратно выталкиваться из межвалкового клина, образуя противоток, “вращающийся запас”, а слои материала, прилегающие к поверхности валков, затягиваются в зазор.
Это наблюдается лишь в том случае, когда силы трения, увлекающие смесь в зазор, превосходят когезионную прочность и силу внутреннего трения смеси.
В зоне “вращающегося запаса” наблюдаются наибольшие деформации сдвига, возникающие в резиновой смеси, а следовательно, и наибольшие напряжения сдвига, что обуславливает наиболее интенсивное смешение. При смешении на вальцах ингредиенты внедряются в слой вращающегося запаса смеси, прилегающего к заднему валку вальцов, и поэтому концентрация ингредиентов всегда больше в поверхностном слое смеси, находящейся на переднем валке.
Режим смешения и оптимальный объем единовременной загрузки устанавливают в зависимости от состава смеси, свойств и физического состояния загружаемых материалов.
Температуру смеси при смешении на вальцах устанавливают в зависимости от свойств смеси; она не должна превышать температуру, при которой происходит активация вулканизирующей группы. Температуру смеси и рабочих поверхностей валков контролируют чаще всего игольчатой и лучковой термопарами.
Очень часто каучуки и регенерат загружают на вальцы при малом зазоре, который затем увеличивают.
Для повышения эффективности смешения необходимо:
• более равномерно распределять загружаемые сыпучие и жидкие ингредиенты по всей длине переднего валка;
• производить более частую подрезку смеси после введения всех ингредиентов и перевертывание полотна смеси на другую сторону, если можно подрезать механическими ножницами;
• пропускать полотно смеси через дополнительный валик для воздушного охлаждения;
• загружать ингредиенты, вводимые в небольших количествах, в виде паст, или так называемых композиций, которые более равномерно распределяются по всей массе смеси.
Важное значение при смешении на вальцах имеет порядок введения компонентов. Сначала на вальцы загружают каучук и обрабатывают до тех пор, пока он не станет проскальзывать на валках. Затем в смесь последовательно вводят диспергирующие агенты (жирные кислоты), ускорители активаторы вулканизации. Большое значение имеет порядок загрузки технического углерода и пластификаторов. Для лучшего диспергирования наполнители, как правило, загружают отдельными порциями. Так как пластификаторы снижают вязкость резиновой смеси и напряжения сдвига при ее деформации, их обычно вводят после наполнителей. Иногда для предотвращения чрезмерного увеличения жесткости смеси, расхода энергии и распорных усилий между валками пластификаторы добавляют в смеси после введения в них некоторой части наполнителей. Во избежание подвулканизации вулканизующие агенты обычно вводят в резиновую смесь в конце процесса смешения. Если вулканизующий агент плохо диспергируется в смеси, то его вводят в начале процесса смешения, а ускорители вулканизации в конце.
После введения ингредиентов смесь всегда подвергают тщательной гомогенизации (подрезают, скатывают в рулоны и подают в зазор между валками в другом месте). Наиболее хорошие результаты достигаются, если рулон смеси направлен в зазор перпендикулярно валкам, то есть концом рулона в зазор.
Изменение последовательности введения компонентов при смешении может привести к существенному изменению технологических свойств резиновой смеси и свойств вулканизатов. Оптимальный режим смешения определяют для каждого состава резиновой смеси и заносят в техническую документацию.
Готовую резиновую смесь, состоящую из каучука, вулканизирующего агента, ускорителя вулканизации, активатора, наполнителей, стабилизатора и т.п., направляют на завершающий процесс резинового производства – вулканизацию. Вулканизацию проводят или после формования из резиновой смеси соответствующих изделий, или одновременно с процессом формования изделий. Вулканизация протекает при нагревании.
Оборудованием для процесса вулканизации выступают различные гидравлические пресса, на которых устанавливается технологическая оснастка – пресс-форма, состоящая из двух полуформ. Заготовка резиновой смеси расплавляется под действием давления, по литниковым каналам затекает в оформляющую полость пресс-формы и резина принимает форму изделия .В процессе изготовления формовых резинотехнических изделий, как и на любом химическом предприятии, образуются различные вредные вещества, они негативно воздействуют как на окружающую природную среду, так и на организм человека, поэтому существуют различные очистные сооружения для их нейтрализации, улавливания (пыль серы, сажи).
Для улавливания взвешенной пыли используют, например, гидродинамический пылеуловитель. Гидродинамический пылеуловитель работает следующим образом: запыленный газовый поток поступает в корпус через патрубки и и увлекает жидкость в канал (импеллер) между наклонными лопатками. Часть капель из образующейся газожидкостной смеси прижимается воздухом к вогнутой части пластин и отбрасывается затем на перегородки, остальная часть увлекается воздухом через зазоры между этими пластинами в верхнюю часть корпуса, где окончательно отклоняется пластиной 6. Очищенные газы, пройдя каплеуловитель, выбрасываются в атмосферу, а вода вместе с уловленной пылью стекает в шламоприемник .
Необходимый уровень жидкости в аппарате поддерживается регулятором. В верхних слоях жидкости размещен вибратор, закрепленный к корпусу посредством упругой перфорированной мембраны, который увеличивает поверхность взаимодействия газожидкостной взвеси с пылью созданием виброкипящего слоя в верхних слоях жидкости, что приводит к более интенсивному перемешиванию газа и жидкости.
Аппарат может быть применен для очистки от тонкой фракции пыли и увлажнения воздуха в вентиляционных установках и установках кондиционирования воздуха, а также при улавливании туманов, хорошо растворимой пыли, а так же при совместном протекании процессов пылеулавливания, охлаждения газов и их абсорбции.
Эффективность конструкции аппарата увеличивается за счет большей поверхности газожидкостной взвеси, путем применения вибропсевдоожиженного слоя в жидкости и составляет в вышеуказанных процессах и при улавливании пылевых частиц размером больше 5 мкм порядка 92...95% [8].
Дата добавления: 2019-07-15; просмотров: 758; Мы поможем в написании вашей работы! |
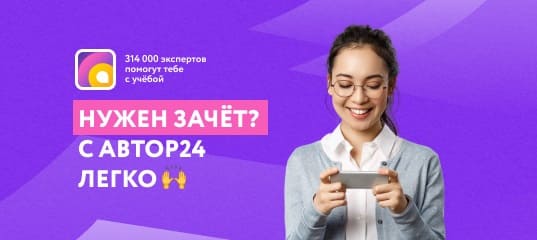
Мы поможем в написании ваших работ!